Metal corrosion has a substantial impact on the economies of many industrialized enterprises. Nanocomposite coatings are considered a potential solution due to their anticorrosive properties.
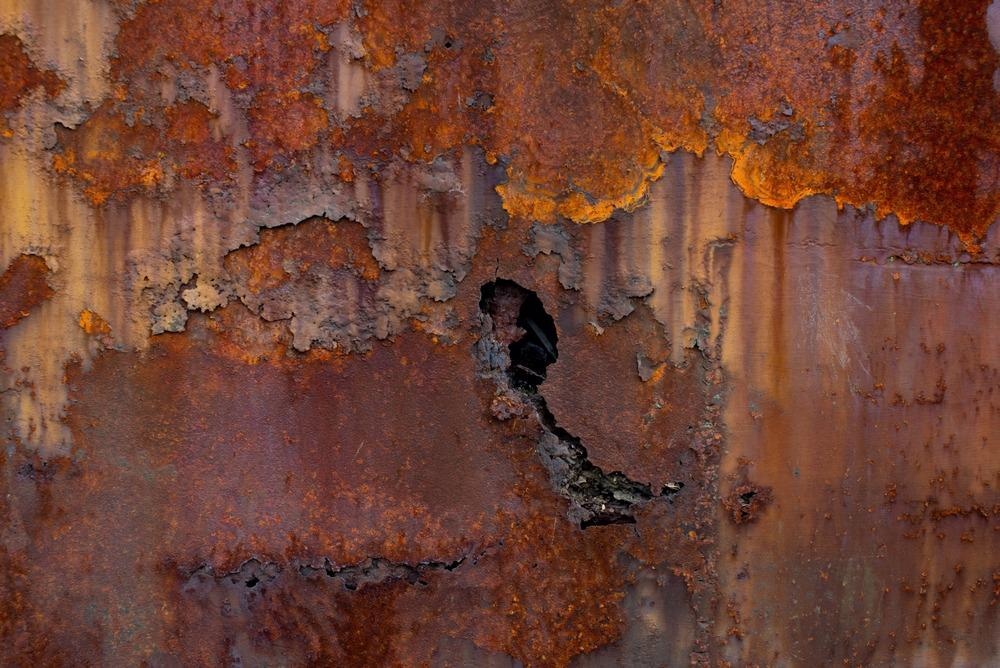
Image Credit: Quisquilia/Shutterstock.com
Anticorrosive nanocomposites are organic coatings that protect against corrosion, and are composed of various polymers, metals, and ceramics in diverse matrix topologies. These anticorrosive nanocomposite coatings feature smaller particles and at least two phases, either nano-crystalline or amorphous or two nano-crystalline phases. The matrix is the most significant component of these nanocomposite materials and is separated by an interface zone.
Anticorrosive nanocomposites are classified depending on the matrix or fillers used in their creation. The matrix can be organic or inorganic, and the fillers can be one-dimensional, two-dimensional, or even three-dimensional at the nanoscale scale.
Epoxy resin, polyaniline, polyvinyl alcohol, and other polymers with zinc oxide, titanium oxide, silicon oxide, graphene, and carbon nanotubes (CNTs) as fillers or additives are the most extensively used polymers for organic-inorganic nanocomposite coatings.
Sol-gel, chemical vapor deposition, electrodeposition, or spin coating processes such as spray coating and dip coating are all used to produce nanocomposite coatings on metal substrates.
Corrosion Prevention Mechanism of Anticorrosive Nanocomposites
Anticorrosive nanocomposite coatings provide good thermal characteristics and strong barrier qualities, mechanical strength, wear, and abrasion resistance. They limit corrosion by managing both oxidation and reduction processes, preventing it by producing a barrier shield between the metal and the corrosive environment.
The tiny nanoparticles enter the matrix's cavities, small holes, and capillary regions, boosting the crosslinking density of the fillers and enhancing the stiffness of the coatings. It also works as a sacrificial substance, protecting metal components from water, acid, and other corrosion-causing causes by producing a layer.
The performance of anticorrosive nanocomposites is influenced by several parameters, including the kind of nanomaterials employed, their size and concentration, as well as the additives utilized.
Spherical and tiny round shape particles have a high integration ability when combined with surface smoothness. The concentration must also be adjusted to achieve exceptional anticorrosive qualities because increased concentration can result in the loss of desired properties when the particles begin to agglomerate.
Furthermore, the optimum property balance is dependent on the concentration of nanocomposites, which must be carefully maintained by corrosive environmental conditions and criteria. Moreover, some studies even show that mixing and agitation processes also play an important role in determining the behavior of the anticorrosive coating, as slow or fast mixing can result in poor dispersion of nanoparticles or a decrease in contact between the nanoparticles and matrix, respectively.
