Sponsored by InovensoReviewed by Louis CastelNov 4 2024
Daily consumables in the average man’s life largely go unnoticed by users surrounding the nature of the product. This includes food (ice cream), cosmetics (lotions), paints, and more. The same concept of formation or production, known as “emulsification,” is enacted to create these products, and the product formed is emulsion.1
These emulsions combine two immiscible liquids where one is lured with a mechanical shear as a droplet within the other, making a semi-stable mixture. The most well-known forms of emulsion units are oil and water.
If an emulsion is left alone, it may lead to phase separation of the two immiscible liquids. This can be avoided by utilizing emulsifiers or stabilizers—agents that form an interface between the two liquids by bonding or keeping them together.
Combining emulsions with electrospinning, where a charged solution is ejected using high voltage to create ultrafine fibers on a substrate,2 brings nano and microfiber technology into a new era. This process enables the development of advanced materials for various applications, including biomedical, filtration, energy generation/storage, and more.
Some key factors in emulsion electrospinning, including product characteristics, material considerations, parameters, and future, are currently being discussed.
Mechanism and Product Features
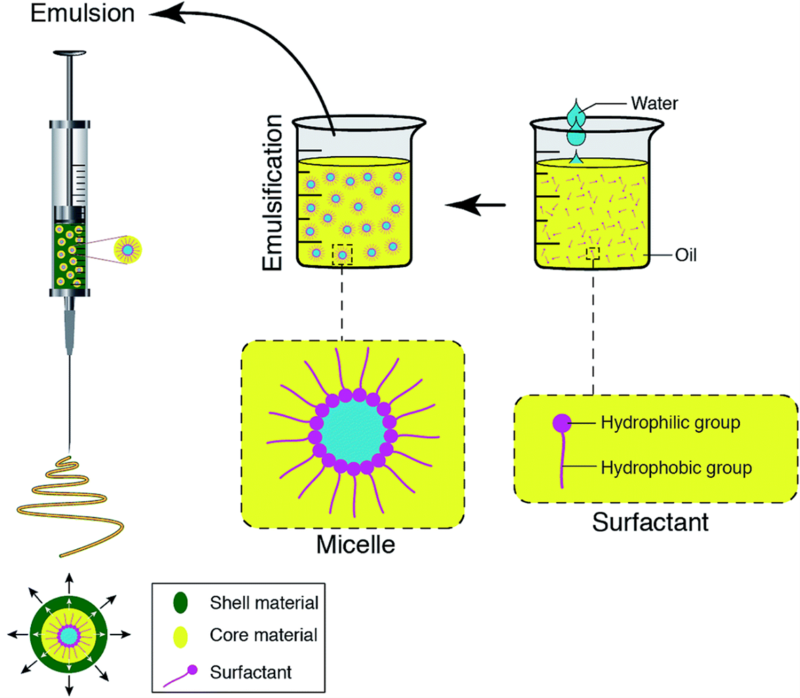
Figure 1. Emulsion electrospinning scheme. Image Credit: Nikmaram, N., et al. (2017)
When two immiscible liquids are exposed to one another, like water in oil, and supported by a surfactant, which has a hydrophilic or water-loving group that stays/likes water and a hydrophobic or water-repelling or disliking group, the water and oil molecules will orient themselves around this surfactant (Fig. 1).
Minute particles or micelles will form with water on the inner part of the micelle, behaving as the structure’s core, and brushes protruding outside enable the micelle to stay intact and afloat in the oil.
Emulsions can be electrospun via at least two approaches. 1) Utilizing a single spinneret, an emulsion solution is electrospun as the emulsion constituents in the emulsion structure are reorganized, forming a core-shell structure as in the coaxial method. 2) Several spinnerets can be utilized where the emulsion structure permits reorientation in a core-shell fiber structure, leading to a higher production rate.
These approaches for stabilizing particles in a solution are used in research to entrap numerous molecules for use cases, including drug delivery.2
Defined Parameters
General electrospinning processes and associated parameters must be understood and accounted for to obtain successful fiber/emulsion formation. These parameters are crucial for deciding the mode(s) of electrospinning operation and the type of product formed. Some of these parameters are described below:
Table 1. General parameters considered for the electrospinning process. Source: Sharma, G.K. and James, N.R. (2022); Haider, A., Haider, S. and Kang, I.-K. (2018)
General parameters |
Individual parameters |
Keywords |
Electrospinning |
Applied Voltage (in kilovolts) |
Ease of jet formation and polymer stretching due to charge repulsion within polymer |
Distance between collector and needle, and needle diameter |
Affects morphology of fibers, deposition time, evaporation rate, whipping interval etc. |
Flow rate |
Affects morphology of fibers, balance needed between incoming solution and outgoing via jets i.e., stable Taylor cone formation |
Solution |
Solvent type |
Affects the rate of evaporation and material solubility, high evaporation cause problems such as clogging on the needle tip. |
Polymer concentration |
Affects stretching of charged jet, low concentration could lead to fiber fragmentation before reaching collector |
Viscosity |
Flow of solution through the needle tip, defected fibers/clogging issues |
Solution conductivity |
Control of Taylor cone formation and fiber diameter-no/low conductivity means no/low electrospinning-can be improved by adding salt |
Environment |
Humidity |
Fiber diameter and morphology control due to jet solidification process, porous fiber formation, and lower sized diameter with increase in humidity possible |
Temperature |
Rate of solvent evaporation, solution flow rate, fiber production |
Typical categories of electrospinning include needle-based (single, coaxial, triaxial, multi-channel) systems, needle-free systems with free surfaces by companies like ELMARCO, and the open surface and hybrid technology of INOVENSO Ltd. Other modes of electrospinning are melt and emulsion and, most commonly, solution electrospinning.
