Titanium and its alloys have been intensively investigated in biomedical applications including artificial joints, because of their excellent resistance to corrosion, elastic modulus characteristics, strength, and biocompatibility. Tribological parameters are low for these alloys, however, this makes them unsuitable for alloys used in artificial joints. Many methods have been trialed to improve tribological performance, such as ion implantation and physical vapor deposition.
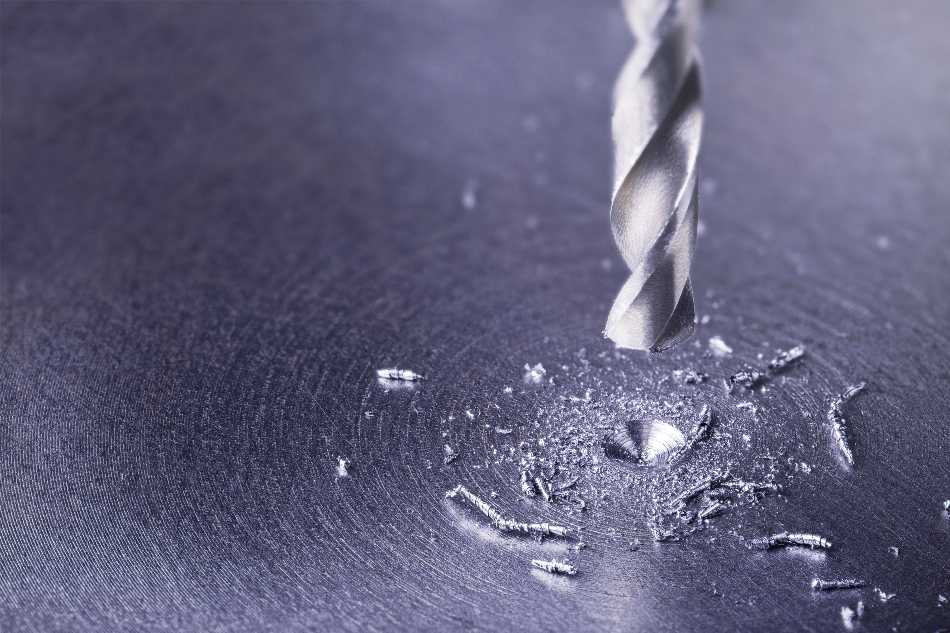
ImageCredit/Shutterstock: Evkaz
Among these materials, titanium carbide is a hard-refractory ceramic material appearing as a black powder, in the form of a face-centered cubic crystal-like sodium chloride (common salt). Its elastic modulus is about 400 GPa, while the shear modulus is 188 GPa.
Aluminum – the good and the bad
Aluminum alloys have generally been preferred in many industries, including aerospace, automobile, defense, and marine industries since the 1930s, as they are strong for their weight and have good corrosion resistance. They are classified as heat-treatable or precipitate-strengthened alloys, and non-heat-treatable or solid solution hardened alloys. They make vehicles of all kinds more fuel-efficient by reducing the overall weight and hence the drag, on the engine and battery. For instance, reducing the automobile weight by 10% boosts fuel economy by about 6-8%.
Aluminum alloys are stronger at lower temperatures, below zero, which makes them more useful. However, at very high temperatures they weaken.
These alloys are notoriously difficult to weld. This is due to their microstructure, which makes them refractory to solidification and subject to hot cracks during fusion welding, as well as the porous nature of the fusion zone. Thus, fusion welding techniques cannot be used as this then causes them to lose their mechanical strength.
On the other hand, friction stir welding allows pieces to be joined in the solid-state, preserving the properties of the alloy, however microstructural changes occur that accelerate the onset of corrosion. It is also completely mechanized, which limits its application to complicated weld shapes where space is limited. Moreover, the need for workpiece restraint in a good setup makes it difficult to use in complicated welds.
AA 7075
Aluminum alloy AA7075 is a thin light metal that is comparable to steel for strength, though only a third of its weight. It is composed of 90% aluminum, roughly 6% magnesium, 2.5% zinc, 1.6% copper and less than 0.3% chromium. Therefore, it has been extensively used to make the fuselages of airplanes and wings, where welding is not required. Instead, parts are bolted or riveted together. Other areas of use without welding include the frames of smartphones and the carabiners used in rock climbing.
