Nanomaterials are often utilized to describe the unique characteristics and applications of materials in the nm size range. These materials are being developed to exploit new electronic, chemical, and physical properties compared to the same material lacking nanoscale features.
.jpg)
Shutterstock | whitehoune
Nanomaterials are present in hundreds of products that are already in use, such as anti-bacterial clothing, batteries, and coatings.
The increasing developments and applications of nanomaterials have created several challenges to correctly characterize their physical, chemical, structural, and electronic properties. It is now being recognized that published reports and studies on nanomaterials’ behaviors and properties have largely reported incomplete or inadequate characterization.
Nanomaterials should be fully characterized if researchers want to discover the dynamics of these materials’ properties during formulation, processing, and storage. The characterization methods developed for nanomaterials should be further exploited. For this purpose, suitable application of new and conventional surface sensitive analysis techniques can provide critical data regarding this mysterious characterization.
Nanofillers
The performance of various composites is improved with a subset of nanomaterials called nanofillers. Some of the key features for structural applications of nanofillers comprise of surface functionality, modulus¸ strength/toughness, and dimensions (i.e. aspect ratio and surface area).
When considering interfacial adhesion between the base composite material and nanofiller, surface chemistry is an important factor. For instance, surface energies establish the way that the nanofillers interact with themselves (nanofiller-nanofiller interactions) and with polymers/epoxies (nanofiller-substrate interactions).
Nanomaterials are generally exposed to different surface functionalization processes to improve the adhesion properties at the interface. Accurate measurement of the surface energy values of nanofiller materials is important to ensure effective formulation, development, and characterization of nanocomposites.
Cohesion and adhesion phenomena often describe the filler-matrix interactions. Both properties rely on the materials’ surface energetic condition, which is normally expressed by the surface energy. The nanofiller-matrix interactions can be measured using the adhesion’s thermodynamic work from the surface energy values and associating with composite mechanical properties.
Wad = 2• (γfiller/fiberD•γpolymerD) 1/2 + 2• (γfiller/fiberSP•γpolymerSP) 1/2 |
(1) |
Wcoh = 2• (γfiller/fiberD•γfiller/fiberD) 1/2 + 2• (γfiller/fiberSP•γfiller/fiberSP) 1/2 |
(2) |
In the equations given above:
Wad is the work of adhesion
Wcoh is the work of cohesion
γD is the dispersive surface energy
γSP is the specific surface energy
The Wad/Wcoh ratio indicates the balance of forces between cohesion and adhesion. For example, if interactions between particles are very high, leading to a low Wad/Wcoh ratio and high Wcoh value, then it is likely to result in poor particle dispersion or agglomeration.
If the particle-matrix interactions are very low, leading to a low Wad/Wcoh and low Wad ratio, then it is likely to cause poor particle-matrix adhesion. Formulations should be ideally developed to improve the Wad/Wcoh ratio.
IGC SEA is a well-known tool used to characterize films,1 fibers,2 and particulates.3 The IGC SEA process involves a sorption between known physicochemical properties and vapor (probe molecule) on an adsorbent stationary phase (polyolefin sample) with unspecified physicochemical properties.
This method inverts the traditional association between stationary and mobile phase seen in analytical chromatography. If the interaction is stronger, the surface becomes more energetic and the retention time becomes longer. Due to this a wide range of thermodynamic parameters can be derived from the retention behavior.
IGC has been effectively used to determine the surface energy of a host of nanomaterials, such as carbon nanotubes,4 cellulose nanocrystals,5 graphene,6 nano fibers,7 ultrafine silk,8 and nanoclays.9 In nanocomposites, IGC has been specifically used to measure the surface energy values of nanoclay and carbon nanotube composites with polyurethane.
Please click here if you would like more information on the instrument used in this article or a quote
Case Study
In this analysis, the work of cohesion/work of adhesion ratios achieved through surface energy values, were directly correlated with the mechanical performance of composites. This step was determined through dynamic mechanical analysis experiments. Figure 1 shows dispersive (solid) and specific (shaded) surface energies for a PU film and nanoparticles.
