Industrial metrology ensures the conformity and validity of production in any industry to meet global standards. This article demystifies the concept of industrial metrology and delves into its importance and application.
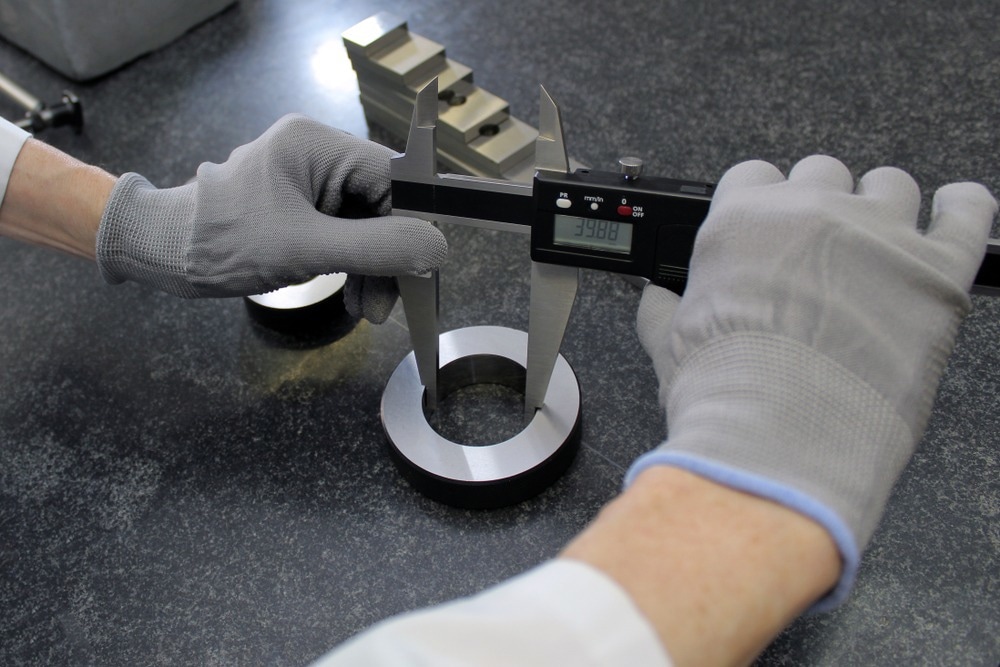
Image Credit: Zabolotskikh Sergey/Shutterstock.com
What is Industrial Metrology?
Metrology is a broad field that refers to the science of measurement, both theoretical and experimental, and its application in industrial settings is termed industrial metrology. Thus, industrial metrology is the infrastructure in a manufacturing unit that ensures high quality and precision during the manufacturing of products.
In addition to maintaining standardized measurements, industrial metrology utilizes computers (hardware and software), microelectronics, and optical techniques to monitor defects, the interchangeability of spare parts, tool wear, and the measurement of machine movement in the machining process.
Thus, utilizing relevant sensing techniques that involve sensors and transducers is common practice in industrial metrology.
Industrial Metrology in Material Science and Engineering
The demand for industrial metrology in materials science has grown over the years to tailor processes, materials, structures, and performance based on desirable applications. The persistent need for miniaturization of critical components and increasing product complexity in nanotechnology have created new challenges to ensure high-quality future products.
In this regard, the challenge of evaluating the shape, size, optical, physical, and other properties of nanomaterials, which is crucial for developing highly reliable nanodevices, has been overcome by industrial metrology through advancements in instruments.
For instance, a recent article published in the journal ChemPhysChem discussed the application of optical tweezers, used in industrial metrology setups, in analyzing objects of atomic size by utilizing the radiation pressure of light.
Another article published in The Journal of Measurement Science discussed the application of a scanning electron microscope (SEM) to detect stress-induced fractures in metallic engineering materials owing to its considerable depth-of-focusing ability. This industrial metrology technique facilitates the fabrication of materials with structural integrity.
Industrial Metrology: Techniques and Technologies
Coordinate Measuring Machine (CMM)
A CMM in an industrial metrology setup helps measure three-dimensional (3D) geometric features, geometric tolerance, shape, and surface finish. Utilizing CMMs aids product development and quality control in the manufacturing, automotive, and aerospace industries.
Optical Digitizers and Scanners
These are non-contact industrial metrology systems used for inspection, dimension measurements, and reverse engineering. This industrial metrology system uses white-light-based scanning technology to obtain several coordinate points that can reveal the 3D structure of an object through reconstruction using the software.
