Assessing the status of heavy machinery during operation is essential in order to prevent costly repairs and breakdowns. One vital aspect involves monitoring the status of the lubricants or oil used to lubricate a wide range of components such as gearboxes, transmissions, engines and various other vital areas: if the oil becomes highly contaminated or degrades too much, it can damage various components.
Even though a number of aspects of in-service oils have to be monitored, the metal content provides information regarding the condition of both the oil and the engine to help determine when the oil has to be changed and also gauge the health of the engine. In view of this importance, ASTM developed a method for analyzing in-service oils: method D5185.
Given that metal concentrations are usually greater than 1 ppm, D5185 has specified ICP-OES as the analytical technique, together with specific criteria, as shown in Table 1. However, several labs that run D5185 process hundreds of samples on a daily basis, making it difficult to adhere to the method.
As a result, shortcuts are frequently taken to enhance sample throughput while maintaining quality data. Table 1 also shows the most common modifications.
Table 1. Highlights of ASTM D5185 and common implementation.
Parameter |
Specified by D5185 |
Common Implementation |
Elements |
Al, Ba, B, Ca,Cr, Cu, Fe, Pb, Mg, Mn, Mo, Ni, P, K, Na, Si, Ag, S, Sn, Ti, V, Zn |
Elements important to the components being tested |
Sample Preparation |
By weight |
By volume |
Internal Standard |
Cd, Co, or Y |
Co |
QC Frequency |
Every 5 samples |
Varies between 10-25 samples |
QC Limits |
± 5% |
± 10% |
Simultaneous ICP-OES instruments are preferred for high-throughput labs because of their ability to run many wavelengths at the same time. However, there are a reasonable number of labs with lower sample volumes where analytical speed is not as important. A lower-cost, hybrid scanning ICP-OES is considered to be the ideal instrument in these instances.
This article will focus on the analysis of in-service oils using PerkinElmer’s Avio™ 200 ICP Optical Emission Spectrometer1 (ICP-OES), following a common implementation of ASTM D5185.
Experimental
Samples and Standards Preparation
In-service oil samples were obtained and diluted 10x by volume with V-Solv™ as a diluent, which was spiked with 40 ppm cobalt (Co) (to act as an internal standard).
Calibration curves were produced from a 75 cSt base oil as a blank, three V-23 stock solutions at 50, 100, and 500 ppm (PerkinElmer), and a Metals Additives Standard (MA4) (PerkinElmer) which contains Ca at 5000 ppm and P, Mg, and Zn at 1600 ppm.
All standards and the blank were prepared the same way as the samples. The 50 ppm V23 and the MA4 standards were used as QC samples during sample analysis. The MA4 was used as the QC for the additive elements, and the 50 ppm QC was used for all wear and contaminant metals.
Instrument Conditions
All analyses were carried out on the Avio 200 ICP- OES running in radial mode using the conditions in Table 2, with the analytes and wavelengths listed in Table 3.
These wavelengths have proven over many years to be interference-free in this application when using a spectrometer whose measured resolution is equal to or less than 0.008 nm at 200 nm. The nebulizer gas flow was altered so that the tip of the “green bullet” in the central channel was just below the top flat plate, as shown in Figure 1.
Table 2. Avio 200 ICP-OES instrumental parameters and conditions.
Parameter |
Value |
Nebulizer |
GemCone™ (modified Babbington) |
Spray Chamber |
Baffled glass cyclonic |
RF Power |
1500 W |
Torch |
3-Slot Avio torch for organics |
Injector |
1.2 mm ceramic |
Plasma Gas Flow |
10 L/min |
Aux Gas Flow |
0.8 L/min |
Nebulizer Gas Flow |
0.40 L/min |
Torch Position |
-4 |
Sample Uptake Rate |
2.0 mL/min |
Sample Uptake Tubing |
Black/Black (0.76 mm id), Viton |
Drain Tubing |
Red/Red (1.14 mm id), SolvaFlex |
Read Delay |
18 sec |
Replicates |
2 |
Rinse Between Samples |
12 sec (fast pump at 6 mL/min) |
Auto Integration Range |
0.2 - 1.0 sec |
Table 3. Analytes and wavelengths.
Element |
Wavelength (nm) |
Al |
394.401 |
Ag |
328.068 |
B |
249.677 |
Ba |
232.527 |
Ca |
315.887 |
Cd |
228.802 |
Cr |
205.560 |
Cu |
324.752 |
Fe |
259.939 |
K |
766.490 |
Mg |
279.077 |
Mo |
203.845 |
Mn |
257.610 |
Na |
588.995 |
Ni |
232.003 |
P |
214.914 |
Pb |
220.353 |
Sb |
217.582 |
Si |
288.158 |
Sn |
189.927 |
Ti |
334.940 |
V |
292.464 |
Zn |
213.857 |
Co (internal standard) |
228.616 |
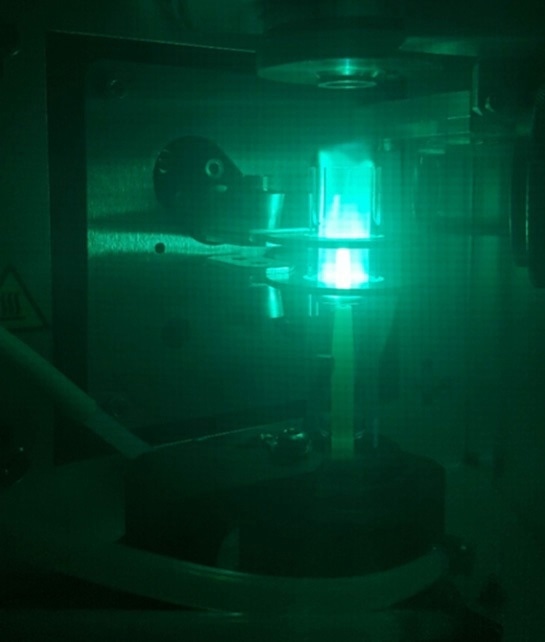
Figure 1. Correct position of green carbon "bullet" just below the second plate of Avio’s unique Flat Plate plasma technology, when aspirating V-Solv.
