The University of Manchester is a world leader in science and innovation in advanced materials. In this interview, AZoNano visits The University of Manchester's Graphene Engineering and Innovation Centre to talk with Mark Dickie, Composite Applications Manager, about how the GEIC is helping to take graphene composite innovation out of the lab and into the wider industry.
Please could you introduce yourself and tell us about your current position at the Graphene Engineering Innovation Centre (GEIC)?
My name is Mark Dickie and I am the Applications Manager for composites within the GEIC; this covers everything from fiber-reinforced plastics to polymers, mixed metal matrices, and ceramics.
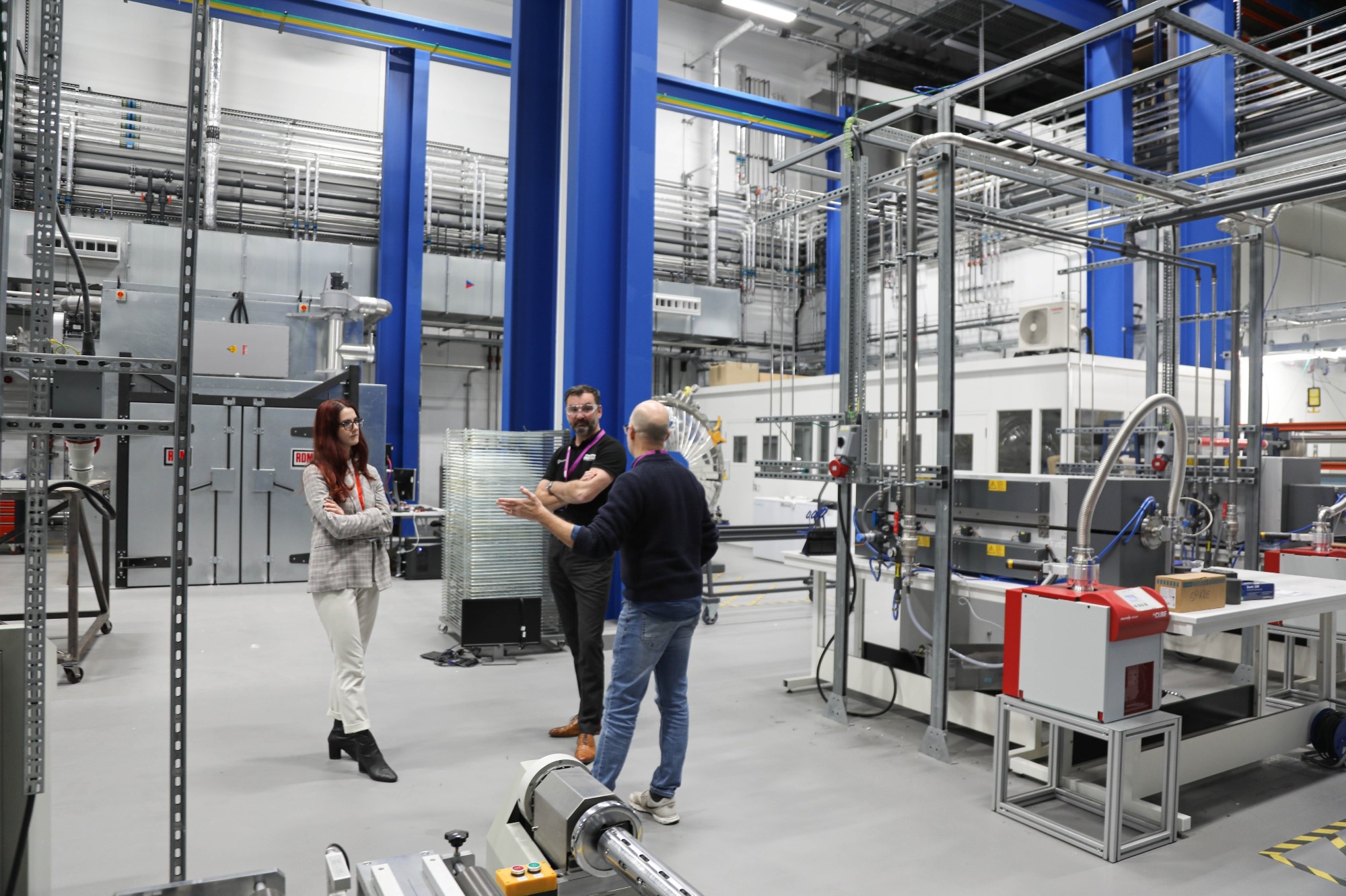
Megan Craig/AZoNano (left), Mark Dickie (middle) and Alan Beck (right) in one of the GEIC's labs. Image Credit: Joao Pinto/AZoNetwork
What is the GEIC, and how did you become involved?