Optical digitizers and scanners can scan objects with complex geometrical features, with high accuracy and precision. This industrial metrology system is used in the automotive, aerospace, heavy machinery, and defense industries.
X-Ray and Computed Tomography
X-ray and computed tomography as an industrial metrology system reveals an object’s internal details of 3D geometries and properties in a non-destructive manner. This equipment is used in materials science, engineering, paleontology, petroleum and reservoir engineering, and other related fields.
Automated Optical Inspection
Automated optical inspection helps detect and classify defects on an object’s surface and is an essential tool within the industrial metrology infrastructure in the manufacturing industry. This technology has efficiently achieved the goals of quality and process improvement.
Using Metrology in Industry
Industrial metrology rooms within manufacturing units, encompassing various instruments, have become crucial for production of high-quality products. The framework, standards, and techniques of industrial metrology play a critical role in determining the reliability of measurement techniques in an industrial setting.
The techniques used in industrial metrology involve mechanical instruments, such as gauges, micrometers, calipers, and non-contact optical, laser, and scanning-based instruments, that guarantee compliance with industry-specific requirements for traceability, consistency, and comparability.
The assessment and management of measurement uncertainty, as a part of industrial metrology, through calibration, statistical analysis, and traceability, makes the manufacturing process a reliable method. Thus, the application of industrial metrology in analyzing and interpreting measurement standards is common practice in process optimization and quality control.
Commercial Landscape of Industrial Metrology
The persistent need for cutting-edge technologies and high-quality products has led to a surge in inspection equipment in recent years. Based on these antecedents, experts anticipate a 3.7 billion growth in the industrial metrology market by 2027, with a compound annual growth rate of 6.1%.
Prominent market players, including Belgium-based Nikon Metrology, United States-based Faro, and German-based Carl Zeiss, offer data management and security, big data analytics, and mobile application solutions within the industrial metrology market.
In particular, the rise of the fourth industrial revolution has led to significant growth in the market for 3D industrial metrology, involving machine learning, interconnection, and real-time data.
Industrial Metrology: The Future
Overall, industrial metrology is a beneficial process that helps meet the demand for manufacturing high-quality products that comply with internationally recognized standards. The industrial metrology infrastructure enforces and confirms the accuracy and traceability criteria necessary to validate the reliability of the measurements.
However, the high cost of precision equipment has hampered the maintenance of inventory consistency in various industries, necessitating manufacturers to outsource measurement needs. Thus, there is scope for cost-effective production of high-precision equipment.
References and Further Reading
Stavroulakis, P. I., & Leach, R. K. (2016). Invited review article: review of post-process optical form metrology for industrial-grade metal additive manufactured parts. Review of Scientific instruments, 87(4). doi.org/10.1063/1.4944983
Kolbow, J. D., Lindquist, N. C., Ertsgaard, C. T., Yoo, D., Oh, S. (2021). Nano‐Optical Tweezers: Methods and Applications for Trapping Single Molecules and Nanoparticles. ChemPhysChem, 22(14), pp. 1409–1420. doi.org/10.1002/cphc.202100004
Czichos, H. (2009). Metrology and testing in materials science and technology. NCSLI Measure, 4(4), pp. 46-77. doi.org/10.1080/19315775.2009.11721494
Mian, S. H., & Al-Ahmari, A. (2014). New developments in coordinate measuring machines for manufacturing industries. International Journal of Metrology and Quality Engineering, 5(1), p. 101. doi.org/10.1051/ijmqe/2014001
Valigi, M. C., Logozzo, S., Butini, E., Meli, E., Marini, L., & Rindi, A. (2021). Experimental evaluation of tramway track wear by means of 3D metrological optical scanners. Tribology-Materials, Surfaces & Interfaces, 15(2), pp. 150-158. doi.org/10.1080/17515831.2020.1830532
Vitoriano, P. M., Amaral, T. G., & Dias, O. P. (2011). Automatic optical inspection for surface mounting devices with IPC-A-610D compliance. In 2011 International Conference on Power Engineering, Energy and Electrical Drives, pp. 1-7. doi.org/10.1109/PowerEng.2011.6036444. https://www.marketsandmarkets.com/Market-Reports/industrial-metrology-market-190782079.html
Disclaimer: The views expressed here are those of the author expressed in their private capacity and do not necessarily represent the views of AZoM.com Limited T/A AZoNetwork the owner and operator of this website. This disclaimer forms part of the Terms and conditions of use of this website.