Nanoimprint Lithography (NIL) is an advanced nanofabrication technique that replicates nano-scale features with high resolution and cost-effectiveness.
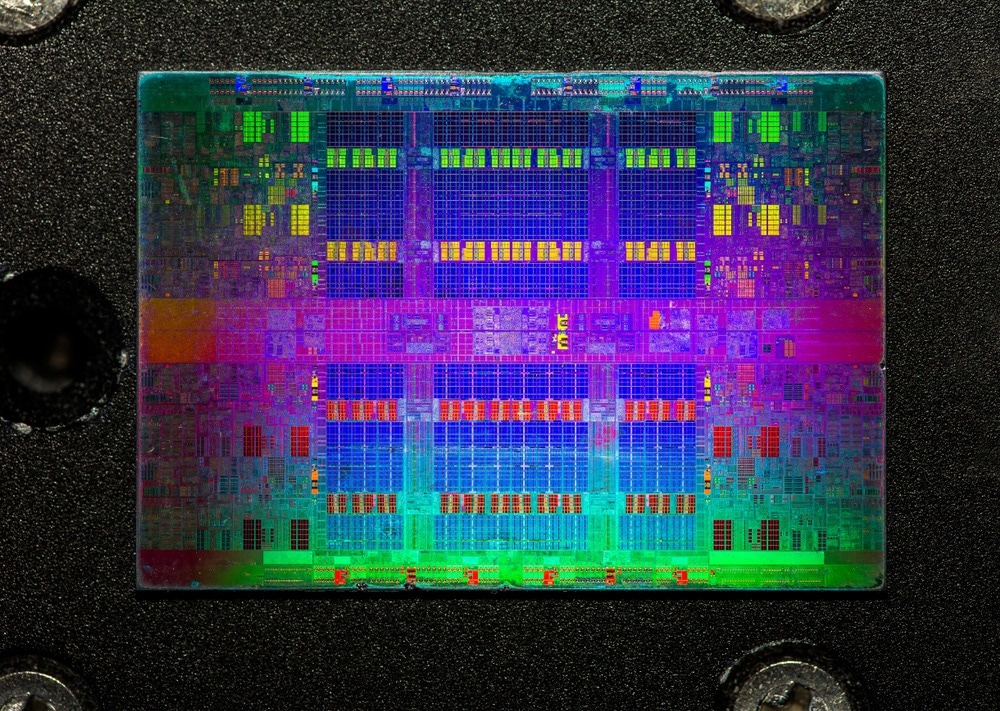
Image Credit: Ersan Uzunoglu/Shutterstock.com
Unlike traditional methods, NIL simplifies the process by eliminating complex optics, making it ideal for semiconductor memory applications with resolutions better than 10 nm. However, NIL faces challenges such as tight overlay requirements and pattern transfer issues, necessitating ongoing improvements in technology and process control.
What is Nanoimprint Lithography?
NIL is a pivotal technology in nanofabrication, significantly advancing the creation of intricate micro- and nano-scale patterns. Renowned for its high resolution, uniformity, and cost-effectiveness, NIL excels at replicating nano-scale features with minimal material waste. This method allows for creating detailed semiconductor patterns with a single mask, simplifying the process and reducing costs.1
Despite its advantages, NIL faces challenges in achieving tight overlay requirements for devices like Dynamic Random-Access Memory due to the need for precise alignment of multiple layers during fabrication to ensure optimal performance and avoid defects.2
Improvements are necessary to enhance overlay control, resolution, and pattern transfer. Ongoing advancements focus on optimizing imprint force, mask-to-wafer alignment, and pneumatic controls at the wafer edge.3
How Does Nanoimprint Lithography Work?
NIL involves creating nanoscale patterns on a substrate using a template or stamp. The process begins with the creation of a stamp or template, which can be configured in various formats such as plate-to-plate, roll-to-plate, or roll-to-roll.
The substrate is pretreated to reduce fill time and an imprint resist, typically a polymerizable material, is applied to form a composite coating.4 The stamp is subsequently brought into contact with the substrate, upon which pressure is exerted to facilitate the pattern transfer from the stamp onto the substrate.5
During the imprinting process, the resist material is cured, usually through thermal or UV methods, solidifying the pattern on the substrate.
Materials used in NIL include polymerizable compounds like glycerol-containing polyvinyl alcohol, which offer predictable results through simulation-based learning. NIL can create various patterns suitable for applications in fields such as plasmonics, superhydrophobicity, biomimetics, optics/datacom, and life sciences. These patterns can range from simple linear designs to complex three-dimensional structures, providing a versatile tool for advanced manufacturing and nanotechnology applications.
Through continuous advancements, NIL continues to enhance its capability to produce high-resolution, intricate patterns efficiently and cost-effectively.5,6
Advantages of Nanoimprint Lithography
NIL offers significant advantages, making it a valuable tool in nanofabrication. One key benefit is its high resolution, capable of producing features under 10 nm, which is essential for the miniaturization trends in advanced electronics.
Additionally, NIL is cost-effective due to its simple process and minimal material waste, making it an economically viable option for mass production. Its high throughput allows for rapid replication of intricate patterns, enhancing production efficiency.
In the electronics industry, NIL's ability to create precise and complex structures is crucial for developing advanced devices like semiconductor memory and microprocessors. This high-resolution capability ensures better performance and reliability in electronic components.
