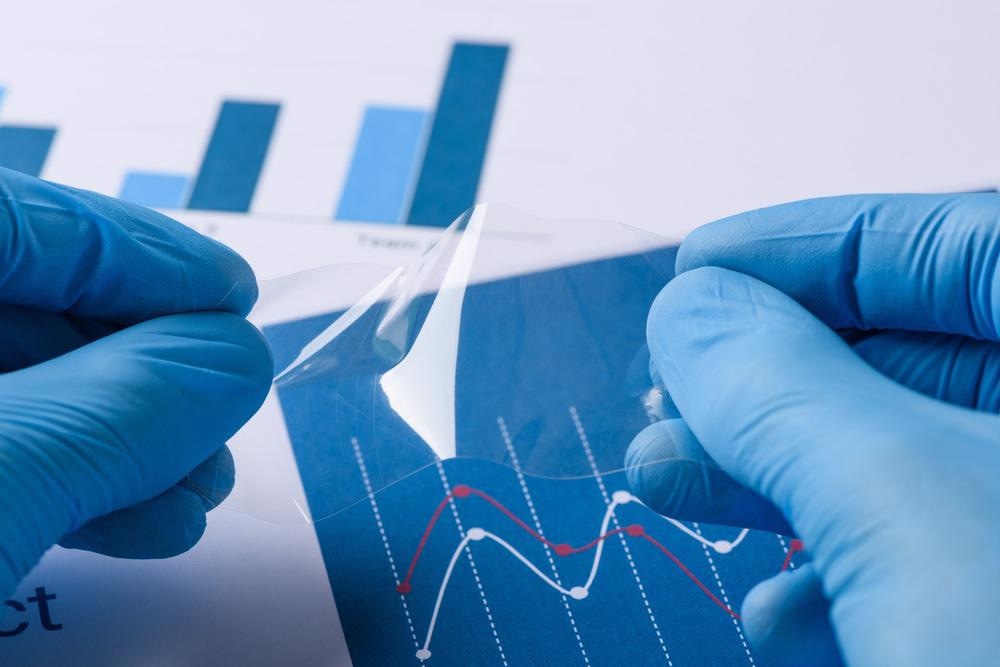
Image Credit: nevodka/Shutterstock.com
Tungsten oxide – when applied as a thin film nanostructure – is an important advanced material used by optics and electronics industries. Research published in February 2021 laid out a deposition method using heat treatment which resulted in a thin film with superior properties to other methods.
Nanotechnology and New Manufacturing
Nanotechnology works with materials and components only nanometres thick (billionths of a meter). Devices built at this minuscule scale are important for many types of advanced manufacturing today – especially in electronics, optics, and related industries.
Nanotechnology is a very recent industrial and academic field, as it has only been possible to work at these scales due to advances in microscopy, precision engineering, and computation. As such, the field is constantly innovating with new techniques and research horizons.
This latest step forward in nanotechnology manufacturing is one of many cutting-edge advances that will likely have real-world applications in the near future due to the field's rapid progression.
What is Heat Treatment?
The paper – published in Materials Science in Semiconductor Processing – describes a heat treatment deposition method for creating a tungsten oxide thin-film material.
The method used – hot filament chemical vapor deposition (HFCVD) – is an additive (or bottom-up) manufacturing method. Instead of chipping away at a material until the desired properties are achieved, tungsten oxide is “grown” into nanometer-thick films through chemical processes.
A hot filament is applied to a chemical mix in vapor form. Chemical reactions then begin to form tungsten oxide in a thin film on top of the substrate material.
How Do We Use Tungsten Oxide Thin Film Materials?
Tungsten oxide is a metal oxide semiconductor material with typical function transition properties. It is used in numerous precision sensing and semiconductor applications.
In the electronics industry, tungsten oxide thin film is used in optoelectronic devices (electronic light sources and sensors) and iontronics (bridging between biological systems and solid-state electronics).
This advanced material is also favored in gas sensing applications due to its selectivity toward toxic gases.
Researchers highlighted tungsten oxide thin films’ already widespread applications in clean technology as well. This semiconductor material is used in photovoltaic energy generation (solar power) and advanced energy storage (batteries).
What are The Effects of Heat Treatment on Tungsten Oxide Thin Film Properties?
Researchers identified numerous and diverse effects of the HFCVD deposition method on the tungsten oxide thin film material they manufactured in tests.
Using X-ray diffraction (XRD), scientists noted development in the WO2 and WO3 phases of the material. XRD also showed up enhanced crystallinity resulting from higher temperatures in the substrate material.
The tungsten oxide thin film itself had fewer defects than had previously been achieved with other manufacturing methods. As well as exhibiting fewer defects, this material also has a lower density of occurrences of dislocation. In nanotechnology, dislocation refers to abrupt changes in the crystalline structure of a material.
XRD performed on the thin film material also revealed that the heat treatment manufacturing method resulted in a material with relatively low micro-strain values (this refers to the mechanical stresses that the material is under).
Tungsten oxide thin films produced by HFCVD in this study benefited from being smoother, with low surface roughness, large grains, and large clusters. Researchers used recent microscopy breakthroughs to accurately describe the material's nanostructural elements, making good use of atomic force microscopy (AFM) for this purpose.
Finally, researchers noted that the tungsten oxide thin films were more electrically conductive relative to the temperature applied to the substrate material. Higher temperatures in manufacturing resulted in more conductivity (lower electrical resistivity) in the final material. This property was studied using the four-probe resistivity method.
Electrical resistivity is closely related to the larger grain and cluster sizes of the material produced with HFCVD. The smoothness and lack of defects in the tungsten oxide thin film contributed to good electrical conductivity.
Next Steps for Tungsten Oxide Thin Film Manufacturing
With these latest findings, researchers and advanced manufacturing enterprises will now be investigating the possibility and viability of using heat treatment for manufacturing tungsten oxide in thin films at larger, commercial scales of production.
If this can be achieved, then the numerous benefits of heat treatment on tungsten oxide thin films' properties will inevitably result in devices with more precision, accuracy, and features in the future.
References and Further Reading
Afsari, A., Sarraf, M.J. and Khatib, F. (2021). “Application of tungsten oxide thin film in the photonic crystal cavity for hydrogen sulfide gas sensing.” Optik. [Online.] https://doi.org/10.1016/j.ijleo.2020.165664.
Hai, Z. et al. (2019). “Nanostructured tungsten oxide thin film devices: from optoelectronics and ionics to iontronics.” Journal of Materials Chemistry C. [Online.] https://doi.org/10.1039/C9TC04489B.
Tan, G-L. et al. (2021). “Effect of heat treatment on electrical and surface properties of tungsten oxide thin films grown by HFCVD technique.” Materials Science in Semiconductor Processing. [Online.] https://doi.org/10.1016/j.mssp.2020.105506.
Disclaimer: The views expressed here are those of the author expressed in their private capacity and do not necessarily represent the views of AZoM.com Limited T/A AZoNetwork the owner and operator of this website. This disclaimer forms part of the Terms and conditions of use of this website.