Empower Materials Inc. manufactures QPAC®, the cleanest thermally decomposable organic/sacrificial binders in the world, which cleanly decomposes into water and CO2 in various types of atmospheres, leaving almost no residue. This property contributes to the extensive usage of QPAC® in many challenging applications.
.jpg)
Shutterstock.com/Ilkin Zeferli
QPAC® poly(alkylene carbonate) copolymers are an exclusive range of ground-breaking thermoplastics representing a real innovation in polymer technology. While conventional plastics have been mostly petroleum based, these materials are derived from carbon dioxide and are produced through the copolymerization of CO2 with one or more epoxides. This results in polymers that are clear, amorphous, readily processible, and have enduring mechanical stability. They are also eco-friendly as they consume 50% fewer petrochemicals, as opposed to other polymers which are 100% petrochemical based. Furthermore, the polymers may have biodegradable properties consistent with an eco-friendly binder.
QPAC® 40, polypropylene carbonate, and QPAC® 25, polyethylene carbonate, are the two most commonly used products within Empower Materials’ family of binders. However, a vast range of QPAC® polymers can be obtained by changing the epoxide monomer or using blends of epoxides to create a specific reaction. The technical group at Empower Materials has the expertise needed to efficiently work with the customers to develop the right product for their application.
Production Capabilities of Empower Materials
As the world’s only commercial manufacturer of polyalkylene carbonates, Empower Materials is capable of manufacturing large quantities (1000's kgs) of QPAC® 100, a terpolymer of polypropylene carbonate and polycyclohexene carbonate; QPAC® 40, polypropylene carbonate; and QPAC® 25, polyethylene carbonate.
Moreover, an extensive variety of other QPAC® polymers are possible through substitution of oxiranes (epoxides) using the same production equipment configuration. Besides QPAC® 25, QPAC® 40 and QPAC® 100 (polypropylene carbonate, polyethylene carbonate and polypropylene carbonate/polycyclohexene, respectively), the following have been effectively synthesized on pilot scale equipment: QPAC® 130 (poly-cyclohexene carbonate) and QPAC® 60 (poly-butylene-carbonate).
Also, Empower Materials has the technology to modify the molecular weight polymer across an extremely wide range.
QPAC Organic Binders in Technical Glass Applications
QPAC® polyalkylene carbonates are perfect for use as a binder in glass applications, such as joining materials to glass substrates, glass frit, and glass performs. QPAC® is being used in various high technical sealing glass applications including OLED and AMOLED.
The following properties can be attributed to the growing interest in QPAC® in technical glass applications:
- QPAC®'s molecular weights and viscosities can be customized for specific solution or paste requirements
- QPAC® is compatible with a wide range of sealing glasses and metals
- Both QPAC® 40 polypropylene carbonate and QPAC® 25 polyethylene carbonate are naturally tacky and their degrees of plasticity can be adjusted as necessary
- QPAC® decomposes completely between 200 to 300 °C which can be as much as or more than 100 °C below the decomposition temperature of other binders.
- Decomposition is complete through three phases: solid, liquid and vapor
- Upon decomposition, QPAC® leaves very low ash residue with the complete burnout of carbon.
- QPAC® binders are also unique in that they burn out mild, without violent gas formation; therefore, whether the process operates in a reducing, oxidizing, or inert atmosphere, there is less cracking in the part
These properties result in a glass paste with properties better than those of pastes prepared with more traditional binders. Additionally, QPAC® 25 polyethylene carbonate and QPAC® 40 polypropylene carbonate consume up to 50% less petrochemicals than conventional plastics.
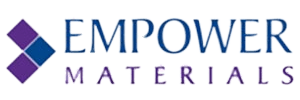
This information has been sourced, reviewed and adapted from materials provided by Empower Materials.
For more information on this source, please visit Empower Materials.