When it comes to precisely directing light in two axes, optical system designers wield several well-established technologies.
These include galvanometer mirror scanners (galvo scanners), piezoelectric fine steering mirrors, voice coil-driven steering mirrors, and kinematic mirror mounts and gimbal mounts. Each of these technologies was crafted for specific applications, and this article will outline some of their strengths and limitations.
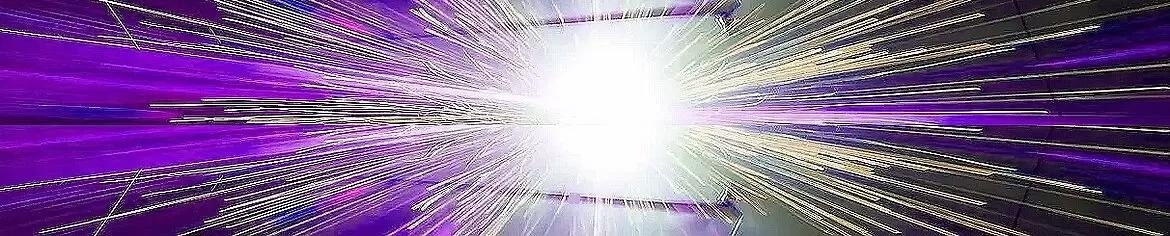
Image Credit: PI (Physik Instrumente) LP
2-Axis Galvo Scanners – 2 Individual Mirrors
These optical scanners comprise two separate, perpendicular planar mirrors that rotate independently. They are positioned in a manner wherein laser light bouncing off the first mirror (axis 1) redirects to the second mirror (axis 2) and subsequently reaches the target.
Galvo scanners are frequently used in laser material processing, benefitting from their high production volume, allowing for relatively inexpensive costs.
Because of their lightweight mirrors, they enable highly dynamic motion in closed-loop operation, achieving step response times in the sub-millisecond range. Another advantage lies in their expansive scanning field, typically around 20 degrees for both axes.
However, the drawback of the galvo scanner's dual single-axis mirror design is the polarization rotation effect it induces.
This effect can pose challenges in applications reliant on a specific polarization state, such as certain types of interferometry, the increasingly popular optical coherence tomography in dermatology, and ellipsometry. Ellipsometry is a technique for determining film properties and thickness optically.
