A nanoindenter is a versatile tool used to measure the mechanical properties of a material. Although this instrument was primarily developed to assess the localized hardness of a material, presently, nanoindentation is used to measure fracture toughness, creep, elastic modules, dislocation nucleation, stress relaxation, cracking, and the viscoelastic properties of samples.
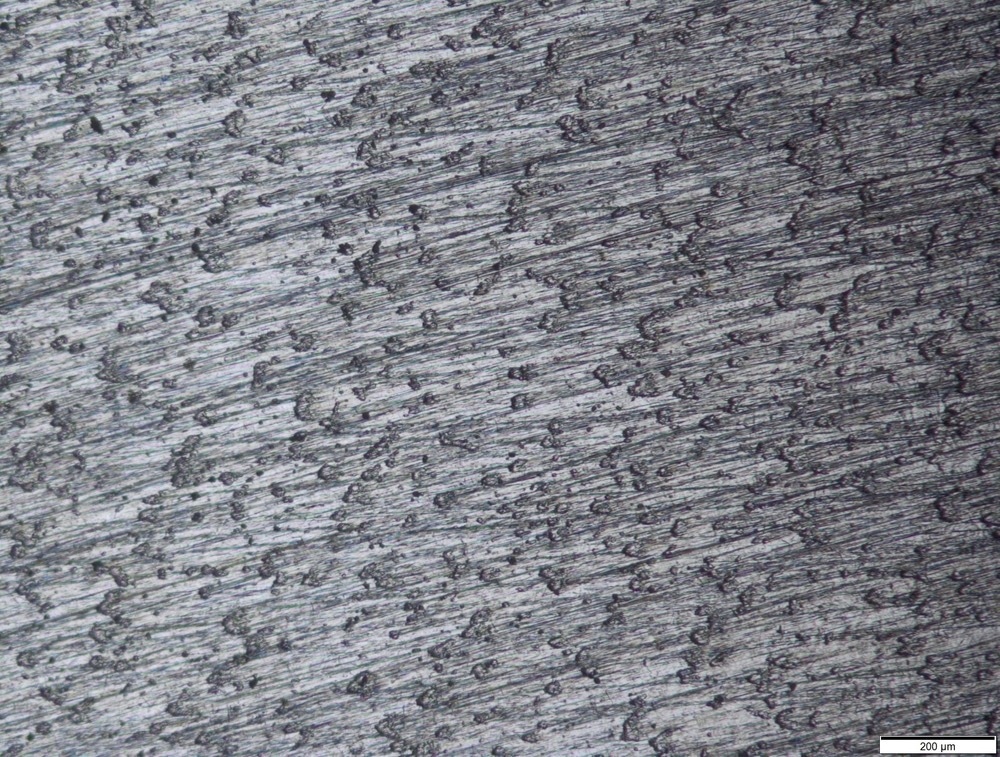
Image Credit: Maniock/Shutterstock.com
Historically, researchers in the field of mechanical sciences have identified the significance of surface contact between materials, which is dependent on mechanical properties. Over the years, several indentation tests have been developed, which have helped analyze the mechanical properties of surfaces. The recent development and advancements of sensors and actuators have enabled to study indentations at a nanoscale dimension, which is popularly referred to as nanoindentation.
Evolution and the Working Principle of Nanoindenters
Since the mid-1970s, nanoindentation has become the key method for measuring the mechanical properties of surfaces. The main component of a nanoindenter is a small probe that contains a calibrated indenter tip. An indenter tip is conventionally made of diamond, which comes with variable shapes, including flat, spherical, pyramidal, and wedged. Scientists select the optimal indenter tip based on the interrogated surface materials. Simply put, a nanoindenter provides force-displacement data.
Most conventional nanoindenters are load-controlled instruments, wherein the tip is brought in contact with the surface in the presence of a pre-defined load. Upon contact with the sample, the load gets increased and the tip indents into the material.
The material’s mechanical property is measured based on the contact area between the tip and sample, the applied force of nanoindenters, and the displacement depth. The main limitation of the conventional system is its inability to perform compression tests on small structures, such as micropillars, and 3D structures. However, the latest nanoindenters have successfully overcome this shortcoming.
The latest nanoindentation technology enables the measurement of the mechanical properties of varied surfaces, such as the modulus and hardness of materials of different sizes, shapes, and scales. Recent nanoindentation tests enable the characterization of a wide range of materials, including hard alloys and soft biomaterials. This technique is also used to analyze inorganic and organic samples.
Conventional and Advanced Applications of Nanoindenters
As stated above, the most common use of nanoindentation is for measuring mechanical properties, such as hardness, creep parameters, residual stresses, and elastic modulus, of a surface. These measurements have varied applications across physical science.
