Sponsored by ELMARCOReviewed by Louis CastelDec 3 2024
Nanofiber membranes have long been used to filter air, yet scientists have only tested them as water filters since 2020. For some time, the elevated pressure the membrane must withstand when filtering liquids has resulted in the belief that nanofibers are too fragile for this use case, but research has proven them to be completely capable of this task. Precautions should, however, still be taken when filtering oil and fuel.
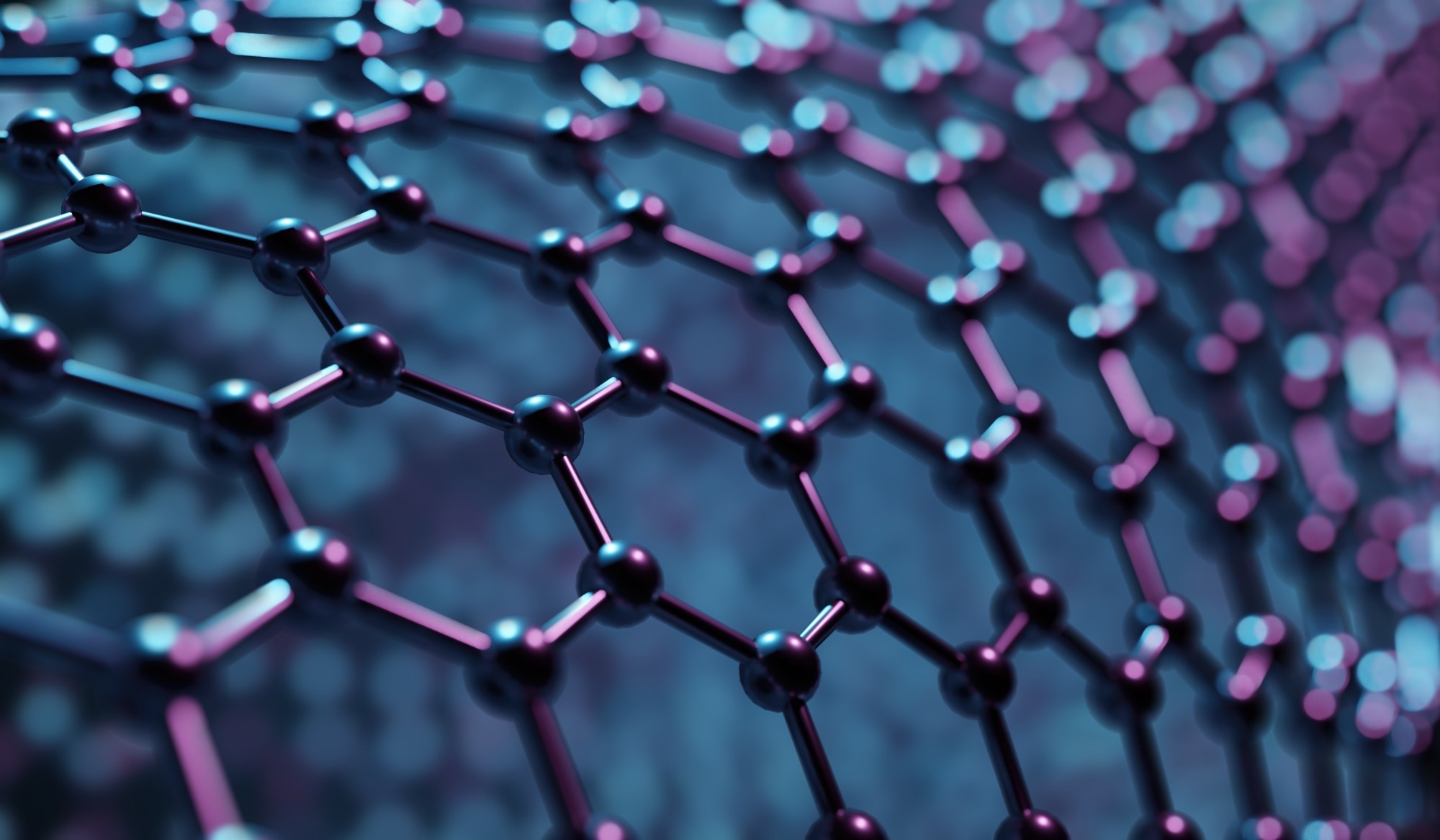
Image Credit: vchal/Shutterstock.com
Issues with Filtration Materials
Oil filtration media have at least two layers in practice, but typically three or more. Porous filtration materials like cotton, polyester, and non-woven fiberglass fabrics segregate particles from a liquid.
These widely used materials also have significant drawbacks, including a greater pore diameter and fluctuating pressure, making them less effective as filters. This has led to filters being made with electrospun nanofibers.
Advantages of Nanofiber Filters
A 2014 study by Jian Yong Feng found that a filter with a cotton foundation layer overlaid with a layer of smaller pore diameter nanofibers produced elevated levels of oil/fuel filtration accuracy. The large surface area-to-volume ratio more effectively optimized the capture of dangerous particles from the liquid.
