A pre-proof published recently in the journal Carbon investigates shifts in fiber morphologies, particularly inter- and intra-bundle voids, as a result of solution spinning. This thorough examination of fiber creation, according to the authors, offers valuable information regarding the synthesis of high-performance multipurpose carbon nanotube (CNT) fibers.
Study: Fiber Optic Sensors for Detection of Sodium Plating in Sodium-Ion Batteries. Image Credit: Yurchanka Siarhei/Shutterstock.com
What Makes Carbon Nanotubes Stand Out?
Carbon nanotubes (CNTs) have great appeal due to potential usage in sensing, actuation, military hardware, robotic systems, and energy storage equipment due to their unique mix of features. These include exceptional electrical, mechanical, and thermal capabilities. Owing to their excellent elasticity and low densities, CNTs are predicted to emerge as a next-generation fiber of choice.
While several efforts have helped recognize the characteristics of isolated CNTs as the characteristics of the bulk fiber, their macroscopic qualities are dependent on the type, quality and interconnection of CNT bundles.
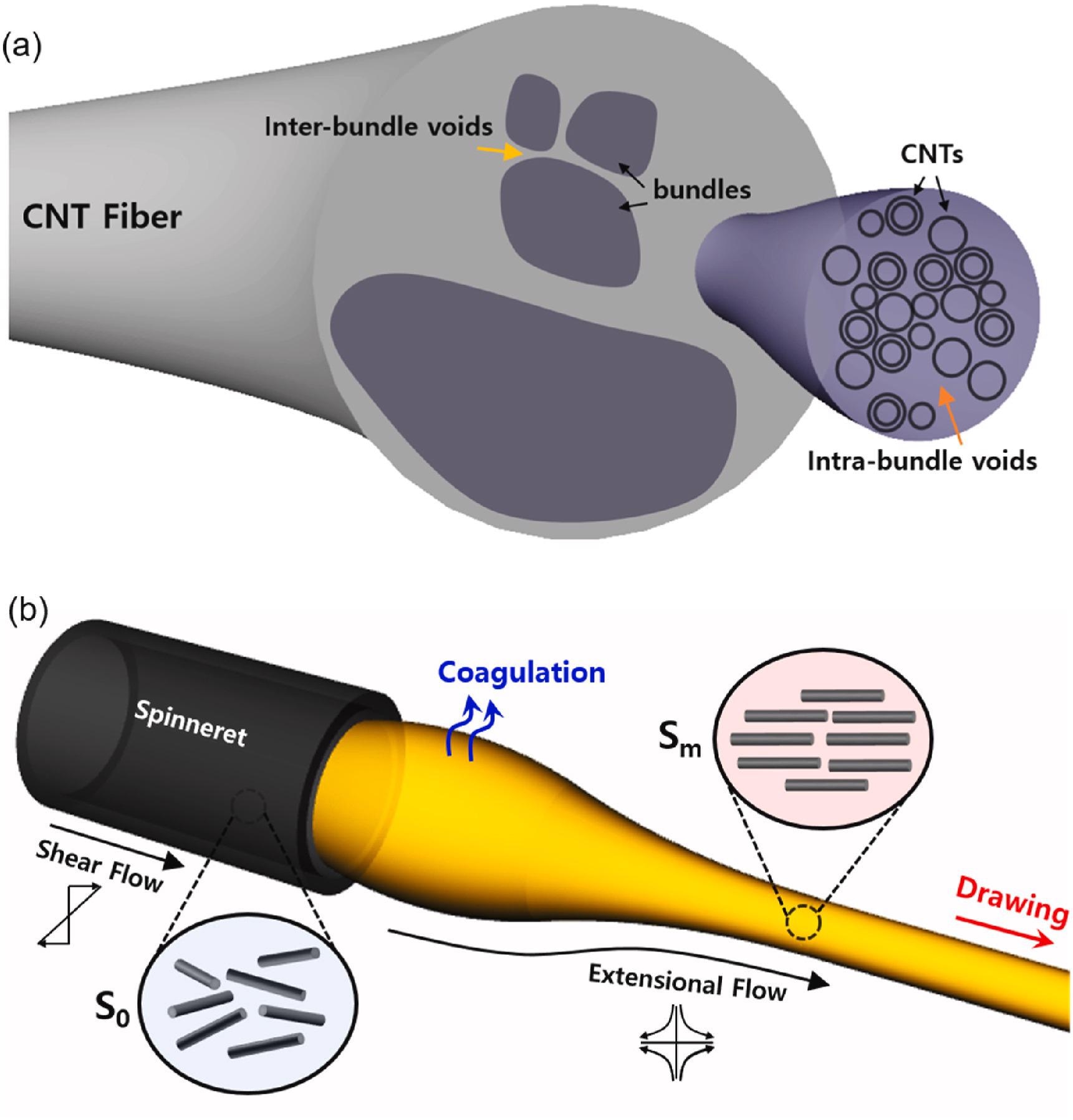
Figure 1. Schematic illustrations of (a) hierarchical structure of CNT fiber and (b) unit operations for solution spinning. (A color version of this figure can be viewed online.)
