Textile manufacturers have begun to use nanomaterials in their products. The unique properties of nanoparticles and nanofibers mean they can be used to design fabrics with excellent mechanical strength, chemical resistance, water repellence, antibacterial properties and a wealth of other properties that are unattainable by any other means.
However, there is still a lot of research required in this area. The different techniques needed to produce nano-enhanced textiles are not always easily compatible with existing manufacturing processes, leading to increased development costs. This can also cause further issues, such as quality control and inhomogeneities in nanoparticle dispersion through the fabric.
There are also issues around the implications of nanoparticle exposure, both for human health and the environment. A great deal of recent research has focused on this issue, but we are still some way from understanding fully the toxicological effects of various kinds of nanoparticles which are already appearing in consumer products.
Nanomaterials Used in Textiles
The most common type of nano-enhanced fiber currently studied is a simple composite of a conventional natural or synthetic fiber with nanoparticles to improve the performance or add novel properties to the fabric. Some examples are given in the table below.
Table 1. Properties of nanomaterials used in textiles
Nanomaterial |
Properties |
Carbon black nanoparticles or nanofibres |
Abrasion resistance |
Higher tensile strength |
Good chemical resistance |
Electrical conducting |
Carbon nanotubes |
Exceptionally strong (100x tensile strength of steel) |
Lightweight |
Electrically conducting |
Thermally conducting |
Metal oxide nanoparticles |
Photocatalytic |
Electrically conductive |
UV Protection |
Antimicrobial |
Metal nanoparticles |
Antimicrobial |
Solar cells |
Aesthetic properties |
Clay nanoparticles |
Electrical resistance |
Chemical resistance |
Fire retardant |
UV shielding |
Nanofiber Technologies
In addition to combining nanoparticles with conventional textiles to enhance their properties, textiles can now be manufactured entirely from nanoscale fibers. Using these nanofibers, researchers have been able to develop fabrics with unique and valuable properties.
Applications of Nanofibers
- Air and water filtration
- Controlled drug delivery
- Tissue reconstruction
- Barrier materials
- Anti-microbial fabric
Nanofiber Fabrication Techniques
Electrospinning
This is a well-established technique for manufacturing polymer fibers. The apparatus consists of a syringe with a capillary needle. A high voltage across the needle creates a charged jet of material, which is spun out into fibers collected on a charged plate.
Electrospinning is one of the most commonly used techniques for making nanofibers that can later be incorporated into meshes and textiles for medical use or for waterproof fabrics.
Split spinning
Split spinning is similar to electrospinning but involves splitting the filament that would form the nanofiber into multiple smaller filaments. This technique is capable of producing very long lengths of fiber with high manufacturing throughput, but it is difficult to produce filaments smaller than a few micrometers in diameter. Research is ongoing to push the capabilities of split spinning into the nanoscale range.
Self-Assembly
This is a biomimetic, "bottom-up" nanofabrication technique that relies on the tendency of materials to assemble into nanoscale structures. By changing the conditions of the nanofiber environment, such as temperature or pH, different nanofibers can assemble together to make more complex structures, resulting in fascinating materials with unique properties. While this kind of process can be difficult to control and each self-assembly protocol is limited to a specific set of materials, it is a valuable technique for both fabricating new materials and enhancing our understanding of nanoscale interactions.
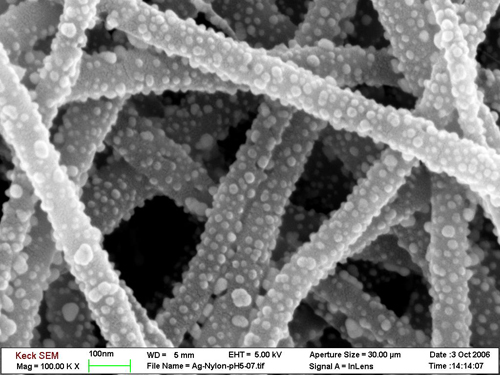
Figure 1. Electrospun nylon nanofibres, coated with antibacterial silver nanoparticles, make an effective sterilizing air filter. Image Credits: Cornell Centre for Materials Research.
Nano-Enhanced Finishing Treatments
Traditionally, many of the application-specific properties given to textiles are obtained at the finishing stage, where chemical or physical treatment of the fibers can change their appearance and improve their resistance to water, chemicals, and abrasion from daily use.
Nanotechnology offers many benefits to these types of processes. Current wet finishing methods, such as dyeing, produce large amounts of contaminated wastewater. Dry finishing processes, like lamination and coating, often consume large amounts of energy, and only so much laminating material can be applied to a piece of fabric without adversely affecting its properties.
Nanoformulations for dyes could greatly reduce the amount of coloring agent needed, reducing the levels of waste produced. Nanocoatings are capable of modifying fabric properties much more drastically whilst remaining flexible and transparent, opening up many applications for treated textiles that were previously difficult to achieve.
Nano-Textile Products
- Sports fabrics with improved mechanical and odor-reducing antibacterial properties
- Medical textiles, such as antimicrobial wound dressings, clothing, and bedding
- PPE (personal protective equipment) with improved chemical or heat resistance
- Military textiles, such as flexible body armor, radio shielding, and camouflage
- Wearable electronics, ranging from conducting fabrics to connect devices together to full portable computers made from nanofibers and flexible circuit boards
Sources and Further Reading
This article was updated on the 29th April, 2019.