With ever-increasing reliance and use of electronics, new products are being continually developed by manufacturers with improved capabilities. As a result of this, the lifetime of electronics is becoming shorter as consumers upgrade to newer more advanced models, more frequently.
Although electronic recycling programs have been implemented and still continue to grow, the number of electronic products being discarded continues to rise.
Electronics contain a number of components, so there is a possibility that metals will enter into the environment after the product is discarded. The toxicity of metals such as mercury (Hg), cadmium (Cd), lead (Pb), and chromium (Cr, particularly hexavalent Cr [CrVI]), are of greatest concern.
The Restriction of Hazardous Substances (RoHS) directive1 enforced limits for the levels of CrVI, Cd, Pb, and Hg which can be found in electronic devices, as shown in Table 1.
Table 1. RoHS elemental limits.
Element |
Limit |
Cadmium |
0.01% |
Chromium (hexavalent) |
0.1% |
Mercury |
0.1% |
Lead |
0.1% |
The most efficient and easy way to satisfy the RoHS directive is to use of inductively coupled plasma optical emission spectroscopy (ICP-OES) for analysis and microwave digestion for sample preparation.
Although ICP-OES cannot distinguish the various element forms, the total Cr present can be measured to determine if it is below or above the regulated level. If it is above the limit, other techniques can be used for sample preparation and analysis to determine CrVI.
This article focuses on the analysis of different sample types existing in electronics to satisfy the RoHS directive using ICP-OES, together with sample preparation considerations.
Experimental
Samples and sample preparation
It is impossible to evaluate all of the various sample types that come under the RoHS directive. Nevertheless, a representative selection of sample types were analyzed: wire insulation, plastics, solder, a circuit board, and wire, all collected from discarded electronic products (except the solder, which was new).
As the sample types were diverse, microwave digestion provides the most flexibility and highest probability of complete digestion. For each sample type, the microwave methodology can be optimized, but the aim was to develop a single sample preparation scheme that could be used for several sample types so that the sample preparation process can be simplified.
The preparation variations between sample types were minimized, although a single method was not possible for this sample set.
Table 2 displays the details of the assessed samples, which were collected from disposed electronic equipment (with the exception of the newly purchased solder). After cutting the samples into small pieces, portions weighing 0.2 g were used for analysis.
Table 2. Sample information.
Group |
Acids Used for Digestion |
Sample Type |
Specific Sample Info |
1 |
HNO3 (70%) 6 mL
H2SO4 (98%) 4 mL |
Plastic
Wire Insulation
Metal |
Black (from TV remote control)
White (from cordless telephone)
Green(from surge protector)
Black (from surge protector)
White (from surge protector)
Tan (from surge protector power cord)
Copper wire (from surge protector) |
2 |
HNO3 (70%) 8 mL
HF (49%) 2 mL |
Circuit Board
Metal |
From cordless phone (chips removed)
Solder (RoHS compliant) |
A PerkinElmer Titan MPS™ Microwave Sample Preparation System was used to digest the samples. Initially, a sample weighing 0.2 g was added to every digestion vessel, followed by the suitable acids (trace metal grade) as illustrated in Table 2; nitric acid was added first to each vessel.
The vessels were kept open for approximately 10 minutes to permit any pre-digestion that can occur; then they were sealed and kept in the Titan MPS system. Table 3 lists the Titan program used for all samples; only the acids were different for the sample types.
Table 3. Titan MPS microwave digestion program.
Step |
Temp (°C) |
Pressure Limit (bar) |
Ramp (min) |
Hold (min) |
Power (%) |
1 |
170 |
35 |
5 |
5 |
90 |
2 |
220 |
35 |
5 |
15 |
90 |
3 |
50 |
35 |
1 |
10 |
0 |
After digestion, the samples were diluted to 50 mL with 5% HCl (v/v) to complex the mercury. With the exception of the solder, which was diluted with deionized (DI) water because HCl caused the formation of a white precipitate. Table 4 shows the regulatory levels for the elements in solution after the sample preparation scheme.
Table 4. Regulatory levels for RoHS elements in solution with current sample preparation procedure.
Element |
RoHS Limits (% in solid) |
RoHS Limit in Solution (mg/L) |
Cadmium |
0.01 |
0.4 |
Chromium |
0.1 |
4 |
Lead |
0.1 |
4 |
Mercury |
0.1 |
4 |
All quantitative measurements were made against calibration curves prepared in a mixture of 1% HCl (v/v), 5% sulfuric acid (H2SO4) (v/v), and 10% nitric acid (HNO3) (v/v) using 0.5 and 1 ppm standards; yttrium (Y, 0.5 ppm) was used as an internal standard. To evaluate accuracy, pre-digestion spikes at the regulatory levels and 10x below were added to the digestion vessels before adding the acids.
