The Institute of Electron Technology (ITE) engineers have designed silicon-based micromechanical valves utilizing process technologies of semiconductor materials. These silicon microvalves belong to the MEMS category.
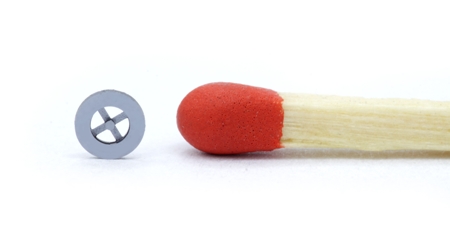
ITE has developed a check valve that does not need a control mechanism and a through-flow valve that is controlled electronically using a piezoelectric stack. The key components of these two valves are uniquely designed micrometer-accurate sockets and silicon membranes. According to one of the designers, Pawe³ Kowalski, the silicon microvalves are capable of delivering tightness down to µL/min even at high pressures.
When pressure is applied in the flow direction of the check valve, its silicon membrane deforms, making fluids to flow freely. The membrane presses against an inlet orifice when pressure is applied in the reverse direction, thus stopping the flow of fluid. Pressure range and the valve’s sensitivity are based on the thickness of brackets clasping the silicone membrane in position above the orifice.
In the through-flow valve, the piezoelectric stack is attached to the silicon membrane. The stack contracts or expands with respect to the applied voltage, causing the silicone membrane to deform, which in turn controls the flow of the fluid. Pressure range can be proportionately increased by either increasing the applied voltage or the size of the piezoelectric stack.
The silicon components of the two valves are made of high-cost processes, including photolithography, plasma etching, and deposition of aluminum and silicon oxides. However, the unit price can be significantly decreased, thanks to the way of producing several working components in a single production cycle using a single silicon plate.