A novel approach for laser-driven bubble printing using Gold (Au) and Silver (Ag) to build strong nanostructures is presented in a study published in The Journal of Physical Chemistry.
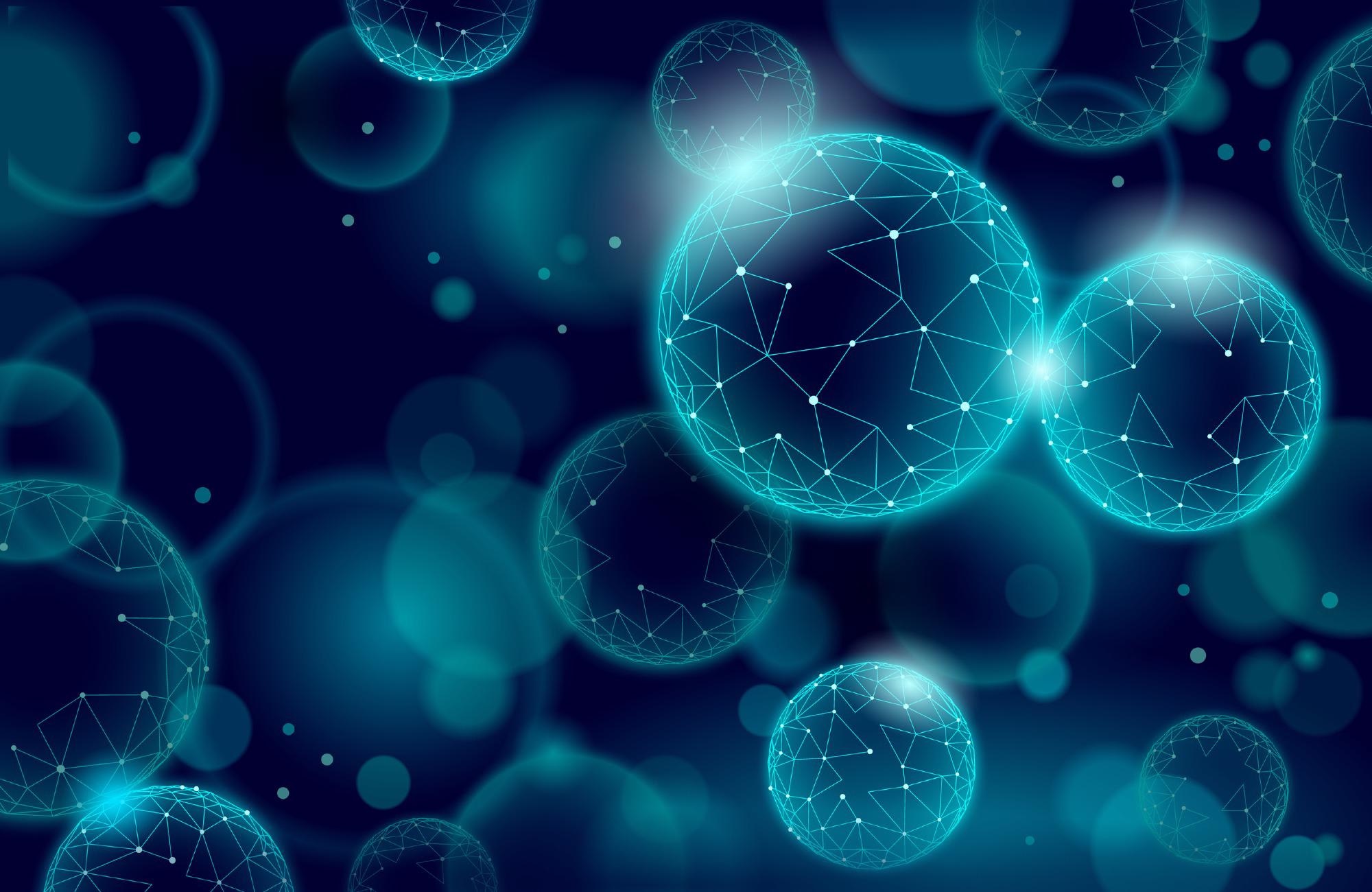
Study: Laser-Driven Bubble Printing of Plasmonic Nanoparticle Assemblies onto Nonplasmonic Substrates. Image Credit: LuckyStep/Shutterstock.com
Are Lasers the Future?