Instrumental Conditions
A PerkinElmer Avio™ 200 ICP Optical Emission Spectrometer was used for all analyses, where the spectrometer was operated in axial mode. Table 5 lists the elements and wavelengths, and Table 6 shows the instrumental parameters. At 0.5 ppm, yttrium was added to all standards and samples. The rinse solution contained 5% HNO3 (v/v) and 2% HCl (v/v); HCl aids in mercury washout.
Table 5. Elements and Wavelengths
Element |
Wavelength (nm) |
Cadmium |
228.802 |
Chromium |
267.716 |
Lead |
220.353 |
Mercury |
253.652 |
Yttrium (int. std.) |
371.029 |
Table 6. Avio 200 ICP-OES instrumental parameters
Parameter |
Value |
Nebulizer |
Cross flow |
Spray Chamber |
Ryton Scott double-pass |
Sample Uptake Rate (mL/min) |
1.5 |
Plasma Flow (L/min) |
8 |
Aux Flow (L/min) |
0.2 |
Nebulizer Flow (L/min) |
0.6 |
RF Power (W) |
1500 |
Viewing Distance (mm) |
15 |
View |
Axial |
Integration Window |
0.1-2.0 sec |
A short auto integration time window could be used, because the compliance limits for RoHS are at concentrations easily seen with the Avio 200. This increases the analytical speed and sample throughput without compromising accuracy.
All analyses were conducted using only 8 L/min of argon, due to Avio's unique Flat Plate™ plasma technology. Argon consumption and cost are minimized due to the low flow combined with the rapid sample analysis.
Results and Discussion
It is important to establish the digestion conditions at the initial stage. While the goal of a single acid mixture and single Titan program for all samples was not realized in this study, it was discovered that two different acid mixtures could be used with the same program to digest all samples effectively.
As the samples were of diverse nature, H2SO4 was effective, as it substantially reduces the vapor pressure in the vessels, allowing higher temperatures to be reached, which increased the efficiency of the HNO3. However, the H2SO4/HNO3 mixture did not fully dissolve the solder or circuit board, probably because of the presence of silica. As a result, HCl was required and found to be effective when mixed with HNO3.
In all cases, the digestion process involved the generation of a significant amount of gas. Most of the dissolved gas was ejected during the transfer to the autosampler tubes and dilution. However, it is recommended that for complete degassing, the samples need to be allowed to be kept in open containers for 30 minutes before the analysis. Dissolved gas present in the samples leads to high relative standard deviations during the analysis.
These conditions were effective for all of the samples in this study, but there is no guarantee that they will lead to full digestions for all sample types listed in the RoHS directive, but can serve as a starting point. Irrespective of the required acid combinations, closed vessel digestion needs to be used for preventing the loss of Hg, which is a volatile element.
To ensure calibration accuracy, check standards at 10 times less than the RoHS levels (in solution) were analyzed directly after the calibration curves. Table 7 shows the recoveries, indicating precise results at high and low levels.
Table 7. Recoveries of low and high level check standards.
Element |
Low Standard (ppm) |
Recovery (%) |
High Standard (ppm) |
Recovery (%) |
Cd |
0.04 |
101 |
0.4 |
97 |
Cr |
0.4 |
96 |
4 |
93 |
Hg |
0.4 |
99 |
4 |
97 |
Pb |
0.4 |
98 |
4 |
96 |
After ensuring that low and high concentrations can be accurately measured, the samples were analyzed, and the results are presented in Table 8. For Cr, Cd, and Hg, all samples were below the RoHS limits, but the Pb levels varied substantially between samples.
Plastics and the copper wire had Pb below the regulated levels. Pb was present in the solder but was below the RoHS level, confirming that the solder is RoHS compliant. However, Pb was more than the regulated level in the circuit board and the wire insulations.
Repeated analyses of other samples of the circuit board and the wire insulations presented equivalent results. The high Pb values from the circuit board could have resulted from the use of the non-RoHS-compliant solder.
Table 8. Sample analysis.
