Research institutions across the globe are looking for ways to redefine the development of high-quality graphene sheets. This can be achieved by reducing graphene oxide (GO) to produce reduced graphene oxide (rGO).
While this method is cost effective, it affects the quality of the graphene sheets, which when used with certain techniques exhibit properties that are lower than the hypothetical potential of pristine graphene in comparison to other techniques like mechanical exfoliation. However, there is a significant scope to improve and use the rGO effectively.
Graphene Oxide to Reduced Graphene Oxide
The exact process parameters used when reducing GO into rGO play a major role in the quality of the material, affecting how close a structure to perfect graphene is achieved.
If graphene is going to be adopted for large-scale applications such as energy storage, reduced graphene oxide could provide a suitable solution, since it is easier to manufacture in large quantities than perfect single-layer or few-layer graphene, and the quality will be sufficient for these bulk material applications.
The reduction of graphene oxide can be achieved a number of ways - through thermal, chemical, or electrochemical methods. The methods which are capable of producing the highest quality graphene tend to be more complex.
Some reported examples of graphene oxide reduction include:
- treating graphene oxide with hydrazine hydrate at 100°C for 24 hours
- exposure to hydrogen plasma for several seconds
- exposure to powerful pulsed light from xenon flashtubes
- heating the graphene oxide with urea as an expansion-reduction agent
- direct heating of graphene oxide in a furnace to very high temperatures
Using chemical reduction to reduce GO is a scalable technique; however, the rGO produced by this method often has substandard electrical conductivity and surface area.
On the other hand, thermally reducing GO at above 1000°C produces a high surface area rGO which is similar to a pristine graphene. However, this process has a major drawback - the structure of the graphene platelets is damaged by the heating process, resulting in significant mass loss, and potentially impacting the mechanical strength of the rGO.
Electrochemical production of rGO could be the preferred commercial method used in the future, since it produced a material almost identical in structure to pristine graphene. In the electrochemical method, substrates like glass or indium tin oxide (ITO) are coated with a thin layer of graphene oxide. Electrodes are attached to each end of the substrate, and then linear sweep voltammetry is performed in a sodium phosphate buffer.
This method produces a very high quality material, and uses minimal harmful chemicals. However, it is difficult to scale, due to the need to deposit large quantities of GO on substrates.
Reduced Graphene Oxide
As mentioned above, GO is reduced to obtain rGO (Figure 1). This process is carried out thermally, chemically, or through IR or UV irradiation to obtain a powder form. Thanks to its excellent electrical conductivity, the product is used in a number of research projects.
.png)
Figure 1. Reduced graphene oxide
Properties of Reduced Graphene Oxide
Properties of rGO are as follows:
- Reduction method: Chemically reduced
- Color: Black
- Form: Powder
- Odor: Odorless
- Sheet dimension: Variable
- Solubility: Insoluble
- Density: 1.91g/cm3
- Dispersability: It can be dispersed at low concentrations of less than 0.1mg/mL in DMSO, NMP, DMF
- Electrical conductivity: 666,7 S/m
- Humidity (Karl Fisher, TGA): 3.7 - 4.2%
- BET surface area: 422.69 – 499.85m2/g
Elemental Analysis
- Oxygen (%): 13 – 22%
- Hydrogen (%): 0 – 1%
- Nitrogen (%): 0 – 1%
- Carbon (%): 77 – 87%
- Sulfur (%): 0
Applications
rGO is used in the following applications:
- Graphene research
- Batteries
- Biomedical
- Supercapacitors
- Printable graphene electronics
Quality Control
Graphenea’s rGO is made to go through a stringent quality control process so as to ensure that the product produced is of high quality and has good reproducibility. Graphenea also provides customized solutions for application requiring more specific quality control.
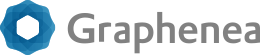
This information has been sourced, reviewed and adapted from materials provided by Graphenea.
For more information on this source, please visit Graphenea.