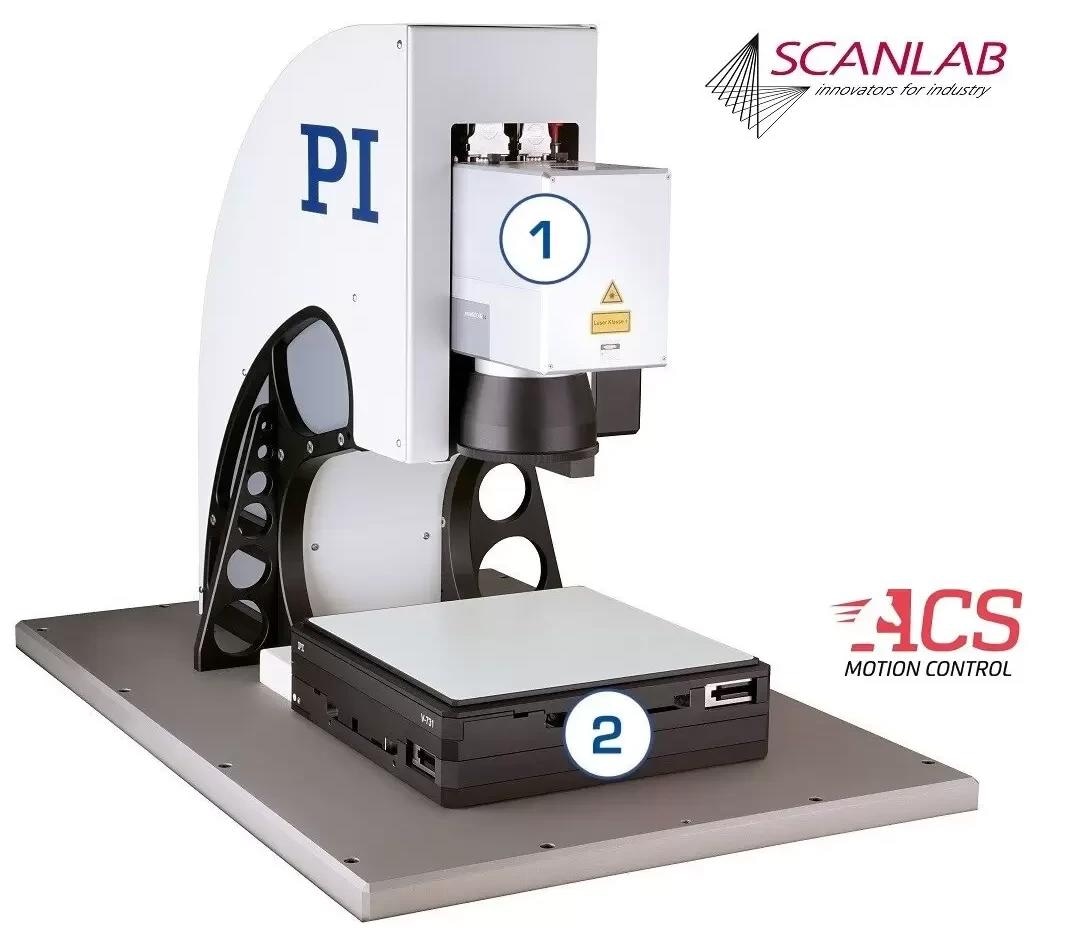
A high precision laser processing demonstrator, based on a Scanlab 2-axis galvo scanner and 2-axis XY linear stage for virtually infinite field of view operation. Combining the linear motion provided by the XY-stage with the high-bandwith angular deflection of the galvo scanner improves both the detail precision and throughput. The ACS motion controller allows for continuous operation over large areas, avoiding idle time and eliminating stitching errors. Image Credit: PI (Physik Instrumente) LP
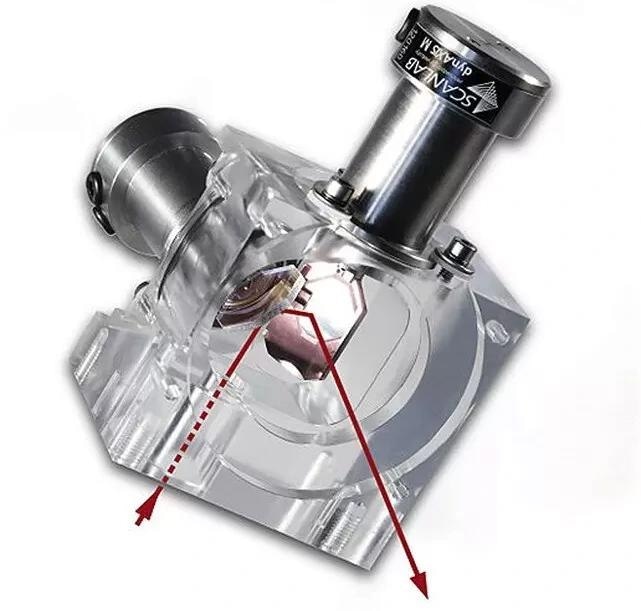
Basic design of a 2-axis galvo scanner with laser beam path. Image Credit: Wikipedia / Scanlab
Expert Interview: Increase Speed and Accuracy of Photonic Test & Assembly w/Advanced Motion Control
Laser Machining - Large Area, High Throughput, High Path Accuracy: PI Motion Systems & Controls. Synchronized motion of high-bandwidth galvo scanners and 2-axis linear motor stages - working together to extend the field of view in precision laser processing applications. Video Credit: PI (Physik Instrumente) LP
Single Mirror, 2-Axis Scanners with Fixed Pivot Point for Both Axes
A) Piezoelectric 2-Axis Steering Mirrors
Fast steering mirrors using piezoelectric technology can shift a single mirror along two axes around a fixed pivot point. This design retains light polarization, shrinks the overall size, and boosts durability.
Frictionless flexures guide the mirror's movement, ideal for small angles and high accelerations achievable with piezo drives. These flexures do not need lubrication, are maintenance-free, work in high vacuum, and handle broad temperature ranges.
