Researchers have used Accelrys' DMol3 to examine bonding differences between two types of nanotube deformation: (1) bending, and (2) pushing with atomically sharp AFM tips.
Design Ultrasensitive Sensors Based on Carbon Nanotubes
Such an understanding should lead to a better design of ultrasensitive sensors that could detect even the smallest mechanical perturbations, and also the design of new types of strain gauges based on carbon nanotubes.
Potential Applications of Carbon Nanotubes
Carbon nanotubes have recently turned into a hot area of research activity, fuelled by experimental breakthroughs that have led to realistic possibilities of using them in a host of commercial applications: Field emission-based flat panel displays, novel semiconducting devices in microelectronics, hydrogen storage devices, chemical sensors, and most recently in ultra-sensitive electromechanical sensors.
Measuring the Conductivity of Metallic Nanotubes
An important experiment with regards to developing electrochemical sensors involved a metallic nanotube suspended over a 600 nm long trench. When the middle part of such a suspended nanotube was pushed with the tip of an atomic force microscope (AFM), the conductivity was found to decrease by almost two orders of magnitude. This drop in conductance was much higher than previously computationally predicted values for tubes bent under mechanical duress.
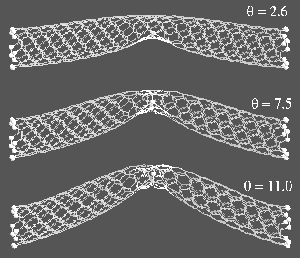
|
Figure 1. Structure of a (5, 5) tube (fixed ends) when a tip-constrained atom in the middle (in ball representation) is displaced to various tip-deformation angles. At a critical angle of 7.5º, a top atom forms a bond with the tip-constrained atom leading to sp3 coordination. Larger deformation leads to a complex defect with dangling bonds
|
Examining Bonding Differences between Two Types of Nanotube Deformation
The DFT code DMol3 in combination with classical molecular dynamics and the Universal Forcefield (UFF) has been used to examine bonding differences between two types of nanotube deformation: (1) bending, and (2) pushing with atomically sharp AFM tips. Bent tubes maintain an all-hexagonal network up to large angles. AFM-probed tubes, in contrast, display a more complex behavior, which depends on the details of how the AFM-tip is represented in the simulations.
Electrical Responses of Carbon Nanotubes under Two Types of Deformation
More recently, the electrical response of carbon nanotubes was computed under the two types of deformation. It was shown that bent tubes do not display large changes in conductance. In contrast, AFM-pushing led to a net tensile stretching of the tube, which for zigzag tubes opened up an energy gap at the Fermi level, and led to a significant drop in the room-temperature electrical conductance.
Carbon Nanotube Based Strain Gauges
Ongoing collaboration with the nanotechnology group of NASA Ames Research Center, Moffet Field, USA, is expected to yield more interesting results in the near future. The work has prompted nanotechnologists to explore the design of new types of strain gauges and pressure sensors based on carbon nanotubes.
|