Iron oxide nanoparticles can be synthesized through careful control of experimental temperature. These nanoparticles can be tuned to offer desirable properties such as porosity and large surface area, making them suitable candidates in catalysts, for biomedical applications, or as electrode materials for metal-ion batteries. This article looks at how researchers use temperature-controlled procedures to synthesize and characterize porous maghemite nanoparticles.
Investigating Porous Nanomaterials
Iron oxides are a family of chemical compounds comprising iron and oxygen that are important for many biological, geological, and electrical processes. They occur naturally in the form of iron ores in the environment, as ferritin in mammals, or simply as rust, but they can also be synthesized and tuned to suit a variety of applications from catalysts, sorbents, pigments, or functionalized materials. Maghemite is one such iron oxide that can be fabricated as a model compound for energy storage purposes, in which case temperature control during synthesis facilitates tuning of the material’s surface area and porosity.
Microporous and mesoporous nanomaterials are of particular interest to the materials science industry due to their unique surface, structural and chemical properties1. They can be fabricated from inorganic or organic frameworks that often include metal ions. The Department of Materials and Environmental Chemistry at Stockholm University, Sweden, plays an important role in furthering the understanding of functional nanoparticles for a range of applications. The research addresses important challenges in energy, environment, and health, with scientists developing advanced techniques for chemical analysis and structural characterization. The department also focuses on analyzing porous materials (including micro-, meso-, and macroporous materials), studying applications of nanocellulose for water treatment or heat insulation, and developing computer simulations of biological molecules.
The research group at Stockholm University has recently worked with two lines of research: one dealing with structural determination at the atomic and mesoscopic level of various nanomaterials; the other looking at the fabrication and surface modification of nanocellulose for applications such as battery components, i.e. binders of electrode materials or separators.
Iron oxide nanoparticles are often used as adsorbents for water purification (e.g. for removal of arsenic) and have recently been investigated as potential catalysts for the oxidation of water, producing hydrogen as a possible alternative to fossil fuels. This process is directly dependent on the available surface area and the catalytic/adsorption performance can be enhanced by introducing small pores. As well as understanding what the pores look like after the reaction, it is important to understand how the pores appear over time. The group used lepidocrocite (γ-FeOOH), an iron oxyhydroxide, as a precursor which, upon heating to about 250 °C, loses water and transforms into maghemite (γ-Fe2O3).
Iron oxide nanomaterials, such as synthetic maghemite, have become popular as electrodes for lithium-ion, sodium-ion, and alkaline-ion batteries. Parameters such as surface area, pore size, and porosity are important for the mass transport of ions required for charge and discharge cycles. Fabricating maghemite nanoparticles with high surface area is a key focus for our research group. However, analyzing this process is not without its challenges - the most difficult issue faced is determining the shape and location of the pores, and accurately measuring the increase in the surface area resulting from pore formation, which can be challenging.
Temperature-Controlled Experiments
The degree of iron oxide porosity depends on the heating treatment conditions during pore formation, so to understand this transformation, the temperature must be controlled precisely and the residence time at a given temperature must be known (Figure 1). There are a number of experimental techniques to study porous nanoparticles, including surface adsorption, infrared spectroscopy, liquid and solid-state nuclear magnetic resonance (NMR), transmission and scanning electron microscopy (TEM and SEM), X-ray diffraction (XRD), thermal analysis, Raman spectroscopy, magnetometry, and atomic force microscopy (AFM).
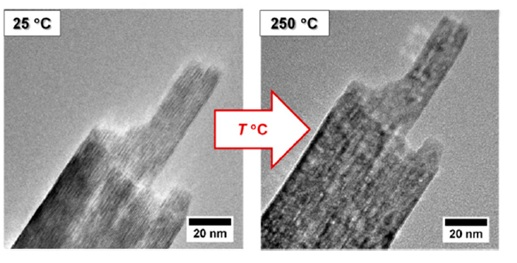
Figure 1. High-resolution TEM images showing the morphology of lepidocrocite nanoparticles before (left) and after (right) thermal transformation at 250 °C. Reproduced from reference 2 in accordance with Creative Commons Attribution (CC BY) license.
In a recent study conducted at Stockholm University, the research group investigated the transformation of lepidocrocite nanoprisms into porous maghemite nanoprisms2. The structural transformation was followed by in situ XRD, which points to a time delay between the decomposition of lepidocrocite and the nucleation of maghemite. During heating, hydroxyl groups acquire enough energy to form a water vapor via condensation with the closest hydroxy group (H+ + OH–). The size and morphology of the nanoparticle remain the same during and after the transformation, so the change in the surface area is therefore likely related to the change in the particle porosity.
