RHK Technology’s SPM control systems have been used world over by leading researchers for the past two decades. Highly specialized inertial piezo motors are often needed for nanoscale motion and position control of system parts in scanning probe tools. In order to handle strong frictional holding forces between the piezo and the secondary component, the piezo motors require a very swift change in voltage. Special high voltage amplifiers with rapid slew rates are the solution.
RHK’s PMC 100 piezo motor controller can generate such a signal and also has the capacity to direct it to nine different outputs to enable nine separate motors to operate.
The low voltage shape of the waveform output (before the high gain amplification stage) is shown in the diagram to the left. The slow rise segment (A) expands the piezo element, and then the rapid drop (B) contracts the piezo suddenly, overcoming the static friction between it and the moving component. Speed of inertial motion is controlled by varying the time (t) between sweeps or the period (p) of cycle.
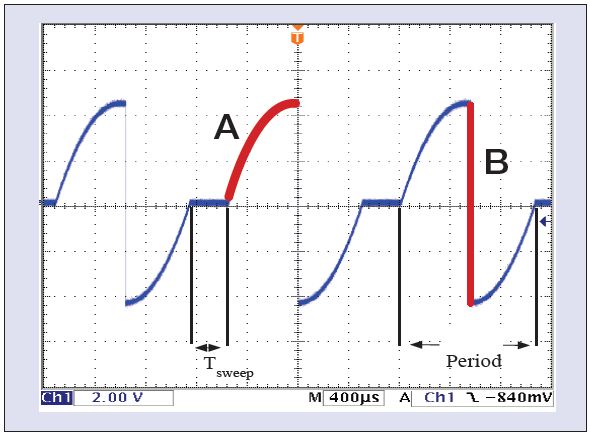
The PMC 100 controller package includes the following components:
- PMC 100 control electronics
- Computer interface and software
- Remote control handset
- Ethernet hub
- Interconnecting cables
- 100-baseT cables
Key Features
The main features of the PMC 100 controller are listed below:
- Can be efficiently operated independently or with an R9 control system
- Supports both software
- Front panel LED displays output fault
- Separate channel configuration for all operations
- AND remote handset operation
- Remote operation capability over TCP-IP
- Outputs shorted to ground when not in operation