Inter-Tube Interactivity is Critical for High-Performance Carbon Nanotubes
Optimizing the interactivity of neighboring carbon nanotubes is essential for high-performance carbon nanotube fibers from the perspective of micromechanics.
From a materials viewpoint, carbon nanotube features including aspect ratio (L/d, where L represents length and d represents the diameter of the carbon nanotube) and purity may boost inter-tube connection in the fiber, leading to a considerable link with fiber characteristics.
Greater purity may reduce the influence of remnant contaminants with tube alignment and inter-tube interactivity. Moreover, the significance of the aspect ratio for fiber characteristics has often been noted.
Mechanically, inter-tube friction is a crucial element in defining the carbon nanotube fiber's tensile strength, and a larger aspect ratio creates a stronger friction force at the carbon nanotube interfaces. The fabrication or refinement procedures significantly influence the quality and type of CNTs.
Direct Spinning Vs. Solution Spinning – Which Synthesis Method is Better?
Direct spinning and solution spinning are two widely recognized ways of producing high-performance carbon nanotube fiber.
CNT fibers and sheets formed by direct spinning have excellent tensile strength and fairly long component nanotubes (∼1 mm) but have limited electric conductance due to low alignment and packaging density.
Fibers produced by solution spinning, on the other hand, comprise comparatively shorter nanotubes (∼12 μm) but possess great tensile strength and electric conductance.
To enhance macroscopic features of carbon nanotube fibers such as fiber orientation and packaging, pre- and post-treatment of the nanotube fibers are some of the strategies reported.
The solution spinning method is a continuous complicated process wherein the liquid crystal (LC) solution flows inside the spinneret while coagulation and extensional deformation take place outside the spinneret.
