In a study published recently in the journal nanomaterials, a new composite capacitance pressure sensor was produced by hybridizing zinc oxide nanoparticles into a permeable polydimethylsiloxane dielectric material.
Study: Porous Polydimethylsiloxane Elastomer Hybrid with Zinc Oxide Nanowire for Wearable, Wide-Range, and Low Detection Limit Capacitive Pressure Sensor. Image Credit: Andrew Berezovsky/Shutterstock.com
Polymer-based Nanomaterials
With rapid growth for portable healthcare equipment and human-machine interfaces, researchers have shifted their focus to polymer nanocomposites which utilize adaptable polymeric materials in tandem with sensory perceptions nanoparticles. These components have received great interest in their ability to sense climate, humidity, illumination, and contact fluctuations.
Polymer-based nanomaterials, as opposed to traditional hybrids or a single kind of element, can provide significant improvements in heat, electromagnetic, visual, biochemical, and mechanical characteristics.
Many different types of nanoparticles with high conductivity, insulating, or stress-sensitive qualities have been investigated for use as adaptable sensing elements due to their prospects in elevating stress/strain detection sensitivity for applications such as human movement identification, clinical documentation, and electronic parts.
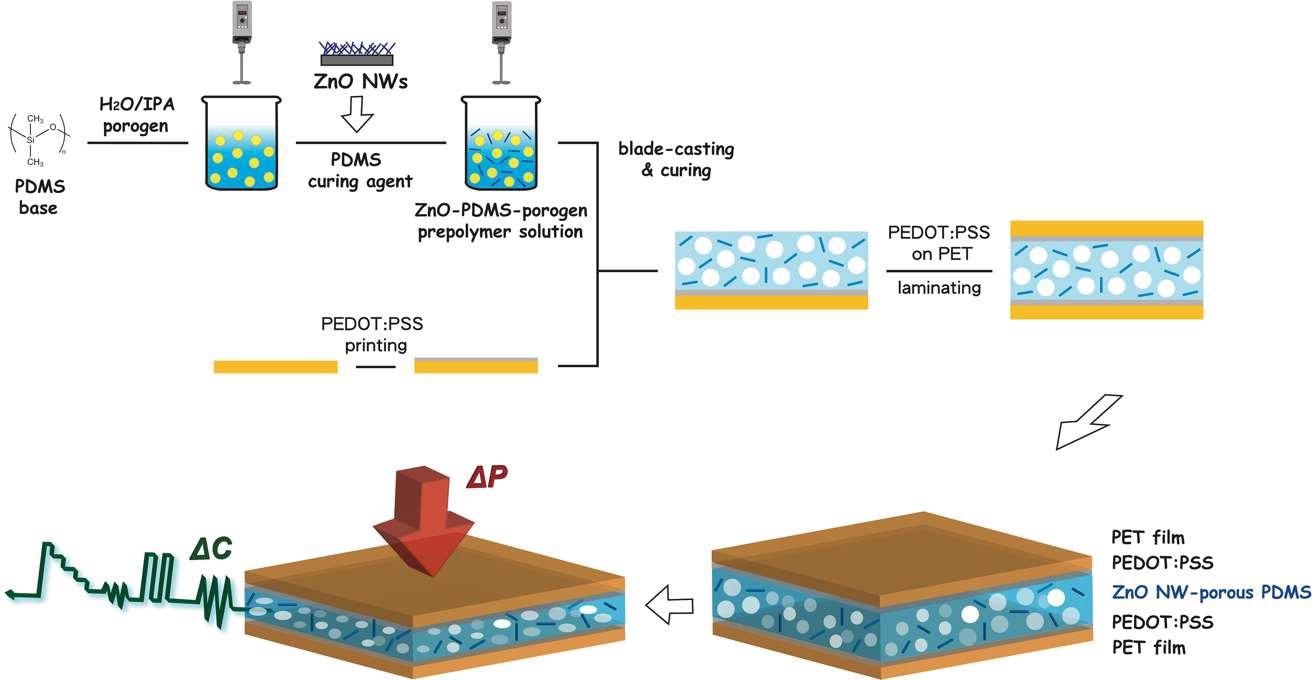
Figure 1. Schematic illustration for fabricating a porous polydimethylsiloxane-based nanocomposite dielectric film hybrid with zinc oxide nanowire for the formation of flexible capacitive pressure sensors. © Wen, G. et al. (2022)
Capacitive Proximity Detection
As a result of its straightforward design, low power, and superior energy resilience, capacitive proximity detection has recently obtained a great deal of attention.