.jpg)
Figure 1. Dispersive (solid) and specific (shaded) surface energies for the nanoparticles and PU film. (Taken from Surface Measurement Systems Case Study 609: Comparing Surface Energy/Thermodynamic Adhesion Values with Mechanical Performance in Nanocomposites.
IGC is a prime technique to measure the surface energy values of nanomaterials compared to contact angle (CA) and atomic force microscopy (AFM) techniques. This is because IGC is a gas/vapor phase method, while CA is a liquid-based method. In practical terms, consistent contact angles on fibers, particles, powders, and porous surfaces cannot be easily obtained.
It is also very difficult to achieve consistent contact angles when the contact angle liquids dissolve or swell into the solid. However, these limitations do not restrict the IGC as it is a gas phase technique and is often used to achieve consistent surface energy values on nanofibers, nanoparticles, and nanocrystals.
For AFM only the small regions of the sample that remain in contact with the AFM tip are used to determine the forces. In such situations, at least hundreds of measurements are required to achieve surface energy values that represent the whole surface. However, the injected vapors or gases in IGC will have complete access to the columns’ entire surface, with surface energy values becoming more representative.
Surface Measurement Systems has developed a new iGC-SEA instrument that employs a special injection system which enables experiments to be carried out across a range of gas or vapor concentrations. Also, the iGC-SEA can precisely control the volume of vapor/gas injected and allows experiments to be performed at precise adsorbate/surface ratios.
This enables the unique ability to measure surface energy distributions in a fast and accurate way and helps to determine the materials’ energetic heterogeneity. However, regardless of the fact that most materials are energetically heterogeneous, both home-built IGC and CA instruments create a single surface energy value.
Conclusion
The IGC technique can be applied as part of the ‘analysis toolkit’ to achieve complete characterization and a better understanding of nanomaterial properties. It can accurately measure surface energy values for a host of nanomaterials, which are important for developing effective nanocomposites.
In addition to measuring surface energy values, IGC has access to a range of bulk and surface properties, such as heats of sorption, Lewis acid-base properties, crosslink densities, diffusion coefficients, and solubility parameters.
References
- Pawlisch, C., Macris, A. and Laurence, R., Macromolecules 20 (1987), 1564.
- van Astem, A. et al, J. Chrom. A 888 (2000), 175.
- Thielmann, F., J. Chrom. A 1037 (2004), 115.
- Zhang, X., Yang, D., Xu, P., Wang, C., and Du, Q., J. Mater. Sci. 42 (2007), 7069-7075.
- IA Sacui, RC Nieuwendaal, DJ Burnett, SJ Stranick, M Jofri, C Weder, EJ Foster, RT Olsson, and JW Gilman“Comparison of the Properties of Cellulose Nanocrystals and Cellulose Nanofibrils Isolated from Bacteria, Tunicate, and Wood Processed Using Acid, Enzymatic, Mechanical, and Oxidative Methods” Applied Materials & Interfaces, 6:6127-6138 (2014).
- Lazar, P., Otyepková, E., Banáš, P., Fargašová, A., Šafářová, K, Lapčík, L., Pechoušek, J., Zbořil, R., and Otyepka, M., Carbon 73 (2014) 448-453.
- Diaz, E., Ordonez, S., and Vega, A., Journal of Physics 61 (2007) 904-908.
- Rajkhowa, R., Kafi, A., Zhou, Q.T., Kondor, A., Morton, D.A.V., and Wang, X., Powder Technology 270 (2015) 112-120.
- Geyer, B., Rohner, S., Lorenz, G., Kandelbauer, A., J. Applied Polymer Science 132 (2015) 41227.
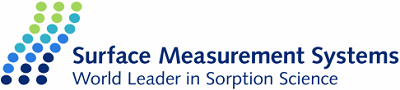
This information has been sourced, reviewed and adapted from materials provided by Surface Measurement Systems Ltd.
For more information on this source, please visit Surface Measurement Systems Ltd.