From InovensoReviewed by Olivia FrostJan 14 2025
Can you please introduce yourselves and your current roles?
Ronish Shrestha (RS): I am Ronish Shrestha, the lead scientist and engineer at Materic. My background is in chemical engineering, and I have been leading our electrospinning projects for about two years.
At Materic, I oversee the research, optimization, and commercialization of these electrospun products, ensuring we bring innovative materials from the lab to full-scale production.
Waleed Mustafa (WM): I am Waleed, the customer support specialist and R&D engineer at Inovenso. We provide innovative, customized electrospinning solutions and help clients across various industries navigate the challenges of scaling up nanofiber production.
What is Materic’s primary focus in material science, and how has electrospinning contributed to your projects?
RS: Materic’s primary mission is to develop advanced materials and take them from concept to large-scale production. We are actively involved in cutting-edge fields like nanomaterials, specialty textiles, controlled-release systems, and electrospun products.
Electrospinning has been a huge focus, especially for creating high-performance nanofibers with specific properties, such as gas diffusion layers (GDLs) for fuel cells. We work with various clients and agencies, customizing materials and production processes to fit each project’s requirements.
Can you explain how Materic is working to commercialize carbon nanofiber mats for gas diffusion layers in fuel cells and what role the Department of Energy’s $10 million contract plays in this effort?
RS: We are thrilled to be part of the “SPIN into Power” project, which is funded by the U.S. Department of Energy (DOE) with a $10 million contract. This project involves scaling up our electrospun carbon nanofiber mats to serve as GDLs in fuel cells.
GDLs play a crucial role in regulating gases within fuel cells, and the nanofiber structure we produce through electrospinning enhances performance due to its fine morphology and high tunability.
Our goal with the DOE contract is to build a manufacturing line that can produce over 65,000 m2 of GDL material per year, addressing about 10 % of the national demand for this component.
Collaborating with Los Alamos National Labs, Plug Power, and the University of Toronto has also been essential in pushing this project forward and ensuring we meet the DOE’s high standards for clean energy.
What are the key phases in scaling up electrospun products from lab-scale to commercial production, and what challenges do you encounter at each phase?
RS: For us, scaling up is a multi-phase process, broken down into three key stages: lab-scale, pilot-scale, and commercial-scale production.
The concept begins at the lab scale. We typically work with research-grade chemicals and small prototypes to test the technology; however, the methods used at this stage do not translate directly to industrial production because they are often too specific to research environments.
The pilot scale is where things start to get exciting—and challenging. At this stage, we shift from a single-needle setup to multi-nozzle systems to produce larger rolls of material. We also work closely with customers to ensure we use commercially viable chemicals and materials, addressing any scalability or toxicity issues that might arise as production increases.
At the commercial scale, the focus shifts toward meeting production and cost targets rather than just technical specifications. This phase requires refining the methods developed in the pilot phase to operate on large commercial machines. The transition from pilot to commercial scale emphasizes economics and quality control rather than the highly technical challenges of the lab-to-pilot shift.
Each phase brings new challenges, especially in managing environmental controls and aligning production with regulatory and commercial standards.
How do you optimize materials and processes during the pilot phase to ensure a smooth transition to commercial-scale production?
RS: Optimization is critical during the pilot phase because this is where we develop scalable procedures. One big part is choosing cost-effective chemicals and materials readily available in bulk. We also emphasize creating a reproducible process, meaning we must see consistent results across different conditions.
This is especially true when moving from a batch to a continuous process; we adjust parameters, like the number of nozzles and the material flow, to prevent quality degradation as we scale up. By the time we reach commercial production, we want minimal deviations in our output.
What major challenges do you face when scaling up the electrospinning process, especially regarding environmental control and transitioning from batch to continuous production?
RS: One of the main challenges in scaling up is controlling the environment, especially humidity. Some of the solvents we use are moisture-sensitive, which can lead to defects in the nanofiber mats if the air is not carefully regulated. In the pilot phase, we have developed a dedicated clean room with HVAC and dehumidification systems to tackle these issues effectively.
