Nanoindentation is a type of mechanical indentation testing that is performed on small areas. Indentation is one of the most frequent methods for determining a material's mechanical characteristics. Nanoindentation is a method for measuring the hardness, plasticity, and elasticity index of minute quantities of materials.
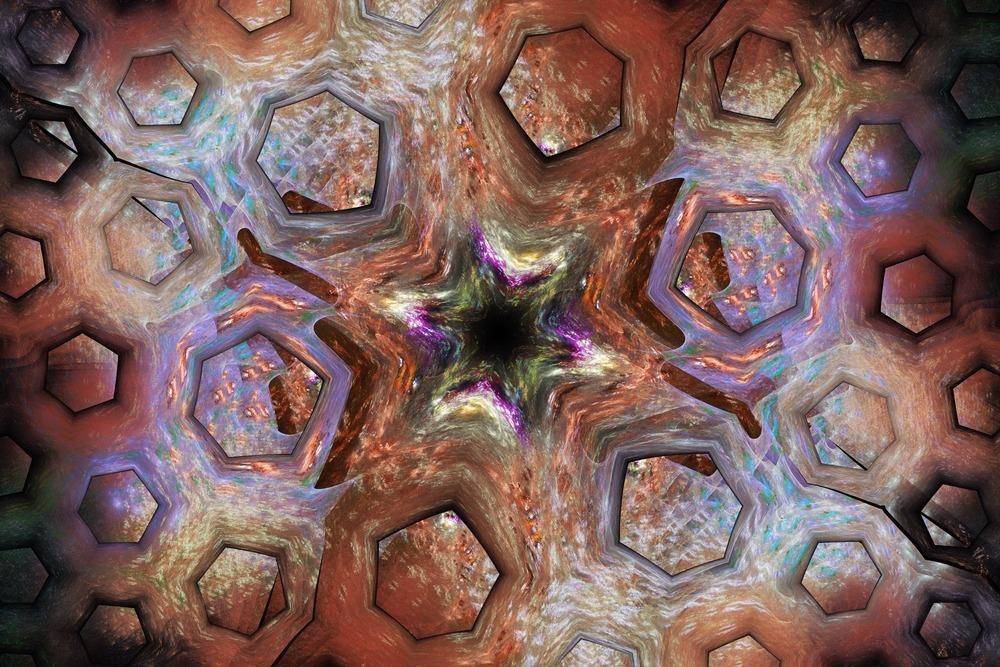
Image Credit: Eugenock/Shutterstock.com
Nanoindentation can be used to test raw materials, composite interactions, nanomaterials, thin films, and surface coatings; however, in many situations, the surrounding material influences the composite response. Understanding the foundations of the nano-mechanical characteristics measured by nanoindentation is critical.
Nanoindentation Experimental Procedure
Nanoindentation is an effective approach in which a defined indenter tip is forced into a specified spot in the test sample, increasing force is applied, and gradual unloading is conducted until the required depth is achieved. Before unloading, the resting section is provided, which enables the material to relax.
The operation is done repeatedly, and the divergence transformer is used to track the location of the indenter tip and the surface.
Sensors Used in Nanoindentation
The addition of exact motion and stress sensing devices allows for creating a depth-sensing indentation mechanism. Loading detectors must be able to measure loads in the micro-newton scale, whereas motion sensors often have sub-nanometer precision. The instrument's functioning requires complete atmospheric confinement.
During testing, vibrations conveyed to the instrument, variations in ambient temperature, and thermoelectric oscillations of the materials may all produce considerable inaccuracies.
Advantages of Nanoindentation
Nanoindentation has many benefits: it can be used to evaluate not only the Young's modulus and micro-hardness, but also other mechanical characteristics at the nanoscale, such as shear strength, creep, and fracture toughness.
Nanoindentation, unlike micro-hardness testing, does not need strong microscopy to determine the imprint of the indentation since the contact area is determined by the thickness of indentation and the indenter shape.
The nanoindentation method is also suited for evaluating nanoscale thin coatings because it can eliminate substrate impacts by limiting the indentation depth. This capability comes in handy when evaluating materials that have been covered with layers or when evaluating dissimilar materials.
The durability of a nanoindentation device is exceptional, allowing the stress or depth signals to be held for lengthy periods. In addition, when paired with thermal and humidity factors, nanoindentation can enable unrivaled atmospheric investigations of non-ambient materials.
The nanoindentation tests are the quickest mechanical characterization approach since each indent can be made in under a second. The data analysis is computerized, reducing any potential for human error. Traditional test techniques are too difficult for certain materials, such as hybrids and electronics, where nanoindentation provides a distinct benefit.
Applications of Nanoindentation
Testing coating characteristics for which traditional testing is not possible was the application that sparked the technique's development.
Nanoindentation can be used to determine the local characteristics of both heterogeneous and homogeneous materials. The approach has been widely used for items when the manufacturing condition does not provide adequate material for micro-hardness testing due to the decrease in specimen size restrictions.
Surgical implants, commodities, and packaging are all examples of applications in this field. Alternative applications of the approach include testing biosensors using the nanoindenter's low-load and small-scale displacement capabilities.
Limitations of Nanoindentation
Nanoindentation techniques for calculating Elastic modulus are confined to smooth, isotropic solids. The indented material's surface should be completely flat and aligned to the indenter tip.
As the indentation thicknesses are in the nanoscale range, the surface finish will significantly impact the nanoindentation results. Obtaining a perfectly smooth surface, on the other hand, is a challenging task. To counteract the impact of irregularity, the indentation should be performed with a maximum depth of approximately 20 times the surface roughness.
While nanoindentation analysis is very straightforward, interpreting the data may be difficult. One of the most difficult tasks is selecting the right tip for the job and properly interpreting the findings.
The elastic modulus, for example, has been demonstrated to be tip-dependent. Also, due to adherence, interface detection, and tip sensitivity of findings, nanoindentation of soft materials poses unique obstacles. There is continuous effort to find solutions to such issues.
Future Prospects
Nanoindentation is a hotspot of research and innovation, with analytical procedures improving all the time. Future innovations are projected to include the widespread use of computer models and quantification imaging methods to contribute to the understanding of complex data, as well as improvements in DCA procedures, including the use of acoustic approaches.
Continue reading: Measuring Nanohardness via Nanoindentation
References and Further Reading
Fischer-Cripps,, A. and Nicholson,, D., (2004) Nanoindentation. Mechanical Engineering Series. Applied Mechanics Reviews, 57(2), pp.B12-B12. https://doi.org/10.1115/1.1704625
Schuh, C., (2006) Nanoindentation studies of materials. Materials Today, 9(5), pp.32-40. https://www.sciencedirect.com/science/article/pii/S136970210671495X?via%3Dihub
Sasmal, S. and Anoop, M., (2019) Nanoindentation for evaluation of properties of cement hydration products. Nanotechnology in Eco-efficient Construction, pp.141-161. https://www.sciencedirect.com/science/article/pii/B9780081026410000074?via%3Dihub
Disclaimer: The views expressed here are those of the author expressed in their private capacity and do not necessarily represent the views of AZoM.com Limited T/A AZoNetwork the owner and operator of this website. This disclaimer forms part of the Terms and conditions of use of this website.