Additive manufacturing refers to the process whereby complex objects are created by joining materials layer by layer using a 3D model data guide. Having significant advantages over traditional casting, such as high efficacy, less wastage, and high flexibility, this printing process has become a focal point for researchers. The use of CNTs within nanocomposite ink for additive manufacturing is an innovative development that aims to provide a higher functionality of this already advanced intricate printing method.
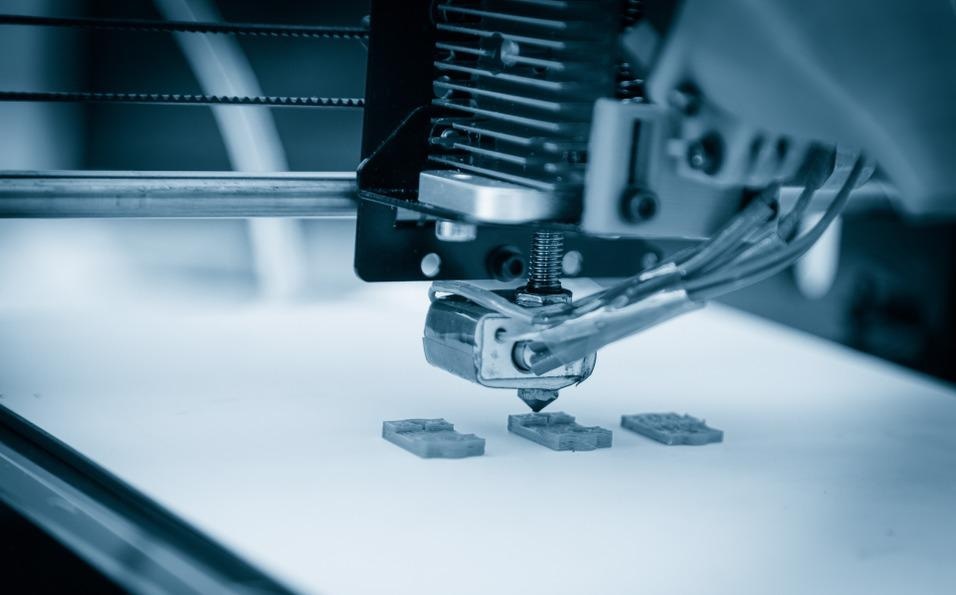
Image Credit: Alex_Traskel/Shutterstock.com
Epoxy-based ink can enable 3D printing of composites with high control over the creation of multiscale hierarchical structures. Polymers such as carbon nanotubes (CNTs) can also be used as a filler material in order to enhance the stiffness of composites.
Additive manufacturing, or 3D printing, was first commercialized in 1990, with fused deposition modeling (FDM) becoming one of the most commonly used 3D printing processes due to being simple and cost-efficient.
FDM has illustrated great potential for a variety of applications, from medical devices to vehicle parts. Additionally, a wide range of thermoplastic polymers can be used in FDM. As the field of additive manufacturing has increased, the inclusion of polymers as filler materials has also expanded, from metals, ceramics to nanomaterials such as carbon nanotubes.
Nanocomposite Polymeric Ink
Novel research into nanocomposite polymeric ink has utilized carbon nanotubes for additive manufacturing, potentially providing a higher performance level of printing manufacturing with higher precision and complexity of various shapes.
The focus on advancing additive manufacturing has led researchers from Michigan Technological University, USA, to undertake a project on their innovative printing process, which optimizes functionality through carbon nanotubes (CNTs) and directly links the gap between real-world applications and 3D printing.
The team has published their novel research within the journal Additive Manufacturing, directly link the gap between real-world applications and 3D printing.
The inclusion of CNTs within their novel nanocomposite ink, along with nano-clay and epoxy, has the potential to provide the global market with higher-performing nanomaterial for various applications.
Benefits of Utilizing Carbon Nanotubes
The researchers included CNTs to increase the performance level of their nanocomposite ink. Nano-clay was incorporated with various concentrations of CNTs such as 0.25, 0.5, and 1 vol%, 0.43, 0.86, and 1.7 wt% within epoxy to evaluate the optimum CNT level.
The team found 0.5 vol% of CNTs to be the optimum level for mechanical enhancement, with the end product having an increase in flexural strength by 61%, flexural modulus by 59%, and tensile strength by 31%.
Enhancing properties such as electrical and mechanical characteristics of materials would innovate and advance the global materials market, increasing demand for higher quality and functionality. The use of 3D printing provides a solution to the complexity of material printing. CNTs offer a higher level of conductance, electrical and thermal conductivity due to the strength between their carbon atoms and flexibility and strength, which competes with steel. This novel material may be revolutionary.