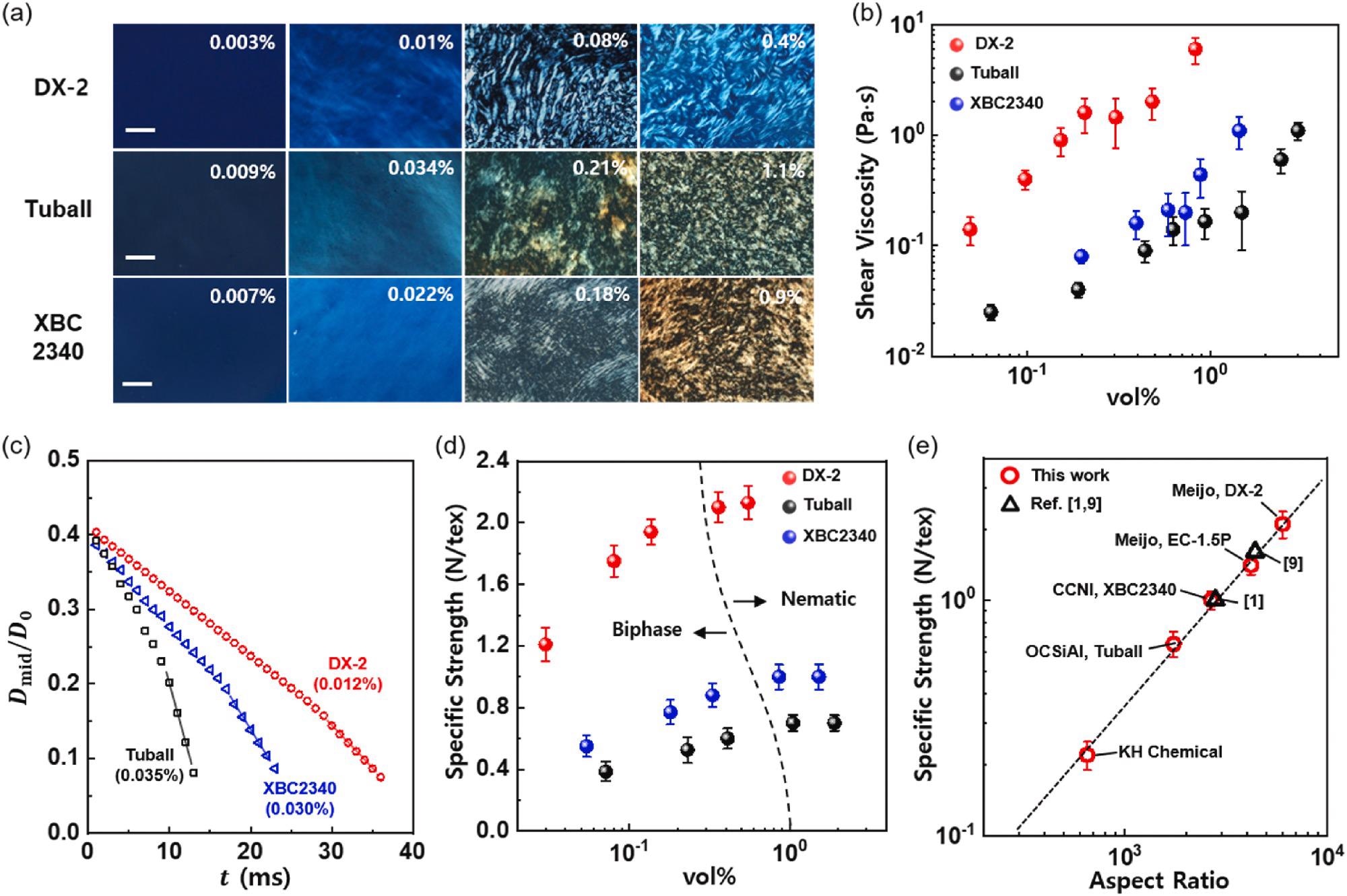
Figure 2. Rheological properties of LC dopes and aspect ratio of CNTs. (a) Polarized microscopy images for DX-2, Tuball, and XBC2340 depending on the concentration. Scale bars are 100 μm. (b) Phase transition concentration from biphase to nematic phase determined from the steady shear viscosity at 52 s−1. (c) The diameter evolution with time by the dripping-onto-substrate rheometry for DX-2 (0.012 vol%), Tuball (0.035 vol%), and XBC2340 (0.03 vol%) solutions. The extensional viscosity was extracted through the linear fits of capillary thinning curves. (d) The specific strength of CNT (DX-2) fibers as a function of the concentration. (e) Dependence of aspect ratio on the specific strength of CNT fibers. (A color version of this figure can be viewed online.)
Improving the Fiber Properties of Carbon Nanotubes
There are many structural ways of improving the characteristics of carbon nanotube fibers. CNT fiber has a hierarchal structure, with multiple nanotubes forming a bundle and numerous bundles forming the CNT fiber.
As a result, CNT fibers possess multiple voids and flaws on the inter- and intra-bundle interfaces that are created in fiber synthesis. The macroscopic characteristics of the resulting fiber are strongly reliant on the number and size of existing defects.
As a result, it is critical to optimize packaging density by reducing voids and defects in carbon nanotube fibers. Optimizing fiber alignment may also be a viable approach used to increase inter-tube interactions by lowering the number of voids in the fiber.
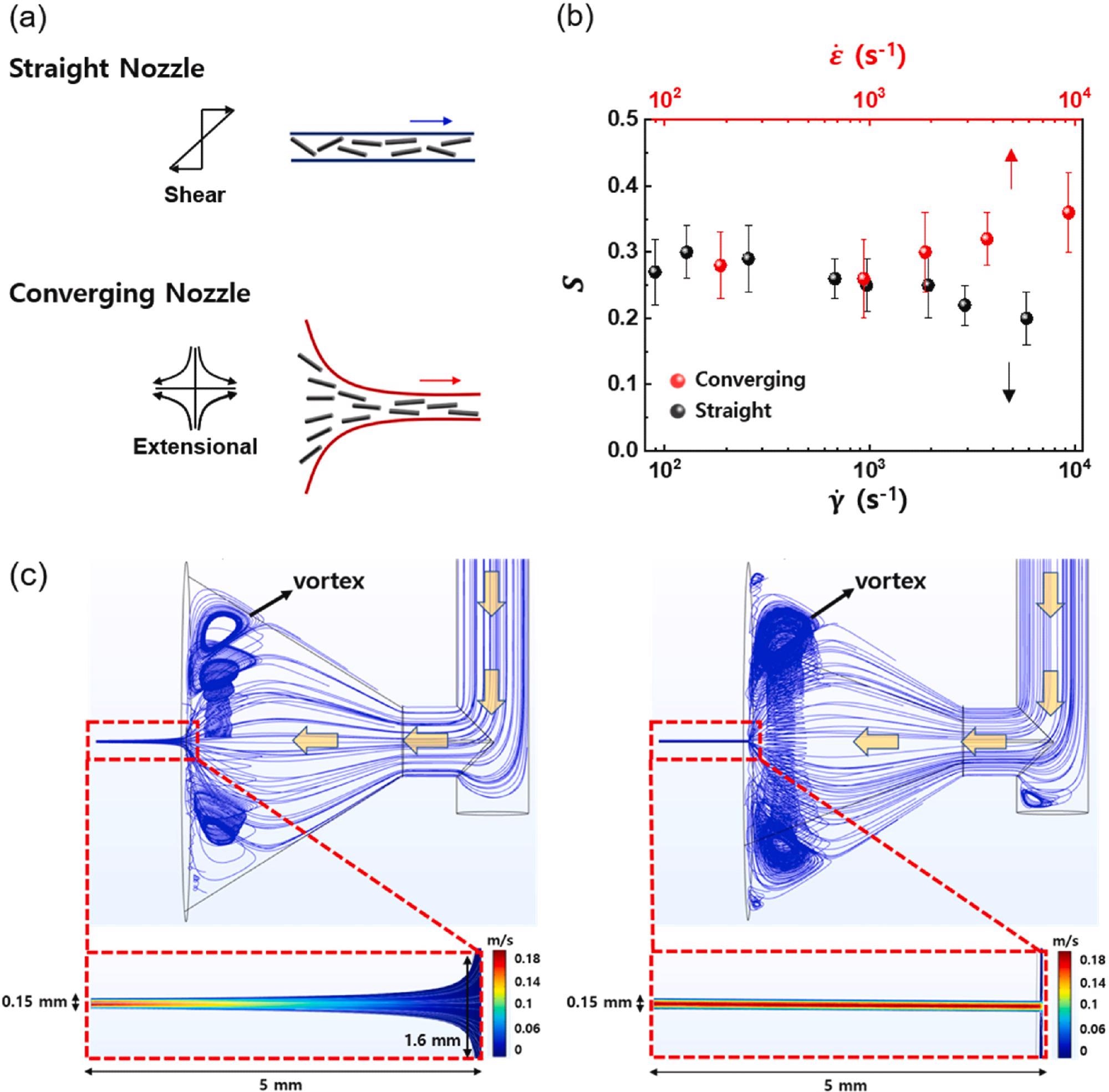
Figure 3. Flow fields depending on the nozzle design. (a) Schematic illustration of flow fields for LC dope in straight and converging nozzles. (b) Changes in initial orientation factor (S0) by shear and extension rates. The experiments were performed with an nematic LC solution (DX-2, 0.43 vol%). (c) Flow patterns in the converging nozzle and straight nozzle by Comsol Multiphysics. (A color version of this figure can be viewed online.)