The sensitivity of a basic superconductor is often modified as a consequence of the exterior pressure applied to the capacitors.
For inductive sensing elements, elastomeric polydimethylsiloxane (PDMS)-based silicone rubbers have been used as the dielectric substrate because of its greater freedom, environmental friendliness, and cheap availability of equipment compared to other materials.
Due to the limitations imposed by its viscoelastic nature and limited ductility, such PDMS sheets are unable to create sufficient compression even when subjected to very reduced pressure. Furthermore, after stress offloading, their healing process for returning to the starting state is relatively long.
To address these constraints, incorporating mini nanostructures or holes into a viscoelastic substrate has been proposed as a potential method of improving sensing capability.
With force applied, these incorporated leakages or holes in the twisted PDMS films may cause enormous cubic distortion and increases in inefficient dielectric properties, enhancing the inductance variation and stress responsiveness of the device being studied.
Such improvements, nevertheless, can only be obtained in the minimal domain.
Other drawbacks include sophisticated, expensive, and hard to regulate production methods for these elastic sensing elements, making them unsuitable for use in human sensory interfaces.
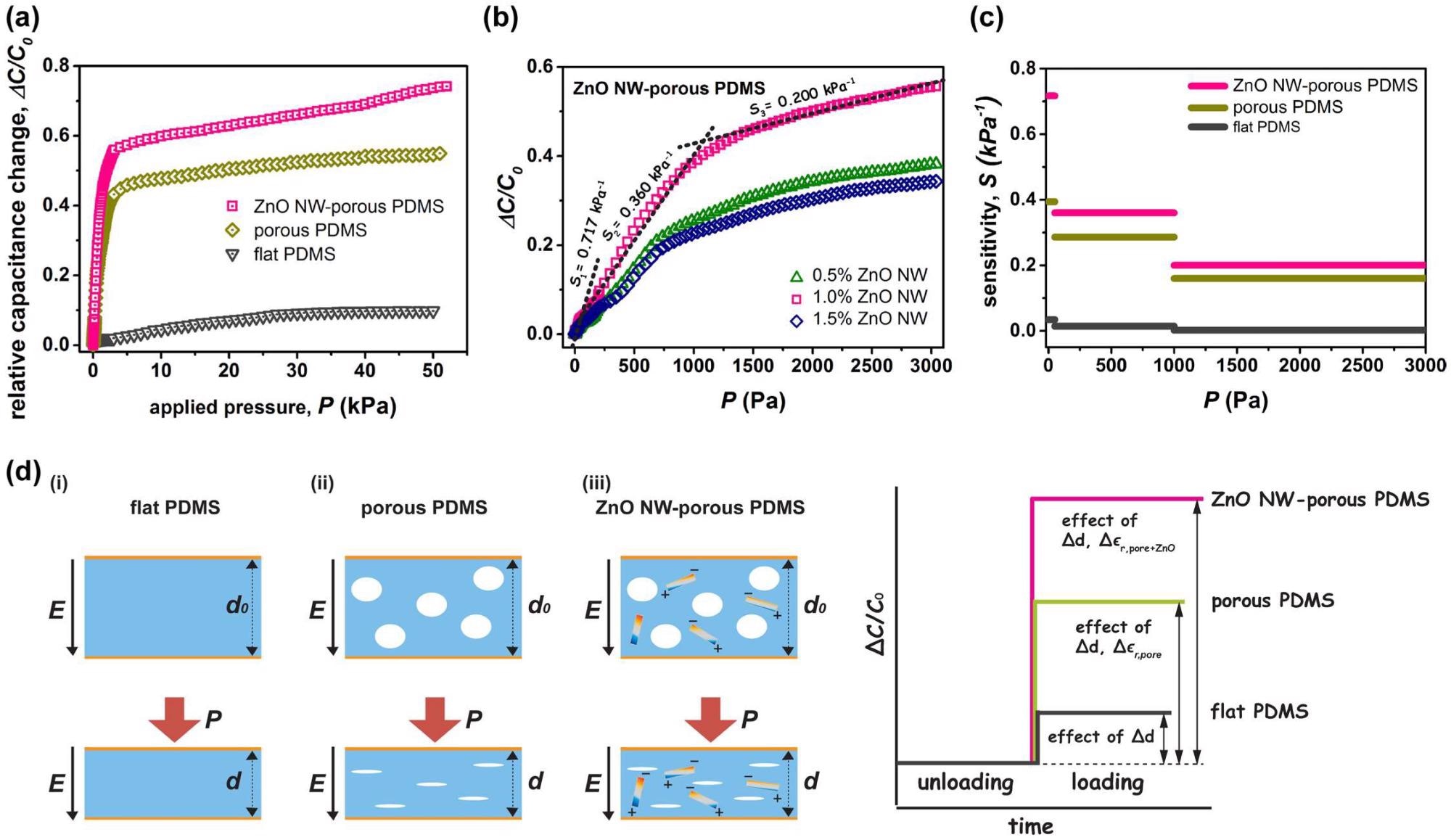
Figure 2. (a) Measured relative capacitance change (ΔC/C0) as a function of the applied pressure (P) for the capacitive pressure sensors with different types of dielectric layers: flat PDMS, porous PDMS, and ZnO nanowire–porous PDMS (sensing area: 10 mm × 10 