For EBSD analysis, sample preparation is crucial due to the possibility of escaping of the diffracted electrons from within just a few tens of nanometers of the sample surface. Nevertheless, it is possible to achieve specimen preparation requirements by adhering to some simple recipes.
Significance of Specimen Preparation
As a surface-sensitive technique, the diffraction signal comes from the top few nanometers of the crystal lattice in EBSD. Hence, the top layer needs to be devoid of oxidation, contamination and damage. This makes specimen preparation highly significant for acquiring good EBSD data. Considering the need to tilt the sample up to high angles (typically 70°), it is essential to maintain the surface topography to a minimum.
Standard sample preparation methods are adequate to the final polishing stage for most materials. Hence, the finish suitable for the EBSD analysis can be achieved by means of an additional polishing stage utilizing colloidal silica.
Since different materials react differently to standard preparation methods, the material being analyzed must be taken on an individual basis and prepared properly. The preparation equipment manufacturers can be consulted for applying a given method for a specific material.
Preparation Methods
Various sample preparation techniques are available for the EBSD analysis. However, the selection of the appropriate technique is based on the structure and composition of a sample. Some common examples are discussed in the following sections.
Mechanical Polishing
For EBSD analysis, mechanical polishing is crucial on virtually all samples. It is the appropriate technique to prepare multiphase materials, which are the most difficult to prepare well. It is also ideal to prepare ceramic or geological materials. This process involves the following steps:
Mounting
Although no specific mounting process is ideal for the EBSD analysis, it can be helpful in using a conductive medium, which will minimize any drift or charging when using insulators. Nevertheless, materials such as many geological minerals will expand and possibly fracture when hot mounting processes are used.
Grinding
Grinding is the first mechanical stage of specimen preparation to remove the deformation layer created in sectioning and forms a flat surface. Typically, SiC paper is used for this process. Nonetheless, since different materials exhibit different abrasion characteristics, grinding material and conditions are selected specific to a given sample.
After every grinding stage, it is recommended to analyze the sample surface on a light microscope to ascertain the complete removal of all damage from the earlier stage. The sample preparation is continued in this manner until the finest abrasive size achieved for polishing. The amount of polishing needed to obtain a good surface will greatly be reduced by carefully performing the process.
Polishing
Polishing eliminates most of the damage caused by grinding. Different types of abrasive and suspension mediums are available to perform this task. Diamond polishing compounds or slurries are suitable for preliminary stages for a majority of the materials. Typically polishing is begun on a hard cloth with a coarser abrasive and ended on a softer cloth with a finer abrasive.
Minor deformation remaining after mechanical preparation is removed by Vibratory Polishing, which is engineered for high quality polished surface preparation on many different materials and applications.
A horizontal vibratory motion at a typical rate of 7200 cycles per minute generates a very efficient polishing action with outstanding flatness and superior quality results. The unique vibratory action yields less deformation, flatter surfaces and minimizes edge rounding. It also produces a stress-free surface.
Colloidal Silica
A final polishing stage utilizing colloidal silica is normally required for the EBSD analysis. Final polishing must not be prolonged, but just adequate to obtain the required surface finish without causing excessive relief.
Electropolishing
Electopolishing is ideally suited to prepare samples for many metals, involving material removal from the sample surface through electrolytic action. Most surface irregularities and any deformation layer on the surface are removed by this method. The selection of the appropriate electrolyte solution is specific to the given material.
Ion Milling
Ion milling is capable of producing surfaces ideal for the EBSD analysis with minimal prior preparation. This technique can be used on all types of samples. This process involves bombarding a selected area of the sample surface by an energetic ion beam under vacuum.
The bombardment erodes the surface, but can damage the surface by ion implantation that can result in the formation of an amorphous layer. Hence, rotation and angle of attack is critical.
Well-documented and established sample preparation techniques for most materials are listed in Table 1 for the EBSD analysis.
Table 1. Well documented and established methods for the preparation of most materials.
|
Mechanical Polish |
|
|
Technique |
Standard Metallographic Polish |
Colloidal Silica |
Vibromet |
Electropolish (post mechanical polish) |
Ion mill (ideally post mechanical polish)* |
Metals |
Single Phase |
Y |
Y |
optional |
Y |
Y |
Multi Phase |
Y |
Y |
optional |
No - may cause preferential etching |
Y |
Soft metals e.g. Al, Cu |
Y |
Y |
very useful |
very useful |
Y |
Steels |
Y |
Y |
optional |
Y |
Y |
Ceramics |
Single Phase |
Y |
Y |
very useful |
not required |
Y |
|
Multi Phase |
Y |
Y |
very useful |
not required |
Y |
Geological |
Multi Phase |
Y |
Y |
very useful |
not required |
Y |
|
*Ion milling should ideally be post mechanical polishing. It can be performed on an unprepared sample, but the milling time will be significantly longer
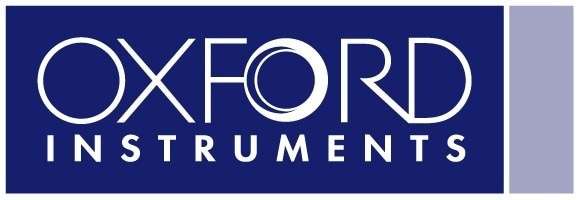
This information has been sourced, reviewed and adapted from materials provided by Oxford Instruments Nanoanalysis.
For more information on this source, please visit Oxford Instruments Nanoanalysis.