An article published in the journal Functional Composites and Structures introduces a method for improving the mechanical characteristics of different welded components with advantages such as a strong bond, high speed and affordability.
Study: Study of the effect of nano ZrO2 and TiO2 and rotation speed on friction behavior of rotary friction welding of HIPS and PP. Image Credit: Factory_Easy/Shutterstock.com
Rotatory Friction Welding
Rotatory friction welding (RFW) is a strong connecting procedure for plastics, also known as spin welding.
Two chucks hold the components during the welding process, one rotating and the other fixed. The desired heat is generated by the friction of connecting the components.
The chuck, as well as the rotating and heating stages, is continuously driven by the driving motor.
The driving motor is turned off and friction welding force binds the two materials together. While the spinning speed drops, it is possible for the deposited kinetic energy in the flywheel to be released at the weld surface as heat energy.
In engineering design, connecting different materials is quite important and has a wide range of applications.
Using the Friction Stir Welding (FSW) technique to connect various components has revolutionized engineering applications.
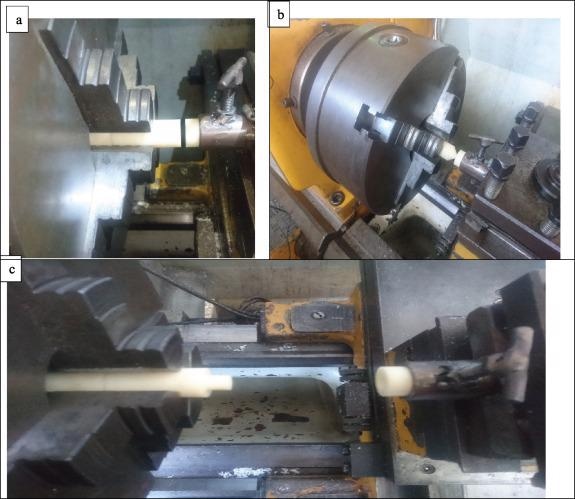
Figure 1. (a)Flat surface. (b)Cone surface. (c)Step surface are respectively the steps of the welding process for 3 different welding area. © Afzali, M., & Asghari, V. (2022).
Suitable Materials for Joining Workpieces
High impact polystyrene (HIPS) is a strong and hard component that proves useful in a variety of applications.
It can be used to combine materials via a thermoforming procedure. Polypropylene (PP) is broadly applied in industrial and engineering applications owing to its great chemical and mechanical properties.
FSW is a great alternative for joining two workpieces and producing a great number of materials to expand and improve the mechanical properties of plastic joining.
Welding of plastic-based components was performed with desirable results by using particle reinforcement methods with the original component.
Before welding different polymer materials, the capacity to intermix plastic-based components was thoroughly examined.
In most cases, different polymers are not thermodynamically blended homogeneously. To enhance the impacts of polyethylene FSW on the morphological features of welds, a unique milling configuration was used.
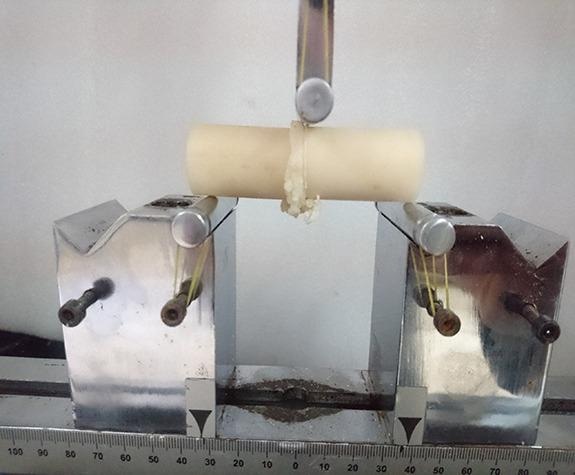
Figure 2. Bending test of joined HIPS and PP. © Afzali, M., & Asghari, V. (2022).
This research discusses the impact of mechanical properties on FSW high-density polyethylene (HDPE) and low-density polyethylene (LDPE) with iron metal powder reinforcement.
According to recent research, reinforcement of metal particles can be used to produce rheological characteristics of polymeric components such as melt flow index and glass transition temperature.
The mechanical properties of polyethylene sheets, comprising HDPE and HIPS, were evaluated after they were welded with FSW, as a result of which a unique approach for producing nanocomposite polymers was introduced.
PS-welded polymer components were studied for strengths and weaknesses. In the FSW procedure, the tool and shoulder profile is of great importance.
Prior to the welding process, one of the components was joined to the drive flywheel of a provided weight and the rotatory chuck simultaneously.
To store the required energy in the flywheel, the second piece was then rotated significantly.
The motor was powered on after the rotating components reached their usual speed, and the pieces were forced together under pressure.
Researchers have been drawn to nano TiO2 because of its unique traits, such as great mechanical characteristics that improve the structure. Nano TiO2's impact on cementation components has also been extensively researched.
Important Findings of the Study
The speed of rotation is an important element in the process of welding as it advances with rising temperature and provokes the melting procedure, which is essential for welding.
At an approximate speed of 2400 rotations per minute (RPM), the greatest speed of rotations used in this work, improved results were obtained even in environments lacking controlled nanoparticles.
In addition to this, a factor that influenced welding performance was the surface, which indicated a rise in the contact's cross-sectional area, thus expanding the area of welding, and, ultimately, the step surface demonstrated the greatest combining power.
As a result of joining two distinct directions and the floor and rotating surface, better welding performance was obtained.
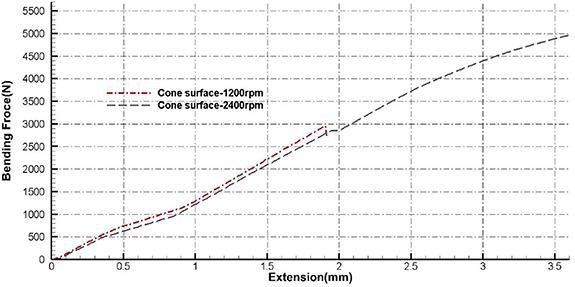
Figure 3. Results of cone surface joined by HIPS-PP bending without nanoparticles. © Afzali, M., & Asghari, V. (2022).
The step surface was examined next, and the greatest joining characteristic was determined.
Comparing the step surface and cone surface it was observed that the combined power in the step surface-enhanced due to the higher friction rate.
The results showed that samples using nanoparticles varied significantly from those without nanoparticles.
Due to their intrinsic features, ZrO2 nanoparticles demonstrated improved mechanical characteristics than nano TiO2 in samples containing nanoparticles. A step shape surface and nano ZrO2 were also found to improve mechanical characteristics.
Reference
Afzali, M., & Asghari, V. (2022). Study of the effect of nano ZrO2 and TiO2 and rotation speed on friction behavior of rotary friction welding of HIPS and PP. Functional Composites and Structure, 4. Available at: https://iopscience.iop.org/article/10.1088/2631-6331/ac407d
Disclaimer: The views expressed here are those of the author expressed in their private capacity and do not necessarily represent the views of AZoM.com Limited T/A AZoNetwork the owner and operator of this website. This disclaimer forms part of the Terms and conditions of use of this website.