mm). (b) Pressure-response plots for these nanocomposite sensors with varying ZnO nanowire loading. (c) Comparison of the sensitivity of capacitive pressure sensors at different applied pressure ranges. (d) Proposed sensing mechanisms with graphical capacitance change for the capacitors containing (i) flat PDMS, (ii) porous PDMS, and (iii) ZnO nanowire–porous PDMS. © Wen, G. et al. (2022)
A Novel Nanocomposite Piezoelectric Medium
A unique nanocomposite piezoelectric medium in which a one-dimensional ZnO nanoparticle is integrated into a porous elastomeric polymer to generate adjustable sensitive devices is presented.
ZnO nanoparticle is a one-of-a-kind elevated, hygienic, and low-cost substance with various semiconductors, capacitive, and pyroelectric characteristics that can be readily distributed in liquid solution and polymer matrices.
A porogen-assisted technique was used to create permeable polydimethylsiloxane (PDMS)-based composites with controlled permeability, and ZnO nanowires are randomly dispersed in PDMS.
By increasing the interlayer polarisation and percentage of elongation of the composites, a substantial shift in dielectric properties combining huge fluctuations in inductance may be produced upon exterior pressure.
When compared to simple PDMS instruments, the observed pressure responsiveness of the manufactured capacitive sensing element improved by more than 21%.
The nanofiber dielectric layer also demonstrated excellent resilience and endurance after 4000 loading-unloading rounds, as well as a broad detection limit, indicating a high possibility for the recognition of diverse human feelings.
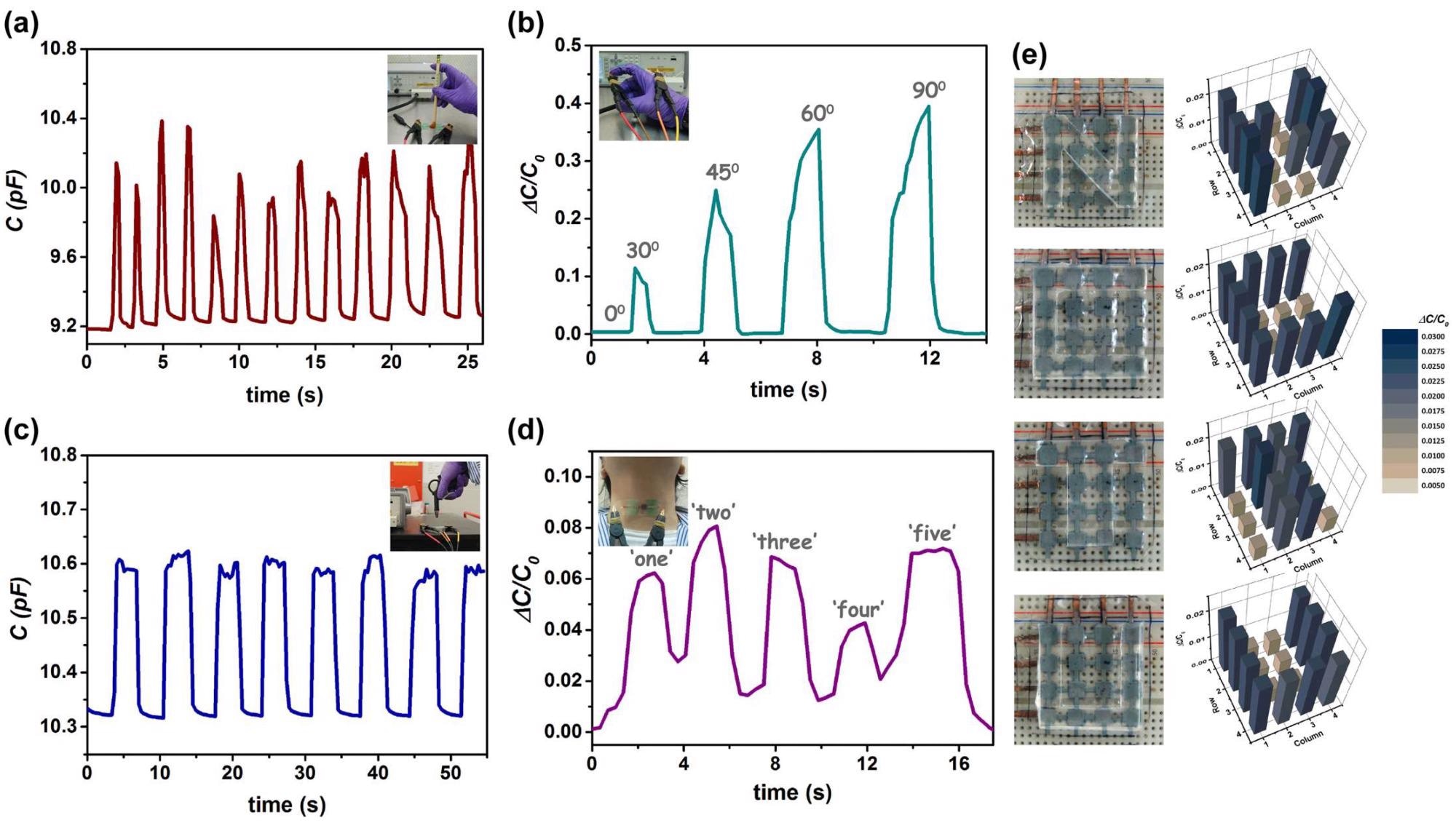
