Article updated 11th December
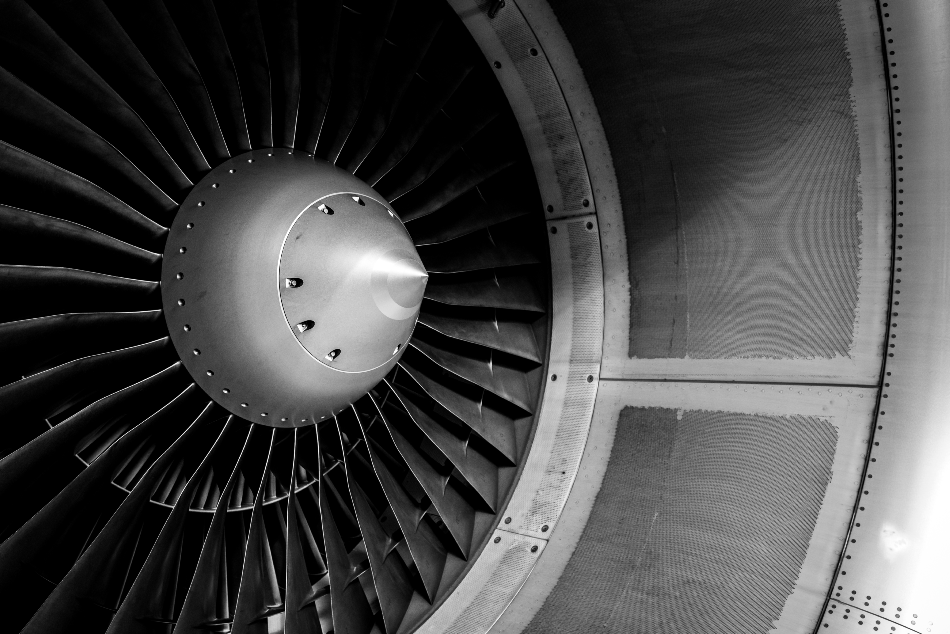
Bychykhin Olexandr / Shutterstock
The aerospace industry has always been an early adopter of the latest technological inventions, and at a time when they are under increasing pressure to improve their environmental credentials, they are in prime position to take advantage of additive manufacturing.
The technique, also known as 3D printing, builds objects up from a computer-aided design model, layer by layer. The most widespread method builds items layer wise on a powder-bed, selectively melting powder particles with a laser or electron beam.
The aerospace industry - which includes the military and security industry, as well as the space sector and air transportation – is focused on complex, low volume production. It is, however, hampered by environmental performance and concerns, high manufacturing costs and competitive market conditions, which additive manufacturing can overcome.
Complex Shapes
Additive manufacturing can create complex shapes with complicated internal dimensions and intricate geometries, it can shorten the design processes and make shapes previously thought impossible. No longer is industry limited by mathematics and what is possible with other methods of manufacture as additive manufacturing offers superior design in terms of geometries and increased innovation and design.
One of the big engineering challenges is to create complex shapes without compromising its shape; if a hollow object is required, this must often be created with multiple parts joined together. This can be time consuming and restrictive in terms of what objects can be created; furthermore, it can cause weak spots at the joints. Additive manufacturing can overcome these issues to create complex yet strong shapes, thus decreasing the number of subcomponents in a system, and the cost and time taken to manufacture them.
Weight Loss
In an industry where weight is an important factor, additive manufacturing is a quick, flexible and economical process that can decrease the weight of components such as engines and turbines, air conditioning units, buckle belts, heating elements and cockpit equipment. The technique utilizes alternative materials, such as metals and plastic, to reduce weight. In the case of laser sintering, it can decrease the total weight of a component by between 40% and 60%.
The knock-on effect of this is that the aircraft will use less fuel and therefore less CO2 is produced and released into the atmosphere. If 1kg were removed from every aircraft of a fleet of 600, around 90,000 liters of fuel would be saved, and 230 tons of CO2 would not be released.
It is also especially important in the space sector, where parts need to be intricately designed to minimize packaging space and weight.
The technique also challenges the dilemma between scale and scope; it reduces capital to achieve economies of scale – one printer can build several complex parts with variable designs without the need for assembly lines.
Quicker Design
Not only that, additive manufacturing can shorten the design process and time to market. Rapid prototyping and conceptual design review and validation mean multiple configurations can be tested for preference and tweaks can be made in the computer program quickly without weeks of recalculation and reconfiguring. It’s also good for the one-off production of demonstration units and low volume production.
The speedy nature of the process also means that there is no longer the need to stockpile high quantities of components or buy in bulk from suppliers just in case something breaks or malfunctions. The technique allows components to be created on demand and on site, and, if necessary, be modified. This negates the need for large storage areas or warehouses and allows for single components to be made one at a time.
Conclusion
It is highly likely that additive manufacturing will become increasingly useful over time, and that the aerospace industry will be just one of many industries that can utilize its power to manufacture cheap, lightweight components. In addition to creating items with complex geometries, the technique can lower the cost of manufacturing and help reduce the damage the industry contributes to the environment.
Sources
Disclaimer: The views expressed here are those of the author expressed in their private capacity and do not necessarily represent the views of AZoM.com Limited T/A AZoNetwork the owner and operator of this website. This disclaimer forms part of the Terms and conditions of use of this website.