The parameters described above apply to every type of technology and should be maximized according to the machine scale, production rate, and other machine-related and electrospinning parameters.
Electrospraying
In addition to electrospinning, enhancing parameters like viscosity and applied voltage disrupt the Taylor cone and lead to highly charged droplets, which may be improved to form micro- or nano-sized particles.
This process is known as electrospraying and may be utilized for various applications like incorporating other molecules inside the core and in the shell, such as in drugs for drug delivery systems, and including other functional materials like peptides, proteins, enzymes, etc.5,6
Applications
Electrospinning is an evolving approach, and further use cases may emerge over time. There are several current applications for emulsion electrospinning, which include but are not limited to:
Food Industries
Among multiple applications, emulsions electrospinning shows potential in the encapsulation of functional components and controlled release of bioactive components (antioxidants, vitamins, flavonoids, fatty acids, etc.) for improving health, immobilizing enzymes, and packaging food.7
Drug Delivery
Utilizing biodegradable polymers is preferable for materials employed in physiological conditions, which suggests the significance of degradation and the controlled release of drugs from inside these polymeric structures—emulsion shell structure is critical here.
Emulsion electrospinning permits sustained release of biomolecules compared to coaxial spinning and, in other cases, bioavailability compared to blended spun fibers. Some critical drugs that have been explored with emulsion electrospinning include anticancer (doxorubicin, paclitaxel, etc.), anti-inflammatory (ketoprofen, etc.), and antibiotics (vancomycin, etc.).8
Other Biomedical/Pharmaceutical Applications
Emulsion electrospinning is extremely helpful for delivering susceptible molecules that may sustain the bioactivity of biomolecules like proteins, enzymes, neuronal stimulating cells, etc.
Other use cases include the development of vascular grafts via peptide and growth factor release and delivery of biomolecules like heparin, VEGF, bFGF, and collagen for use cases like cardiac, tissue, and bone engineering use cases like bone repair and tendon repair.8.9
Advantages and Current Challenges
Electrospun fibers have several benefits, including tunable fiber diameters, porosity, surface-to-volume ratio, morphology, and mechanical characteristics.
Compared to coaxial spinning strategies, the formation of core-shell structures in emulsion electrospinning is plausible even with a single nozzle. Utilizing the approach of electrospraying can also enable the thin film to coat emulsions.10
Despite the benefits, limitations like low throughput can pose challenges, yet they can be addressed through system changes, e.g., multiple needle setup.
Pharmaceutical and biomedical use cases face challenges such as finding compatibility within the core-shell materials, leaching out of entrapped molecules like drugs, and penetrating physiological fluids upon exposure to a biological medium. It is possible to address issues linked to leaching by crosslinking molecules like glutaraldehyde and chlorine dioxide on the formed fibers.
References and Further Reading
- Kale, S.N. and Deore, S.L. (2016). Emulsion Micro Emulsion and Nano Emulsion: A Review. Systematic Reviews in Pharmacy, [online] 8(1), pp.39–47. https://doi.org/10.5530/srp.2017.1.8.
- Nikmaram, N., et al. (2017). Emulsion-based systems for fabrication of electrospun nanofibers: food, pharmaceutical and biomedical applications. RSC Advances, 7(46), pp.28951–28964. https://doi.org/10.1039/c7ra00179g.
- Sharma, G.K. and James, N.R. (2022). Electrospinning: The Technique and Applications. [online] www.intechopen.com. Available at: https://www.intechopen.com/chapters/83223.
- Haider, A., Haider, S. and Kang, I.-K. (2018). A comprehensive review summarizing the effect of electrospinning parameters and potential applications of nanofibers in biomedical and biotechnology. Arabian Journal of Chemistry, [online] 11(8), pp.1165–1188. https://doi.org/10.1016/j.arabjc.2015.11.015.
- Rostamabadi, H., et al. (2021). Electrospraying as a novel process for the synthesis of particles/nanoparticles loaded with poorly water-soluble bioactive molecules. Advances in Colloid and Interface Science, 290, p.102384. https://doi.org/10.1016/j.cis.2021.102384.
- Tanhaei, A., et al. (2021). Electrospraying as a novel method of particle engineering for drug delivery vehicles. Journal of Controlled Release, 330, pp.851–865. https://doi.org/10.1016/j.jconrel.2020.10.059.
- Zhang, C., Feng, F. and Zhang, H. (2018). Emulsion electrospinning: Fundamentals, food applications and prospects. Trends in Food Science & Technology, 80, pp.175–186. https://doi.org/10.1016/j.tifs.2018.08.005.
- Matej Buzgo, et al. (2018). Blend electrospinning, coaxial electrospinning, and emulsion electrospinning techniques. Elsevier eBooks, pp.325–347. https://doi.org/10.1016/b978-0-08-102198-9.00011-9.
- McClellan, P. and Landis, W.J. (2016). Recent Applications of Coaxial and Emulsion Electrospinning Methods in the Field of Tissue Engineering. BioResearch Open Access, 5(1), pp.212–227. https://doi.org/10.1089/biores.2016.0022.
- Khan, M.K.I., et al. (2013). Electrospraying of water in oil emulsions for thin film coating. Journal of Food Engineering, [online] 119(4), pp.776–780. https://doi.org/10.1016/j.jfoodeng.2013.05.027.
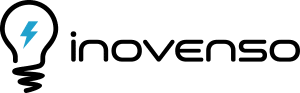
This information has been sourced, reviewed, and adapted from materials provided by Inovenso.
For more information on this source, please visit Inovenso.