Researchers have studied the effects of tool shape and configuration variation on the quality of the exterior of monocrystalline nickel nanofabrication, publishing their research in the journal molecules.
Study: Influence of Tool Shape on Surface Quality of Monocrystalline Nickel Nanofabrication. Image Credit: Stock-Asso/Shutterstock.com
Advantages of Monocrystalline Nickel
Nickel's conductance and magnetization allow it to discharge electromagnetic impulses in aeronautical components.
Because the nickel nanowires are monocrystalline, they grow indefinitely from a nucleus until the nickel antecedent is exhausted.
Monocrystalline nickel is particularly appealing for this purpose because electromagnetic filtration may be performed without considerably adding the weight of the composite.
One of the substances widely utilized in aerospace engines is monocrystalline nickel and its alloys. Conducting processes at the nanoscale is a crucial aspect of its fabrication due to high-quality standards.
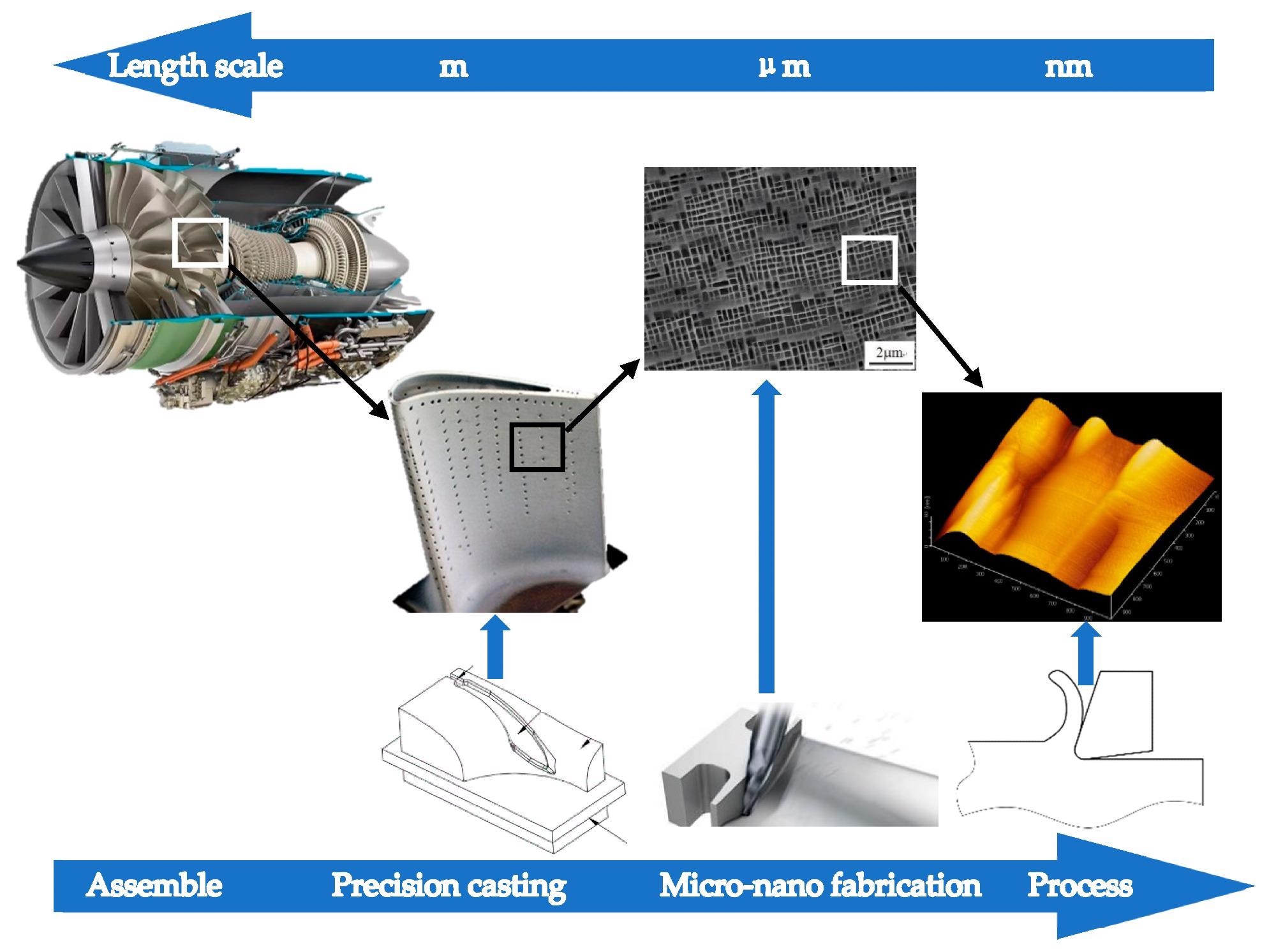
Figure 1. Ultra-precision parts of aero-engines. In the previous study of monocrystalline nickel grinding, it was found that the size of the abrasive grains had a significant influence of surface quality of monocrystalline nickel. The effect of abrasive particle diameter is essentially the reaction of an effective rake angle during processing. Thus, it can be concluded that the size and shape of the machining tool will affect the workpiece even when the size range is small to the nanometer level. Therefore, this study discusses the nanofabrication of tools with different rake angles, different clearance angles, and different tool edge radii, and their impact on the processing mechanism of monocrystalline nickel. © Ren J, Yue H, Liang G, Lv M. (2022)
What is Nanofabrication Technology?
