New research published in the journal Polymers aimed to re-purpose waste acids generated from the production of Graphene Oxide via the Hummers method.
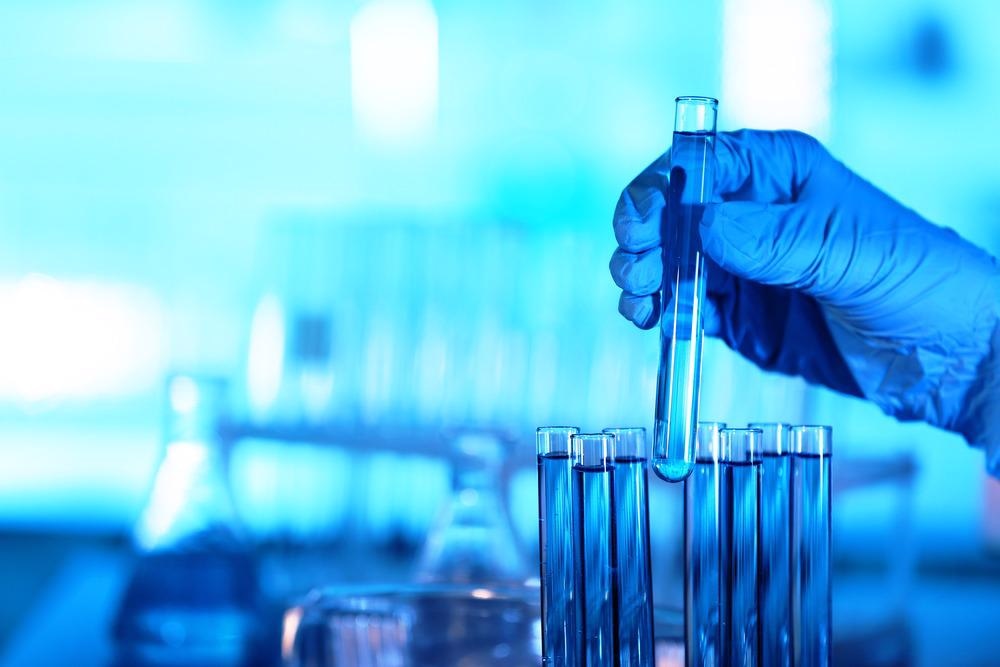
Study: Preparation of Graphene Oxide/Cellulose Composites with Microcrystalline Cellulose Acid Hydrolysis Using the Waste Acids Generated by the Hummers Method of Graphene Oxide Synthesis. Image credit: Africa Studio/Shutterstock.com
Importance of Graphene Oxide
Graphene oxide (GO), an essential oxygen-containing derivative of graphene, offers the benefits of low manufacturing cost, commercial manufacturing, and excellent stability. It is frequently utilized as a predecessor in the production of reduced graphene oxide (RGO).
With more studies on GO recently developing, researchers have discovered its excellent performance due to rich active oxygen-containing functional groups.
These oxygen-containing groups have the potential to serve as catalytic activity centers. The surface modification of graphene oxide has advanced significantly. It has been used in applications such as desalination plants, medication delivery, petroleum segregation, chemical catalysis, photovoltaic panels, power storage, and medical treatment.