Optically (laser) driven microbubbles (MB) offer a diverse environment for particle generation and structuring at the interface. This lays the groundwork for future research into the assembly of nanoparticles and the accumulation of optically driven MBs at the interface surface of a substance.
In laser-driven methods, the laser heat generates an MB at the surface between the substrate and colloidal suspension, owing to the solvent’s vaporization.
Convective flow created by the temperature differential draws colloidal particles towards the MB through intense Marangoni convection at the surface of the bubble, whereupon contacts of van der Waals cause the colloidal particles to be chained to the MB.
For various metals, particularly quantum dots, conducting polymers, and even constantly alternating conductor/insulator multilayers, laser-driven "bubble printing" techniques for guided production and accumulations of nanoparticles on various surfaces have been created.
Figure S1. (a) Schematic of the breakage of the upper portions of NP assembly at the bubble interface induced by bubble breakage/movement/rupture. (b) Optical microscope image of printed AuNS patterns on glass directly after printing; floating broken-off pieces formerly at the top of the bubble are circled in yellow. (c) An SEM micrograph of one of the broken off pieces showing a sheet of AuNS. (d) SEM micrographs showing AuNS printed ring-like patterns with broken-off hemispherical fragments still partially attached.
Where the Concept Falls Short
Despite the many utilities where anisotropic particle alignment may play a key role, awareness concerning the assembly of nanoparticles using bubble printing technologies has still not been obtained.
Spectroscopy techniques, such as surface-enhanced Raman scattering spectroscopy (SERS) sensing using plasmonic metal particles, may be greatly enhanced when particles are packed into tight structures, yet research in this domain is limited.
Previous attempts to bubble print plasmonic metals required printing a Silver (Ag)-precursor ink onto a substrate for heating, in turn producing in silver nanostructures.
To test these nanoparticles, diethylene-glycol-butyl ether was used. In this ether, silver nanoparticles were directly printed to produce conductive lines; yet, the assembly of the resulting nanoparticles was not clearly observed, possibly due to local melting and fusing of nearby nanoparticles.
While opto-thermophoretic entrapment has been used to control the assembly of Gold (Au)-based nanoparticles, bubble printing on non-plasmonic surfaces has yet to be shown.
The Promise of Bubble Printing Using Lasers
To comprehend the limits of this technology for guiding the self-assembly of metallic nanoparticles, bubble printing of Au and Ag nanoparticles of various designs was implemented in this study. Plasmonic nanoparticles were bubble-printed on Indium tin oxide (ITO) and glass substrates, and the parameters of the experiment such as beam chopping rate and laser fluence were tested.
Various nanoparticle geometries were utilized to compare the impact of particle morphology on assembly packing and order, as well as the consequent SERS efficiency.
The motion of an optically driven microbubble in an aqueous environment of plasmonic particles enabled the straightforward printing of quasi-ordered nanoparticle ensembles, allowing for the rapid production of SERS sensing devices with substantial freedom in particle and substrate selection.
Overall, bubble printing has the potential as a quick and easy approach for directing the assembly of functional particles on random surfaces.
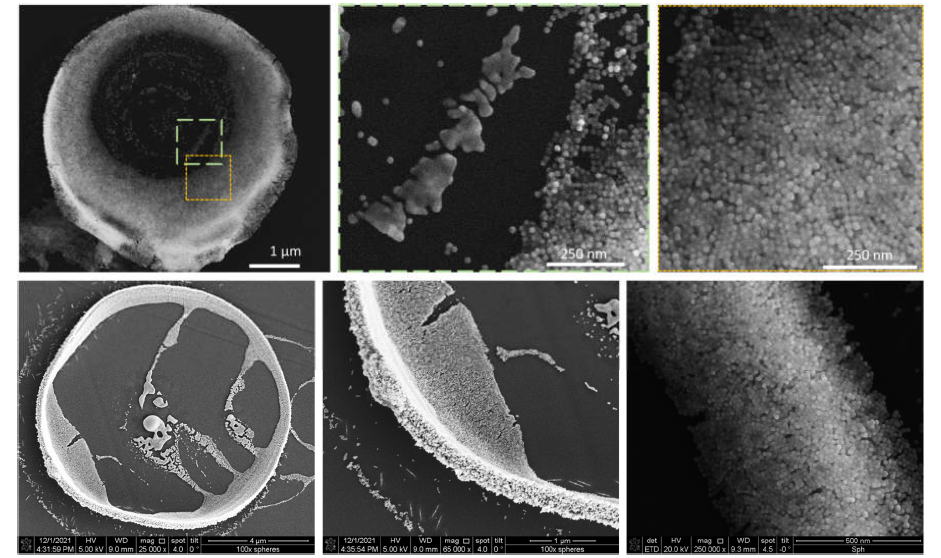
Figure S2. SEM micrographs of bubble-printed ring-shaped AuNS assemblies.
