Researchers have published an article in the MDPI journal sensors exploring the developmental process of liquid metal (LM) based nanocomposites as well as their applications in printable stretchable electronics.
Study: Liquid Metal Based Nano-Composites for Printable Stretchable Electronics. Image Credit: Shawn Hempel/Shutterstock.com
What are Stretchable Electronic Gadgets?
Researchers across the world are becoming more interested in stretchable electronic devices because they have the capacity to be used in a variety of new disciplines such as epidermis integrated electronic devices, bioengineering, medical applications, and softer robotics automation. Flexible circuits are devices made up of electronics materials and/or circuitry that are incorporated onto flexible platforms.
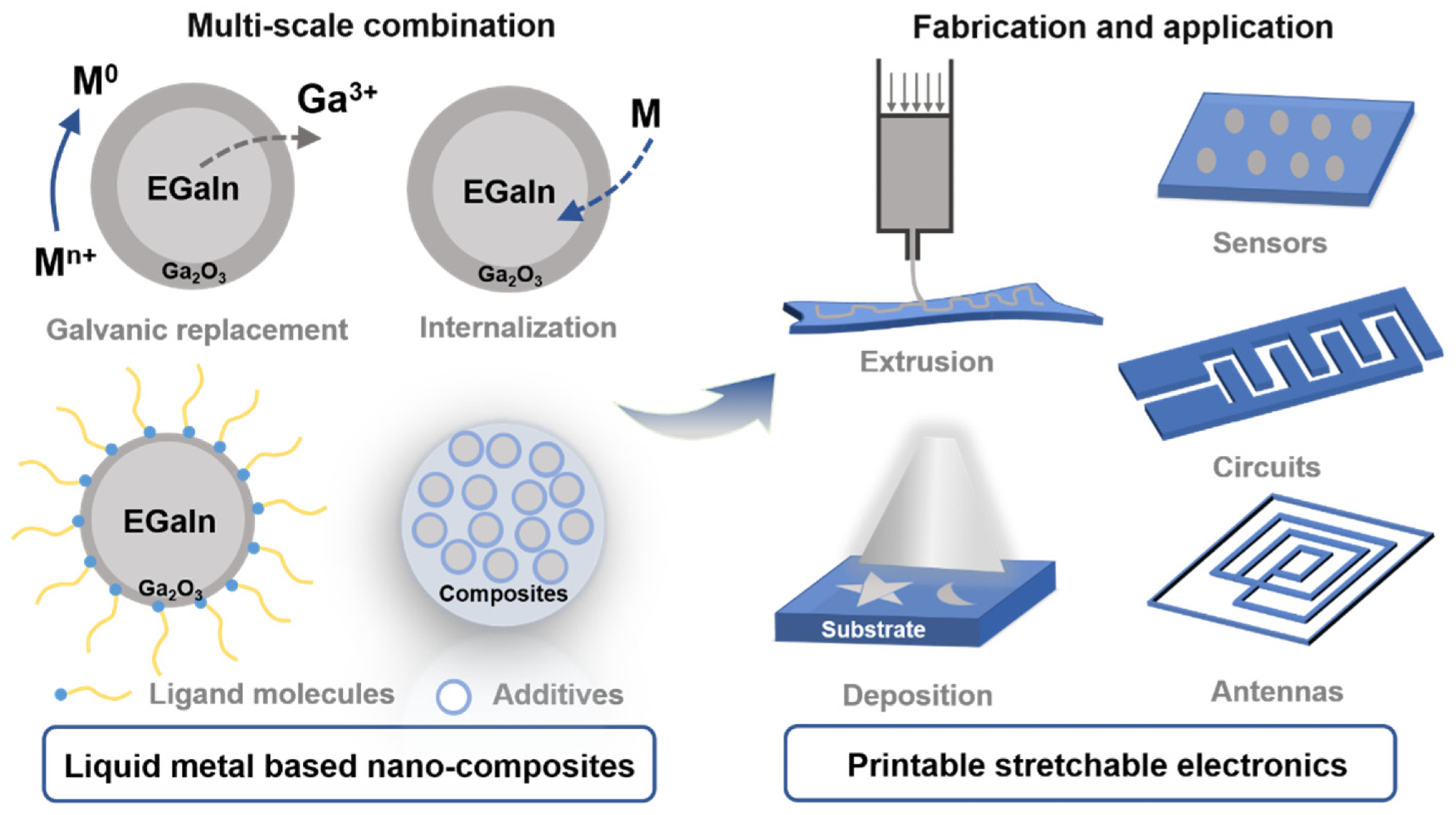
Figure 1. Schematic illustration of liquid metal-based nano-composites and the application of printable stretchable electronics. © Xu D. et. al. (2022)
Importance of Liquid Metals
Liquid metal (LM), a popular electrical conducting material, has superior elastic properties and robustness and has the ability to eliminate Young's modulus discrepancy between rigid and flexible connections. Owing to its superior electrical conductivity value and optimal thermal conductivity when compared to its counterparts, LM is commonly used in stretchy electronics.
