Understanding radiation-induced plastic flow in amorphous silica glass is vital for glass science and technology, and for decades it has been studied using high-energy ions and particles. However, researchers still do not truly comprehend the deformation behavior of such material irradiated by low-energy electrons.
Electrons have much greater penetration depths compared to heavier particles and ions, so they can generate uniform damage and structural changes throughout a material. This article will explore an investigation into plastic flow of silica particles under a combined effect of compressive stress and electron radiation inside a scanning electron microscope (SEM).
In-Situ Compression Testing
The compression experiments were conducted in-situ, on 1 μm diameter silica particles using Bruker's Hysitron PI 85L SEM PicoIndenter equipped with a 5 μm flat punch diamond probe (see Figure 1). Tip-sample alignment was performed using SEM imaging, in tandem with the XYZ sample staging of the Hysitron PI 85L.
.jpg)
Figure 1. Hysitron PI 85L SEM PicoIndenter.
Once the alignment was correct (Figure 2), load-controlled quasi-static compression experiments were conducted to peak forces of 1 mN and 4 mN under several beam dosages. A typical load function used to control the compression experiments is shown in Figure 3a, and Figure 3b shows a comparison of the acquired compression data under beam-on and beam-off conditions.
As the particles used were highly uniform, approximately 1 μm diameter, they can be considered identical for the purposes of this testing.
.jpg)
Figure 2. A 1 μm silica particle prior to compression with a 5 μm flat punch probe.
.jpg)
.jpg)
Figure 3. (a) A typical load function; (b) p–h curves show the dramatic effect of the electron beam.
Plastic Flow and Fracture Behavior
Figures 4a–h chart the load-displacement curves and deformation behavior of the particles before (inset) and after the experiments with beam-off and beam-on conditions. The plastic strain varies considerably with changing peak loads and beam conditions. Plastic strain (ε) is calculated as d/D, where D is the original diameter of the particle and d is the amount of compression along the indentation axis.
The particle showed negligible strain (<0.05%, Figure 4b) at 1 mN load and beam-off condition. However, when beam currents of 30 pA and 480 pA were applied, similar diameter particles deformed plastically to 47% and 67% strain (Figure 4c and 4d). This can be compared to the “beam off” condition for the higher load experiments, where considerable plastic strain, almost 36%, was observed with fracture that separated the particle (Figure 4f).
The 30 pA beam-on condition also shows conjunctive plasticity (57%) and separation fracture (Figure 4g). However, when the beam current is raised to 480 pA, fracture is completely suppressed (Figure 4h).
.jpg)
Figure 4. Load-displacement curves and a selection of corresponding pre- and post-test SEM images from the compression tests. The extent of plasticity in the particle appears to be closely linked to the condition of the incoming electron beam.
Conclusions
This study observed the compression behavior of micron-sized silica spheres in-situ using a Hysitron PI 85L. From the data it can be seen that the mechanical properties of small-scale silica spheres is highly dependent on the conditions of the incoming electron beam. It was found that by increasing the beam current in the range of hundreds of pA, fracture behavior of this normally brittle solid material can be almost completely suppressed.
As well as this, it was also found to be possible to quantify the transient behavior in plastic flow as a function of incoming beam current by dynamically switching the beam on and off during the hold segment of the test. Such behavior could be taken advantage of in applications where the shaping of silica glasses by conventional methods is impractical and a transient, highly localized ductility is desired.
Acknowledgments
Produced from materials originally authored by Sanjit Bhowmick, Ph.D. and Douglas Stauffer, Ph.D. from Bruker.
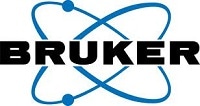
This information has been sourced, reviewed and adapted from materials provided by Bruker Nano Surfaces.
For more information on this source, please visit Bruker Nano Surfaces.