Researchers added graphene to electrolytes to manufacture a micro-arc oxidation coating to improve the corrosion and wear resistance of a Titanium alloy as reported in the latest article published in the journal metals.
Study: Effects of Graphene on the Wear and Corrosion Resistance of Micro-Arc Oxidation Coating on a Titanium Alloy. Image Credit: RHJPhtotoandilustration/Shutterstock.com
Introduction to Titanium Alloys
Titanium alloy is relatively light, and its alloys are extremely resistant to most oxidizing, neutralizing, and hindered reduction circumstances.
It is also extremely durable. Because of its lightweight and high tensile stiffness, it is widely used in aircraft, mechanical, automobile, petrochemical, and other areas.
However, titanium alloys are not perfect and possess low wear tolerance and thermal conductivity. Surface treatment is commonly used to improve the characteristics of titanium alloys.
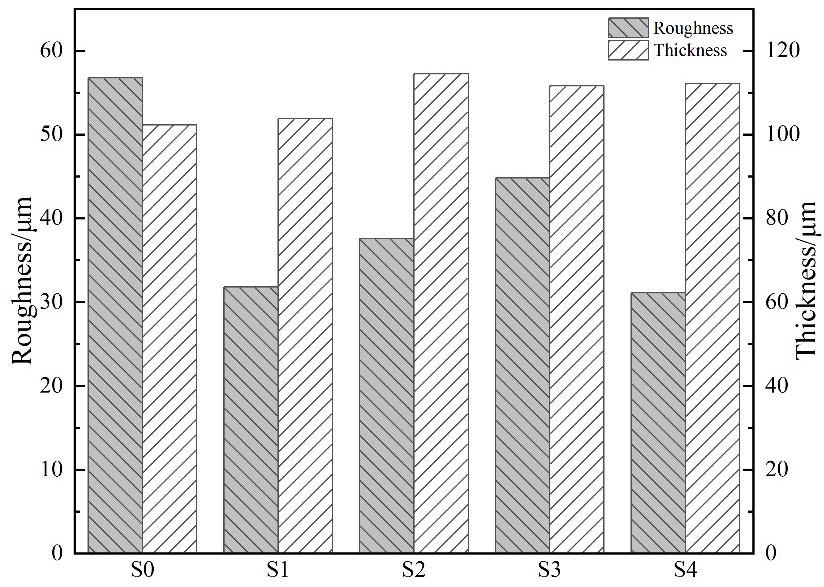
Thickness and roughness of MAO coatings. © Zhang, R. et al., (2022)
Micro-arc Oxidation
Micro-arc oxidation (MAO) is a technique for growing porcelain coatings precisely on Magnesium, Aluminum, and Titanium surfaces. MAO produces an oxide layer tightly bound to the metals and has excellent abrasion, erosion, and electromagnetic insulating qualities.
Electrolyte concentrations are critical in the MAO mechanism. The micro-arc melts the substrate's composition, which is then cemented by the electrolytes.
The conductance of the electrolytes and the content of the coatings are modified throughout this procedure, which affects the coating's effectiveness. As a result, ceramic coatings are created by incorporating particles (such as ZrO2 and graphene) into the electrolyte to increase the coatings' density, hardness, corrosion, and fatigue strength.
Importance of Graphene
To improve its toughness and structural qualities, graphene has been combined to form a composite.
Graphene is used in aviation, the nanostructures industry as well as in capacitors and ferroelectric technologies, while graphene oxide has also been used as an ingredient in airplane gasoline for better combustion and greater power generation.
Graphene has been demonstrated to be useful in the micro-arc oxidizing of other metals. It is, however, infrequently utilized as an addition in the micro-arc processing of titanium alloys, particularly Ti-5Al-1V-1Sn-1Zr-0.8Mo alloys.
In this investigation, graphene was introduced to the electrolyte and its effect on the coating's shape, resistance to abrasion, and corrosion resistance were explored.
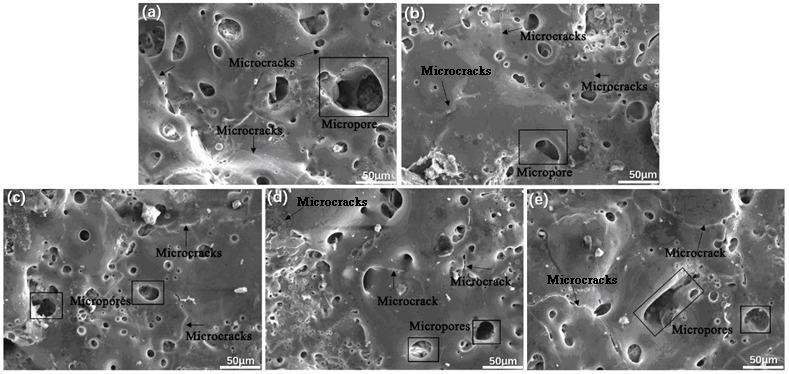
Surface morphology of MAO coatings (a) S0; (b) S1; (c) S2; (d) S3; (e) S4. © Zhang, R. et al., (2022)
Research Findings
With no graphene in the electrolytic solution, the roughness of the covering was 56.76 m (Ra), and the roughness greatly decreased with the introduction of graphene.