Piezoelectric actuators swiftly respond to changes in voltage. Their speed depends on the piezoceramic material's speed of sound. For small elements, microsecond response times are possible.
While traditional direct-drive piezo mirrors were limited to a few milliradians in angular range, new designs using flexure motion amplifiers can deflect light up to 70 mrad (4°).
Strain gauges are built into these mirrors for high-bandwidth, closed-loop operation, and linearization. Using a differential drive design with two actuator pairs operating in a push-pull mechanism greatly enhances angular stability across various temperatures compared to a single actuator/axis approach.
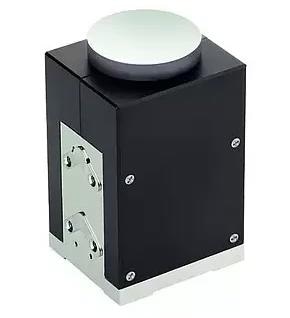
The S-335 integrated, single-mirror, 2-axis piezo scanner for fast beam steering mirror employs flexure motion amplifiers to extend its angular range. 2 angular ranges are available – shorter travel allows for higher frequencies. Image Credit: PI (Physik Instrumente) LP
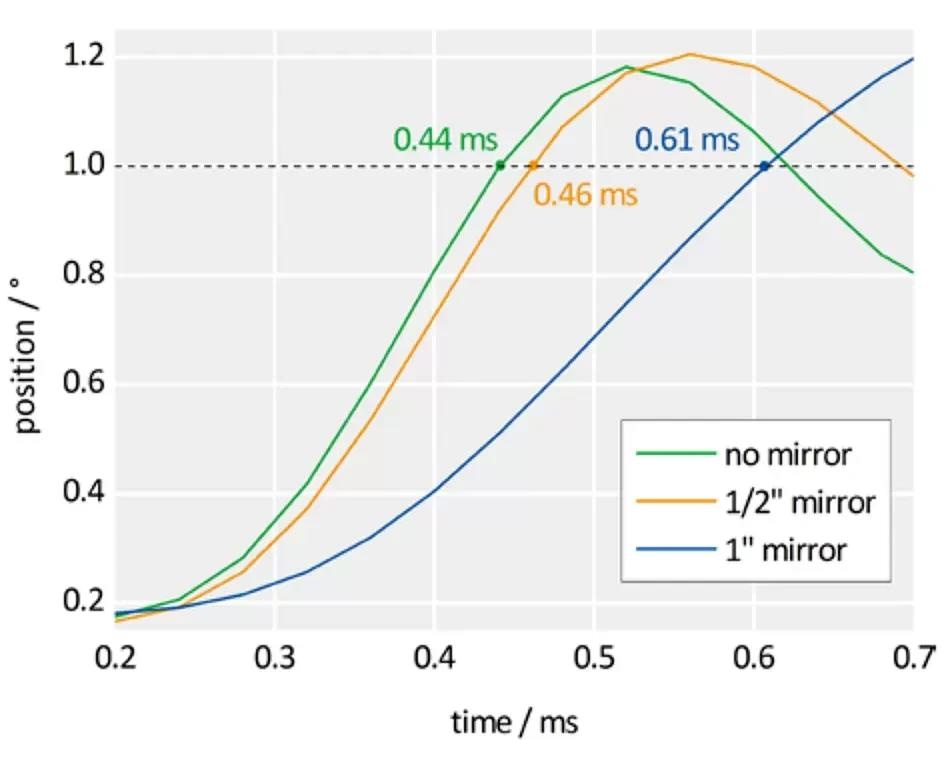
Open loop step performance of an S-335.2SH, 2-axis piezo steering mirror mount: unloaded, ½” and 1” mirror. The selected step size is 50% of the max range: 17.5 mrad ~1 degree. Image Credit: PI (Physik Instrumente) LP
Flexure-guided piezo mirror scanners are maintenance-free, work in ultra-high-vacuum environments, and can be tailored for space operations.