The framework and construction of systems with proportions during fabrication in nanometre scale is known as nanofabrication.
Nanofabrication employs cutting-edge technologies and is mostly employed in the production of high-tech microelectronics, embedded systems, as well as other forms of intrinsic semiconductors.
Nanofabrication technologies are critical in generating innovative nanostructures, electronics, and compounds with distinctive features as a gateway bridging basic knowledge and clinical use of nanotechnology.
Nanoscale biomedical frameworks are employed for tailored medicine administration, quick diagnostics, high-throughput genetic analysis, and the next generations of vaccinations. There are two techniques for developing functional nanostructures: top-down and bottom-up.
Factors Affecting Nanofabrication of Monocrystalline Nickel
The present nanofabrication technologies are primarily concerned with investigating various treatment rates, treatment layers, and crystalline orientations.
The impact of the tilt angle, clearance angle, and blade curvature on the machining operation and processing performance is considerably enhanced due to the decrease of manufacturing tolerance and the enhancement of manufacturing precision.
Studying the effect of tool shape on monocrystalline nickel nanofabrication will aid in the advancement of manufacturing techniques.
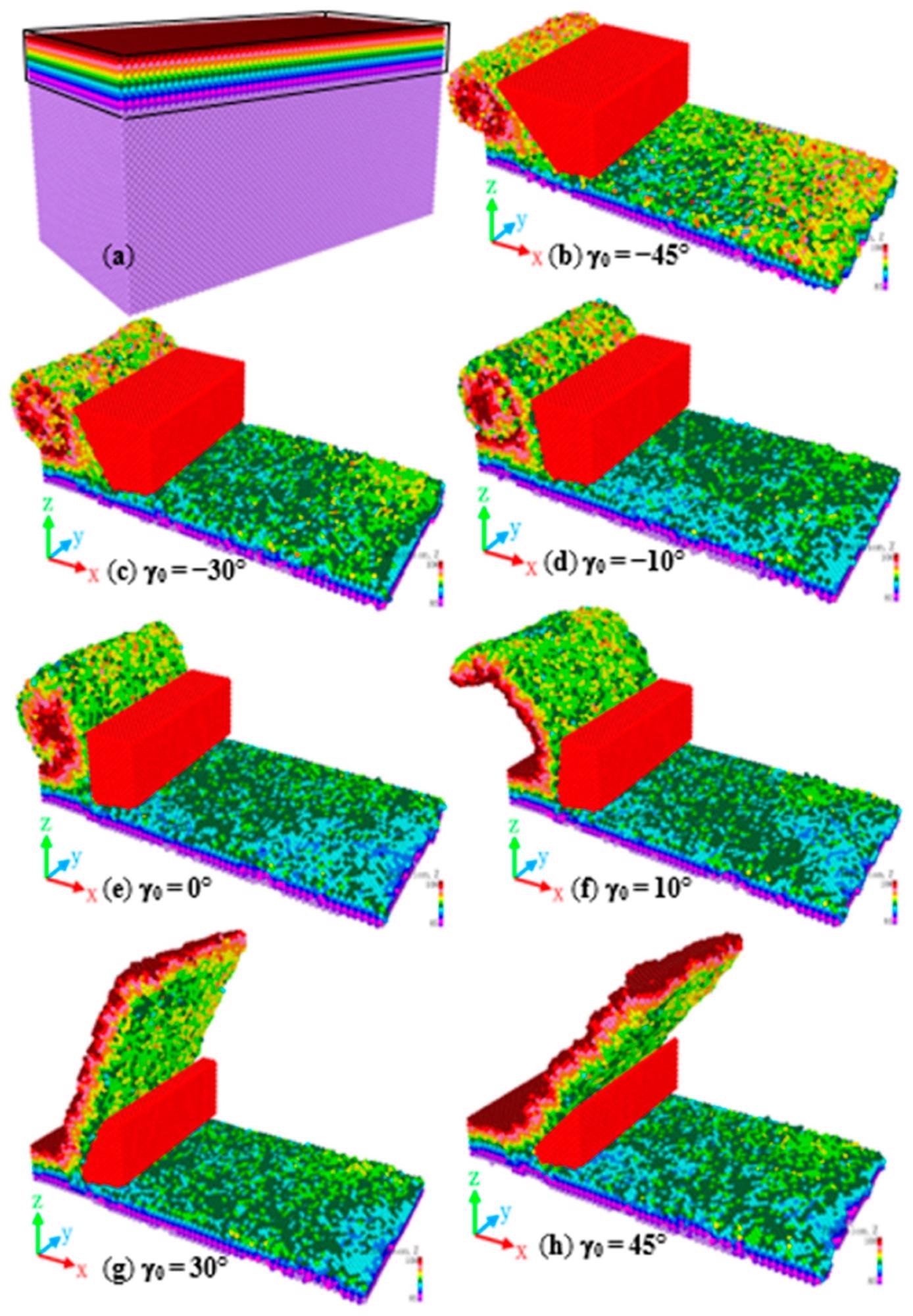
Figure 2. Chip morphology of monocrystalline nickel processed by different tool rake angles. © Ren J, Yue H, Liang G, Lv M. (2022)
Importance of Molecular Dynamics
Owing to the limits of nanofabrication in experiments conducted, molecular dynamics is a practical and dependable approach for researching extremely high precision machining processing and nanofabrication.
