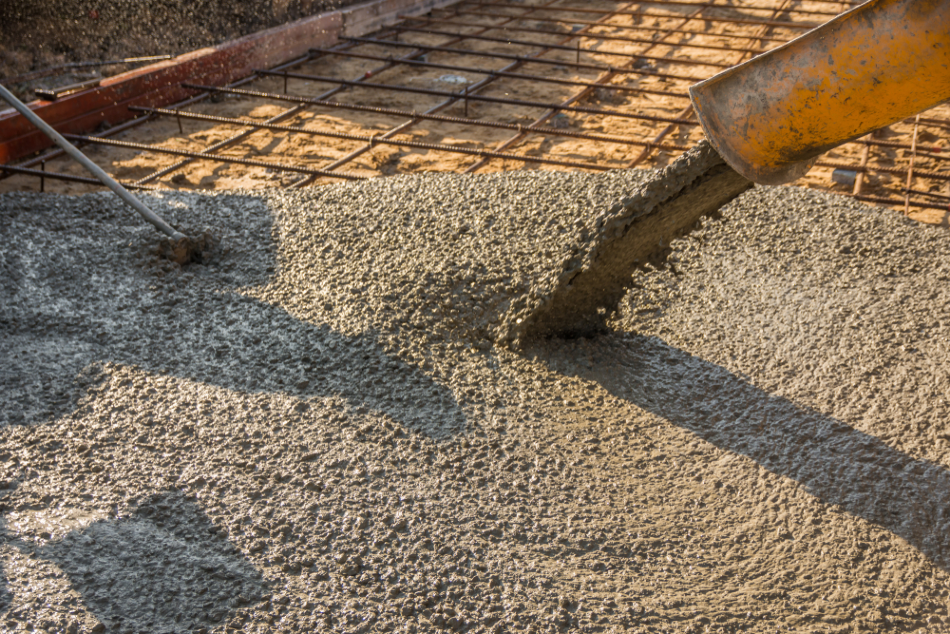
Image Credit: Nopphinan/Shutterstock.com
Various types of nanotechnology have enhanced the performance capabilities of cement and concrete used within the construction industry.
An Overview of Nanotechnology in Construction
By definition, nanotechnology is the application of materials that are typically 100 nanometers (nm) or less in size. Although some of the most notable applications of nanotechnology are found within the fields of electronics, energy harvesting and medicine, this exciting technology has also been widely used throughout the construction industry. More specifically, nanotechnology can be applied to almost every component within the construction industry, some of which include the design and development of high-performance concrete (HPC), functionalized concretes and coating materials.
Nanoparticles as Cement Additives
Some of the most common types of nanotechnology that have been used as cement additives include nano-silica (NS), calcium carbonate (CaCO3) nanoparticles, titanium dioxide nanoparticles (NT), various carbon nanostructures, polymers and coatings.
Nano-silica
Since the 1960s, researchers have researched the usefulness of incorporating silicon dioxide, otherwise referred to as silica, into cement. Since then, several different types of silica have been used as cement additives, including silica fumes (SF), amorphous polymorphs of silica dioxide, and NS.
Typically, NS has an average size below 120 nm. As compared to SF, NS is associated with a superior pozzolanic effect and can also serve as nucleation sites and enhance the density of interfacial grain zones, improving the overall strength of cement.
Despite its advantageous properties, NS can agglomerate within cement and cause detrimental effects, including enhanced pore formation associated with reduced chloride ion penetration and lower cement lifetime, as well as an overall reduction in the strength of the cement material.
Low NS loadings can also fill concrete pores. Therefore, NS is often added to cement with a high superplasticizer percentage, which reduces porosity and capillary water absorption upon the introduction of NS into the cement.
Overall, a maximum content loading of approximately 1.25% of NS, nano-iron oxide (NF) and/or nano-alumina (NA) is associated with benefits to the cement. Higher concentrations of these cement/water/superplasticizer mixtures are associated with detrimental effects on the compressive strength and porosity of the cement.
CaCO3 nanoparticles
When incorporated into Ordinary Portland Cement (OPC), CaCO3 nanoparticles within the size range of 50 nm to 120 nm accelerate the hydration rate. CaCO3 nanoparticles are also often mixed with fillers, such as fly ash, to compensate for the hardness that fillers often introduce into cement.
What nanoparticle production systems are available on the market today?
Titanium dioxide nanoparticles
Like many other types of nanoparticles, NT is used to increase the mechanical properties of cement. NT also contributes to the surface contact angle reduction of water in concrete materials.
Since the surface of concrete is hydrophobic, it is believed that these materials exhibit self-cleaning properties. As a result of this hydrophobicity, water that reaches the surface of concrete will leave, allowing any dust particles that have been absorbed onto the surface to be transported elsewhere as the water moves.
Find out more about the diverse nanomaterials available on the market today
Carbon nanostructures
Various types of carbon nanostructures enhance the properties of cement. Cement pastes, for example, have been doped with several different carbon allotropes that have had widespread effects on the intrinsic properties of the cement. For example, a mixture containing 3% of single-walled or multiple-walled carbon nanotubes (CNTs) increases the strength of OPC by 50% and the Vickers hardness by as much as 600%.
Despite the advantages associated with CNTs in cement pastes, further work is needed to evaluate the proper method of dispersing these nanostructures into the cement.
Polymeric additives
The goal of incorporating nanopolymers into cement materials is to increase the elastic modulus by binding to defective sites and silicate chains within the cement. Some of the different grafting polymers investigated for this purpose include hexadecyltrimethylammonium (HDTMA), polyethylene glycol (PEG), polyvinyl alcohol (PVA), poly-dimethyl acrylamide (PDMA), polyacrylic acid, and methylene blue.
Coatings
Tribocorrosion is the degradation of materials caused by the combination of mechanical, chemical and/or electrochemical interactions between two surfaces that are in relative motion. If a material experiences tribocorrosion, irreversible transformation and subsequent damage of the materials arises, hindering the ability of these materials to function correctly. To prevent the occurrence of tribocorrosion of construction materials, several different lubricating nanoparticles have been investigated, including FeCu/WC-Co and WC-Co coatings, electrodeposited Ni-Co alloys, Ni-nano SiC, electroless Ni-I-nano SiC coatings, and nanostructured titanium.
References and Further Reading
Dahlan, A. S. (2021). Impact of nanotechnology on high performance cement and concrete. Journal of Molecular Structure 1223. doi:10.1016/j.molstruc.2020.128896.
Raki, L., Beaudoin, J., Alizadeh, R., et al. (2010). Cement and Concrete Nanoscience and Nanotechnology. Materials 3(2); 918-942. doi:10.3390/ma3020918.
Sankara Narayanan, T. S. N. (2012). Chapter 8 – Nanocoatings to improve the tribocorrosion performance of materials. Corrosion Protection and Control Using Nanomaterials; 167-212. doi:10.1533/9780857095800.2.167.
Disclaimer: The views expressed here are those of the author expressed in their private capacity and do not necessarily represent the views of AZoM.com Limited T/A AZoNetwork the owner and operator of this website. This disclaimer forms part of the Terms and conditions of use of this website.