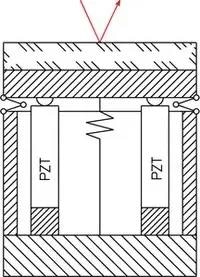
Basic design of a fast steering mirror with differential piezo (PZT) actuation (push/pull). One of the advantages is angular insensitivity to temperature changes. Image Credit: PI (Physik Instrumente) LP
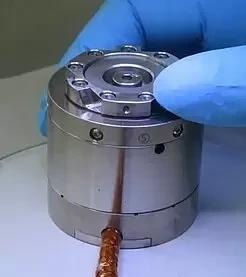
A space-qualified integrated 2-axis piezo steering mirror mount used on the secondary mirror of the PHI telescope on the solar-observing satellite. This compact unit with diameter of a 45 mm is only 44 mm tall and weighs 255 g. The mirror mounted on the tip/tilt platform weighs 71 g and is made of Zerodur. Image Credit: PI (Physik Instrumente) LP
Fast Laser Steering Mirror Mounts for 2-Axis Beam Control, Optical Communication. Piezo & Voice Coil
Fast Laser Steering Mirror Mounts for 2-Axis Beam Control, Optical Communication. Piezo & Voice Coil. This video shows a piezo-driven 2-axis fast steering mirror scanner in an 8x8 laser-fiber-coupling / switching demo, showing the mechanical basics required for beam control in free space optical communication.Video Credit: PI (Physik Instrumente) LP
Advantages of piezo-driven steerable mirrors over galvo scanners include:
- Parallel kinematics (coplanar multi-axis motion without polarization rotation)
- The quadra-pod differential drive design (in S-335 and S-330 model families) runs two orthogonal axes with a fixed pivot point based on two pairs of actuators operating in push/pull mode.
- Channels/Axes can be operated simultaneously or independently, due to the paired piezo actuators in the design.
- Piezoelectric solid-state properties provide for fast response (sub-millisecond) and high resolution (down to the nanoradian range).
The reliability of piezo flexure-guided steering mirrors is high due to the lack of any wearing parts. Tests demonstrated lifetimes of over 2 billion cycles without failures or degradation. NASA life-tested the actuators integrated into the steering mirror for 100 billion cycles for the Mars mission.
