The use of QPAC® polyalkylene carbonate in 3D printer applications has been studied by several research organizations. The distinctive decomposition properties which include low temperature and contaminant free burnout of QPAC® can be applied to this technology. There are various types of Additive Manufacturing (AM) Technology.
.jpg)
Image Credit: Shutterstock.com/Alex_Traksel
Additive Manufacturing (AM) Technology
The QPAC® has a different utility based on the AM technology. Laser Sintering technology is an example of Binder Jetting Technology, where the binder is placed layer by layer onto a powder bed by inkjet head. A laser is subsequently applied to sinter the powder. If the end product is used in an application where contaminants are rejected, then the QPAC® is the perfect option for a binder in this system.
The QPAC® is also being extensively examined in another type of 3D printer technology, called Fused Deposition Modeling (FDM). After the filament of the thermoplastic is unwound through a coil, it is extruded through a nozzle which later solidifies to make layers. The object is produced through extrusion of molten plastic to form layers as the material hardens immediately after being extruded from the nozzles. In this case, the QPAC® functions as the thermoplastic. If the final part demands the polymer to be decomposed (such as a mold), then the QPAC® can indeed be a suitable choice, again because of its decomposition properties.
AM Technology may use glass, metal, ceramic, or polymer as the mass to build the 3D shape. In several cases, these powders are sensitive to high curing temperatures. As the QPAC® can be removed at lower temperatures compared to other binders, the QPAC® binder is the perfect material for these applications.
Conclusion
Hence, there are various kinds of AM Technologies that are exploring the use of QPAC® as either a material or a binder in their printer systems. The QPAC® polymers being tested depend on the final application. Overall, the QPAC®40 and QPAC®25 tend to be more flexible and offer good adhesion strength when used, while the QPAC® 130 and QPAC® 100 provide higher rigidity and stiffness when desirable. All provide the same benefits of clean burnout and low temperature debind.
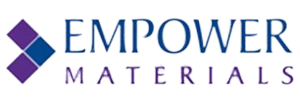
This information has been sourced, reviewed and adapted from materials provided by Empower Materials.
For more information on this source, please visit Empower Materials.