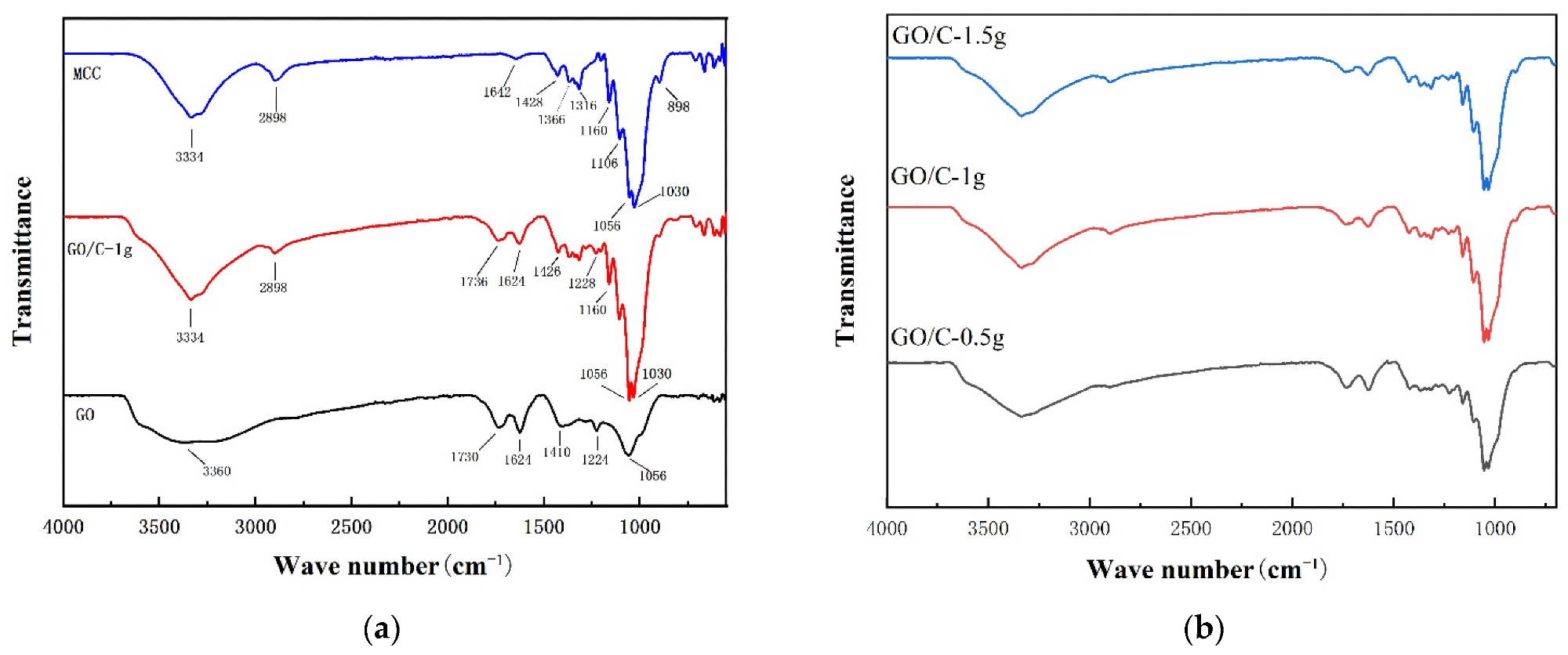
The FTIR spectra of (a) microcrystalline cellulose (MCC), graphene oxide (GO), GO plus 0.5 g MCC composite (GO/C-1 g); (b) GO plus 0.5 g MCC composite (GO/C-0.5 g), GO plus 1 g MCC composite (GO/C-1 g), and GO plus 1.5 g MCC composite (GO/C-1.5 g). © Miao, Y. et al., (2021)
Preparation Processes and Limitations
The Brodie approach, Staudenmaier method, and the Hummers method are the most developed GO preparation methods. Under long response circumstances, the Staudenmaier and Brodie methods have the drawbacks of generating toxic fumes such as ClO2 and NO2 throughout the reaction, occupying far too much time, and consuming too many raw materials.
As a result, when graphene oxide is utilized in experimental processing and commercial production, the Hummers technique is commonly used as the synthesis process.
The Hummers Method
In comparison to prior technologies, the Hummers approach offers significant benefits such as a short processing time. However, this approach has some space for improvement, such as having too much acid waste that is difficult to remove and insufficient GO oxidation degree.
Because of this, numerous researchers have developed various modifications to the Hummers technique of preparing GO. However, because all of the processing conditions use strong acid to handle graphite, acid residue remains a concern that must be addressed.
