In-situ plasma cleaning is crucial to avoid gradual contamination of vacuum chamber surfaces and samples at the time of analysis and characterization of nanocrystalline materials and nanostructures.
A plasma cleaner is an essential accessory for the quick and efficient removal of hydrocarbon contamination from samples and vacuum chambers.
The Evactron® plasma radical source functions at turbopump pressures and can produce low-temperature RF plasma with the help of its special RF hollow cathode, thereby enabling it to make oxygen radicals when air is the feed gas.
The pumping system has the ability to eliminate gaseous phases developed by surface hydrocarbons by blending with the oxygen radicals.
Plasma cleaning offers several advantages, such as quicker pump-down times1, no harm to EDS detectors or X-ray windows caused by oxygen radical generation, inhibiting hydrocarbon deposition at the time of imaging, and enhanced image quality of serial block-face SEM volumetric sets2.
Electron backscatter diffraction (EBSD) and transmission Kikuchi diffraction (TKD) are two kinds of scanning electron microscope (SEM) methods for characterizing the microstructures of crystalline materials on the micro- and nano-scale.
The diffraction patterns arise from close proximity to the surface of the sample, implying that to achieve optimal EBSD and TKD results, specimen preparation is crucial. A surface free from preparation-induced contamination and dislocations is essential3.
During the analysis of nanostructured materials, the use of excellent spatial resolution of TKD is favored. The aggregated electron dose (or the electron dose per square micrometer) is very high due to the comparatively weak diffracted signal and the small measurement step size.
The method’s effectiveness is affected by the probability of contamination and drift.
A nanostructured Ni sample was examined by means of TKD to analyze the advantages of plasma cleaning for such kinds of experiments—as part of the test, an analysis speed of around 66 patterns per second (with a CCD-based EBSD detector) and a step size of 4 nm were used.
The data was processed by means of AZtecCrystal, a Nordlys Nano EBSD detector, and a Zeiss Ultra Plus FEG-SEM that used Oxford Instruments Aztec EBSD system. For the initial analysis, plasma cleaning was not performed.
During the second analysis, the sample was cleaned for 5 minutes with plasma inside the microscope chamber before the analysis, even though exactly the same electron beam and EBSD detector settings were used as in the initial analysis.
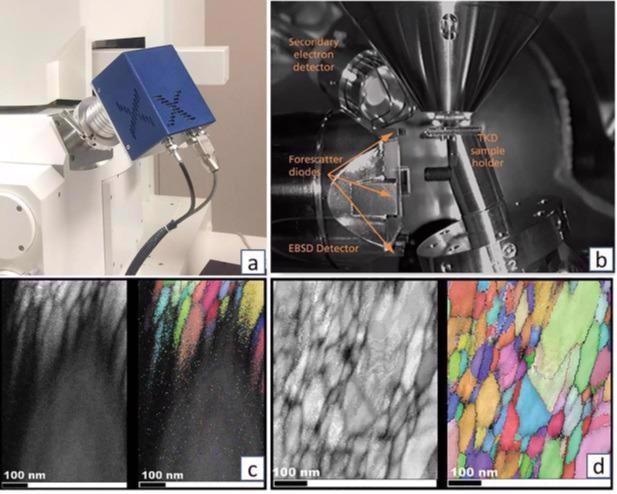
Figure 1. Image Credit: Evactron (XEI Scientific)
Figure 1a illustrates an Evactron® E50 fitted on a SEM chamber. This instrument is one of the latest additions to the XEI Scientific product line.
Positioning of an electron-transparent sample at a short working distance ranging from 5 to 7 mm for TKD experiments is shown in Figure 1b, placing it just on top of the EBSD detector’s phosphor screen.
Figure 1c illustrates the findings from the first test, where plasma cleaning was not performed before analysis.
From the figures, it is clear that even though there was good indexing at first, contamination accumulated, and the pattern’s quality went down quickly with a corresponding drop in indexing. Noticeable sample drift takes place, resulting in a perceived stretching of grain shapes.
Figure 1d illustrates the second analysis, performed following in-chamber plasma cleaning. In this analysis, there was constantly good indexing across the analysis and no deterioration of pattern quality. There was minimal data processing but efficient characterization of the microstructure with some minor drift.
Plasma cleaning integrated with the latest generation of fiber-optic coupled CMOS EBSD with higher sensitivity could allow considerably higher resolution and/or higher speed analyses. This is due to the absence of surface degradation and comparable enhancement in the quality of the diffraction patterns.
The findings illustrated in Figure 2 could be reproduced by making use of optimal sample preparation and then in-situ plasma cleaning—the image depicts a nanocrystalline shear band in a highly deformed AI alloy displayed in a high-resolution TKD map.
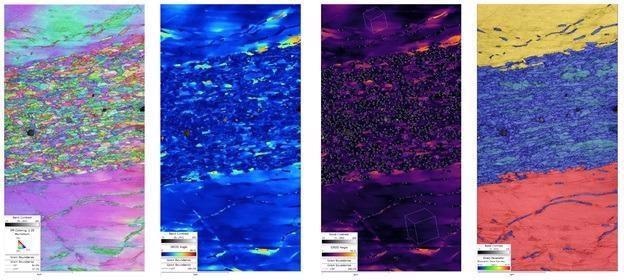
Figure 2. (a) Orientation map using the inverse pole figure (surface normal) coloring scheme. (b) Grain relative orientation deviation (GROD) map superimposed with grain boundaries. (c) Grain relative orientation deviation (GROD) map superimposed with 3D representations of the unit cell orientation of each grain. (d) Grain size map (equivalent circle diameter) with superimposed grain outlines. In all images, the scale bar marks 5 μm, and the maps were collected using a measurement step size of 7.5 nm. Image Credit: Evactron (XEI Scientific)
Several advantages were illustrated in this article concerning plasma cleaning of a sample before TKD experiments.
Experiments of long duration would require improved measurement efficiency and enhancement in pattern quality, which can include several quick scans of the same sample position, for example, repeated analyses for in-situ heating or straining experiments.
Plasma cleaning offers various benefits and is suggested for all high-resolution EBSD and TKD experiments. The plasma cleaning process cleans the chamber, detectors, and holder at the same time, the reason why it is recommended to plasma clean the sample within the microscope chamber.
References
- Ewa Kosmowska et al., (2017) Improved Pump Down Time with Evactron® Turbo PlasmaTM Cleaning. Microsc. Microanal. 23 (Suppl 1): 74-75.
- Barbara Armbruster et al., (2017) Plasma Cleaning Improves the Image Quality of Serial Block-face Scanning Electron Microscopy (SBFSEM) Volumetric Data Sets. Microsc. Microanal. 23 (Suppl 1): 1266-1267.
- Patrick Trimby (2012) Orientation mapping of nanostructured materials using transmission Kikuchi diffraction in the scanning electron microscope. Ultramicroscopy 120: 16-24
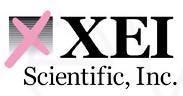
This information has been sourced, reviewed and adapted from materials provided by XEI Scientific.
For more information on this source, please visit XEI Scientific.