These experiments used the Linkam TS1500 in combination with an X-ray single-crystal diffractometer (Xcalibur, Oxford Instruments) to obtain the data shown in Figure 2. The transformation temperature increases with the heating rate converging towards 250 °C, similar to reports in the literature (Figure 2B), and the heating rate is crucial for the determination of the transformation temperature (Figure 2C). The precise temperature control achievable enabled the group to reproduce the transition temperature obtainable with a thermogravimetric balance.
The patterns obtained in Figure 2C with small temperature increments are very difficult to achieve with the traditional accessories and the typical powder diffractometers. Due to the fast and extremely accurate temperature control of the TS1500, the XRD acquisition times could easily synchronize with the heating profile without the need to spend valuable (and irreversible) time on stabilizing the temperature to either prevent overshoot or to wait for an accurate reading. A time resolution of ca. 1-2 min per diffractogram/temperature setting could be achieved, mainly due to the time that it takes for the detector of the diffraction instrument to acquire and save the data.
The single-crystal diffractometer provides an intense beam that reduces the time to acquire data to a couple of minutes, while the fast and reliable heating profiles achieved with the TS1500 allows very small temperature increments. The data shown in Figure 2D shows a gap between the dehydration of iron oxyhydroxide (FeOOH) and the formation of Fe2O3. Knowing that the processes are not simultaneous provides more scope to control the pore formation and offers insights into the mechanism of Fe2O3 formation.
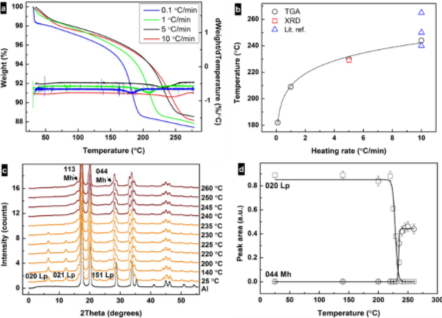
Figure 2. (a) Thermogravimetric analysis (TGA) curves and their derivatives for the samples heated at 0.1, 1, 5, and 10 °C/min rates. (b) Correlation between heating rate and transformation temperature of lepidocrocite as obtained from TGA and X-ray diffraction (XRD) data and from literature3,4,5. (c) Changes in intensity of diffraction peaks from XRD patterns showing the transformation of lepidocrocite (orange) to maghemite (red) upon heating at 5 °C /min under air. The black curve represents Al from the specimen pan. (d) Change in integrated intensities of the 020 lepidocrocite and 440 maghemite diffraction peaks under heating. Reproduced from reference 2 in accordance with the Creative Commons Attribution (CC BY) license.
Looking to the Future
Understanding the properties underlying pore formation is essential for fabricating functional porous nanomaterials. Following the structural transformation of lepidocrocite nanoprisms into porous maghemite nanoprisms, XRD allowed the Stockholm University research group to observe the temporal decoupling of the decomposition of lepidocrocite and the growth of maghemite. Accurate temperature-controlled experiments provided us with insights into the dependence of the transformation temperature on heating rate, suggesting that kinetic factors influence this transformation.
Advanced studies of porous nanoparticles are crucial to the development of tomorrow’s highly functional materials. Experts are examining how novel nanomaterials can solve modern challenges in energy applications, and experiments such as those in Sweden show promising solutions such as synthetic maghemite for catalysis, adsorption, and energy storage. The analytical techniques available today, such as temperature-controlled stages, are proving to be powerful tools for improving the understanding of porous materials.
Acknowledgments
Authors: Dr. Germán Salazar-Alvarez, Group Leader at the Department of Materials and Environmental Chemistry at Stockholm University, and Dr. Duncan Stacey, Sales and Marketing Director at Linkam Scientific.
References and Further Reading
- Bhaumik A. “Porous Nanomaterials for Energy, Environment and Biomedical Applications” 2017 J. Mater. Sci. Nanomater 1: e109.
- Trushkina Y, Tai CW and Salazar-Alvarez G. “Fabrication of Maghemite Nanoparticles with High Surface Area” 2019 Nanomaterials 9. 1004 doi:10.3390/nano9071004.
- Song X and Boily JF. “Surface and Bulk Thermal Dehydroxylation of FeOOH Polymorphs” 2016 J. Phys. Chem. A 120 6249–6257 doi.org/10.1021/acs.jpca.6b04294
- Ennas G, Marongiu G, Musinu A, Falqui A, Ballirano P and Caminiti R. “Characterization of Nanocrystalline γ–Fe2O3 Prepared by Wet Chemical Method” 1999 J. Mater. Res. 14 1570–1575 doi.org/10.1557/JMR.1999.0210
- Fang J, Kumbhar A, Zhou WL and Stokes KL. “Nanoneedles of maghemite iron oxide prepared from a wet chemical route” 2003 Mater. Res. Bull 38 461–467 10.3390/nano9071004

This information has been sourced, reviewed and adapted from materials provided by Linkam Scientific Instruments.
For more information on this source, please visit Linkam Scientific Instruments.