There are a number of methods of making carbon nanotubes (CNTs) and fullerenes. Fullerenes were first observed after vaporizing graphite with a short-pulse, high-power laser, however this was not a practical method for making large quantities. CNTs have probably been around for a lot longer than was first realized, and may have been made during various carbon combustion and vapor deposition processes, but electron microscopy at that time was not advanced enough to distinguish them from other types of tubes.
The first method for producing CNTs and fullerenes in reasonable quantities – was by applying an electric current across two carbonaceous electrodes in an inert gas atmosphere. This method is called plasma arcing. It involves the evaporation of one electrode as cations followed by deposition at the other electrode. This plasma-based process is analogous to the more familiar electroplating process in a liquid medium. Fullerenes and CNTs are formed by plasma arcing of carbonaceous materials, particularly graphite. The fullerenes appear in the soot that is formed, while the CNTs are deposited on the opposing electrode.
Another method of nanotube synthesis involves plasma arcing in the presence of cobalt with a 3% or greater concentration. As noted above, the nanotube product is a compact cathode deposit of rod like morphology. However when cobalt is added as a catalyst, the nature of the product changes to a web, with strands of 1mm or so thickness that stretch from the cathode to the walls of the reaction vessel. The mechanism by which cobalt changes this process is unclear, however one possibility is that such metals affect the local electric fields and hence the formation of the five-membered rings. [“Nanotechnology: Basic Science and Emerging Technologies”, M. Wilson et al, (2002)]
Arc Method
The carbon arc discharge method, initially used for producing C60 fullerenes, is the most common and perhaps easiest way to produce CNTs, as it is rather simple. However, it is a technique that produces a complex mixture of components, and requires further purification - to separate the CNTs from the soot and the residual catalytic metals present in the crude product. This method creates CNTs through arc-vaporization of two carbon rods placed end to end, separated by approximately 1mm, in an enclosure that is usually filled with inert gas at low pressure. Recent investigations have shown that it is also possible to create CNTs with the arc method in liquid nitrogen. A direct current of 50 to 100A, driven by a potential difference of approximately 20 V, creates a high temperature discharge between the two electrodes. The discharge vaporizes the surface of one of the carbon electrodes, and forms a small rod-shaped deposit on the other electrode. Producing CNTs in high yield depends on the uniformity of the plasma arc, and the temperature of the deposit forming on the carbon electrode. [“Nanotechnology: Basic Science and Emerging Technologies”, M. Wilson et al, (2002)]
Laser Methods
In 1996 CNTs were first synthesized using a dual-pulsed laser and achieved yields of >70wt% purity. Samples were prepared by laser vaporization of graphite rods with a 50:50 catalyst mixture of Cobalt and Nickel at 1200°C in flowing argon, followed by heat treatment in a vacuum at 1000°C to remove the C60 and other fullerenes. The initial laser vaporization pulse was followed by a second pulse, to vaporize the target more uniformly. The use of two successive laser pulses minimizes the amount of carbon deposited as soot. The second laser pulse breaks up the larger particles ablated by the first one, and feeds them into the growing nanotube structure. The material produced by this method appears as a mat of "ropes", 10-20nm in diameter and up to 100µm or more in length. Each rope is found to consist primarily of a bundle of single walled nanotubes, aligned along a common axis. By varying the growth temperature, the catalyst composition, and other process parameters, the average nanotube diameter and size distribution can be varied.