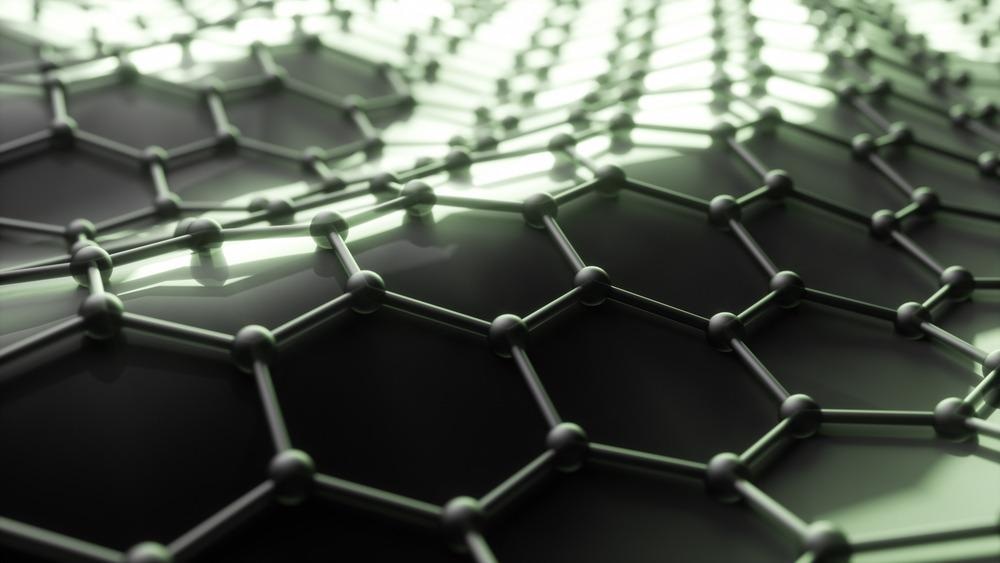
Image Credit: OliveTree/Shutterstock.com
Overcoming Real-World Challenges
The polymer nanocomposite and 3D printing product and service market are worth more than a billion dollars, while the nanomaterial 3D printing process has an estimated value of $43 million dollars.
The lead researcher, Parisa Pour Shahid Saeed Abadi, has commented that “For national prosperity and sustaining global leadership in manufacturing, the gap between the real-world applications of 3D printing and nanomaterials versus nanomaterial 3D printing needs to be closed."
The gap exists due to lack of control of nanocomposite properties in the 3D-printing process, because we don't fully understand the process-morphology-property relationship.
Parisa Pour Shahid Saeed Abadi, Lead Researcher, Michigan Technological University
Additive manufacturing uses automated strategies to create 3D complex objects that are difficult to produce using other approaches, making this method a significant player in the fourth industrial revolution. A scalable, low-cost, and precise method to produce highly functional materials would be significant in the global market.
The increase in reliability of complex shapes, which will ultimately create higher demand for high-quality products, illustrates the significance of the role of CNTs within this novel research. From advancing electrical wiring and developments in the electronics market to medical applications like creating actuators for guiding catheters within blood vessels, 3D printing has taken another step towards innovation.
Adding carbon nanotubes to nanocomposite ink would revolutionize additive manufacturing; this highly flexible and high tensile strength material can effectively compete with steel, illustrating how this innovative development holds a universal promise that can advance nanotechnology and the material industry.
References and Further Reading
Kasraie, M. and Pour Shahid Saeed Abadi, P., 2021. Additive manufacturing of conductive and high-strength epoxy-nanoclay-carbon nanotube composites. Additive Manufacturing, 46, p.102098. Available at: https://doi.org/10.1016/j.addma.2021.102098
Electronics For You. (2021) 3D Polymer Nanocomposite Ink For Future Electronics | Electronics For You. [online] Available at: https://www.electronicsforu.com/technology-trends/research-papers/3d-polymer-nanocomposite-ink-for-future-electronics
Jiang, Q., Zhang, H., Rusakov, D., Yousefi, N. and Bismarck, A., (2020) Additive Manufactured Carbon Nanotube/Epoxy Nanocomposites for Heavy-Duty Applications. ACS Applied Polymer Materials, 3(1), pp.93-97. Available at: https://doi.org/10.1021/acsapm.0c01011
Science Daily. (2021) 3D nano-inks push industry boundaries. [online] Available at: https://www.sciencedaily.com/releases/2021/09/210924182516.htm
Disclaimer: The views expressed here are those of the author expressed in their private capacity and do not necessarily represent the views of AZoM.com Limited T/A AZoNetwork the owner and operator of this website. This disclaimer forms part of the Terms and conditions of use of this website.