The problem
The welding performance of AA 7075 is poor under the type of welding that is normally resorted to in automobile manufacture. The heat generated during welding causes the elements comprising the alloy to flow unevenly. This phenomenon, known as phase segregation, inhibits the flow of the liquid metal during cooling. The metal will shrink and cause cracks to form along the weld as it cools.
The solution
Engineers have found a solution to this long-drawn search. They discovered that by infusing titanium carbide nanoparticles into the AA 7075 welding wires that serve as the filling material at the welding joint, they can use arc welding to create AA 7075 joints without hot cracks.
In the current process, 1.7 percent by volume of 40–60 nm TiC nanoparticles were infused into AA7075. Since the nanoparticles are dispersed into an aluminum matrix as they are introduced into the melt pool during the welding process, there is a more efficient transition of these reinforcing elements into the melting zone.
TiC nanoparticles and phase control
The secret is the use of a nanoparticle-enabled phase-control element during welding. The nanoparticles prompt a more uniform solidification of the elements in the molten metal alloy, causing the phases to remain together, preserving its strength.
This prevents the uneven flow of the heated elements, preventing phase segregation and thus preventing cracking so that the alloy retains its strength.
Conventional fillers vs TiC-infused fillers
With conventional aluminum filler alloys, such as ER5356, the melting zone solidifies first, before the adjacent partially melted zone. As a result, the solid part of the melt pool elements is larger than the solid part of the pure AA 7075 in the partially melted zone. The weakened partially melted zone is pulled towards the middle of the melt pool, causing liquation cracks to occur.
With the use of ER5356, solidification cracking relieves this stress and prevents this mode of failure. But with the use of TiC, the solid fraction curve smooths out indicating that there is a continuous grain growth up to the last stages of solidification, at which point solidification cracking occurs.
A second advantage is the delay of about 120 C in the onset of secondary phase nucleation, which acts along with the reduced growth of alpha grains to improve the flow pattern of the liquid melt pool throughout the solidification process of the melting zone.
The TiC slows the progress of solidification, reduces the speed at which the dendritic grains grow from the interface of solid and liquid metal, and allows an area of increased undercooling to form. The absence of dendritic grain growth in a directional manner is a huge advantage in preventing hot cracking during welding of susceptible alloys.
Moreover, at this point, heterogeneous nucleation occurs due to nanoparticles. The aluminum grains nucleating at the surface of the nanoparticles show a complete epitaxy.
Avoiding hot cracking
TEM (transmission electron microscopy) and SEM (scanning electron microscopy) analysis of the joints welded in this manner at the atomic level shows they have fine globular grains and the secondary phase undergoes modification. TiC nanoparticles tend to associate with the secondary MgZn2 phase, altering its properties for better welding characteristics. These two factors make hot cracks unlikely.
High tensile strength
At the same time, they have a very high tensile strength, both in the welded condition and after post-weld heat treatment. The alloy can be welded to produce a material that has a tensile strength of up to 302 mPa at the joints. Moreover, the researchers suggest that refinements or adaptations to the technique such as post-welding heat treatments could make the welded AA 7075 joints as strong as 551 mPa, similar to that of steel.
The microhardness testing of these samples shows that the melting zone created during welding is completely heat treatable and is even harder than the base material as a result of the reinforcement performed by the TiC nanoparticles. With heat treatment, the fracture occurs far away from the melting zone and the partially melted zone, showing that the welded joint is probably just as strong as the unwelded material.
Compare this to its nearest competitor, aluminum AA6061, found in many dozens of aircraft and automobile joints, which has a tensile strength of about 186 mPa in welded joints.
Conclusion
The new technique is just a simple twist, but it could allow widespread use of this high-strength aluminum alloy in mass-produced products like cars or bicycles, where parts are often assembled. Companies could use the same processes and equipment they already have to incorporate this super-strong aluminum alloy into their manufacturing processes, and their products could be lighter and more energy-efficient, while still retaining their strength.”
Xiaochun Li
The technique described above is being used currently to develop bicycle frames using the AA 7075, but the use of TiC nanoparticle-infused filler wires could make it an invaluable method to join other metals that are refractory to ordinary welding.
Sources
Disclaimer: The views expressed here are those of the author expressed in their private capacity and do not necessarily represent the views of AZoM.com Limited T/A AZoNetwork the owner and operator of this website. This disclaimer forms part of the Terms and conditions of use of this website.