Several researchers have investigated the use of molecular dynamics in nanostructures.
The effect of substrate particle sizes on the nano-cutting process was investigated, and it was discovered that while slicing polycrystalline aluminum, the thrust force rises and the friction factor reduces as particle size grows.
The temperature was shown to be related to the number of hole imperfections in the composite machining operation by doing a molecular modeling simulation on thermally vibration-assisted nanocomposite manufacturing.
Simulation Model Intricacies and Importance
The molecular dynamics simulation framework can aid researchers in obtaining more efficiently visualizing kinetic findings and analysing data, as well as being cost-effective.
Different qualities are created for the atoms in the workpiece to be as similar to the real manufacturing circumstances as possible.
To stabilize the workpiece, bounding molecules with a velocity of 0 are put up during manufacturing.
To mimic thermal transfer, the thermostatic particles are maintained at 293 K. The workpiece is made of made monocrystalline nickel, according to the lattice constant, and the size is fixed to 21.2 × 10.6 × 10.6 nm owing to appropriate boundary conditions.
Influence of Rake Angle on Chip Morphology
It was found that when the tool's rake angle is positive, the shards are strip-shaped, and the treated particles are predominantly green.
This is because the tool is relatively 'sharp' at this moment, therefore the tool's funneling threshold is minimal, and the majority of the particles in interaction with the tools produce shards rather than being crushed under the edge after being shunt.
The chips build up when the tool has a negative rake angle, and the produced chips migrate to the surface of the workpiece because of the protrusion of the rake face of the tool.