When transitioning from batch to continuous production, we often encounter problems related to consistency and quality. A pilot system running continuously introduces issues like fiber build-up or electrostatic interference, which can affect the overall quality of the mats. Keeping all parameters steady—temperature, humidity, or solvent recovery—is crucial for ensuring we get a uniform product at the commercial scale.
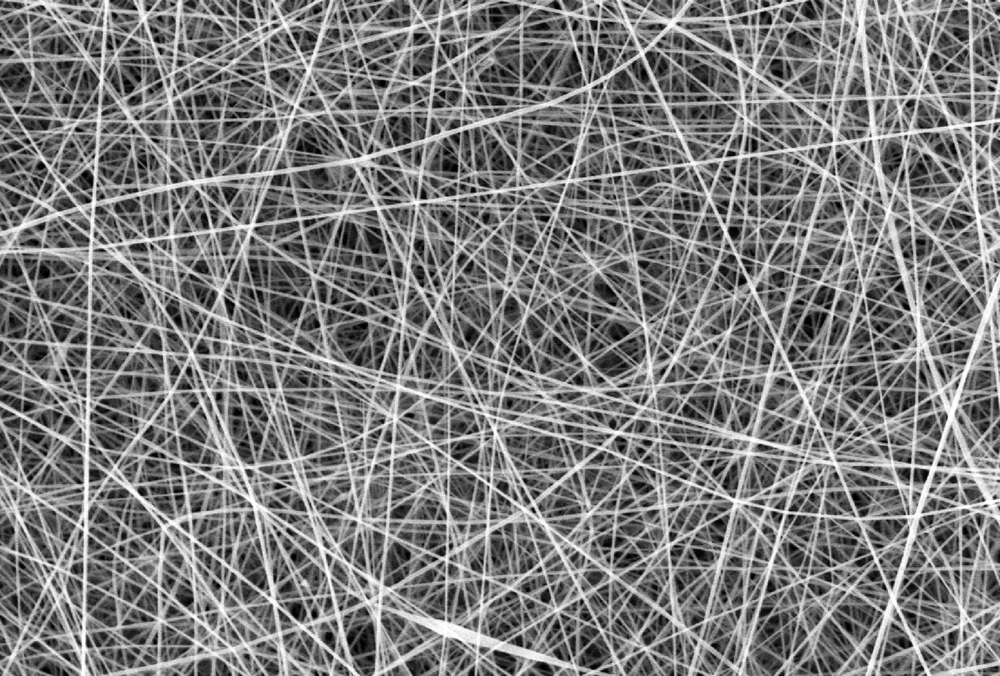
Image Credit: Smartlearnskills/Shutterstock.com
How do hybrid and open-surface electrospinning technologies help overcome some limitations of traditional needle-based electrospinning systems?
WM: At Inovenso, we have developed hybrid and open-surface electrospinning technologies to address some common limitations in traditional needle-based systems. For example, needle-based systems often suffer from clogging, limited throughput, and high waste. Our hybrid technology allows multiple jets to form from a single source, reducing the risk of clogging and boosting productivity.
On the other hand, open-surface electrospinning is even more efficient for large-scale production. This bottom-up approach significantly increases throughput by generating spontaneous jets, making it ideal for industrial applications. By using these advanced systems, we can better support companies like Materic in reaching high production volumes while maintaining consistent quality.
How has Materic’s collaboration with Inovenso improved the scalability and efficiency of electrospun products?
RS: Working with Inovenso has been incredibly valuable for us. Their expertise in designing lab-scale and industrial-scale electrospinning machines helps us overcome the technical barriers in scalability.
Their hybrid and open-surface systems give us more control over production and improve efficiency by minimizing downtime and material waste. Inovenso’s support with custom machinery also allows us to push the limits of what we can do with electrospinning, helping us transition from the lab to commercial scale more seamlessly.
What are some promising applications of electrospun nanofibers that Materic is currently working on, particularly in energy, healthcare, and filtration?
RS: We are involved in various exciting applications for electrospun nanofibers. Our work with the KoylaWeb carbon nanofiber mats as gas diffusion layers for fuel cells is particularly promising in the energy sector. These mats help fuel cells operate more efficiently and could make clean energy more accessible.