Figure 3. Real-time capacitance variations of the sensor in response to (a) calligraphy writing, (b) index finger straightening and bending, (c) air streaming, and (d) vocal speaking. (e) Photographs of a working pressure sensor array and their spatial pressure responses to the letters N, C, T, and U. © Wen, G. et al. (2022)
Concluding Remarks
To summarise, a new composite capacitance pressure transducer was produced by hybridizing zinc oxide nanoparticles into a permeable polydimethylsiloxane dielectric material.
The maximum sensitivity of the sensing device was 0.717 kPa at a nuanced operating pressure and 0.200 kPa at moderate operating pressure.
Moreover, exact tests demonstrated that this nanoparticle permeable pressure gauge was sensitive enough to detect finger flexing, handwriting, voice-induced shaking, air blowing, hydraulic submerged force, and item spatial distribution.
The findings suggest that elastic nanofiber viscoelastic nanomaterials might be employed in conductive strain gauges for a spectrum of uses, including healthcare monitoring and skin-like devices.
Continue reading: Integrating Nanotechnology into the Internet of Things.
Reference
Wen, G. et al. (2022). Porous Polydimethylsiloxane Elastomer Hybrid with Zinc Oxide Nanowire for Wearable, Wide-Range, and Low Detection Limit Capacitive Pressure Sensor. Nanomaterials. Available at: https://www.mdpi.com/2079-4991/12/2/256
Disclaimer: The views expressed here are those of the author expressed in their private capacity and do not necessarily represent the views of AZoM.com Limited T/A AZoNetwork the owner and operator of this website. This disclaimer forms part of the Terms and conditions of use of this website.