Sample |
Cd (weight %) |
Cr (weight %) |
Hg (weight %) |
Pb (weight %) |
Plastic (white) |
< 0.001 |
< 0.001 |
< 0.001 |
< 0.001 |
Plastic (black) |
< 0.001 |
< 0.001 |
< 0.001 |
0.001 |
Wire Insulation (green) |
< 0.001 |
0.005 |
< 0.001 |
0.927 |
Wire Insulation (black) |
0.004 |
< 0.001 |
0.001 |
1.01 |
Wire Insulation (white) |
< 0.001 |
< 0.001 |
< 0.001 |
1.31 |
Wire Insulation (tan) |
< 0.001 |
< 0.001 |
< 0.001 |
1.09 |
Solder (RoHS compliant) |
< 0.001 |
< 0.001 |
0.002 |
0.053 |
Circuit Board |
< 0.001 |
< 0.001 |
< 0.001 |
0.363 |
Copper Wire |
< 0.001 |
< 0.001 |
0.002 |
< 0.001 |
* Results in bold indicate concentrations above the RoHS limits.
Pre-digestion spikes were evaluated to assess the accuracy of the methodology and confirm that the sample preparation process does not influence recoveries. For selected samples, spikes were added to the digestion vessels after the addition of sample, but prior to the addition of the acids.
Spikes were made at two levels: 10 times below and at the RoHS levels (in solution). The Cd was spiked at concentrations 10 times lower than the other elements, since the RoHS regulations were 10x lower for Cd than the other elements. All recoveries were within 10% of the spiked values (as illustrated in Table 9), demonstrating that no substantial contamination or element loss occurred during the digestion process. The accuracy of the technique was also validated by the precise spike recoveries.
Table 9. Pre-digestion spike recoveries.
Sample |
Spike (ppm) |
Cd (% Recovery) |
Cr (% Recovery) |
Hg (% Recovery) |
Pb (% Recovery) |
Cd |
Others |
Digest Blank |
0.04
0.4 |
0.4
4 |
100
97 |
95
92 |
100
104 |
103
105 |
Plastic – White |
0.04
0.4 |
0.4
4 |
99
99 |
96
98 |
100
104 |
103
105 |
Copper Wire |
0.04
0.4 |
0.4
4 |
108
101 |
91
90 |
95
95 |
104
107 |
Conclusion
The study demonstrated the ability of the Avio 200 ICP-OES and the Titan MPS Microwave Sample Preparation System to quickly and precisely measure elements in various sample types falling under the RoHS directive.
With suitable selection of acids, various sample types can be digested using a single Titan MPS microwave program, reducing the complexity associated with sample preparation for a wide variety of sample types covered under the RoHS directive. Pre-digestion spike recoveries demonstrate that elements are not lost in the sample preparation procedure and that substantial contamination is not introduced.
Consumables Used
Avio 200 ICP-OES |
Component |
Part Number |
Sample Uptake Tubing – 0.76 mm id (Black/Black) PVC |
09908587 |
Drain Tubing – 1.14 mm id (Red/Red) PVC |
09908585 |
Pure-Grade Cadmium Standard, 1000 mg/L |
N9300176 (125 mL)
N9300107 (500 mL) |
Pure-Grade Chromium Standard, 1000 mg/L |
N9300173 (125 mL)
N9300112 (500 mL) |
Pure-Grade Mercury Standard, 1000 mg/L |
N9300174 (125 mL)
N9300133 (500 mL) |
Pure-Grade Lead Standard, 1000 mg/L |
N9300175 (125 mL)
N9300128 (500 mL) |
Pure-Grade Yttrium Standard, 1000 mg/L |
N9303810 (125 mL)
N9300167 (500 mL) |
Autosampler Tubes – 50 mL, Conical, Free-Standing |
B0193534 |
Titan MPS Digestion System |
Component |
Part Number |
Consumables Kit for Standard 75 mL
Digestion Vessels |
N3132000 |
Rupture Disks for Standard 75 mL
Digestion Vessels (25 pieces) |
N3132001 |
Pressure Seal for Standard 75 mL
Digestion Vessels (10 pieces) |
N3132002 |
End Cap Plug for Gas Containment Manifold |
N3134004 |
Single Lip Seal Forming Tool for Standard 75 mL
Digestion vessels |
N3132015 |
References
1. ec.europa.eu
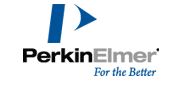
This information has been sourced, reviewed and adapted from materials provided by PerkinElmer Inc.
For more information on this source, please visit PerkinElmer Inc.