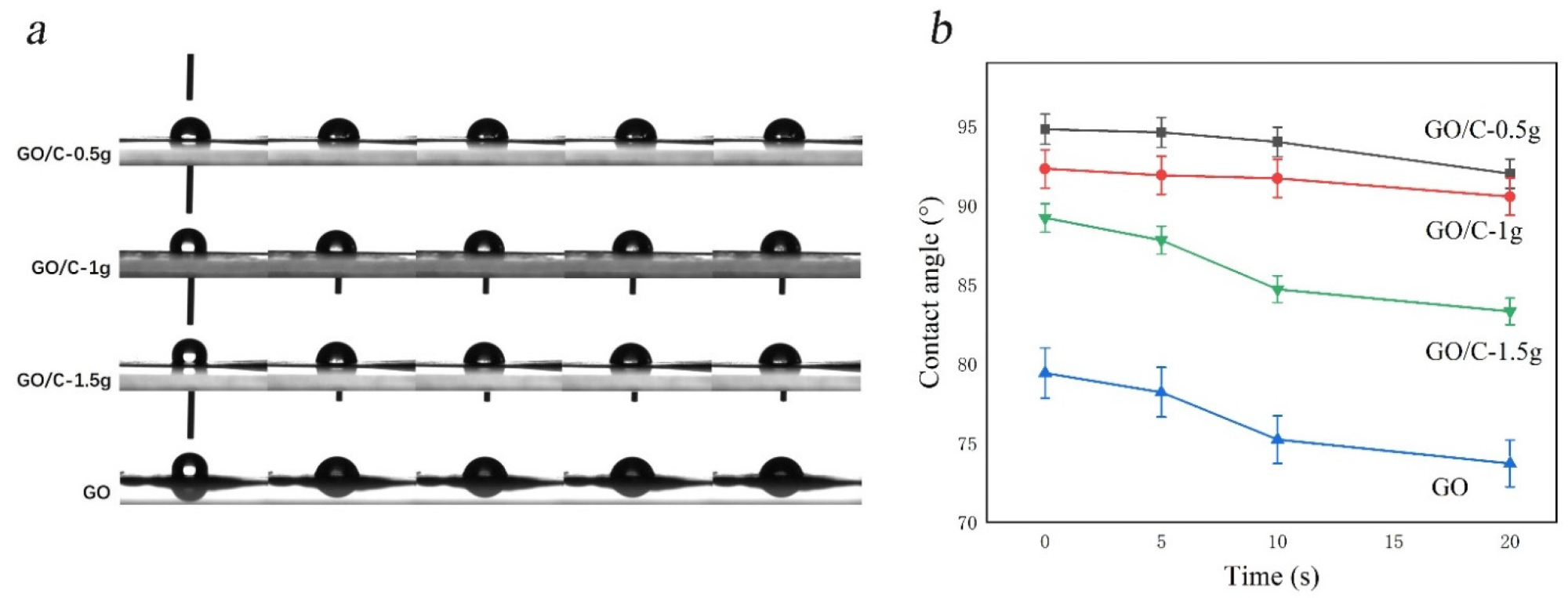
Alterations in water contact angles across all samples. (a) The contact angle test process of the samples (left to right: 1 s, 3 s, 5 s, 10 s, 20 s); (b) Contact angle image of hydrophobic of samples.3.5. SEM. © Miao, Y. et al., (2021)
Importance of Cellulose
Cellulose is a recyclable, biodegradable, and ecologically acceptable substance.
Cellulose nanofibers (CNFs) have a high aspect ratio (up to 1 m in length and 2–5 nm in thickness), a molecularly configurable outer layer, and elevated deformability due to their high crystallization. They are produced using relatively low-cost methods, all of which endow CNFs with huge potential for manufacturing a wide range of functional constructions.
Microcrystalline cellulose (MCC) is a depolymerized, refined type of cellulose.
Although development on GO/MCC composites has made considerable success, there are still several issues that need to be addressed. Organic cellulose, for instance, is difficult to mix with GO immediately. Still, the addition of cellulose solvents (e.g., urea-alkaline or ionic liquids) or modified cellulose can improve this.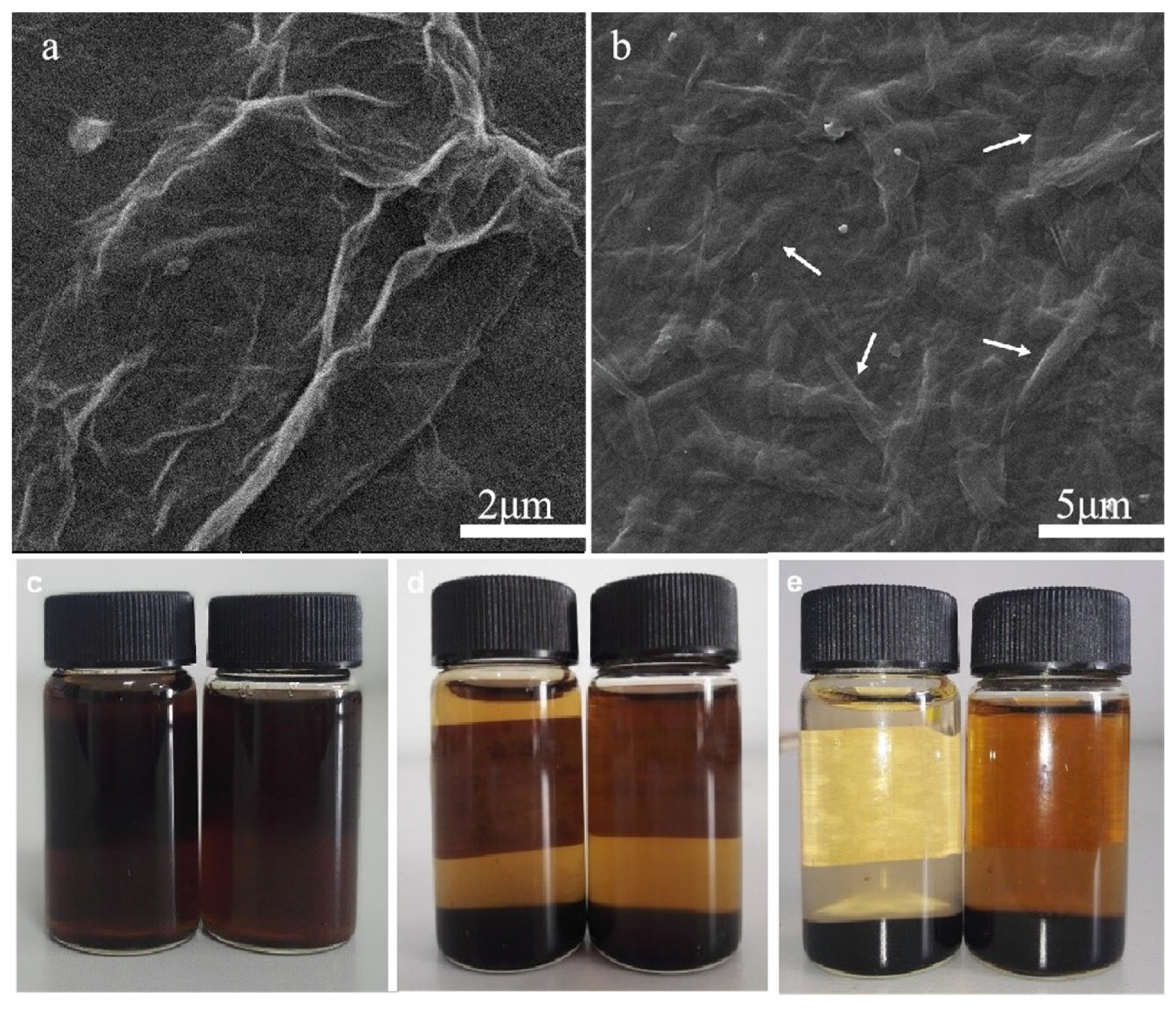
Microscopic and macroscopic morphologies of the samples during sample preparation. (a) SEM image of graphene oxide (GO); (b) SEM image of GO plus 1 g MCC composite (GO/C-1 g); (c–e) the photos of GO (left) freeze-dried powder and GO/C-1 g (right) freeze-dried powder dispersed in water on the 1st, 6th, and 78th days, respectively. © Miao, Y. et al., (2021)
Research Findings
Typical characteristic peaks of GO were seen from FTIR during the experiments, and the MCC's FTIR spectrum was compatible with the spectral properties of cellulose.