Results and Discussion
With the instrumental parameters shown in Table 2, the Avio 200 ICP-OES is capable of running a sample in five minutes, which includes measuring the 23 elements listed in Table 3 as well as the internal standard in two replicates. The analysis time is further reduced when fewer elements are measured.
This analytical speed is all that is required for a low-volume, in-service oil lab running 10 - 50 samples a day. Table 4 shows the results from a typical in-service oil sample.
The QC samples were measured both at the beginning and end of a run consisting of 15 in-service oil samples in order to determine stability. The results of the final QC sample are shown in Table 5, demonstrating that all elements recovered are within ± 10% of the true value and meet the acceptance criteria of standard in-service oil labs.
These results demonstrate the stability of the methodology, enabling a low-volume, in-service oil lab to effortlessly perform their daily analyses with the Avio 200 spectrometer.
A number of instrumental considerations of the Avio 200 ICP-OES contribute to its stability. First, the vertical torch demonstrates that any non-ionized sample will drain back down the torch instead of pooling in the injector, resulting in few carryover effects.
The shear gas cuts off the end of the plasma and prevents deposition on the axial window. Even though the axial mode is not used in this analysis, this feature enables using the Avio 200 for other analyses without having to worry about deposition or cone maintenance.
Finally, Avio’s unique Flat Plate™ plasma technology forms the plasma (Figure 1). This technology is extremely robust and does not require cooling, which translates to increased stability. Additionally, the flat plates reduce argon consumption: only 11.2 L/minute of total argon were used for these analyses.
Table 4. Results from a typical in-service oil sample.
Element |
Concentration (ppm) |
RSD (%) |
Al |
16 |
3.1 |
Ag |
< 0.5* |
- |
B |
81 |
2.8 |
Ba |
< 0.5* |
5.9 |
Ca |
2441 |
0.21 |
Cd |
< 0.5* |
- |
Cr |
1 |
2.6 |
Cu |
1 |
0.26 |
Fe |
27 |
0.44 |
K |
5 |
8.0 |
Mg |
17 |
2.2 |
Mo |
25 |
0.87 |
Mn |
1 |
0.69 |
Na |
236 |
0.44 |
Ni |
2 |
12 |
P |
847 |
1.9 |
Pb |
7 |
0.65 |
Sb |
< 0.5* |
- |
Si |
9 |
4.2 |
Sn |
< 0.5* |
- |
Ti |
< 0.5* |
- |
V |
< 0.5* |
- |
Zn |
974 |
2.8 |
* = lower quantification limit
Table 5. Final QC check samples of a 20 sample analytical run.
Element |
Final QC |
Concentration (ppm) |
% Recovery |
Al |
50 |
100 |
Ag |
48 |
96 |
B |
54 |
108 |
Ba |
49 |
98 |
Ca |
45 |
90 |
Cd |
50 |
100 |
Cr |
50 |
100 |
Cu |
50 |
100 |
Fe |
53 |
106 |
K |
49 |
98 |
Mg |
46 |
92 |
Mo |
49 |
98 |
Mn |
49 |
98 |
Na |
49 |
98 |
Ni |
49 |
98 |
P |
46 |
92 |
Pb |
50 |
100 |
Sb |
50 |
100 |
Si |
48 |
96 |
Sn |
49 |
98 |
Ti |
50 |
100 |
V |
49 |
98 |
Zn |
47 |
94 |
Conclusion
This article has shown the ability of the Avio 200 ICP- OES to examine in-service oils after a common implementation of ASTM method D5185. The five-minute analysis time is fast enough for low-volume labs, even though it is not as appropriate for high-throughput laboratories running hundreds of samples a day.
Analysis time improves as the number of elements decreases, making the Avio 200 an ideal choice for labs wishing to implement D5185 while leveraging the Avio 200 benefits.
Consumables Used
Component |
Part Number |
Sample Uptake Tubing, Black/Black (0.76 mm id), Viton |
N0773118 |
Drain Tubing, Red/Red (1.14 mm id), SolvaFlex |
09923037 |
Metal Additives Standard, MA4 |
N9308259 (100 g)
N0776108 (200 g)
N9308333 (400 g) |
V-23 Wear Metals Standard, 50 µg/g |
N9308243 (100 g)
N0776104 (200 g)
N9308317 (400 g) |
V-23 Wear Metals Standard, 100 µg/g |
N9308245 (100 g)
N0776105 (200 g)
N9308318 (400 g) |
V-23 Wear Metals Standard, 500 µg/g |
N9308249 (100 g)
N0776106 (200 g)
N9308320 (400 g) |
Cobalt Internal Standard, 6% in hydrocarbon oil |
N0776107 (200 g)
N9304168 (400 g) |
V-Solv Solvent |
N9308265 (1 gallon)
N9308378 (5 gallons) |
Sample Tubes, 17x100 mm, 1200 |
N0777167 |
References
1. http://www.perkinelmer.com/product/avio-200-icp-optical-emission-spectrometer-avio200
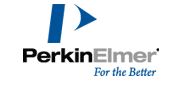
This information has been sourced, reviewed and adapted from materials provided by PerkinElmer Inc.
For more information on this source, please visit PerkinElmer Inc.