I previously worked in the composites industry for 30 years before being introduced to a position that became available as the GEIC was initially being built. The GEIC acts as a link between The University of Manchester and to industry, taking what the academics are doing or what the industry wants to do and enabling knowledge transfer between the two.
All of the equipment at the GEIC is pilot-scale, acting as a step up from the research lab. We work with a range of different partners at various stages of enterprise size, from small start-ups to multinational companies.
I believe that many of our partners believe the GEIC to be an invaluable institute, enabling our partners to do things a lot quicker, with more flexibility, and without having to tie up their own equipment; they can carry on with production work while simultaneously getting the knowledge from a scaled-down process.
Another benefit is that our partners have access to not just the knowledge base we provide, but the whole of the university as well. For instance, each of the GEIC's themes will have an associated academic lead that we can tap into and gain knowledge from, helping out with any problems that we have.
Could you highlight some of the potential applications where 2D material-based composites have received interest?
There are numerous areas that have received attention in this space, including mechanical properties to improve tenant strength, as well as thermal and electrical conductivity. We have also been looking into polymers and fiber-reinforced plastics, and one area in particular to highlight is lightning strike materials for aircraft or wind turbines.
Over the past few years, and even the past six months, we have noticed an increased demand globally for investigating the potential of 2D materials in composite applications.
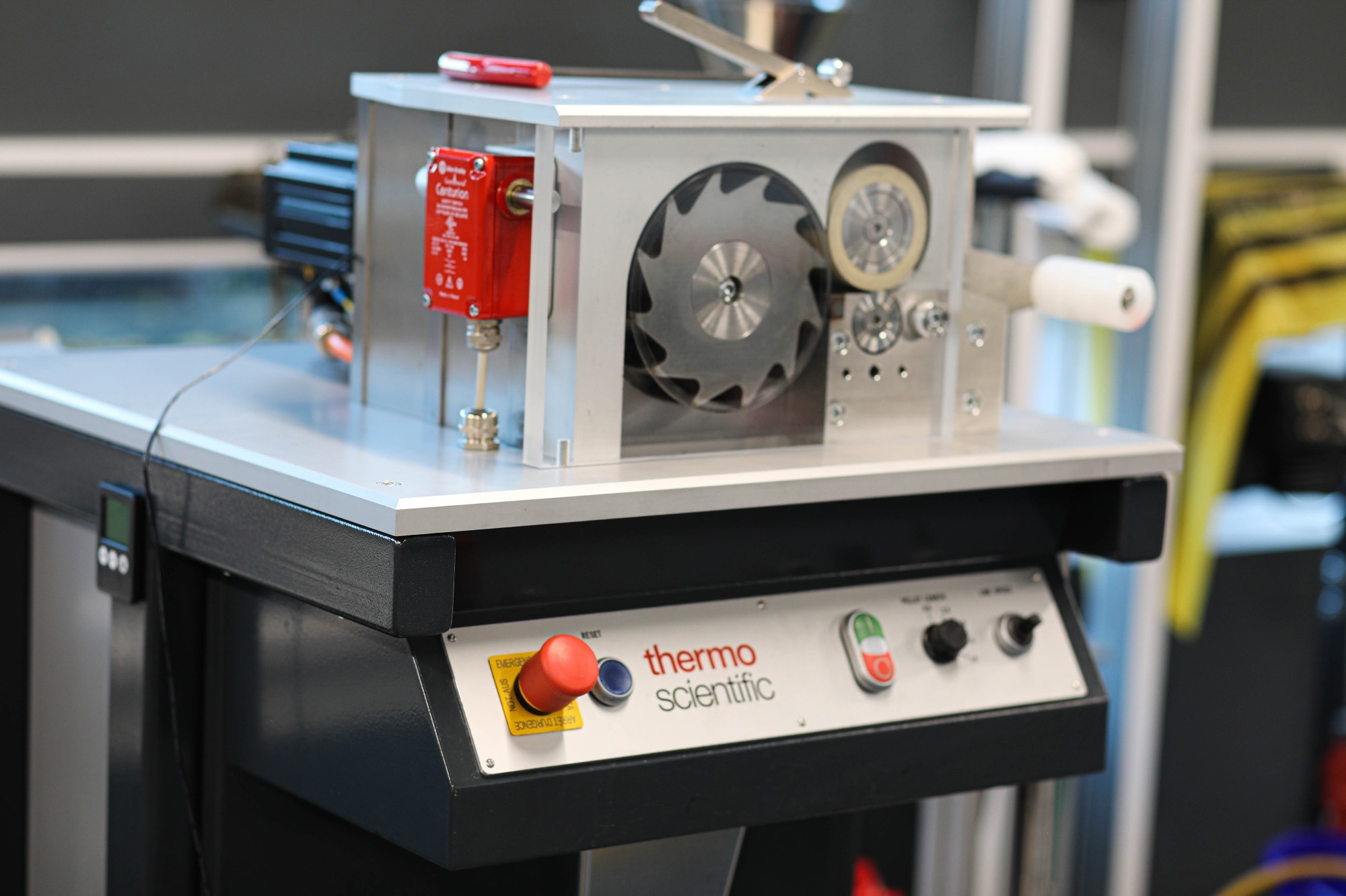
Image Credit: Joao Pinto/AZoNetwork
Are there issues with integrating 2D materials into 3D structures?