Highlights of the Study
In this study, the researchers investigated the development of the structural alignment and interior voids of CNT fibers for every unit process of solution spinning, relating them to the macroscopic fiber characteristics.
To acquire the best fiber qualities, the precise ϕnematic must be determined while the liquid crystal solution is spun, and thereafter the spinning operation must be performed above that ϕnematic.
It was discovered that optimizing the alignment significantly reduced the intra-bundle and inter-bundle voids in the fiber microstructure. During solidification, a large aspect ratio, higher concentration, and smaller D values enabled the fabrication of fibers with circular cross-sections, further minimizing the interior voids in the fiber.
There was a significant link observed between intra-fiber voids and the fiber's macroscopic characteristics. The tensile modulus and electric conductance of the carbon nanotube fiber were enhanced by increasing the packaging density, with the finished version comprising a minimal number of void defects (0.08 vol%).
The fiber demonstrated outstanding tensile strength, heat conduction, and knot efficiency, showing its viability for usage as a multipurpose fiber that outperforms traditional carbon fibers.
Disclaimer: The views expressed here are those of the author expressed in their private capacity and do not necessarily represent the views of AZoM.com Limited T/A AZoNetwork the owner and operator of this website. This disclaimer forms part of the Terms and conditions of use of this website.
Source:
Kim, S. G., Choi, G. M. et al. (2022). Hierarchical structure control in solution spinning for strong and multifunctional carbon nanotube fibers. Carbon. Available at: https://www.sciencedirect.com/science/article/pii/S0008622322003189?via%3Dihub