In healthcare, we are developing electrospun mats that incorporate active pharmaceutical ingredients for controlled-release systems and biocompatible scaffolds for tissue engineering.
We also have filtration projects, where we are creating nanofiber filters for water treatment and air purification. One of these is collaborating with the EPA on biodegradable filters for wildfire smoke.
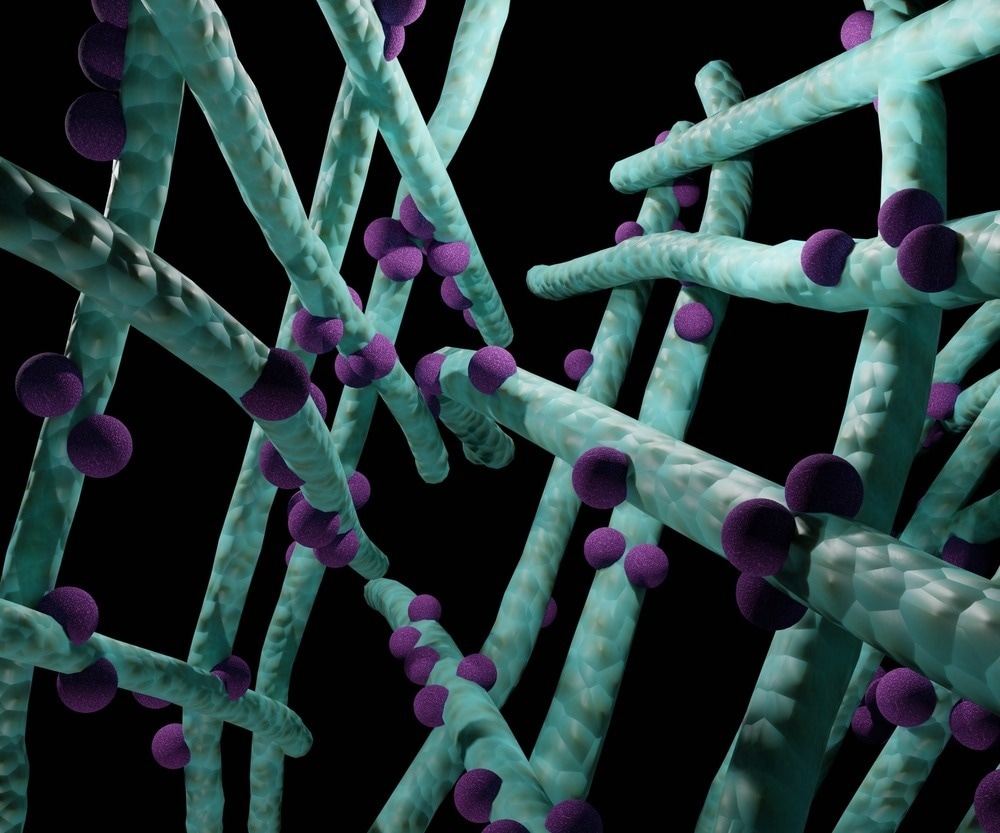
Image Credit: Love Employee/Shutterstock.com
Looking forward, how do you see the field of electrospinning evolving, and what new innovations or applications are you excited about for the future?
RS: The field of electrospinning is evolving rapidly. Technologies like Inovenso’s open-surface electrospinning are pushing the boundaries of production capacity.
New variations of electrospinning, like coaxial and hybrid techniques, also allow us to produce complex fiber structures that open doors to new applications, such as smart textiles and advanced biomedical devices.
Electrospinning’s role in energy and environmental applications will grow significantly, especially as the demand for clean energy and sustainable materials increases.
I am also hopeful that as we continue to innovate, we will find new ways to overcome current limitations and expand the range of substrates and materials we can use, making electrospinning even more versatile across industries.
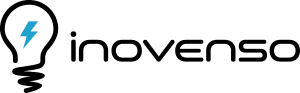
This information has been sourced, reviewed, and adapted from materials provided by Inovenso.
For more information on this source, please visit Inovenso.
Disclaimer: The views expressed here are those of the interviewee and do not necessarily represent the views of AZoM.com Limited (T/A) AZoNetwork, the owner and operator of this website. This disclaimer forms part of the Terms and Conditions of use of this website.