Theta-X, Theta-Y, and Path-Length Modulation
Another parallel-kinematic steering mirror solution uses a tripod piezo stack design. Along with Theta-X and Theta-Y rotation, this design modulates path length with sub-nanometer precision (phase modulation).
B) Voice Coil-Driven, Flexure Guided 2-axis Steering Mirrors
An alternative approach for a single-mirror, 2-axis scanner utilizes voice-coil motors and flexure guides.
Due to the extended travel range of voice-coil motors, larger angular spans can be achieved (beam deflection angles approaching 10 degrees in both Theta-X and Theta-Y). Employing a quadra-pod differential drive design enables excellent temperature stability.
Differences between Piezo Drives and Voice Coil Drives
Although piezo actuators are inherently rigid and can maintain a position with minimal energy consumption and heat loss, voice coils lack inherent holding force when de-energized and require power to maintain a position.
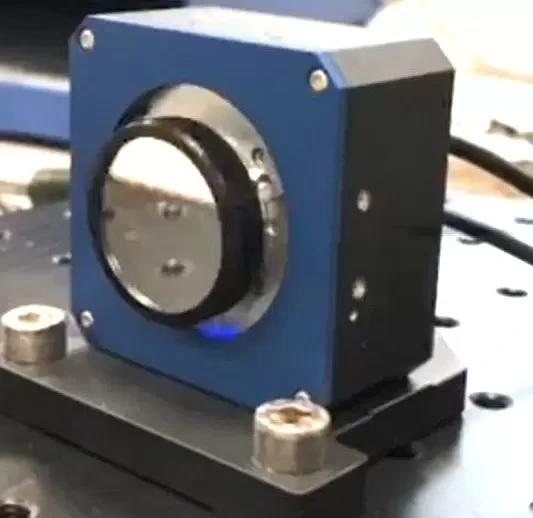
Compact, integrated voice-coil-driven 2-axis fast steering mirror module with single moving mirror platform. Image Credit: PI (Physik Instrumente) LP
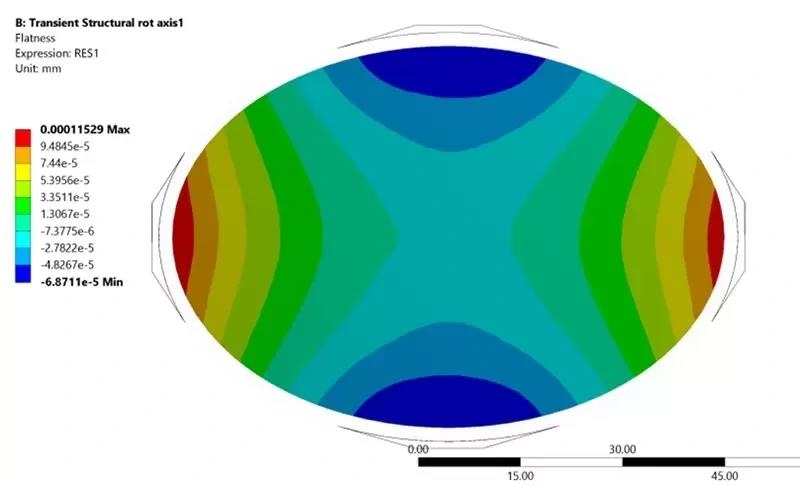
Simulation of mirror surface deformation / flatness. Image Credit: PI (Physik Instrumente) LP
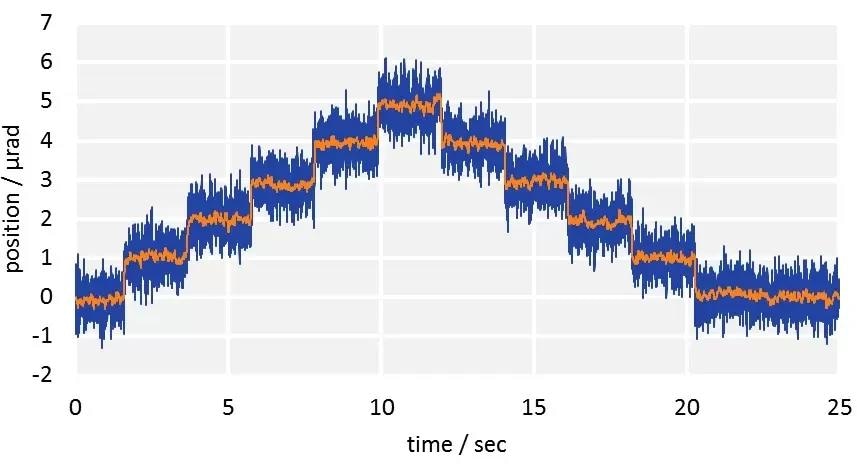
1µrad steps performed with a V-931 voice-coil driven two-axis steering mirror. Image Credit: PI (Physik Instrumente) LP
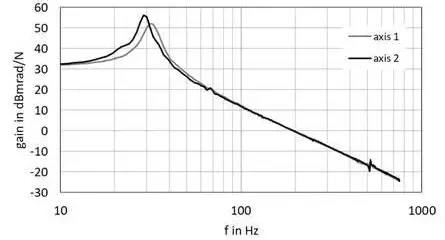
Bode plot of the voice coil 2-axis steering mirror. Image Credit: PI (Physik Instrumente) LP
2-Axis Motorized Kinematic Mirror Mounts
Designed for Set-and-Forget Optical Alignment Applications with High Stability
Most commercially available kinematic mirror mounts allow active adjustments in two axes, often utilizing micrometers or fine-pitch screws. Kinematic mounts are frequently employed in laser systems to precisely adjust the beam path and then sustain the optimal position with very high stability.