The XRD analysis showed that pure GO had a characteristically strong XRD peak at 2θ = 11.4◦. The layer spacing of GO was determined to be 0.77 nm, which is consistent with previous findings. The XRD pattern was identical to that of GO and MCC, with a prominent diffraction peak at 10.9.
The amount of MCC added has essentially little effect on the position of the composite's distinctive peaks. The strength of the composite's diffraction peak at roughly 2 = 11 dropped as the amount of MCC added increased, although the intensity of the cellulose's distinctive peak grew somewhat. This finding showed that as the amount of MCC supplied rose, so did the interactions between the acid-hydrolyzed cellulose and the GO sheet layer, breaking the order of the GO sheet and decreasing the strength of the distinctive peak.
In short, the solution of GO prepared by the Hummers method was involved in dissolving MCC, and GO/MCC composites after washing. It introduces a novel approach to the high-value manufacturing of GO composites. Simultaneously, this GO/MCC composite with outstanding thermal durability, wettability, and long-term preservation offers possible application utility in hydrophobic moieties.
Continue reading: The Applications of Crystalline Nanocellulose (CNC).
Reference
Miao, Y. et al., (2021) Preparation of Graphene Oxide/Cellulose Composites with Microcrystalline Cellulose Acid Hydrolysis Using the Waste Acids Generated by the Hummers Method of Graphene Oxide Synthesis. Polymers, 13(24). 4453. Available at: https://www.mdpi.com/2073-4360/13/24/4453
Disclaimer: The views expressed here are those of the author expressed in their private capacity and do not necessarily represent the views of AZoM.com Limited T/A AZoNetwork the owner and operator of this website. This disclaimer forms part of the Terms and conditions of use of this website.