Sponsored by HORIBAMay 22 2008
Y2O3 films are good materials for use in many applications such as protection of aluminium and silver mirror coatings, intermediate layers in wide band visible AR coatings and for XeCl laser AR and dielectric mirror designs. The Y2O3 films are hard and usually amorphous with high adhesion to glass, germanium, silicon, zinc sulphide and zinc selenide as well as to metals such as aluminium and silver. In some cases, a very thin layer of yttria can serve as an adherence promoter for multilayer coatings on non-oxide substrates. This material is of medium-index and very transparent over the near-UV range (300 nm) to IR (11ìm) region.
Many methods have been used to produce yttria films such as reactive thermal deposition, e-beam deposition, ion assisted deposition (IAD) and magnetron sputtering. As the refractive indices are dependent on the process it is important to know with high accuracy the optical constants and the thicknesses of the films, especially when they are used as high refractive index materials and in combination with higher index materials such as TiO2 and Ta2O5.
This note describes how the UVISEL Spectroscopic Phase Modulated Ellipsometer from HORIBA was used to characterize the influence of substrate to growth of Y2O3, that is the difference of optical properties of the Y2O3 film grown on amorphous glass substrate and the one grown on pre-evaporated layers of ZrO2.
Sample Preparation
The films were prepared by electron beam evaporation in a reactive oxygen atmosphere. The starting materials were grains of Y2O3. The glass substrates were 5 mm thick and were rotated during deposition to improve the uniformity of the films. In the first run two bare glass substrates were put into the chamber and a ZrO2 film deposited. For the second run one bare glass substrate and the sample from the first run with pre-evaporated ZrO2 were placed into the chamber and a Y2O3 layer was deposited.
Three samples were prepared and characterized as follows.
- Sample1: ZrO2 monolayer (See Application Note, Ref: SE06),
- Sample 2: Y2O3 monolayer,
- Sample 3: Y2O3 on ZrO2 pre-evaporated.
Results
The work was performed using the HORIBA UVISEL Visible Spectroscopic Ellipsometer. The Ellipsometric measurements were made at an angle of incidence of 70° across the spectral range 300-830 nm. Both the refractive indexes and thicknesses were extracted from the SE data analysis. The optical constants were determined using the Lorentz Oscillator formula below:

Characterization of Y2O3 on Glass
Y2O3 is a medium-index and low absorption material. Some amount of index inhomogeneity can appear with increasing layer thickness. The effect can be reduced by providing sufficient oxygen backfill during evaporation. As with the ZrO2 sample (AN SE-06) a great improvement to the ÷² value was found with a two layer model, with the top layer being porous. Using the Effective Medium Approximation (EMA) DeltaPsi2 (DP2) software can determine the degree of porosity compared to the layer on the substrate, and in this case it was found to be 25%.
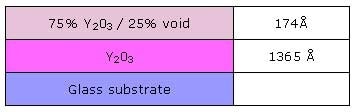
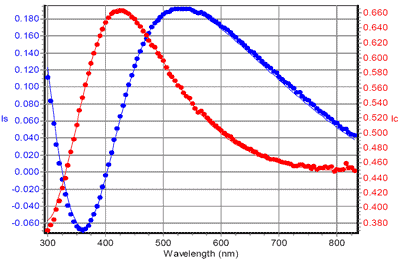
Figure 1. Y2O3 / Glass
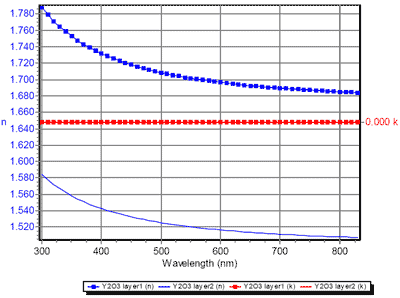
Figure 2. Y2O3 Optical constants
Characterization of Y2O3 on ZrO2
As a first step this sample was characterized using the optical constants found from the previous results. Good values for the films were obtained, but it was found that the results could be improved by the use of a slightly more complicated structure.
Several approaches were followed (interface layer between the two films), but the final model that significantly improved the fit, was the optimisation of the Y2O3 thicknesses, indices and porosity parameters. In the final results the Y2O3 variation in refractive index between two samples was about 0.02.
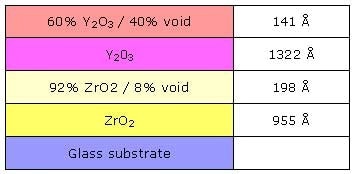
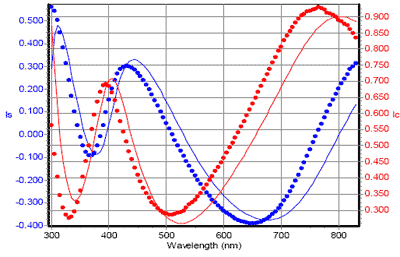
Figure 3. Y2O3 / ZrO2 / Glass
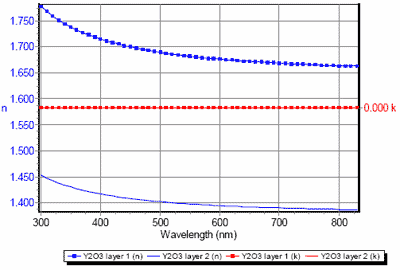
Figure 4. New Y2O3 Optical Constants
Conclusion
The deposition conditions have generated inhomogeneous porous layers that have been observed by the UVISEL Spectroscopic Phase Modulated Ellipsometer. Moreover, the spectroscopic measurements allow determination of the small discrepancies between the optical constants of a Y2O3 film grown at bare substrate and the one grown on a ZrO2 film.

This information has been sourced, reviewed and adapted from materials provided by HORIBA.
For more information on this source, please visit HORIBA.