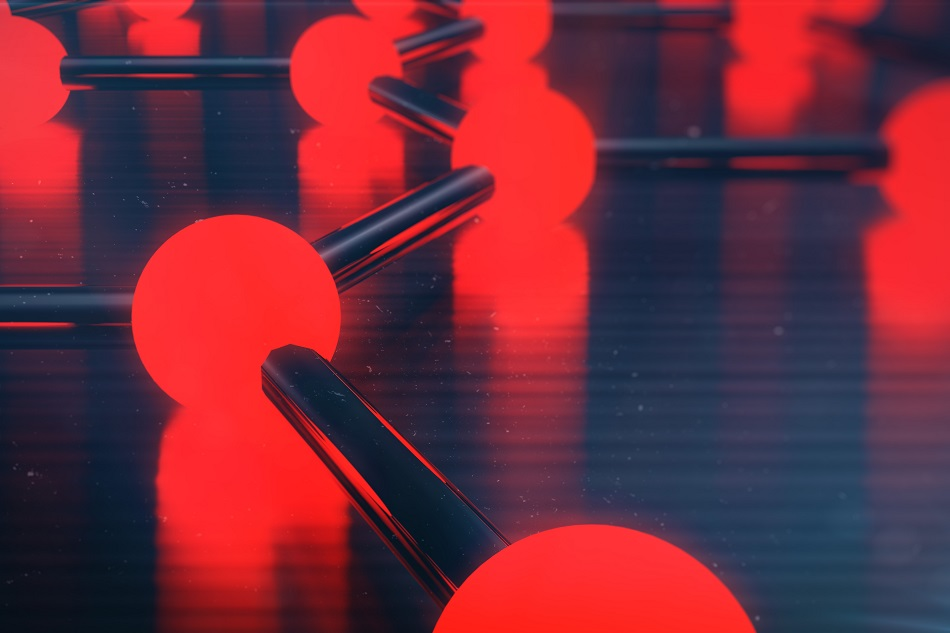
Image Credit: Rost9/Shutterstock.com
The rGO technique and its related processes have their foundations in the Brodie method, which later became the Hummers method. Variants of the technique then developed on from the Hummers method.
The rGO technique uses graphite as a feedstock that is mixed with sulfuric acid to serve as an intercalating agent, with potassium permanganate as an oxidant.
Graphene oxide (GO) is produced when this mixture is heated at high temperatures. Graphene oxide is a graphene material in its own right and is decorated with oxygen on its surface. Graphene oxide can also be reduced (the process of removing a large amount of a material’s oxygen content) to graphene both chemically and thermally, with further steps of sonication, rinsing and dispersion.
Before you can make rGO, graphene oxide must be made first. To make graphene oxide, you have to start with graphite oxide, and once you have this, there are three approaches to the reduction methods to produce rGO thereafter. These approaches can be thermal, chemical, or electrochemical.
Reduction Methods
The approaches to the reduction of oxygen in graphene oxide are varied, and include high temperature treatment (>1000 C), chemical reduction, and optical- or microwave-assisted reduction.
Thermal Annealing
In thermal annealing, graphite oxide is rapidly heated to trigger a sudden expression of carbon monoxide and carbon dioxide gases between the sheets of graphene. This process separates the material to create exfoliated graphene.
Although this process offers the benefit of not needing another reduction step, the heating process does cause significant damage to the graphene. Some estimates suggest that as much as 30 percent of the graphene is destroyed during the thermal annealing process.
An alternative method is to carry out the thermal reduction after the graphite oxide has been exfoliated into graphene oxide. The process requires extremely high temperatures in excess of 700 C, but leads to good results despite the costs for the high energy levels needed for the process.
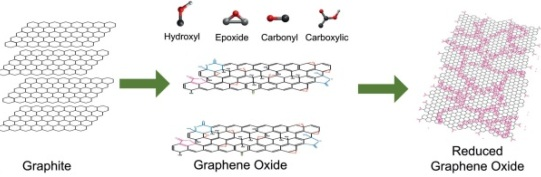
Figure 1. Graphene Oxide Synthesis and Reduction. Graphite can be oxidized with different procedures in the presence of strong acids. The GO flakes are functionalized with epoxy and hydroxyl groups both above and below the horizontal surface, and at the edges. A partial recovery of the electronic properties can be reached following a reduction treatment. Source: Materials Today, December 12, Vol. 15, No. 12
A number of defects are introduced into the lattice structure of graphene because of the rGO process. Additionally, the process also leads to chemical inhomogeneity, which affects the reproducibility between batches. Similarly, this form of material is difficult to characterize.
However, rGO does possess some benefits. It is possible to get down to a single layer of graphene, the material is able to disperse well in a range of solvents, and it is possible to achieve high yields.
Scalability and Market Position
The rGO technique is both simple and highly scalable. Although there are a number of different approaches to the technique, two issues are present among all of them. Firstly, the process subjects the graphene lattice to permanent damage, and secondly, it requires additional processing steps, which adds to the overall cost of the procedure.
The reduction process does not remove all the groups that attach themselves to the surface of the graphene, and removing oxygen from the graphene leaves gaps within the lattice structure, which has detrimental effects on the electrical and optical properties of the graphene produced by the reduction process.
Because of this, rGO graphene cannot find application in high-end electronic or optical devices. For instance, rGO graphene does not have the sheet resistance that is necessary to replace or be an alternative to the indium tin oxide (ITO) used in touch-screen displays. Although thermal reduction techniques can improve rGO’s performance in this application, it is no competition to ITO when considering its performance.
Cost is also an important factor to consider in the rGO reduction process. The need for both an oxidation and a reduction step builds the costs associated with the process and puts rGO at a disadvantage when competing for low-value and high-volume applications. These costly extra steps will also mean that it will be difficult for rGO to be used as a substitute for common forms of carbon (e.g. carbon black) in many applications.
Summary
Overall, the costs associated with the rGO reduction process and the performance characteristics of rGO do limit its success in some applications. As the rGO process grows, scaling up to high-volume production will reduce the costs of the process.
As with all forms of graphene, material that may not be suited for one application will be ideally suited for another. Graphene Oxide (GO) and reduced Graphene Oxide (rGO) are perfect examples of this dynamic for different forms of graphene materials being suited for particular applications.
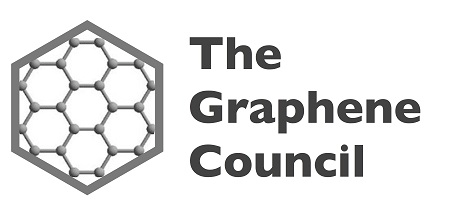
This information has been sourced, reviewed and adapted from materials provided by The Graphene Council.
For more information on this source, please visit The Graphene Council.