The finite element analysis (FEA) is commonly utilized to solve issues in conventional technical and nano research sectors when the experimental study is too expensive. Using finite element analysis methods, complex nanoengineering issues may be solved.
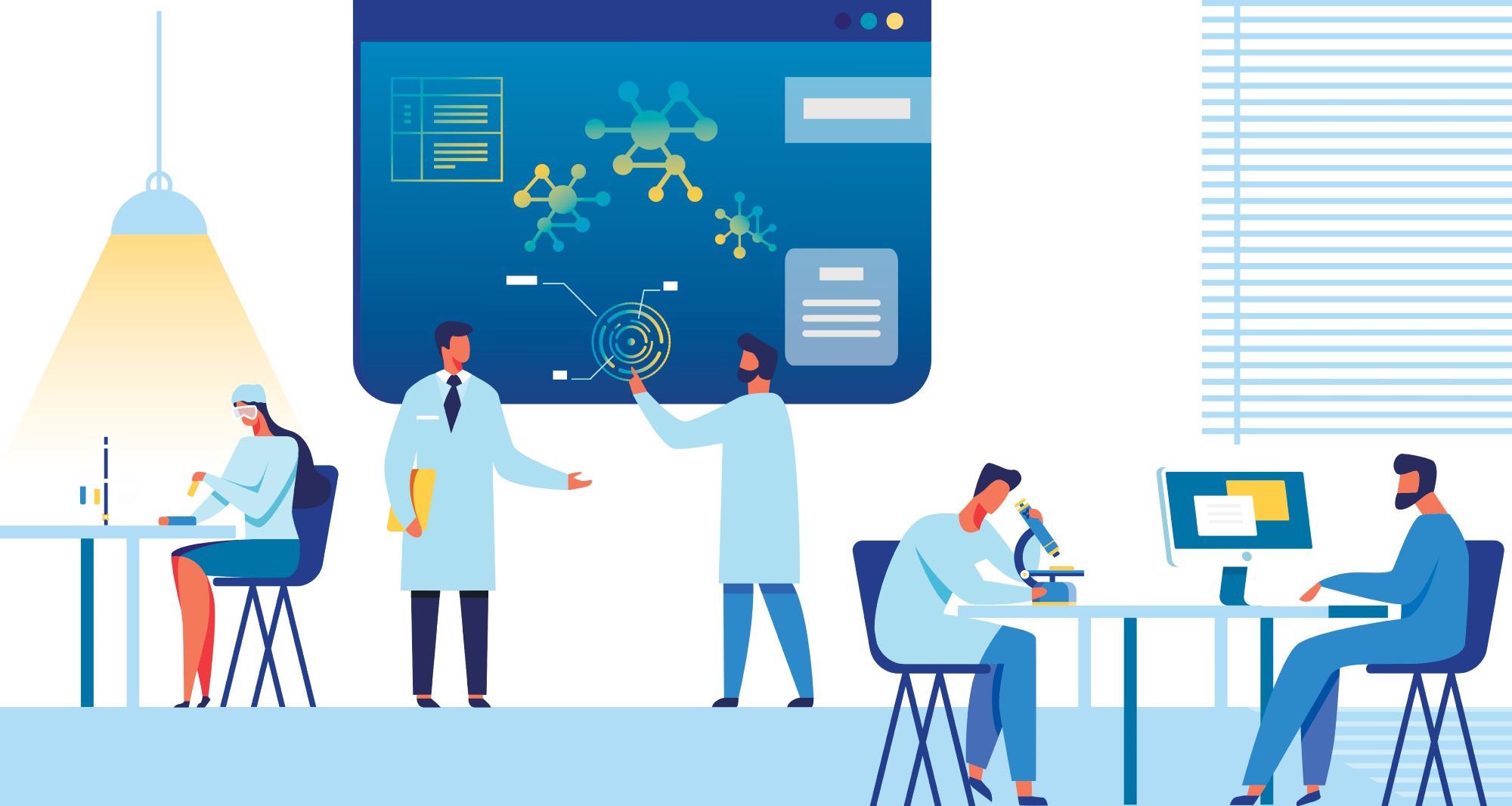
Image Credit: Unitone Vector/Shutterstock.com
What is Finite Element Analysis?
The finite element analysis is an extensively used method for computationally solving partial differential equations in technology and mathematics. The classic domains of structural system, heat flux, fluid mechanics, mass transfer, and electrostatic potential are typical subject areas of interest. It is vital to remember that FEA only offers an estimated solution to the problem and is only a mathematical method for attaining the genuine solution to these differential equations.
The FEA computations employ thousands of tiny components to produce the structure's design. Each of these components is calculated, and the final structure is the product of these mesh adjustments. Extrapolation over tiny elements means that quantities can be computed at some but not all regions. The regions on the element's perimeter where the quantities can be calculated are called Nodal points.
Need for Finite Element Analysis Method in Nanotechnology Research
Nanotechnology research necessitates the development of new methodology and procedures. To move from micro to nano, a thousand-fold decrease in size is necessary. Automation and computational analytic techniques are required to solve complex engineering, analytical, technological, industrial, and research challenges related to nanotechnology. The use of numerical methods is motivated by this goal. FEM employs a variety of research approaches, including direct, vibrational, energetic, balanced residual, linear formulation, and nonlinear analysis.
