A paper published in the journal Ceramics International reported the development of an organic-inorganic covering of polydimethylsiloxane (PDMS) combined with zirconia (ZrO2) nanoparticles for improving the corrosion resistance of magnesium (Mg) alloys.
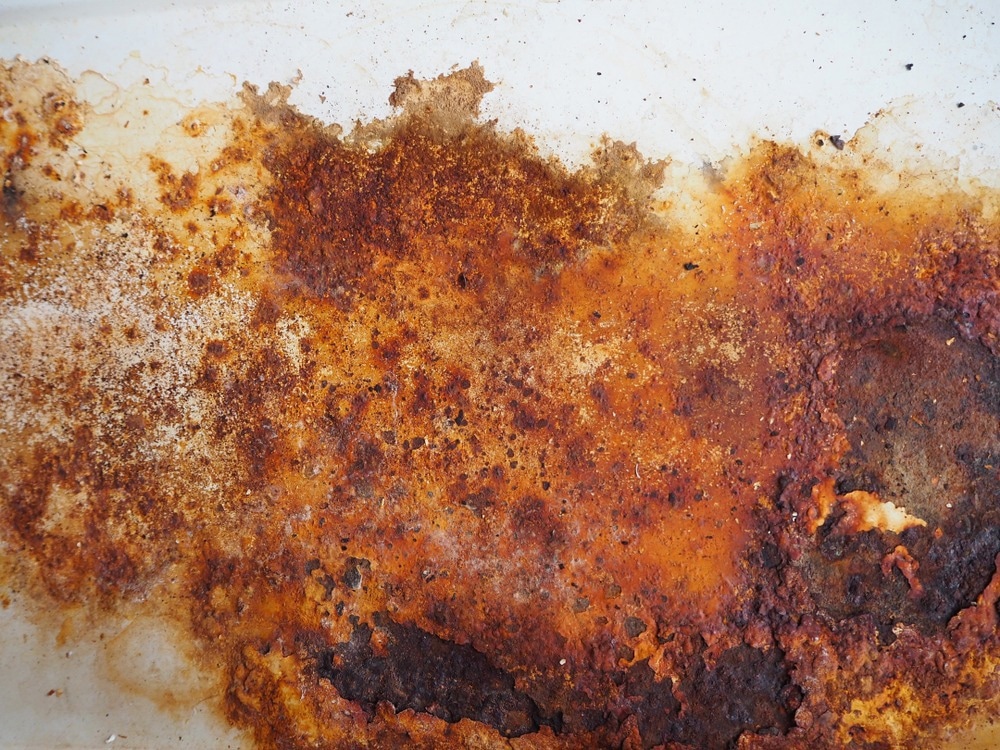
Study: Hybrid coating of polydimethylsiloxane with nano-ZrO2 on magnesium alloy for superior corrosion resistance. Image Credit: olympuscat/Shutterstock.com
The hybridized matrix membrane developed in the study presents a unique design strategy for highly hydrophobic coatings showing great long-term corrosion resistance.
Addressing the Corrosion Problem of Magnesium Alloy
Thanks to their low weight, high specific strength, and recyclability, magnesium (Mg) alloys are employed across many industries, including the automotive and aeronautical sectors and electronic equipment.
Despite this, magnesium alloys can easily suffer from corrosion in aqueous conditions because of their strong chemical activity, restricting their widespread applicability.
Multifarious techniques, including electrodeposition, ionic implants, and surface coatings, have been used to improve the corrosion resistance of magnesium alloys.
Surface coatings, particularly organic surface coatings, offer great corrosion resistance with the advantages of being facile and inexpensive.
PDMS Coatings for Better Corrosion Resistance
Compared to traditional organic coatings, PDMS is a unique polymeric material having low surface energy, high chain flexibility, superior thermal oxidation resistance, and chemical corrosion resistance thanks to the robust silicon-oxygen-silicon backbones.
