Particle Measuring Systems have released a new on-demand E-Book focusing on environmental monitoring for the life sciences and pharmaceutical industry.
This handbook is a timely addition to libraries as the pharmaceutical industry and life sciences sector heads into a new era of requirements with the release of EU GMP Annex 1 2022 and CSS adoption. The handbook is being released to the market on-demand and free of charge in an effort to advance global GMP.
The E-Book covers the fundamentals of cleanroom design and particle counting. It helps establish technology baselines for drug design in the pharmaceutical industry and the manufacture of life sciences products in controlled areas. How to demonstrate control will be explained in-depth.
Standards applicable to production areas, regulatory requirements, and expectations governing aseptic drugs, medical devices, non-sterile products, and advanced therapies release-to-market are covered in the E-Book’s second section.
The final section of this handbook looks into the techniques and instrumentation required to satisfy fundamental principles and the requirements and standards to define the critical approaches to fulfilling quality attributes in the pharmaceutical industry.
Fundamentals: Cleanrooms
Pharmaceutical Cleanroom Design Basics
Pharmaceutical products are manufactured in a controlled environment to satisfy strict regulatory requirements. An example of a controlled environment is a cleanroom employed to reduce contamination risk and overcome challenges with production environment variability.
To meet specific standards, cleanrooms can be regulated. Regular monitoring must ensure constant and comprehensive awareness of current environmental conditions inside cleanrooms and viable and non-viable contamination to satisfy GMP regulations and other standards.
A cleanroom is a controlled environment where air filtration and distribution, equipment, utilities, and construction materials are all tightly maintained to provide control. A cleanroom is the fundamental starting point of contamination control.
Operational procedures are defined and regulated to meet appropriate particulate cleanliness classifications for airborne particle concentration. Rigorous environmental monitoring is vital for the proper operation of cleanrooms.
Types of Cleanrooms
The two basic types of cleanrooms used in the pharmaceutical industry and life sciences sector are detailed below.
Turbulent Airflow Cleanrooms
Turbulent airflow cleanrooms utilize the exchange rate of filtered air to dilute contaminants, ensuring they are within an acceptable threshold. They provide turbulent dilution of contamination.
A central system delivers HEPA-filtered air through diffusion panels located in the ceiling of the cleanroom at an air exchange rate of 10-40+ room volumes per hour. The air exchange rate is a function of operations and the number of personnel within each specific area of the cleanroom.
Returned air in a turbulent airflow cleanroom is then recirculated. A percentage of fresh air is introduced into the environment to maintain an acceptable level of comfort for personnel.
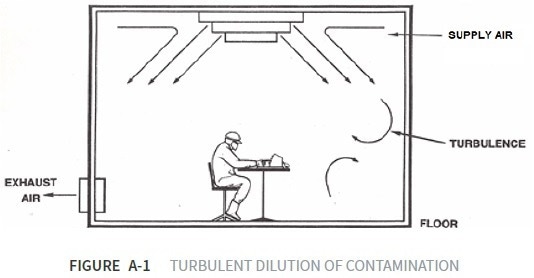
Image Credit: Particle Measuring Systems
Unidirectional Air Cleanroom
In a unidirectional air cleanroom, air velocity is employed as a shroud to prevent contaminant particles from impacting adjacent areas in the controlled environment. The cleanroom is also designed to use airflow to remove operator- or process-generated particles away from critical zones.
The smoke airflow visualization test can confirm the effectiveness of this airflow. Optimal flow rates in a unidirectional air cleanroom are between 0.36 and 0.54 m/s, but other velocities can be employed.
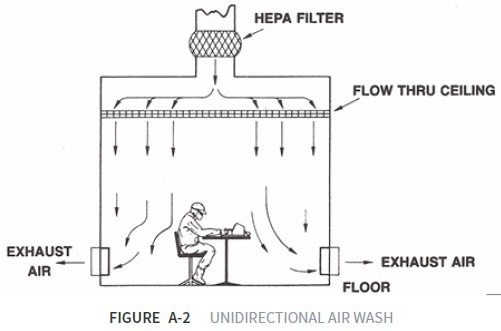
Image Credit: Particle Measuring Systems
Operations typically take place within HEPA-filtered benches in these cleanrooms. This allows for the safe, contaminant-free manual manipulation of products, processing equipment, and containers. Within the benches, either horizontal or vertical airflow can be employed.
Horizontal airflow is directed at the operator. The air flows down over the entire process in the vertical airflow, maintaining a shroud over the critical areas. Both airflows ensure that particulates are blown away from the work area. Vertical airflow allows for fill and finish equipment to be automated and enclosed.
Filling machines can be designed to have access from above, utilizing vertical unidirectional airflow to ensure that processes are isolated from the general room environment. Fixed or flexible curtains can restrict access to critical processing zones.
By utilizing curtains, a certain degree of isolation from the rest of the general room environment is provided for critical process areas. Operators can intervene in the process if required.
Dedicated filters can be employed in critical areas. These filters deliver air specifically to the processing equipment, allowing a lower grade of air to be used in background areas and a higher degree of separation between these areas and critical zones within the cleanroom.
The design can be expanded and scaled up in a unidirectional airflow cleanroom. This creates restricted access barrier protection (RABS), where gloved access ports are required by personnel to access the critical zone. Fully closed isolator systems can be installed to achieve total isolation and enclosed sterilization and sanitation.
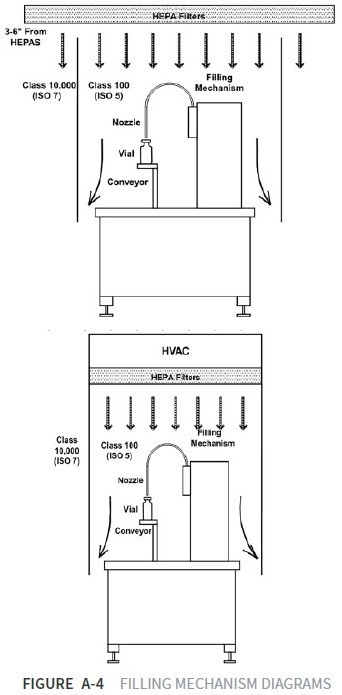
Image Credit: Particle Measuring Systems
Cleanroom choice and activities within these closed environments will also determine the necessary type of environmental monitoring. Greater contamination risk is caused by higher operator access, as personnel are the single greatest source of contamination within a cleanroom.
To read more about environmental monitoring in the pharmaceutical industry, download the full handbook here.
Download the Full Handbook
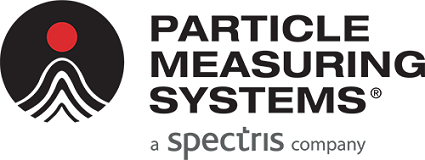
This information has been sourced, reviewed and adapted from materials provided by Particle Measuring Systems.
For more information on this source, please visit Particle Measuring Systems.