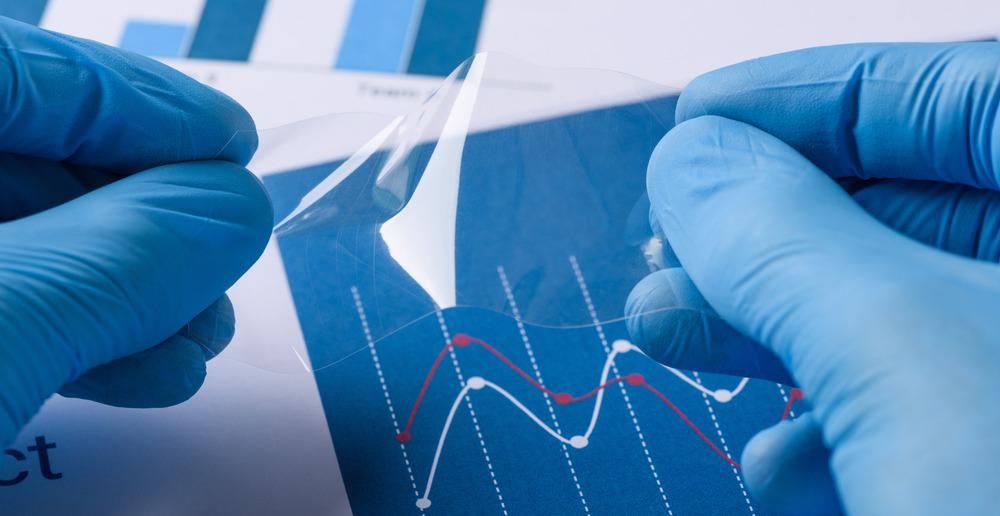
Image Credit: nevodka/Shutterstock.com
In a recent study published in the journal Nano-Micro Letters, a research team led by Prof. MacManus-Driscoll within the Department of Materials Science and Metallurgy at the University of Cambridge (UK) describes an innovative processing step that yields damage-free large-scale oxide thin films. Here, we look at the most promising thin-film technique set to advance the electronic device market and how the team’s methodology addresses the problems that arise with oxides.
Obtaining High-Quality Epitaxial Films
The development of two-dimensional (2D) materials in recent years has accelerated and with it the anticipation of exceptionally advanced properties for low-dimensional, single-crystalline oxide thin films.
Films attract much research attention as their physical properties underpin a wide range of devices, from superconductors and photovoltaics to biological devices and low-power consumer electronics.
Oxide thin films are typically grown by a crystal growth deposition method called epitaxy. In epitaxy, orientated layers are usually formed upon crystalline substrates. Traditionally, a limited range of hard substrates has meant that films have limited mechanical flexibility while the strong chemical bonds at the interface between film and substrate have made separating the two problematic.
As the field has advanced, a method known as the wet etching release method has arguably emerged as the most promising approach to producing free-standing thin films. It provides higher selectivity and is more cost-effective. As it removes the substrate as a sacrificial layer, it retains the high-quality growth of the epitaxial films as there is less damage after transfer than other methods.
It also opens up the possibility of using flexible and semiconductor substrates. The wet etch method involves a lift-off and transfer step, which usually determines the upper limit of the film area and quality.
Although it can produce free-standing thin films of metals when it comes to ceramic or single-crystalline oxide films, the transfer process is challenged by the introduction of cracks, resulting in brittle, fragile films of often no practical use.
One method to prevent crack or fracture formation is the application of a supporting layer on the whole film surface before the wet etching process.
Up until now, a graphene transfer process typically using a polymethylmethacrylate (PMMA) supporting film has been adopted. However, this is not strongly applicable to oxide thin films, as having higher densities than other 2D materials, film flotation can prove difficult and present detachment issues from the substrate. There is also the possibility of film breakage during the PMMA removal step and possible contamination.
Two-Layer Structure Support Method
Prof. MacManus-Driscoll et al. have developed a new method for manipulating and transferring up to 5 mm × 10 mm epitaxial oxide thin films.
Using pulsed laser deposition (PLD), the group grew three different film types (typical thickness ~ 100 nm) onto Strontium Aluminate (Sr3Al2O6) substrates. They then loaded the support layer onto the thin film/substrate combination by spin coating a PMMA solution and attaching a membrane (Polyethylene terephthalate) to the PMMA side of the film/substrate with moderate pressure.
Framing and fixing this polymer resin onto a PMMA attachment film enables the transfer of epitaxial films lifted-off by wet chemical etching of the Strontium Aluminate sacrificial layer (selected because of its water-solubility and therefore avoids using acid etchants).
The two-layer structure support method offers crack prevention during transfer while facilitating the manipulation of large-area films. The overall yields for the three different oxide film types were greatly improved, reflecting successful adaption of the lift-off process as it provides extra rigidity, easier handling, and avoidance of physical damage during the mechanical lifting process.
The method also helps the oxide film transfer onto substrates such as silicon to preserve purity, crystallinity, and surface morphology.
Exploring the structural integrity of the resulting metallic strontium ruthenate films by making resistivity measurements, the group could ascertain enhanced properties and yields of 59.09%, while lift-off yield improvement of around 50% was possible when vertically aligned nanocomposite (VAN) films were used.
Evidence for this was found by comparison between Ceria (CeO2) films alone, with films containing Ceria pillars formed within strontium titanate (SrTiO3) matrices where yields went from 55.93% to 72.31%, respectively. It is believed that the VAN nanocomposite films assist the transfer process because of higher fracture composite toughness with less crack/damage (13.85%) or breakage (6.15%).
No Cracks or Wrinkles
Among the potential advantages of their new PMMA-mediated method, the researchers believe that the PET membrane, (being much more mechanically stable than the PMMA layer) allows the free-standing film to be carefully manipulated without flexing, the spin-coated PMMA layer (easily removed by acetone) provides full coverage of the film. This allows the lifted-off film to be continuous, and the additional PET frame on the PMMA prevents films from sinking, among other advantages.
By obviating cracks, wrinkles, and damages commonly introduced by conventional transfer processes, this new transfer method has revealed new and exciting steps towards realizing large-scale thin-film-based electronic device applications.
References and Further Reading
Disclaimer: The views expressed here are those of the author expressed in their private capacity and do not necessarily represent the views of AZoM.com Limited T/A AZoNetwork the owner and operator of this website. This disclaimer forms part of the Terms and conditions of use of this website.