Key Findings of the Study
In this study, glass, and Indium Tin Oxide (ITO)-coated glass were utilized. It was pointed out that this technology can be utilized for printing on an array of substances owing to the improved plasmon heating of dispersion particles for bubble generation, as compared to the utilization of a plasmonic absorption layer.
The team performed SERS and noted that the melted portions showed a decrease in SERS efficiency when contrasted to the nonmelted sections, which exhibited normal SERS function. Moreover, it was deduced that the specimens' robustness makes this method suitable for printing different kinds of nanoparticles consecutively.
The study showcased that the printed ensembles are very durable and that this method might similarly be applied on flexible substrates, allowing it to be utilized for the automation of desired sequence and area printing using a computer-controlled setup.
The team concluded that additional research into bubble printing technologies for controlled hierarchical nanoparticle assembly is a worthy undertaking, at the same time highlighting that interface chemistry and interface topography play an important part in the process due to variations in wetness, a phenomenon which should be investigated further.
It was also concluded that since the ensembles in this study were not completely organized, this work creates the avenues for additional research into how nanoparticle formation can be regulated more efficiently at the bubble-liquid interface under nonequilibrium settings with rapid kinetics.
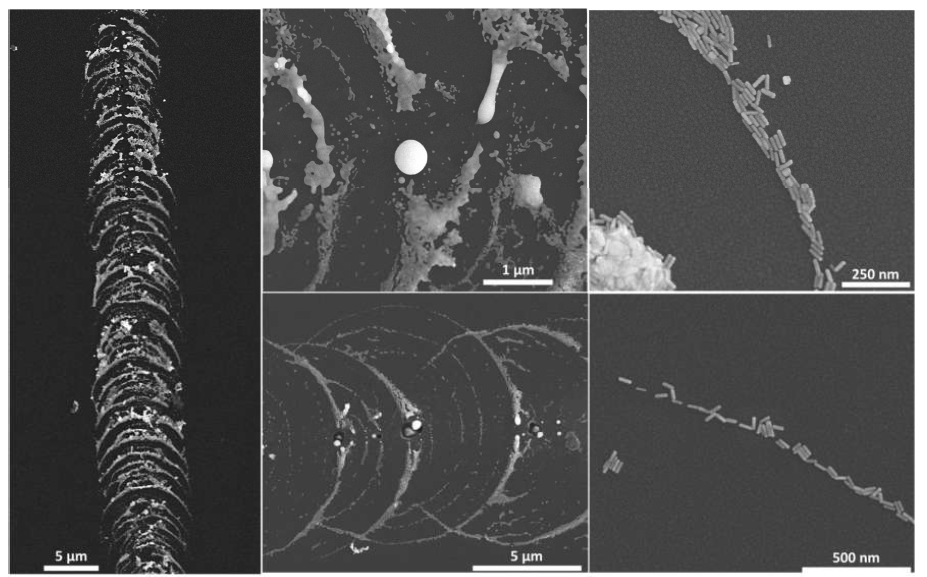
Figure S3. SEM micrographs of bubble-printed lines of AuNR assemblies.
Disclaimer: The views expressed here are those of the author expressed in their private capacity and do not necessarily represent the views of AZoM.com Limited T/A AZoNetwork the owner and operator of this website. This disclaimer forms part of the Terms and conditions of use of this website.
Source:
Hill, E., Goldmann, C., Hamon, C., & Herber, M. (2022). Laser-Driven Bubble Printing of Plasmonic Nanoparticle Assemblies onto Nonplasmonic Substrates. The Journal of Physical Chemistry. Available at: https://pubs.acs.org/doi/10.1021/acs.jpcc.2c02414