Since the first nanoceramics were developed in the 1980s, there has been huge excitement about the application and use of this increasingly diverse technology. Nanoceramics are ceramic materials fabricated from ultrafine particles less than 100 nm in diameter. This is a somewhat arbitrary value but was chosen because in this size range the first signs of “surface effects” and the other unusual properties found in nanoparticles appear.
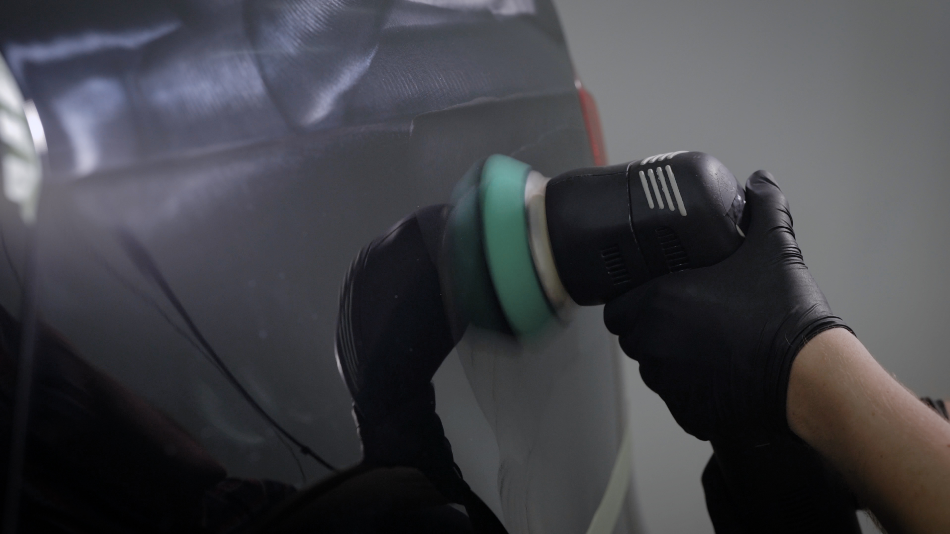
ImageCredit/Shutterstock:Usoltsev Kirill
The effects are directly related to the small size of these particles as when materials are produced from nanoparticles, a substantial number of atoms are exposed on the surface. Ceramic nanoparticles have proved themselves to be highly stable in comparison to metallic ones and their production tends to be cheaper. Much research has been undertaken to widen the range of nanoceramic materials available and to find novel applications for their use.
Properties
Most people associate ceramics with traditional fired pottery made from minerals such as clay, but because of their unique properties, hardness, relative inertness, and low thermal and electrical conductivity, ceramics have always had wider industrial use. Modern and advanced ceramics use high performing materials such as aluminum oxide and silicon carbide. However, it has been shown that the performance and behavior of materials are altered significantly when constructed from a nanoscale. The hardness and strength of ceramic material are just two examples of enhancements that occur when composited from nanoparticles.
Methods of Production
Different methods of production tend to be suitable for various nanoceramic materials. There are currently many different nanoceramics in use, but this is still growing as new or cost-effective methods of production are being discovered. The range of nanoceramic materials can be categorized into two basic types, either oxide or non-oxide and in each case, the particle size for a specific application might differ.
Oxide ceramic nanoparticles such as silica, alumina, titania, zirconia, have all been produced with improved properties. Silica nanoparticles have been used for biomedical applications, such as in vivo pharmacokinetic studies of drugs, high payload targeted delivery and new therapies because of their biocompatibility, low toxicity, and scalable synthetic availability. Although Silica can be found in natural sources, it contains impurities. Synthetic silica nanoparticles forms are colloidal silica, silica gels, pyrogenic silica, and precipitated silica and they can be produced as pure powder and amorphous forms. It is important to control silica particle size, porosity, crystallinity, and shape to tune the nanostructure. The ability to do this with these particles makes them especially useful in these applications.
Silica nanoparticles can be created using a “top-down” or physical approach, starting with larger particles, gradually reducing them by grinding or similar. They can also be produced using a “bottom-up” or chemical approaches such as the earliest Sol-gel method which allows control over the particle size and size distribution.
Silicon Carbide
A non-oxide based nanoceramic such as silicon carbide has been proposed as one of the four layers of isotropic material coating the fuel kernel of the TRISO micro fuel particle used in Generation IV nuclear reactors. This lightweight material maintains chemical and dimensional stability in challenging environments at temperatures up to 3000 C. It is chemically inert and widely used as a semiconductor material in electronics because of its high thermal conductivity, high electric field break down strength, and high maximum current density, making it more desirable than silicon. In 2015 a team led by researchers from UCLA created a super-strong yet light structural metal with extremely high specific strength and stiffness-to-weight ratio by infusing magnesium with a dense and even dispersal of nanoceramic silicon carbide. It could reduce the weight of airplanes, spacecraft, and cars, helping to improve fuel efficiency, as well as in mobile electronics and biomedical devices.
Applications of nanoceramics
An example of how new nanoceramics are becoming available is highlighted by the recent discovery by chemists at the Max-Planck-Institut für Kohlenforschung in Mülheim an der Ruhr who found a way to produce corundum (also known as alpha-alumina), a very stable variant of alumina, in the form of nanoparticles using simple mechanical method in a ball mill.
The resulting particles could be used as a resistant carrier material in automotive catalysts or as a starting material for particularly hard ceramics, making them useful in dental implants or even grinding tools. The researchers can make a powder of the corundum nanoparticles by simply grinding lumps of boehmite, aluminum oxyhydroxide, in a ball mill for 3 hours and then heating them for a short amount of time. Previously, chemists could only produce corundum from other aluminum oxides or hydroxides if they fired them at temperatures higher than 1200°C or pressurized them at milder temperatures of 500°C for weeks.
A company is already working on large-scale production of nanocorundum using the Mülheim process.
Sources
http://newsroom.ucla.edu/releases/ucla-researchers-create-exceptionally-strong-and-lightweight-new-metal
https://www.researchgate.net/publication/283293210_Ceramic_Nanoparticles_Fabrication_Methods_and_Applications_in_Drug_Delivery
https://www.researchgate.net/publication/289652513_Ceramic_nanoparticles_What_else_do_we_have_to_know
https://www.sciencedaily.com/releases/2019/10/191030120328.htm
https://www.sciencedirect.com/topics/engineering/ceramic-nanoparticles
Disclaimer: The views expressed here are those of the author expressed in their private capacity and do not necessarily represent the views of AZoM.com Limited T/A AZoNetwork the owner and operator of this website. This disclaimer forms part of the Terms and conditions of use of this website.