The roughness was minimal with 0.05 g/L graphene supplementation, with Ra at 31.81 µm. It was discovered that the density of the MAO layer grew as the graphite concentration grew, and the severity of the micro-arc response is mostly related to the smoothness of the MAO coating. The degree of MAO grew more moderate as the response intensity reduced and the roughness of the coating decreased.
The influence of graphene on surface ruggedness was also validated by a 3D morphological study. The interface of the films grew smoother with 0.05 g/L and 0.10 g/L graphene in the electrolytic solution, and the continuous scanning findings revealed that the altitude variation of the coatings was decreased.
Surface Morphology of the Alloys
The morphology revealed large-diameter micro-pores and fissures on the surface layer, which were formed without using graphene in the solution. The micro-cracks were produced by molten metal contraction following fast solidification. The conductance of the solution improved as a result of the inclusion of graphene.
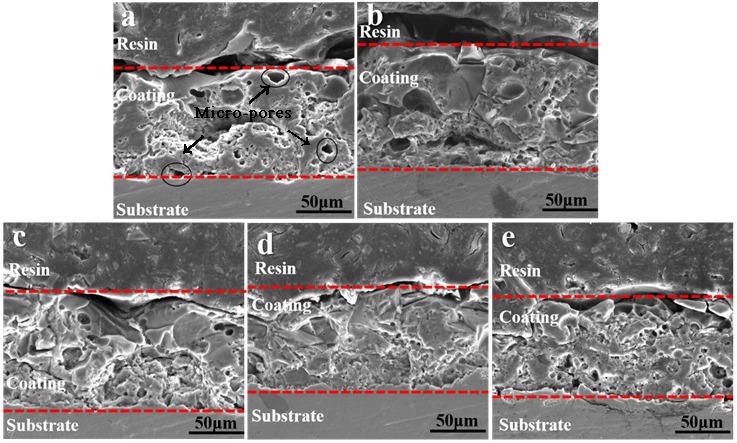
Cross-section morphology of MAO coatings (a) S0; (b) S1; (c) S2; (d) S3; (e) S4. © Zhang, R. et al., (2022)
Porosity Difference Study
The porosity of a coating created using a solution without graphene was 4.386 percent. With 0.10 g/L graphene in the electrolyte, the porosity of S2 was the lowest at 3.188 percent. The reduction in porosity led to the coating's improved resistance to corrosion. This homogeneity was achieved with the inclusion of graphene, which resulted in different diameters holes and fewer fractures throughout the MAO process.
Wear and Corrosion Resistance
The wear was greatest during the first 100 revolutions and subsequently declined throughout the 100th–250th rotations.
The contact pair was in touch with each other during the early stages of wear caused by the actions of loading. After 100 rotations of wear, the thin surface and high micro-convex structure had peeled off, and the contact surface between the frictional pairs had risen, resulting in steady mass loss.
The coating with 0.10 g/L graphene had the maximum wear resistance, and the mass loss after 250 rotations was just 15.8 mg. Furthermore, in saline spraying corrosive environment, the MAO coatings show high corrosion resistance. After 132 hours, significant black pitting corrosion formed on the surface of the coating, most notably on the arc discharge micro holes and the specimen's margins.
To conclude, the morphology and resistances of a graphene electrolyte-derived MAO coating were examined in this research, and the best-added quantity of graphene was determined to be 0.10 g/L.
Continue reading: Why AFM Is Critical To Graphene Research.
Reference
Zhang, R. et al., (2022) Effects of Graphene on the Wear and Corrosion Resistance of Micro-Arc Oxidation Coating on a Titanium Alloy. Metals, 12(1). 70. Available at: https://www.mdpi.com/2075-4701/12/1/70
Disclaimer: The views expressed here are those of the author expressed in their private capacity and do not necessarily represent the views of AZoM.com Limited T/A AZoNetwork the owner and operator of this website. This disclaimer forms part of the Terms and conditions of use of this website.