Negative-stiffness mechanical isolators can be used for achieving high-performance vibration isolation in a small microscope platform.
It can be challenging to use microscopy for imaging materials, molecules, and interfaces at micro- and nanometer scales. Laboratory micro- and nanoanalysis methods like super-resolution optical microscopy, atomic force microscopy (AFM), advanced surface spectroscopy analysis techniques such as surface-enhanced Raman scattering (SERS), and scanning tunneling microscopy (STM), are all intended to enhance rigidity and reduce the drift to influence precise recordings.
In order to realize accurate imaging, the chemical composition and behavior of these small structures necessitate the microscopy instruments to be positioned in an ultrastable operating atmosphere (free from operational and ambient vibrations to the maximum possible extent) since the measured signals can be affected by frequencies in the range of <1 Hz to 400 Hz.
The origin of these vibrations could be from motors, wind, fans, seismic activity, compressors, nearby construction and transportation, pumps, elevators, and air handling equipment for building heating, cooling, ventilation, and safety in laboratories.
These are the sources of ambient vibration throughout the entire building structure, which is transmitted to the sensitive microscopy instrumentation. In general, the vibration is more prominent if the instrumentation is positioned in higher floors within a building, or is positioned closer to the vibration source.
Several vibration-isolation systems have been employed to reduce or eliminate the effect of these vibrations on sensitive microscopy instruments. These solutions range from comparatively simple metal springs, rubber blocks, and bungee cord-suspended breadboards, to more advanced active electronic systems, air tables, and passive isolation systems developed with more sophisticated technologies and materials for higher precision vibration isolation at lower frequencies.
Adaptable Vibration Isolation
The nature of micro- and nanometer-scale research calls for low-frequency vibration isolation with higher precision compared to what was achievable in the past with conventional techniques; therefore, this requires vibration isolation systems to offer improved location flexibility and adaptability to space limitations (Figure 1).
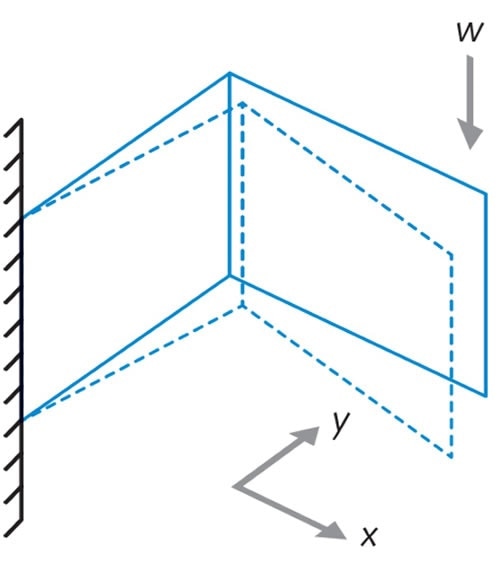
Figure 1. Shown is a schematic of a typical cantilevered horizontal-motion flexure that permits a low isolator height and low horizontal natural frequencies; bearing a weight load W on its end, the flexure has x and y displacement capability.
Floor space for laboratory research is becoming more and more expensive. Engineers and researchers must locate their instrumentation in different locations where vibration noise is considerably high. Interferometers, scanning probe microscopes, and stylus profilers are being installed in locations that present significant challenges to vibration isolation.
As a result, a number of commercial and academic research laboratories do not only provide deficient vibration isolation for their ultrasensitive microscopy instruments, these systems also lack the flexibility to adjust to space constraints and diverse locations.
The new yardstick for vibration isolation systems for micro- and nano microscopy can be specified as ‘universally adaptable’. These can be illustrated by three factors:
- Low-frequency isolation in vibration-prone locations
- Portable vibration isolation, eliminating the need for air or power
- Adaptable for low-frequency vibration isolation within extreme space limitations
Of the above-mentioned features, they have the potential to adapt to extreme space limitations, while isolating low-frequency vibrations, and this has not yet been achieved by microscopy laboratories to date.