Differential equations and mathematical models can simulate numerical solutions in nanotechnology. FEM is used to assess the applicability of a nanotechnology analytical investigation. Scientists and researchers working on the problem anticipate that FEA software will eventually replace expensive nano-research equipment.
The major benefits of finite-element methods are the accurate depiction of geometrically complex components present in practical uses and the product's consistency and general applicability to various modeling settings nanotechnology field.
Applications of Finite Element Analysis in Nanotechnology Research
Many researchers have successfully employed the finite element analysis technique in research fields related to nanotechnology and obtained effective results. Some of the applications of FEA used by researchers are as follow:
Biaxially Tensioned Nanofibrous Mats
In supercapacitors, the nanofibrous mats can be employed as independent anodes. These mats exhibit non-uniform physical characteristics, with nonlinear features in every fiber. To accurately recreate the nanofibrous mats under biaxial tension, Yin et al. (2018) developed two continuous macroscopic simulations with oriented or non-orientated nanofiber arrangements. Researchers investigated the mechanical reaction of the nanofibrous mats, using finite element analysis to reveal the displacement of nanofibrous mats and the progressive damage process and microstructure of nanofibrous mats in their research.
Utilization of Nano-Indentation Finite Element Method To Characterize Thin-Film Coatings
Alaboodi et al. studied thin-film coatings using finite element analysis to reduce the wear and corrosion of nanomaterials. Thin-film coatings for critical stresses that lead to rupture were investigated by the researchers. Nano-indentation is the preferred technique to study characteristics of thin-film coatings since it is non-destructive and must be simulated utilizing the finite element method (FEM).
Toughness, ductility, endurance loads, ideal cross-sectional area, optimized stress, residual stress, and the frictional force between the material and the coating were all determined using FEM by researchers.
Finite Element Analysis of Nanotips
A range of technologies for producing ultra-sharp tips have been developed for scanning probe microscopy. It was observed in a field ion microscope that the sharp edge finished with a single atom (FIM). The last atom was expected to self-collimate a dazzling, coherent electron beam by generating an atomic channel of electrons in field emission mode.
Rezeq et al. (2011) used finite element analysis to look at the dissemination of electric field near the nanotip apex, which contains the highest single atom, both numerically and mathematically. The tip base was determined to be in charge of nano protrusions that augment the electric field. According to the study, nanotips with wide bases generate significantly less electric fields than narrow tips at the same voltage. This underlines the tip base's capacity to endure the high voltages required at the scanning threshold field.
Simulation of Nanoscale Silicon Micromachining Using Finite Element Analysis
Pen et al. (2018) studied the microfabrication method of nanometric silicon carbide particles (SICp) strengthened aluminum matrix composite using the finite element technique. Stress–displacement curves from a computational modeling simulation were used to determine the performance of the cohesive zone model. The model well characterized both the unsystematic features of the silicon–carbide particle dispersion and the interfacial adhesion between SICp and matrix.
Chip structure, stress fluctuation, temperature, and cutting conditions were used to investigate the machining process. SICp created non-uniform interaction between the instrument and the reinforcements, according to the FE simulation. Non-uniform stress variation and uneven cutting force were caused by the fracture mechanics.
Conclusion
For the design, modeling, and evaluation of nano/micromechanical systems, finite element analysis is a method capable of maintaining the integrity of lumped components, dispersed elements, and components of the system. Using FEA, nanoparticles, nanofibers, carbon nanotubes, and nanocomposites are all simulated. Due to the emergence of computing and FEA software, the formerly costly experimental examination of nanotechnology has been replaced by analytical research employing FEM.
Continue reading: Cleanrooms; a Critical Component to Nanotechnology Research
References and Further Reading
Chandran, R. (2022) Finite Element Analysis in Nanotechnology Research. In Finite Element Methods and Their Applications. IntechOpen, https://doi.org/10.5772/intechopen.94590
Yin, Y., & Xiong, J. (2018) Finite element analysis of electrospun nanofibrous mats under biaxial tension. Nanomaterials, 8(5), 1-19. https://doi.org/10.3390/nano8050348
Alaboodi, A. S., & Hussain, Z. (2019) Finite element modeling of nano-indentation technique to characterize thin-film coatings. Journal of King Saud University - Engineering Sciences, 31(1), 61-69. https://doi.org/10.1016/j.jksues.2017.02.001
Rezeq, M. (2011) Finite element simulation and analytical analysis for nano field emission sources that terminate with a single atom: A new perspective on nanotips. Applied Surface Science, 258(5), 1750-1755. https://doi.org/10.1016/j.apsusc.2011.10.034
Pen, H., Guo, J., Cao, Z., Wang, X., & Wang, Z. (2018) Finite element simulation of the micromachining of nanosized-silicon-carbide-particle reinforced composite materials based on the cohesive zone model. Nanotechnology and Precision Engineering, 1(4), 242-247. https://doi.org/10.1016/j.npe.2018.12.003
Disclaimer: The views expressed here are those of the author expressed in their private capacity and do not necessarily represent the views of AZoM.com Limited T/A AZoNetwork the owner and operator of this website. This disclaimer forms part of the Terms and conditions of use of this website.