Industrial Applications of Anticorrosive Nanocomposites
Anticorrosive nanocomposite coatings are widely employed in industries like automotive, construction, aviation, submarines, electrical and electronic, military, aerospace, and oil. The anticorrosive nanocomposites improve the material's mechanical strength, thermal characteristics, wear qualities, and service life, which has a substantial impact on the industrial sector's and country's economics. These sectors benefit from anticorrosive nanocomposite coatings in the sense that the lifetime of components used in the industry that are exposed to corrosive environments are significantly extended and cost-effective.
Market research reports also show that the market size of anticorrosive nanocomposite increased significantly from 2019 to about USD 4.32 billion and is expected to increase to about USD 14.34 billion by 2027, indicating that nanocomposite coatings have significantly affected the industrial market.
Recent Research in the Field of Anticorrosive Nanocomposites
The effectiveness of anticorrosive nanocomposite coatings has been proven in recent research investigations. A graphene-based nanocomposite matrix, which has shown the potential for self-healing and anticorrosive capabilities, is the most intriguing; it also had a low electrical resistance.
The research study conducted by Guerrero et al. (2022) employed NOA73 as the host matrix and added graphene flakes and zinc nano-powders as additives to aluminum alloys often used in the aerospace sector. To examine the mechanical and electrical characteristics, the team employed scanning electron microscopy (SEM), confocal laser imaging, the 4-wire connection Kelvin technique, and Raman spectroscopy.
The self-healing property was put to the test by using it to increase the life service of a healing mechanism. Furthermore, the coatings' outstanding blocking and anticorrosive characteristics were demonstrated in a cyclic voltammetry neutral salt spray test (NSSt), which revealed no evidence of corrosion after 168 hours.
Aside from that, a study by Ramezanzadeh et al. (2017) showed that the use of polyaniline (PANI) was highly beneficial in improving the corrosion properties of organic-inorganic composite coatings by forming a passive oxide film.
Thurber et al. (2018) found that aluminum metal-metal matrix composite coatings with the addition of silicon carbide, aluminum oxide, or graphite fibers had a lower corrosion rate than unreinforced aluminum alloy. It increased the corrosion characteristics of stainless steel in seawater.
According to Zhang et al. (2018) anticorrosion performance of epoxy coatings can be increased by the inclusion of Fe3O4-SiO2 nanocomposites. The evenly distributed nanoparticles in epoxy resin demonstrated outstanding compatibility with the matrix and enahnced performance.
Conclusion
Nanocomposites outperform traditional methods in terms of corrosion resistance. Corrosion inhibitors and coatings based on nanocomposites are increasingly used as versatile smart materials and protective layers against industrial aggressors. Using anticorrosive nanocomposites in coatings results in a denser covering with greater uniformity and decreased porosity than conventional coatings.
Due to the absence of defects and cracks in the coating, as well as the formation of a barrier against corrosive electrolytes penetration, nanocomposite coatings can have stronger corrosion resistance than traditional materials.
Continue reading: Medical Applications of Corrosion Resistant Modified Titanium Implants
References and Further Reading
Benavides-Guerrero, J., Banerjee, D., Gedamu, D., Gerlein, L. F., & Cloutier, S. G. (2022) Conductive, anti-corrosion, self-healing smart coating technology incorporating graphene-based nanocomposite matrix. Frontiers in Materials, 210. https://doi.org/10.3389/fmats.2022.835855
Ramezanzadeh, B., Moghadam, M. M., Shohani, N., & Mahdavian, M. (2017). Effects of highly crystalline and conductive polyaniline/graphene oxide composites on the corrosion protection performance of a zinc-rich epoxy coating. Chemical Engineering Journal, 320, 363-375. https://doi.org/10.1016/j.cej.2017.03.061
Thurber, C. R., Ahmad, Y. H., Calhoun, M. C., Al-Shenawa, A., D'Souza, N., Mohamed, A., & Golden, T. D. (2018). Metal matrix composite coatings of cupronickel embedded with nanoplatelets for improved corrosion resistant properties. International Journal of Corrosion, 2018. https://doi.org/10.1155/2018/5250713
Zhan, Y., Zhang, J., Wan, X., Long, Z., He, S., & He, Y. (2018). Epoxy composites coating with Fe3O4 decorated graphene oxide: Modified bio-inspired surface chemistry, synergistic effect and improved anti-corrosion performance. Applied Surface Science, 436, 756-767. https://doi.org/10.1016/j.apsusc.2017.12.095
Disclaimer: The views expressed here are those of the author expressed in their private capacity and do not necessarily represent the views of AZoM.com Limited T/A AZoNetwork the owner and operator of this website. This disclaimer forms part of the Terms and conditions of use of this website.