Particle size is a critical quality attribute (CQA) in liposome and lipid nanoparticle (LNP) drug-delivery applications that affects bioaccessibility, biodistribution and retention time. Real-time feedback on particle size during production eliminates waste while reducing dependence on deep process knowledge.
Microfluidization is a frequent method for large-scale production of liposomes within a clearly defined size range. The subsequent particle size relies on many process parameters, such as temperature and chamber pressure, which can drift over a period of time.
Existing on-line and off-line control methods do not take samples from the entire lot, which may hide pockets of out-of-spec material. Real-time multi-angle light scattering (RT-MALS) makes sure each batch is consistent by in-line monitoring for size of the whole batch; the production stream can be redirected to waste if the particle size falls out of specification.
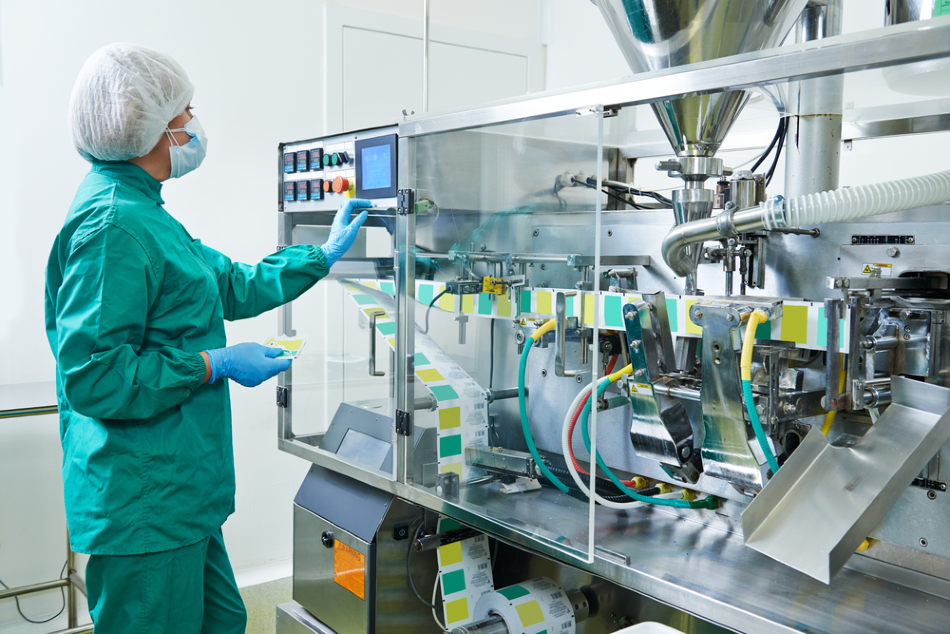
Image Credit: Shutterstock.com/DmitryKalinovsky
Methods and Materials
Crude liposome solution containing heterogeneous liposomes with sizes from 150 nm to 800 nm was sent through a microfluidizer. The internal chamber pressure was held at 8,000 psig at first, then modified to 11,000 psig after 25 minutes to simulate an unwanted drift in the manufacturing process.
After leaving the chamber, the solution passed through the ultraDAWN™ RT-MALS instrument at a flow rate of 4 mL/min. A lag time (RTD, residence time delay) of just 22 seconds occured between the time product leaves the chamber and time of measurement. OBSERVER™ software was programmed to gather ultraDAWN™ data, measure z-average radius 30 times per minute, and trigger the exit stream to divert if particle size varied by 2 nm from the nominal CQA value.
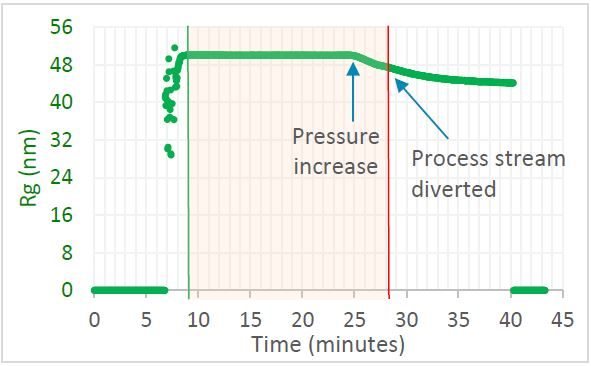
Figure 1. Trace in OBSERVER software of radius of gyration measured by ultraDAWN, indicating deviation from specification when the pressure drifted. Image Credit: Wyatt Technology
Results and Discussion
Liposome Rg was found to be 50 nm, constant to within 0.5%, as long as the chamber pressure was maintained at 8,000 psig. The size was reduced when the internal chamber pressure was increased to 11,000 psig. OBSERVER™ was successful in triggering the process stream to divert when the size decreased to under 48 nm.
Employing the standard procedure of final QC testing by itself, the complete batch would have been rejected; with RT-MALS-based monitoring and control, only about half the batch was rejected and the rest, which was collected, met specification.
Catching the issue also led to re-calibration of the chamber before starting the following batch, averting further losses.
Conclusions
In-line RT-MALS contributed significantly to this liposome production process, cutting waste of valuable product and drawing the attention of the production staff to the necessity of system maintenance.
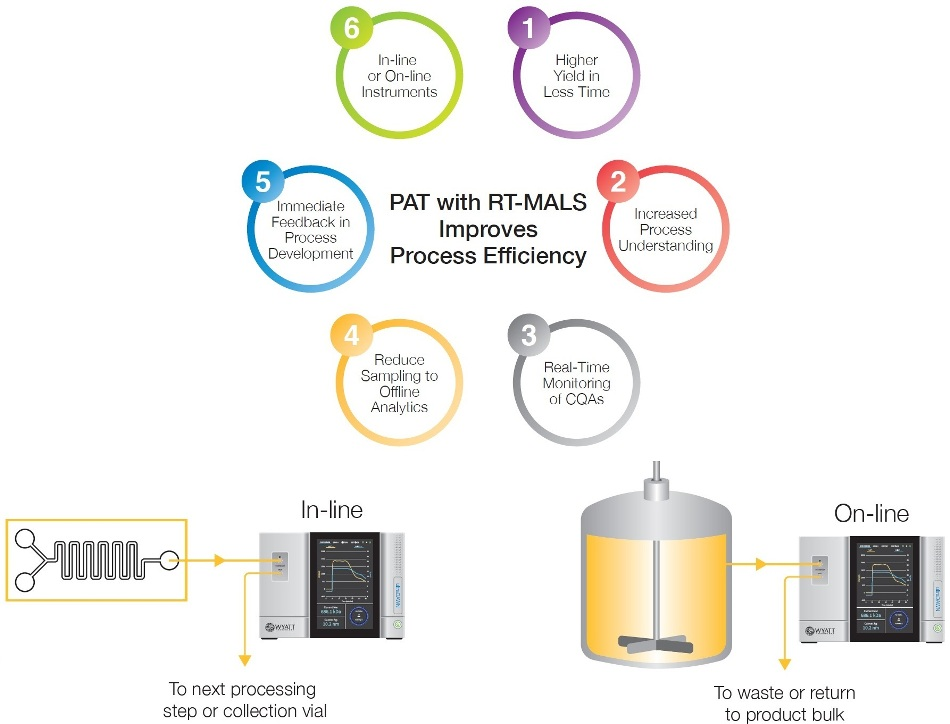
Image Credit: Wyatt Technology
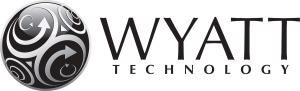
This information has been sourced, reviewed and adapted from materials provided by Wyatt Technology.
For more information on this source, please visit Wyatt Technology.