High-entropy alloys are a promising class of novel engineering materials that potentially possess improved specific strength, corrosion resistance, and fracture toughness when compared to existing structural materials, together with many other distinctive properties [1].
This is likely because of the operation of varied deformation mechanisms, enabling crack bridging as an extrinsic toughening mechanism, for instance [2]. These materials continue to be an active area of research because of their complicated mechanical behavior, and further study is needed for their use as a practical structural material.
.jpg)
One field that still needs more research is processing routes, which involves using plastic strain and heat treatment to obtain a preferred microstructure, similar to other structural metals. Furthermore, just like current duplex steels, a HEA with hard as well as soft phases would be desired. A eutectic alloy [3] is one example of such a material, as is discussed in this article. This HEA is made up of lamellar phases, which have a thickness in sub-micron level.
Therefore, nanomechanical testing techniques are needed to individually assess the mechanical properties of each phase. This article describes the application of in-situ SEM nanoindentation with the Hysitron® PI 88 SEM PicoIndenter® to this material to study the accommodation of plastic strain as a part of investigating processing routes.
In-Situ Nanoindentation on an Advanced Metal Alloy in the SEM
A representative in-situ nanoindentation test video on an advanced metal alloy in the SEM. Synchronized SEM imaging allows for a more detailed analysis of the deformation process during the test, including the evolution of the plasticity and pile-up at the indent periphery.
Experimental Procedure
The high-entropy alloy employed for this study was as cast, and it was prepared by traditional mechanical polishing and a final chemo-mechanical vibratory polish with colloidal silica. With a composition of AlCoCrFeNi2.1, the material was separated into two high-symmetry crystal phases, FCC (L12) and BCC (B2) phases, with approximately 65%–35% volume fraction distribution, respectively [3]. This is demonstrated by electron backscatter diffraction (EBSD) in Figure 1. The two phases as identified by EBSD are indicated in Figure 1a, where the regions marked in green constitute the FCC phase and those marked in red constitute the BCC phase.
.jpg)
.jpg)
Figure 1. EBSD analysis of a portion of the HEA sample: (a) phase map showing the BCC phase in red and the FCC phase in green, and (b) inverse pole figure map showing the orientations within each grain (since both phases are cubic, only one pole map is needed).
In Figure 1c, the inverse pole figure map signifies that the same orientation is maintained with an individual “fiber” of the microstructure, which is an extended lamellar structure. Indentation tests targeting particular parts of the microstructure were conducted through in-situ SEM using the Hysitron PI 88 fitted with a Berkovich geometry probe in load control, with partial unload indents to determine the depth dependence of the properties. The indentation testing was carried out at tilt to enable visualization of the test, and the optional rotation and tilt staging of the Hysitron PI 88 was used to re-adjust the specimen, post-mortem, with the electron column for backscatter (BSE) imaging as well as phase identification of the indent locations.
Results
Regions that indicated various parts of the materials microstructure were chosen for the in-situ SEM indentation. Shown in Figures 2 and 3 is the comparison of three example indentation regions. In Figure 2, post-indent imaging is shown for these areas, in secondary electron mode and backscatter electron mode, both from a tilted view and a top view, respectively. Region 1 is within the minor BCC phase, which looks somewhat darker when compared to the FCC phase. Region 2 is a combination of the two phases, whereas Region 3 is primarily within the FCC phase.
In the post-indent imaging, slip steps are not obvious in Region 1, while they do appear clearly in Regions 2 and 3 within the FCC phase. This is acceptable, as slip by dislocation is supported more easily in the FCC crystal structure. It can also be seen in Regions 2 and 3 that the slip steps accumulate against the neighboring BCC phase boundary.
.jpg)
Figure 2. Post-indent imaging of three regions of the HEA microstructure, with backscatter imaging and secondary electron imaging from the top and from a tilted perspective. The regions are divided by rows and marked on the left.
.jpg)
Figure 3. (a) Low depth portion of the load-displacement curves for the three regions of interest and (b) hardness versus depth from the analysis of the curves in part (a).
The hardness data in Figure 3 is associated with the propensity to create slip steps from the images in Figure 2. In Region 1, the hardness is comparatively constant with depth at ~10 GPa. In Region 2, the hardness is analogous to Region 1 at the lowest depths, which is tolerable as the core portion of the indent is in the BCC phase. However, with the increase in depth, the hardness decreases as increasing amounts of FCC phase are included in the plastic zone of the indent. The hardness reaches that of Region 3, which is largely within the FCC Region. This has a fairly stable hardness of around 6 GPa. These observations are reliable with TEM analysis of cold-rolled material, where it was noticed that the BCC phase larely retained its structure, while the FCC grain structure deformed around it [3].
Conclusions
In-situ SEM indentation is a robust tool for characterizing the mechanical properties of individual portions of the microstructure in emerging alloys. In this article, backscatter and EBSD were integrated into the nanoindentation analysis using the rotation and tilt stages of the Hysitron PI 88. These additional data helped to infer the measured hardness and observed slip steps in the post-indent imaging. For this alloy, the relative hardness of the phases and the accumulation of dislocations at the phase boundary play a vital role in establishing the plastic deformation of the bulk material.
References
[1] M.-H. Tsai, J.-W. Yeh, Mater. Res. Lett. 2 (2014) 107–123.
[2] Z. Zhang, H. Sheng, Z. Wang, B. Gludovatz, Z. Zhang, E.P. George, Q. Yu, S.X. Mao, R.O. Ritchie, Nature Comm. 8 (2017).
[3] I.S. Wani, T. Bhattacharjee, S. Sheikh, I.T. Clark, M.H. Park, T. Okawa, S. Guo, P.P. Bhattacharjee, N. Tsuji, Intermetallics 84 (2017) 42–51.
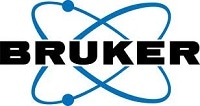
This information has been sourced, reviewed and adapted from materials provided by Bruker Nano Surfaces.
For more information on this source, please visit Bruker Nano Surfaces.