The biggest problem with getting graphene into anything is dispersion. Dispersion is the key thing with anything. Integrating graphene into one part is making sure it is within the system properly; if it is not dispersed properly, it will not give you the properties that you want. Likewise, if the material is not dispersed properly, graphene will not disperse into that polymer or a resin system properly and will not work.
Even if we make, say, a master batch here and then ship it off to a customer, there will be problems if they do not disperse it properly. To combat this, we leave the GEIC and go over to our customers to make sure that the process has been handed over properly and is going through their system correctly.
Ultimately, this process can act as a barrier to taking graphene out of research to industry if not done correctly. The beauty of the GEIC is that customers are present in the building and can actually see processes happening first-hand. Even better, they can then take this knowledge into their companies.
How might the inclusion of graphene/2D materials affect their recyclability?
We are actually working on some projects at the moment for plastics or PET, and there is a company we work for that actually recycles its materials for its bottles. We found that by adding graphene, the longevity of the material is extended - the number of times it can be recycled increases. As a result, the same material can be used over and over again for longer, and helps to delay it from going into the ground.
Another company the GEIC partners with uses recycled polymers of reds, greens, yellows and whites to make panels. These recycled materials are placed through a twin screw extruder for compounding, and after adding graphene, we have observed some promising properties.
Much interest in graphene comes from its functional properties. Could these qualities be incorporated into composites such as thermoplastics? What benefits might this add?
Already graphene has been incorporated into thermoplastic to help produce a material with desirable characteristics like mechanical properties and conductivity. Typically, there is a rule of thumb for the amount of graphene integrated into a product depending on the property: less than 1% by weight for mechanical properties and above, such as 3 - 5%, for thermal properties or conductivity. There is even evidence of 0.01% graphene being used to give good results.
At the GEIC, we have seen that integrating graphene into thermoplastics can extend the life of a polymer as well as strengthen it. We have also seen how graphene can help to reduce the amount of the material actually needed in the final product too, which is of particular interest if you are looking to create something that is lightweight as well as more sustainable.
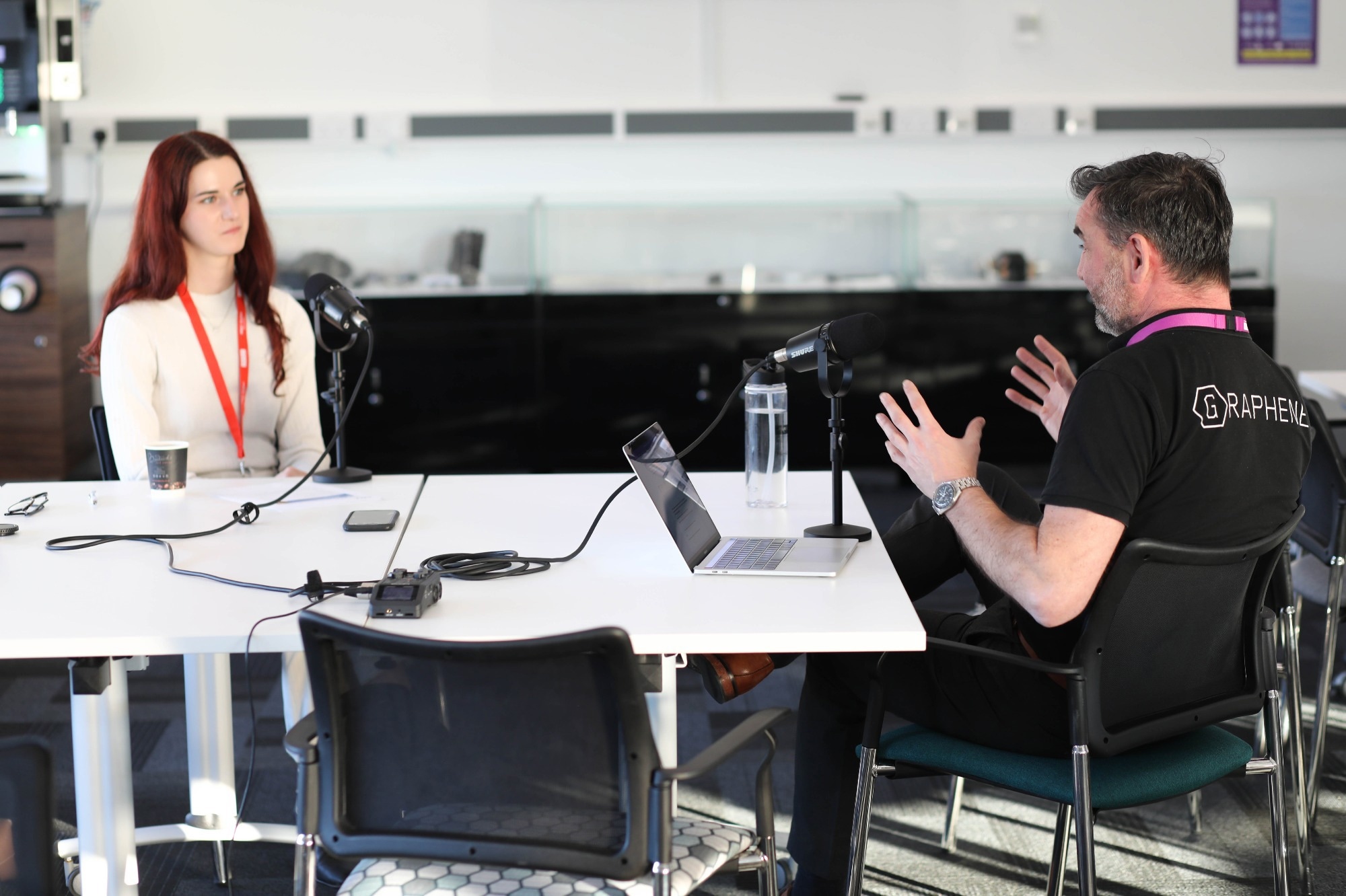