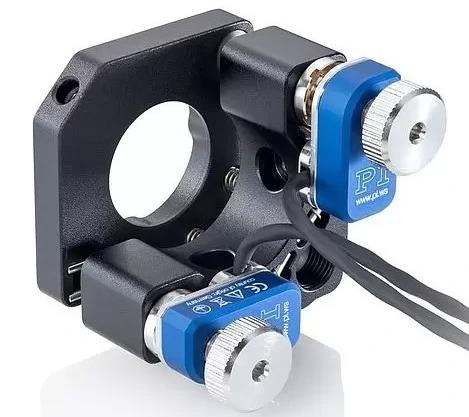
Example of a motorized optical kinematic mirror mount. This unit provides up to 16 degrees of rotation in Theta-X and Theta-Y. High precision piezo motors drive the fine adjustment screws and provide angular step resolution to 0.3 µrad. Image Credit: PI (Physik Instrumente) LP
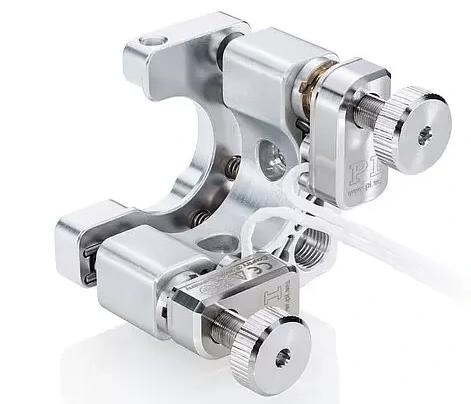
A vacuum-compatible motorized kinematic mirror mount. Image Credit: PI (Physik Instrumente) LP
Motorized variations permit remote control, automatically compensating for variations in system performance or returning a complex optical system post-shipping. As the axis of rotation of a kinematic optical mirror mount is situated behind the mirror, the adjustments of both axes are not entirely independent.
A slight linear beam translation occurs with every angular adjustment, causing the axes to deviate from perfect orthogonality to the optical axis. Typically, kinematic mirror mounts offer larger angular ranges compared to high-bandwidth piezo and voice coil steering mirrors but usually less than 20 degrees.
Gimbal Mounts
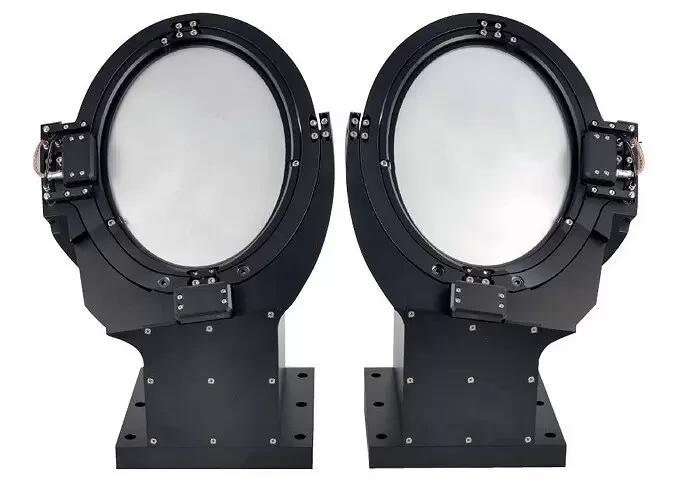
Custom, 2-axis gimbal mounts with ultra-high precision piezo linear motors. Image Credit: PI (Physik Instrumente) LP
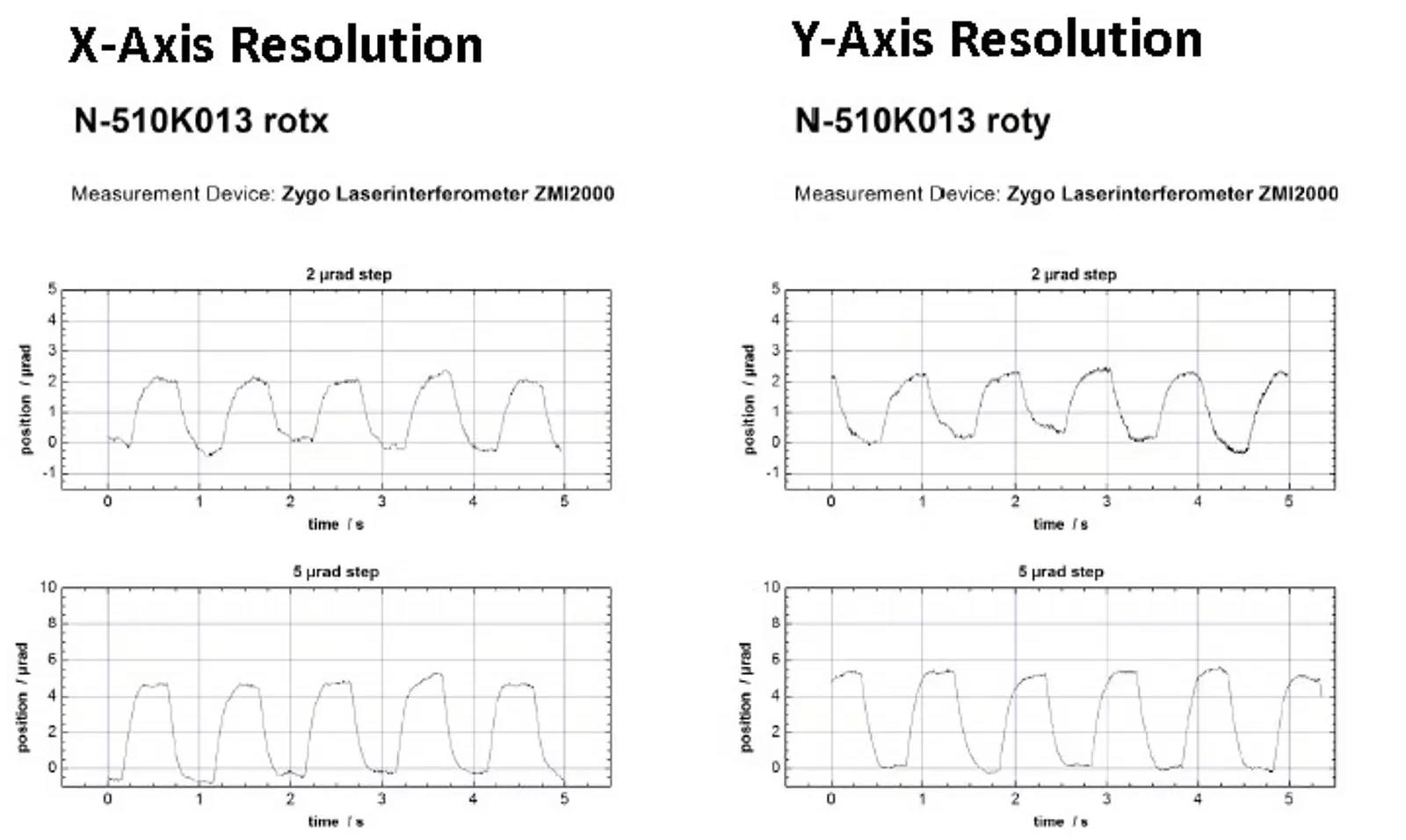
Test results showing 2 µrad and 5 µrad steps, measured with Zygo ZMI2000 laser interferometer. Image Credit: PI (Physik Instrumente) LP
