A borehole is a narrow shaft drilled into the ground, either vertically or horizontally. It is constructed for different purposes, such as the extraction of water, petroleum, and gases, etc.
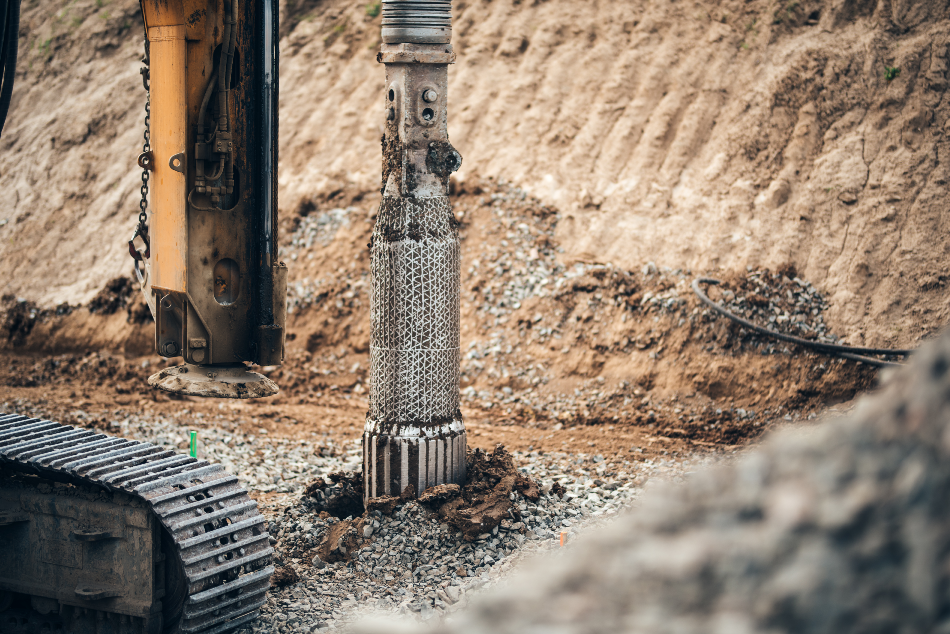
Image Credit: Bogdanhoda/Shutterstock.com
Drilling for oil and gas involves drilling a narrow hole from the surface of the earth to the reservoir, which can be kilometers under the earth’s surface. The mechanism of drilling involves the use of a drilling bit which is connected to a long string of drill pipes. On application of weight and rotation on the bit, the bit crushes the rock into small pieces. Drilling fluid is introduced and circulated from the surface, through the drill pipe to the bit face. The pressure of the drilling fluid lifts the fragmented pieces (cuttings) and brings them to the surface, where separation equipment remove the fragments from the drilling fluid. This circulation takes place with the help of powerful pumps.
Challenges in conventional borehole drilling and characteristic properties of nanomaterials that help mitigate them:
Where nanotechnology has developed nanomaterials with specific characteristic properties, it has helped to overcome the technical and environmental challenges faced during borehole drilling by drilling companies. Some of the problems contributing to financial losses on overall drilling processes are drag and torque reduction, formation consolidation, gel formation, erosion, pipe sticking, reduction in the circulation of drilling fluids, and high-energy consumption.
The viscosity, density and the gelling strength of the drilling fluid are the main factors that determine the functional specifications of a drilling fluid. Scientists have conducted extensive research and developed nano-based drilling fluids with rheological, thermal, mechanical, magnetic, and optical profiles. This drilling fluid possesses a flat type gel strength property with optimal yield stress values. This property provides great potential for better cuttings suspension and improved capacity for lifting the cuttings of drilling fluids.
For commercial applications, the nano-based drilling fluids are optimized in different temperatures and other physical factors. The incorporation of magnetic nanoparticles as drilling fluid additives, indicate a promising development of smart drilling fluids with in-situ rheological controllability upon application of an external magnetic field.
The drilling equipment coated with nanomaterial has better strength, longevity, and flexibility with lighter weight drilling components. The longevity of the drilling equipment is enhanced mainly due to anticorrosion, adhesive, and wear resistance properties of nanoparticles. Nanoparticles can prevent bio-fouling.
Nanofluids and nanomembranes have reduced pipe sticking problems. Nano-based drilling fluid has good thermal conductivity, better heat transfer efficiency, and improved fluid stability. Every year borehole drilling companies suffer millions in losses due to wellbore instability problems due to the exposure of shale to drilling muds. Nanofluid can prevent drilling mud invasion, separating mud filtrate, and the formation of water. This is due to the ultra-small size of nanoparticles, i.e., the particle size is smaller than the pore size of shale which prevents plugging the pores. Therefore, nanofluid decreases the exposure of shale to drilling muds, which avoids swelling and wellbore instability.
The increase in torque and drag problems in the process of borehole drilling is due to the friction between the drill string and the borehole wall. Micro and macro material-based drilling muds have less ability to reduce torque and drag problems. Nanomaterials can develop extremely fine and very thin film/coatings. Nano based fluids reduce the frictional resistance between the pipe and the borehole wall because of the formation of a thin lubricating film in the wall-pipe interface.
Conclusion:
This article focuses on how nanotechnology research has improved borehole drilling operations. The ability to synthesize custom-made nanoparticles by changing their surface properties or by optimizing their terminal units to attain specific functional tasks, promises to significantly benefit the drilling industry.
Sources:
https://nano-magazine.com/news/2019/4/27/nanotechnologys-potential-in-the-mining-industry
lyasiri, M. S. and Al-Sallami, W. T. (2015). How the drilling fluids can be made more efficient by using nanomaterials. American Journal of Nano Research and Applications, 3, 41-45.
Amanullah Md. and Ramasamy J. (2018). Potential Application of Nanomaterials in Oil and Gas Field Drilling Tools and Fluids Design. Journal of Chemical Engineering, 12, 96-110 doi: 10.17265/1934-7375/2018.03.003
Disclaimer: The views expressed here are those of the author expressed in their private capacity and do not necessarily represent the views of AZoM.com Limited T/A AZoNetwork the owner and operator of this website. This disclaimer forms part of the Terms and conditions of use of this website.