Megan Craig/AZoNano (left) and Mark Dickie (right). Image Credit: Joao Pinto/AZoNetwork
Why is it significant to improve the properties like strength and elasticity in thermoplastics, and what applications would benefit the most from this?
If you target the strength and elasticity of a material, its tensile strength, it means that you do not have to use as much of the material in a part. Imagine you have a material that bends a certain amount and, through graphene, are able to improve its properties by 50%, the overall stiffness of the material is improved. As a result, you can reduce the amount of the material being used while maintaining the same characteristics.
The GEIC houses many research groups and start-ups, offering an interdisciplinary environment to work within. Do you think that this environment has a positive impact on innovation within the center?
Definitely. There are so many different projects going on at the GEIC, from membranes to concrete to recycling rubber for rubber mats, but groups do not work in isolation. Everyone gets together, has corridor chats and shares their ideas and experiences.
Officially, the GEIC runs workshops where people at the center and our partners can come together to swap ideas, but it really is more of a family than anything else. Collaboration is really built into the ethos of the GEIC.
What has been the most memorable experience you have had at the GEIC?
Everything, all of it. It is a nice experience being able to take a customer's idea from start to finish and see it through. Knowing that at the end of a project, you have helped to create a product or new jobs successfully, and then have the partner return for another project is the best thing ever.
About Mark Dickie
Appointed to his position in February 2018 after 2 years at 2-Dtech/Versarien, Mark has 20 years of experience in the composites Industry. He was the Business Unit Manager at Caparo Advanced Composites for 3 years, and previously at Cytec for 17 years, 5 years, as Production Manager and latterly Assistant Business Unit Manager.
During the last 4 years as Application Manager for composites within the GEIC, Mark’s team have delivered projects ranging from structured composite power cells for aerospace, graphene enhanced polymers and rubbers for automotive to Graphene enhanced ceramics for the jewellery market and mixed metal matrix composites. Customer requirements range from improving mechanical properties and/or electrical and thermal conductivity and adding multifunctionality to their components.
Disclaimer: The views expressed here are those of the interviewee and do not necessarily represent the views of AZoM.com Limited (T/A) AZoNetwork, the owner and operator of this website. This disclaimer forms part of the Terms and Conditions of use of this website.