In biotechnology, NIL is beneficial for fabricating high-resolution lenses and sensors used in medical diagnostics and biological research. These applications require precise patterning to achieve accurate and reliable results.
NIL's low cost makes it accessible for developing economic single-molecule localization microscopy systems, which can enhance super-resolution imaging in biological studies. This accessibility helps overcome financial barriers, promoting wider adoption of advanced imaging techniques. Overall, NIL drives innovation in electronics and biotechnology by providing high-resolution, low-cost, high-throughput solutions.7,8
Disadvantages of Nanoimprint Lithography
While highly advantageous, NIL faces several significant challenges and limitations. One primary issue is the potential for defect formation during the imprinting process. These defects can arise from dust particles, stamp imperfections, or resist material inconsistencies. Such defects can lead to decreased fidelity and reliability of the patterned structures, which is particularly problematic for high-precision applications.
Another challenge is patterning uneven or non-planar surfaces. NIL relies on the stamp making uniform contact with the substrate, which is challenging when dealing with surfaces that are not perfectly flat. This limitation can result in incomplete or distorted patterns, affecting the overall quality and performance of the final product.
The implications of these disadvantages are significant in practical applications. For instance, in semiconductor manufacturing, defects and uneven patterns can compromise the performance of CMOS devices and transistors, leading to reduced yield and reliability.
These issues are particularly critical as the industry pushes towards smaller, more complex designs, where precision is paramount. Addressing these challenges is essential to fully realizing NIL's potential in advanced nanofabrication.
Advancements and Future Considerations
Ongoing research in NIL aims to address current limitations by enhancing performance in areas such as overlay accuracy, edge placement error (EPE), and defect reduction. Efforts include improving stability, addressing high-order distortion for overlay, and implementing advanced mask inspection methods to minimize defects. 9,10
Future advancements may involve developing new pattern transfer processes to tackle EPE, introducing design constraints specific to NIL for better process margins, and creating environmentally friendly, waste-reducing methods.11
These advancements could significantly expand NIL's application scope and efficiency, making it even more competitive in semiconductor memory applications, biomedical devices, flexible electronics, and beyond. For instance, NIL is being explored to produce biomimetic nanostructures for optics and life sciences, such as moth-eye antireflecting coatings for smart television displays.
NIL is also proposed for manufacturing nanoscale back-contact perovskite solar cells, which could outperform conventional designs by eliminating the need for transparent conductors.
In the future, NIL could support new technologies, including high-resolution drone components and advanced AI storage media with smaller bit grain sizes. NIL's ability to create three-dimensional QR codes could also be used to enhance product identification and security.
More from AZoNano: Enhancing TB Vaccines with Nanotechnology
References and Further Reading
[1]
|
Toshihiro, I., et al. (2022) Nanoimprint performance improvements for high volume semiconductor device manufacturing. Photomask Technology. doi.org/10.1117/12.2643212
|
[2]
|
Naoki, M., et al. (2023) Advances and applications in nanoimprint lithography. Novel Patterning Technologies. doi.org/10.1117/12.2658127
|
[3]
|
Mühlbergercit, M., (2022) Nanoimprint Lithography Technology and Applications. Nanomaterials. doi.org/10.3390/books978-3-0365-4481-6
|
[4]
|
Nakagawa, M., et al. (2022) Micro-print and nano-imprint methods combining laser-drilled screen printing and ultraviolet nanoimprint lithography: a review. Japanese Journal of Applied Physics. doi.org/10.35848/1347-4065/ac575f
|
[5]
|
Hirai, Y., et al. (2022) Smart Systems for Material and Process Designing in Direct Nanoimprint Lithography Using Hybrid Deep Learning. Nanomaterials. doi.org/10.3390/nano12152571
|
[6]
|
Yang, Y., et al. (2019) Using Nanoimprint Lithography to Create Robust, Buoyant, Superhydrophobic PVB/SiO2 Coatings on wood Surfaces Inspired by Red roses petal. Scientific Reports. doi.org/10.1038/s41598-019-46337-y
|
[7]
|
Christopher, A., et al. (2023) UV-Nanoimprint and Deep Reactive Ion Etching of High Efficiency Silicon Metalenses: High Throughput at Low Cost with Excellent Resolution and Repeatability. Nanomaterials. doi.org/10.3390/nano13030436
|
[8]
|
Andrea, G., et al. (2023) Low-Cost Hyperspectral Imaging to Detect Drought Stress in High-Throughput Phenotyping. Plants. doi.org/10.3390/plants12081730
|
[9]
|
Chawla, JS., et al. (2014) Patterning challenges in the fabrication of 12 nm half-pitch dual damascene copper ultra low-k interconnects. Advanced Etch Technology for Nanopatterning. doi.org/10.1117/12.2048599
|
[10]
|
Naoto, H., et al. (2022) Patterning challenges and opportunities in nanosheet device architectures. Advanced Etch Technology and Process Integration for Nanopatterning XI. doi.org/10.1117/12.2615984
|
[11]
|
Makoto, O., et al. (2023) Nanoimprint post processing techniques to address edge placement error. Novel Patterning Technologies. doi.org/10.1117/12.2658125
|
Disclaimer: The views expressed here are those of the author expressed in their private capacity and do not necessarily represent the views of AZoM.com Limited T/A AZoNetwork the owner and operator of this website. This disclaimer forms part of the Terms and conditions of use of this website.