PDMS is extensively used in flexible electronic devices and microfluidics. Moreover, due to its strong water-repellent nature, PDMS is a preferred material for corrosion resistant coatings.
While PDMS polymer coatings exhibit strong corrosion resistance and barrier function, their protective powers become weaker when they absorb water after extended contact with a corrosive medium.
Meanwhile, doping or hybridization can lead to the formation of microcracks and microspores in organic coatings, which ultimately causes poor corrosion resistance durability.
Enhancing Corrosion Resistance with Oxide-based Polymer Coatings
Hybridized coatings consisting of metal oxides and polymers have recently surfaced. These innovative materials incorporate metallic oxide microparticles or nanoparticles into the polymeric framework.
These hybridized coatings combine the advantages of polymer-based behavior of the polymeric framework as a physical barrier and outstanding mechanical capabilities of the metal oxides functioning as crosslinking agents.
Coatings based on non-toxic metal oxides like Al2O3, ZnO, and ZrO2 have shown great promise in terms of their corrosion resistance.
The outstanding thermal, chemical, and mechanical stability of ZrO2 nanoparticles make them a highly promising reinforcement material for coatings with corrosion resistance.
Hetero particles in the polymeric frameworks may contribute to corrosion resistance by reacting with the functional groups in the organic coating. In turn, cross-linkages among the molecular chains are strengthened, restricting the diffusion routes of corrosive fluids.
Hydrophobic polymeric films incorporated with water-resistant inorganic particles to generate interconnected polymeric materials can offer good protection against corrosion.
What Did the Researchers Do?
In this work, the team developed a PDMS-ZrO2 hybridized matrix membrane using a magnesium alloy as the platform.
By reducing the swelling of polymeric framework and the limitations of leaking or obstructing interfaces, the ZrO2-modified bridging networks of PDMS polymeric matrix managed to significantly enhance the long-term corrosion resistance and thermal stability of the coating.
The superhydrophobic PDMS-ZrO2 coatings developed by the team combined the hydrophobic barrier effect of the PDMS layer with the reinforcing ZrO2 nanoparticles, highlighting the potential of organic coatings incorporated with nanoparticles of metal oxides for improving the corrosion resistance of magnesium alloys.
Results of the Study
The team developed a PDMS-ZrO2 coating for magnesium alloy to improve the corrosion resistance of the Mg allow while also mitigating the swelling characteristic of PDMS.
A spin coating process was used to apply PDMS-ZrO2 coatings onto the Mg alloy surface. Including ZrO2 nanoparticles transformed the PDMS molecular chains into a network structure.
The reinforcing ZrO2 nanoparticles incorporated in the PDMS chains enabled the PDMS-10%ZrO2 coatings to show strong hydrophobic behavior and thermal stability up to temperatures of 315 °C.
The PDMS-ZrO2 coatings showed a greatly increased corrosion resistance. The greatest corrosion resistance was provided by the PDMS-10%ZrO2 coating, which exhibited an open circuit potential of about -1.45 V, a corrosion potential of -1.22 V, and a corrosion current density of 1.11-9 A cm-2.
The exceptional corrosion resistance exhibited by the PDMS-10%ZrO2 composite may be attributed to its strong hydrophobic nature, the reinforced framework of PDMS polymers, and the dense stacking arrangement of ZrO2 in the PDMS matrix.
The physical barrier performance achieved by the compact framework also played a critical role in the protection performance of the magnesium alloy.
Reference
Yang, J., Chen, A., Liu, F., Gu, L., Xie, X., & Ding, Z. (2022). Hybrid coating of polydimethylsiloxane with nano-ZrO2 on magnesium alloy for superior corrosion resistance. Ceramics International. Available at: https://www.sciencedirect.com/science/article/pii/S0272884222029145?via%3Dihub
Disclaimer: The views expressed here are those of the author expressed in their private capacity and do not necessarily represent the views of AZoM.com Limited T/A AZoNetwork the owner and operator of this website. This disclaimer forms part of the Terms and conditions of use of this website.