Low-Height, Low-Frequency Platform Mitigates Space Constraints
The conditions of close monitoring needed for controlled environments such as cleanrooms and vacuum chambers, necessitates that every inch of space on breadboards and platforms (which supports the precision microscopy instrumentation of a laboratory within these environments) are used to the maximum possible extent.
In controlled environments such as these, benchtop and floor spaces are both optimized equally. Furthermore, microscopy laboratories that operate outside of controlled environments often function under restricted parameters, with little room to spare.
In such environments, options for vibration isolation for microscopy instrumentation have been restricted to systems measuring several inches in height and even higher, which can be too tall for many people. This could lead to constrained working conditions and restrict the instrumentation that can be included on the platforms and breadboards.
Thanks to the design of the CT-1 negative-stiffness vibration-isolation tabletop platform from Minus K Technology, the product substantially overcomes the space-constraint problem since it has a height of just 2.25 inches.
The platform has a vertical natural frequency of 0.5 Hz and horizontal natural frequencies of 2 to 2.25 Hz (Minus K has been working to achieve even lower horizontal natural frequencies). These are significantly lower figures compared to the vibration isolation performances of active systems and air tables.
Negative-stiffness isolators realize low-frequency vibration isolation based on a completely mechanical concept (Figure 2). The passive mechanical mode avoids the need for compressed air or electricity. There are no pumps, motors, or chambers, as well as no maintenance being required since there is nothing to wear out.
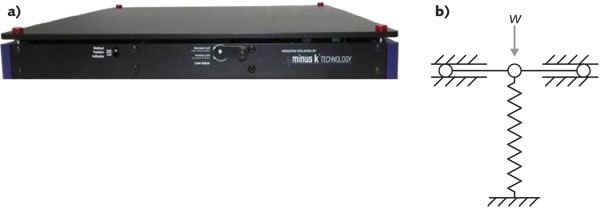
Figure 2. This low-height, low-frequency vibration isolation platform firstly mitigates space constraints in microscopy applications and secondly, relies on negative-stiffness vertical motion isolation.
During negative-stiffness vibration isolation, isolation of the vertical motion is realized by a stiff spring supporting a weight load, together with a negative-stiffness mechanism. The net vertical stiffness is rendered extremely low without any influence on the static load-supporting potential of the spring.
Unique flexures linked with the vertical-motion isolator in series allow for very low-height and horizontal-motion isolation. The outcome is a compact passive isolator with the ability to achieve high internal structural frequencies and low vertical and horizontal natural frequencies.
The isolator realizes a higher isolation level in various directions and has the flexibility to permit customization of resonant frequencies both horizontally and vertically.
Since the isolator operates in a completely flexural mode, and not in a translational mode, (which can lead to frictional, and stick-slip behavior) it has the ability to operate in environments with very low vibration levels that would not be feasible with top-performance air tables and other vibration-mitigation technologies like active systems.
The measure of the vibration transmitted through the isolator as a function of floor vibrations is known as transmissibility. The negative-stiffness isolator’s transmissibility is considerably optimized over air and active isolation systems. Upon being adjusted to a vertical natural frequency of 0.5 Hz, the negative-stiffness isolator created roughly a 93% isolation efficiency at 2 Hz, 99% at 5 Hz, and 99.7% at 10 Hz.
Conclusion
Negative-stiffness vibration isolation systems have turned out to be an increasingly important choice for micro- and nanotechnology microscopy applications. Apart from being a highly practical vibration solution, they also offer portability and location flexibility that cannot be provided by other vibration isolation systems.
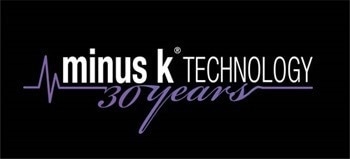
This information has been sourced, reviewed and adapted from materials provided by Minus K Technology.
For more information on this source, please visit Minus K Technology.