PI’s new air-bearing-based high-speed automated photonics alignment system provides maintenance-free, 24/7 performance, and high throughput.
Auburn, MA – PI, a leading provider of precision motion control and nanopositioning solutions, recently unveiled a new automated multi-axis photonics alignment system at the Photonics West and OFC conferences in California. This cutting-edge 3-DOF alignment stage boasts a compact design, powerful algorithms, and intuitive software to provide users with ultra-fast, precise alignment capabilities for fibers, waveguides, and modern silicon photonics devices.
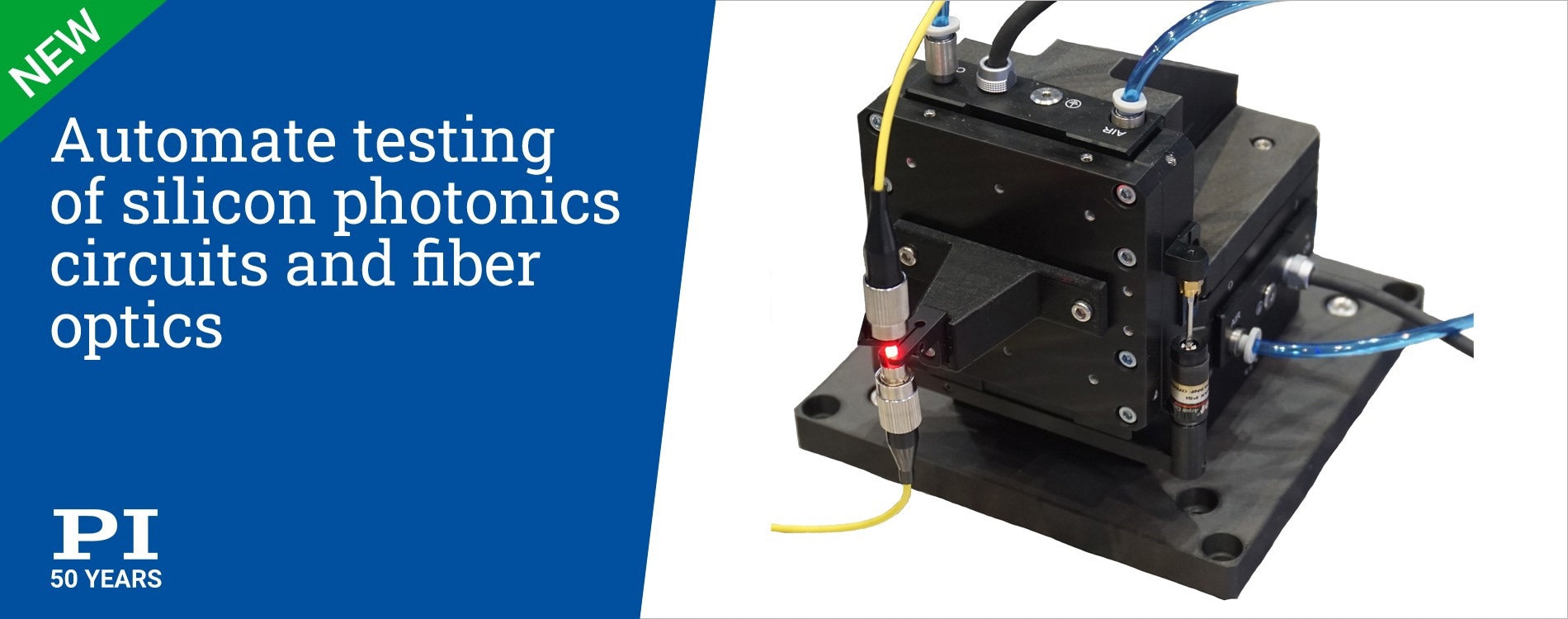
Image Credit: PI (Physik Instrumente) LP
Multi-Axis Stage, Controller, and Software – Ideal for Silicon Photonics and Fiber Alignment Applications
The multi-axis stage is based on friction-free air bearings and linear motors, which enable smooth, continuous motion and nanometer-level resolution. This makes it an ideal solution for high-throughput photonics test and production applications that require high dynamics and long-term stability – i.e. for coupling light into waveguides, fibers, and modern silicon photonics devices.
Ideal for Clean Room Environments – Zero Wear and No Lubricants
The stage's wear-free air bearings and non-contact linear motors ensure clean-room compatibility because no lubricants or wearing parts – such as common in conventional motorized fiber positioning stages with mechanical bearings – are involved in its operation.
On-Board Ultra-Fast Scan and Align Algorithms
The ACS-based motion and alignment controller that powers the stage features embedded ultra-fast scan and alignment routines, including serpentine and circular scans, as well as a fast hill-climb gradient search. Embedded alignment routines provide higher performance, since communication with an external host computer is not required. The advanced photonics alignment system can handle quasi-gaussian profiles, top-hat profiles, and other typical optical power distributions.
User-Friendly Software Packages Reduce Time to Market
To further enhance usability and reduce time-to-market, PI has developed a comprehensive software package called MMI Application Studio. This user-friendly tool enables users to configure, tune, program, and characterize motion performance quickly and easily. The software package also includes ACS host application libraries for popular platforms, such as C/C++, COM, .NET, Python, MATLAB, and Linux, as well as open-source graphical application examples in major languages like LabVIEW, Python, C#, and Visual Basic.
6-DOF Alignment Engines
Finally, for applications that require six degrees-of-freedom alignment, PI also offers a six-axis air bearing alignment engine with controller and software. With this comprehensive suite of solutions, PI is well-positioned to meet the demanding needs of modern photonics and silicon photonics applications.
Working with You
PI’s in-house engineered solutions have enabled customers around the world to increase their productivity and technological advantage for 5 decades. With a large basis of proven motion technologies and methodologies, PI is in the position to quickly modify existing designs or provide a fully customized OEM solution to fit the exact requirements of your application, including fast photonics alignment engines, multi-axis automation sub-systems, nanopositioning stages for semiconductor manufacturing, microscope scanning stages, and piezo transducers / sensors.
About PI
PI is a privately held, global leading company that designs and manufactures world-class precision motion and automation sub-systems including air bearings, hexapod micro-positioning robots, and piezo drives at locations in North America, Europe, and Asia. The company was founded 5 decades ago and today employs more than 1,500 people worldwide. PI’s customers are leaders in high-tech industries and research labs, in market segments such as photonics, life-sciences, semiconductors, industrial automation and aerospace.