Oil filter nanofibers are electrospun using NanospiderTM. The filtration process is split into two phases. The first is stable, and filtration efficiency does not vary as time passes. The second phase is known as “unstable,” and filtration efficiency reduces in accordance with particle sedimentation.
Oil and Fuel Filtration Efficiency in Practice
In 2015, research engineer Russ T. Bretell co-authored Diesel Fuel Challenges and Nanofiber Media Filtration Solutions, a study discussing two nanofiber filters used for cleaning automotive fuel.
He demonstrated by example how the first kind of nanofilter operates, focusing on particles as small as four microns. “If 100,000 particles enter the filter and 1,333 pass through, the efficiency is 98.7 %. Compared to a filter without nanofibers, this performance is good, but it can be improved.”
The second nanofilter could remove particles of the same size with an efficiency of 99.9 %. Bretell noted that while this was just a 1.2 % improvement, from the same 100,000 particles, just 100 particles would enter the fuel, meaning that 1.2 % enhanced efficiency was, in fact, a 13-fold improvement compared to conventional filtration methods.
Elmarco S.R.O. has built a series of products that electrospin nanofibers via NanospiderTM technology. The experts at Elmarco are studying nanofibers and exploring their benefits for filtering oil. They have found:
- Nanofibers in the same material can catch particles up to 5 µm with close to 100 % efficiency (99.6-99.9 %).
- Nanofilters with a minimum 99.2 % efficiency or more can catch particles spanning up to 30 µm.
- Filtration efficiency declines as pressure on the filter increases.
- Nanofilters are most effective in separating particles from fuel soon after filtration starts.
- Filter lifetime can be calibrated to maximize permissible differential pressure.
Filter Fuel in Cars to Reduce Engine Wear
Contemporary vehicles are technologically advanced high-pressure fuel systems. Injection systems are crucial for optimal engine performance and fuel economy. Apart from fuel delivery and consumption efficiency and performance, the negative pressure generated when fuel is injected should also be managed.
Impurities in just one full tank can harm a fuel system. According to the Worldwide Fuel Charter (WWFC), up to 50 % of the world’s diesel fuel supplies do not meet ISO 18/16/13.
This ISO is an internationally recognized purity code for assessing particulate content in fuel. WWFC reports indicate that oil is becoming dirtier.
Fuel purity test results are reported in 18/16/13 format, where 18 is the code for particles 4 µm or bigger, 16 is the code for particles 6 µm or bigger, and 13 is the code for particles 14 µm or bigger.
Not visible to the naked human eye, these impurities prematurely wear out injectors’ internal parts, diminishing engine performance, increasing fuel consumption, and leading to costly damage. Unlike air filters, fuel filters lose efficacy as time passes.
Contemporary fuel filters cannot eliminate the same quantity of dirt at the end of their lifecycles as when first installed. The flow of fluid persists, however, even when the filter has lost its effectiveness, pushing impurities into it and leading to a condition known as “filter load.”
A fuel filter’s efficiency is additionally influenced by “fuel impact” on the membrane surface. This happens when initiating the engine, as fuel impact on the filter is at its peak, and there is an elevated likelihood of impurities contaminating the fuel.
Four Layers for More Effective Filtration
Filters that contain nanofibers are more effective. Fully synthetic, multi-layer nanomedia are reasonably capable of filtering out contaminants down to 4 µm in size and are now becoming candidates for fuel filtration.
Their synthetic composition keeps the filter from becoming vulnerable to damage or liquid saturation, often a problem with traditional membranes. Fuel tanks found in luxury cars have a four-layer fuel filter. They comprise a base layer, a meltblown layer, a nanofiber layer, and another meltblown layer.
References and Further Reading
- Feng, J.Y., Zhang, J.C. and Yang, D. (2014). Preparation and Oil Filtration Properties of Electrospun Nanofiber Composite Material. Journal of Engineered Fibers and Fabrics, 9(4), p.155892501400900. https://doi.org/10.1177/155892501400900413.
- Qin, X.-H. and Wang, S.-Y. (2006). Filtration properties of electrospinning nanofibers. Journal of Applied Polymer Science, 102(2), pp.1285–1290. https://doi.org/10.1002/app.24361.
- https://www.cumminsfiltration.com/sites/default/files/LT36443.compressed.pdf
- Natarajan, R., Kapoor, R. and Tiwari, M. (2008). Performance Characterization of Nanofibers on Fuel Filtration Media in Automotive Filters. SAE International Journal of Materials and Manufacturing, 1(1), pp.465–471. https://doi.org/10.4271/2008-01-1051.
- Zhang, H., et al. (2022). Water-/Oil-Repellent Polyacrylonitrile Nanofiber Air Filter Modified with Silica Nanoparticles and Fluorine Compounds. ACS Applied Nano Materials, 5(6), pp.8131–8141. https://doi.org/10.1021/acsanm.2c01247.
- Khude, P. (2017). Nanofibers for High Efficiency Filtration. Journal of Material Science & Engineering, 06(06). https://doi.org/10.4172/2169-0022.1000399.
- https://www.elmarco.cz/ns-technologie

This information has been sourced, reviewed and adapted from materials provided by ELMARCO.
For more information on this source, please visit ELMARCO.