The advancements in nanoindentation tools, mainly acoustic emission detection, in situ and ex-situ imaging, and high-temperature testing, enabled a better understanding of nanoscale phenomena. This nanoscale analysis helps determine the nucleation defect and dynamics, phase transformations, and mechanical instabilities or strain localization. Nanoindenters test the depth and size of residual imprint to assess material hardness.
Nanoindenters are invaluable for microhardness testing, particularly when the sample is a thin, small, or non-homogenous complex material. Conventionally, nanoindenters have been mostly used in ceramics and glass, metal, and semiconductor industries.
Nanoindentation is also used in wood science and forest product research. It helps study wood cell wall layers, such as compound corner middle lamella and the S2 cell wall layer. Additionally, nanoindentation helps analyze wood-adhesive bondlines in laminated structures, and coatings on engineered wood products.
Recently, nanoindentation has also been used to characterize the mechanical properties of food materials. The microstructure of plant-based food materials (PBFM) mostly comprises clusters of irregular cellular compartments. The deformation, drying kinetics, and quality of PBFM are assessed by measuring its dynamically changing mechanical properties.
Recently, scientists used Hysitron TI-950 TriboIndenter to perform nanoindentation experiments to study different stages of drying of PBFM. Here, the relationship between micro-mechanical properties (e.g., hardness, elastic modulus, and stiffness) of PBFM and the moisture content during drying was established.
Another recent innovation is the development of a new ultra-high temperature nanoindentation system for testing up to 1100°C. This instrument can analyze both small- and large-scale indentation.
The Main Players and Emerging Manufacturers of Nanoindenters
Nanoindenters are manufactured across the globe, including North America, South America, Europe, Asia-Pacific, and the Middle East and Africa. Some of the key and emerging manufacturers of nanoindenters globally are Bruker, Alemnis, ZwickRoell, Fischer, Anton Paar, KLA and NanoTechnology Solutions, Keysight, and Micro Materials.
Recently, Bruker launched a new nanoindenter and scratcher, namely, the CETR-Apex system. This instrument includes atomic force microscopy, a 3D Profiler, and a High magnification optical microscope. It can be used to indent, i.e., measure hardness, Von Mises Stress and Young’s modulus, scratch (scratch-hardness), and measure wear and friction at the micro and nanoscale. Importantly, Apex has been designed to measure thin films, biofilms, hard coatings, microelectronics, solar cells, and magnetic and optical media.
Some of the latest nanoindenters manufactured by Fischer, such as HM2000 and HM500, have a stable and rigid construction that reduces the influence of vibrations and temperature fluctuations. Furthermore, these have high resolution that is ideal for routine testing. These instruments are suitable for both research and industrial applications.
Although the global nanoindenter market is currently moving haphazardly due to the coronavirus disease 2019 (COVID-19) pandemic, it has been predicted to grow more rapidly from 2023 to 2029. At present, small nanoindenter companies need appropriate research to survive the overpopulated business.
References and Further Reading
Dubosq, R. et al. (2023) Electron microscope loading and in situ nanoindentation of water ice at cryogenic temperatures. PLOS ONE, 18(2), e0281703. https://doi.org/10.1371/journal.pone.0281703
Nanoindentation. (2023) [Online] Available at: https://www.nanoscience.com/techniques/nanoindentation/
Global Nano Indenter (Nanoindenter) Market 2023-2030. [Online] Available at: https://mobilityforesights.com/product/nano-indenter-nanoindenter-market/
Jakes, J. E. and Stone, D. S. (2021) Best Practices for Quasistatic Berkovich Nanoindentation of Wood Cell Walls. Forests, 12(12), p.1696. doi.org/10.3390/f12121696
Khan, M. I. H. et al. (2021). Characterisation of mechanical properties of food materials during drying using nanoindentation. Journal of Food Engineering, 291, p.110306. doi.org/10.1016/j.jfoodeng.2020.110306
Minnert, C. et al. (2020) New ultra-high temperature nanoindentation system for operating at up to 1100 °C. Materials & Design, 192, p.108727. doi.org/10.1016/j.matdes.2020.108727
Schuh, C. A. (2006) Nanoindentation studies of materials. Materials Today, 9(5), pp. 32-40. doi.org/10.1016/S1369-7021(06)71495-X
Disclaimer: The views expressed here are those of the author expressed in their private capacity and do not necessarily represent the views of AZoM.com Limited T/A AZoNetwork the owner and operator of this website. This disclaimer forms part of the Terms and conditions of use of this website.