The most substantial angular deflections come from gimbal mount designs. Gimbals can provide rotation up to 360 degrees in 1, 2, or 3 axes.
The axes of a 2-axis optical gimbal mount intersect at the front and center of the attached optic, remaining perfectly orthogonal. Gimbals, designed for large mirror diameters and equipped with direct-drive motors, are often employed in high-precision tracking applications.
Steering Light – What Technology Works Best for Your Application?
Fast Piezo Mirror Mounts for Laser Beam Steering: Laser Eye Surgery with FSM - Piezo Tip/Tilt | PI
Fast Piezo Mirror Mounts for Laser Beam Steering: Laser Eye Surgery with FSM - Piezo Tip/Tilt. Principle of fast multi-axis piezo mirror mounts for laser beam steering in eye surgery. Video Credit: PI (Physik Instrumente) LP
Fast Deformable Piezo Mirror improves Laser Beam Steering, Focusing Welding & Cutting
Fast Deformable Piezo Mirror improves Laser Beam Steering, Focusing Welding & Cutting. Fast deformable piezo mirror improves laser beam steering, focusing welding & cutting. Video Credit: PI (Physik Instrumente) LP
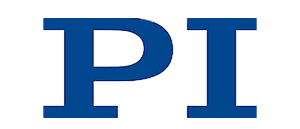
This information has been sourced, reviewed and adapted from materials provided by PI (Physik Instrumente) LP.
For more information on this source, please visit PI (Physik Instrumente) LP.