Mechanical deformation, oxidation state, electromotive force, piezoelectric interference, magnetic force, and even light all act as external stimuli causing a characteristic reaction in LM materials. LM has effectively developed numerous application potential as a consequence of creative design ideas and recent advancements, such as wearable sensors, conductors, transducers, optoelectronics, and power storage platforms.
Limitations of Liquid Metal Materials
Directly processing or patterning LM compounds is still a difficulty. For example, owing to its high vapor pressure, LM is often retained as drops or particles, resulting in poor contact compliance between the LM and substrate material surface. Mainly, because of the low substrate adaptation of LM materials, there is a clear discrepancy between the real engineering sequence and a reduction in printing speed, which may harm the printed items.
Many procedures, including pre-treatment and pre-patterning on the base material, have been suggested to enhance area-specific wettability during printing. However, due to the unpleasant method, selective printing is difficult to extrapolate in large-scale manufacturing. Furthermore, the significant interfacial tension and oxidation of gallium in the air pose significant obstacles to high-resolution LM printing.
Properties of LM-Based Nanocomposites
LM alloys in continuum phases like Galinstan are embedded as nanometer particles in material systems referred to as LM-based nanocomposites. The applicability of LM nanocomposites has been greatly broadened as a result of the size impact of micro/nano components and the novel function supplied by additives.
The characteristics of LM-based nanocomposites are adequate to fulfill the needs of printed flexible semiconductor electronics. More precisely, the most typical composite, which is made up of LM and its inherent oxidation surface, allows for LM viscoelastic modulation, which improves interfacial and intermetallic wettability.
LM-based flexible electronic platforms outperform rigid substances under strain in terms of electrical permeability and durability, as well as low specific hysteresis and infiltration network deterioration.
Fabrication Methods of LM-Based Nanocomposites
There are several approaches for creating LM-based micro to nanoparticles sized composites at the moment. The most popular approach for particulate nanolization is ultrasonic processing, which may decrease bulk LM to nano-sized particulates by producing high mechanical power vibrations that can concurrently in situ optimize the size of the interface with ligand, polymers, or natural or synthetic materials.
A turbulent blending technique was also devised to create the nano/micro-sized LM particulates for easy surface modification and sustainable manufacturing. The supplementary oxide shell is generated constantly in this procedure, preventing LM coalescence, and is extremely effective for introducing fundamentally inorganic compounds.
LM-based Nanocomposite Printing Mechanism
Many problems exist in designing LM-based printable electronics that vary from standard rigid electronics with the aim of soft and flexible features in electronics. Until now, two major methodologies for structuring LM-based nanocomposites have been established including the mechanical extrusion of stabilized LM composites (injector distribution, and inkjet printing) and layering of the LM materials on a platform with a regular sequence.
Because of advancements in composite materials and printing methods, distinctive printing characteristics (line widths, sharpness) founded on LM materials are continually exposing novel indicators.
In brief, liquid metals (especially gallium and its compounds) feature mobility, permeability, stimulus responsiveness, and high reactivity. The spontaneously formed oxide layer on LM confers distinct textural features and enhances its processability making it viable for digital electronics. However, to increase the homogeneity of LM-based hybrid substance, novel material technologies and distribution methods must be developed along with obtaining the perfect balance between system stability and endurance.
Reference
Xu D. et. al. (2022). Liquid Metal Based Nano-Composites for Printable Stretchable Electronics. Sensors. 22(7).2516. Available at: https://www.mdpi.com/1424-8220/22/7/2516
Disclaimer: The views expressed here are those of the author expressed in their private capacity and do not necessarily represent the views of AZoM.com Limited T/A AZoNetwork the owner and operator of this website. This disclaimer forms part of the Terms and conditions of use of this website.