Arc-discharge and laser vaporization are currently the principal methods for obtaining small quantities of high quality CNTs. However, both methods suffer from drawbacks. The first is that both methods involve evaporating the carbon source, so it has been unclear how to scale up production to the industrial level using these approaches. The second issue relates to the fact that vaporization methods grow CNTs in highly tangled forms, mixed with unwanted forms of carbon and/or metal species. The CNTs thus produced are difficult to purify, manipulate, and assemble for building nanotube-device architectures for practical applications. [“Nanotechnology: Basic Science and Emerging Technologies”, M. Wilson et al, (2002)]
Chemical Vapor Deposition
Chemical vapor deposition of hydrocarbons over a metal catalyst is a classical method that has been used to produce various carbon materials such as carbon fibers and filaments for over twenty years. Large amounts of CNTs can be formed by catalytic CVD of acetylene over Cobalt and iron catalysts supported on silica or zeolite. The carbon deposition activity seems to relate to the cobalt content of the catalyst, whereas the CNTs’ selectivity seems to be a function of the pH in catalyst preparation. Fullerenes and bundles of single walled nanotubes were also found among the multi walled nanotubes produced on the carbon/zeolite catalyst.
Some researchers are experimenting with the formation of CNTs from ethylene. Supported catalysts such as iron, cobalt, and nickel, containing either a single metal or a mixture of metals, seem to induce the growth of isolated single walled nanotubes or single walled nanotubes bundles in the ethylene atmosphere. The production of single walled nanotubes, as well as double-walled CNTs, on molybdenum and molybdenum-iron alloy catalysts has also been demonstrated. CVD of carbon within the pores of a thin alumina template with or without a Nickel catalyst has been achieved. Ethylene was used with reaction temperatures of 545°C for Nickel-catalyzed CVD, and 900°C for an uncatalyzed process. The resultant carbon nanostructures have open ends, with no caps. Methane has also been used as a carbon source. In particular it has been used to obtain ‘nanotube chips’ containing isolated single walled nanotubes at controlled locations. High yields of single walled nanotubes have been obtained by catalytic decomposition of an H2/CH4 mixture over well-dispersed metal particles such as Cobalt, Nickel, and Iron on magnesium oxide at 1000°C. It has been reported that the synthesis of composite powders containing well-dispersed CNTs can be achieved by selective reduction in an H2/CH4 atmosphere of oxide solid solutions between a non-reducible oxide such as Al2O3 or MgAl2O4 and one or more transition metal oxides. The reduction produces very small transition metal particles at a temperature of usually >800°C. The decomposition of CH4 over the freshly formed nanoparticles prevents their further growth, and thus results in a very high proportion of single walled nanotubes and fewer multi walled nanotubes. [“Nanotechnology: Basic Science and Emerging Technologies”, M. Wilson et al, (2002)]
Ball Milling
Ball milling and subsequent annealing is a simple method for the production of CNTs. Although it is well established that mechanical attrition of this type can lead to fully nano porous microstructures, it was not until a few years ago that CNTs of carbon and boron nitride were produced from these powders by thermal annealing. Essentially the method consists of placing graphite powder into a stainless steel container along with four hardened steel balls. The container is purged, and argon is introduced. The milling is carried out at room temperature for up to 150 hours. Following milling, the powder is annealed under an inert gas flow at temperatures of 1400°C for six hours. The mechanism of this process is not known, but it is thought that the ball milling process forms nanotube nuclei, and the annealing process activates nanotube growth. Research has shown that this method produces more multi walled nanotubes and few single walled nanotubes. [“Nanotechnology: Basic Science and Emerging Technologies”, M. Wilson et al, (2002)]
Other Methods
CNTs can also be produced by diffusion flame synthesis, electrolysis, use of solar energy, heat treatment of a polymer, and low-temperature solid pyrolysis. In flame synthesis, combustion of a portion of the hydrocarbon gas provides the elevated temperature required, with the remaining fuel conveniently serving as the required hydrocarbon reagent. Hence the flame constitutes an efficient source of both energy and hydrocarbon raw material. Combustion synthesis has been shown to be scalable for high-volume commercial production. [“Nanotechnology: Basic Science and Emerging Technologies”, M. Wilson et al, (2002)]
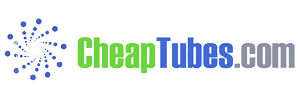
This information has been sourced, reviewed and adapted from materials provided by Cheap Tubes Inc.
For more information on this source, please visit Cheap Tubes Inc.