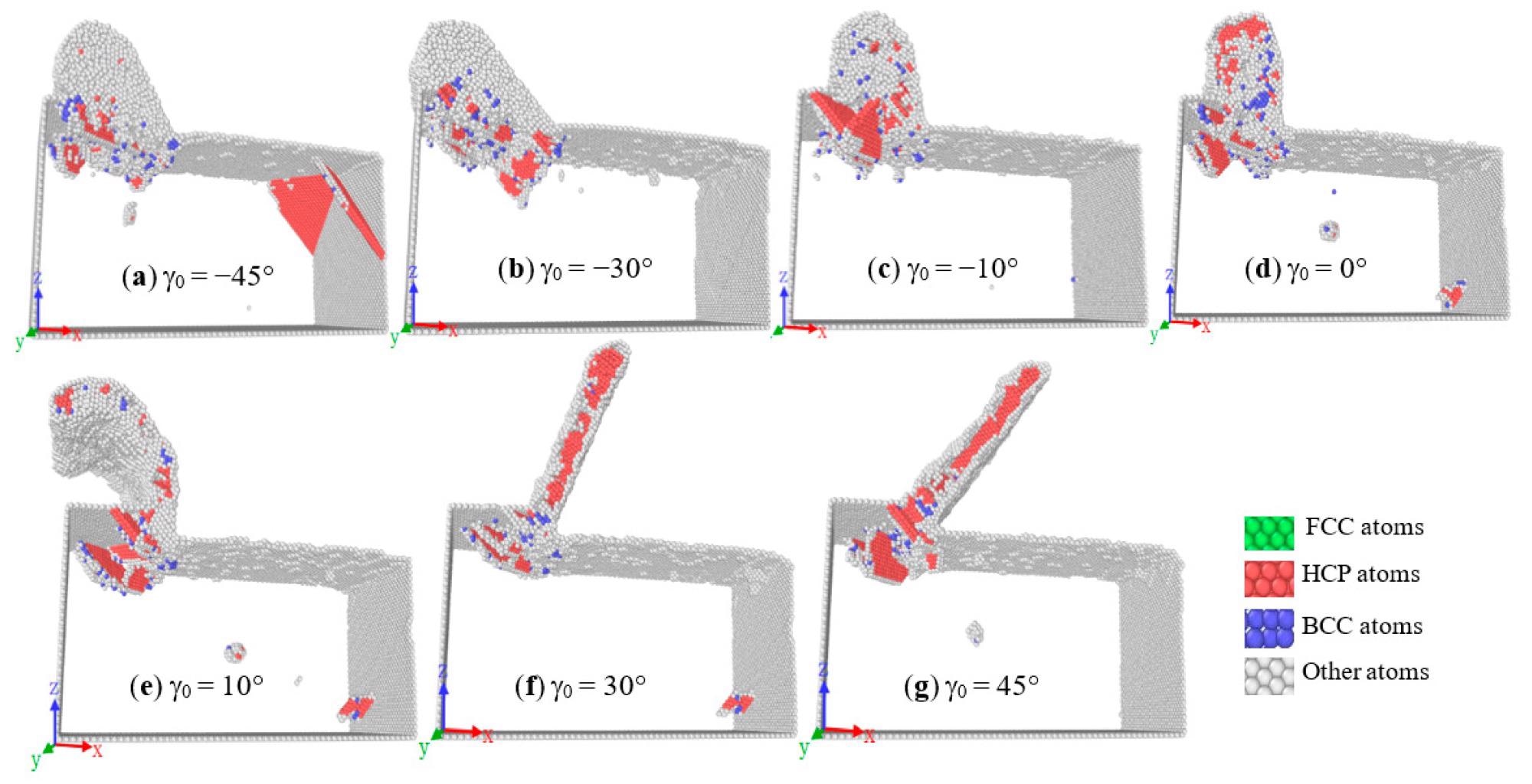
Figure 3. CAN analysis. © Ren J, Yue H, Liang G, Lv M. (2022)
Influence of Tool Shape on Cutting Force and Temperature
When the tool's blade diameter and clearance angle are fixed, the shear force falls as the blade raking angle increases. The bigger the raking angle, the stronger the ripping impact on workplace particles; the lower the rake angle, the higher the compressing impact on workpiece atoms.
Temperature differences act in the same way as thrust force.
The heat of the workpiece increases as the tool raking incidence lowers. The temperature curve is essentially the same when the tool clearance angle is 10, 20, or 30 degrees.
In short, the experiments thoroughly explored the tool shape influence on the nanofabrication process.
Cutting power and temperatures are thought to be more responsive to fluctuations in tool raking inclination, whereas tool geometry diameter has minimal influence on both.
Continue reading: Nanofabrication: Techniques and Industrial Applications
Reference
Ren J, Yue H, Liang G, Lv M. (2022) Influence of Tool Shape on Surface Quality of Monocrystalline Nickel Nanofabrication. Molecules. 27(3). 603. Available at: https://www.mdpi.com/1420-3049/27/3/603
Disclaimer: The views expressed here are those of the author expressed in their private capacity and do not necessarily represent the views of AZoM.com Limited T/A AZoNetwork the owner and operator of this website. This disclaimer forms part of the Terms and conditions of use of this website.